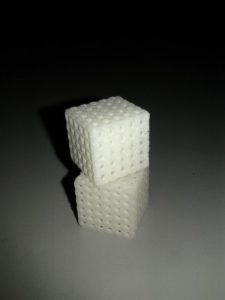
Com’è noto, la prototipazione rapida (Rapid Protoyping) è un insieme di tecniche industriali che consentono la realizzazione di prototipi in tempi e con costi più contenuti rispetto alle produzioni di serie. Nel corso degli anni, e in particolare in questi ultimi, le tecniche di prototipazione rapida sono state perfezionate. Senza entrare nel dettaglio, possiamo dire che la prototipazione rapida si differenzia dalle tecniche tradizionali di asportazione di truciolo in quanto opera su una base concettuale inversa: il materiale, anziché asportato, viene “aggiunto strato per strato” (fabbricazione stratificata o “layered manufacturing”), il che permette di ottenere forme anche molto complesse, a volte impossibili da realizzare con le lavorazioni tradizionali. In questo modo è possibile valutare un oggetto non solo in base alla sua rappresentazione 2D su schermo (o, nella migliore delle ipotesi, attraverso proiezioni tridimensionali con appositi occhialini) ma anche toccandolo materialmente, e potendo così realmente verificare l’ingombro, le dimensioni, l’aspetto estetico, la capacità di essere assemblato assieme ad altri organi, ecc. Il tipo di utilizzo della macchine di prototipazione rapida è mutato negli ultimi anni, soprattutto grazie alla diffusione nelle piccole e medie imprese dovuta alla sensibile diminuzione dei costi di queste tecnologie. Ne è un esempio la recente “esplosione” delle macchine di stampa 3D, che tanto successo stanno riscuotendo sul mercato.
L’evoluzione del “rapid tooling”
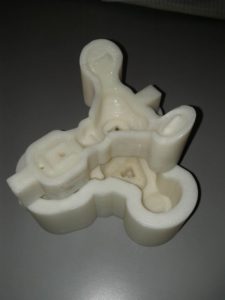
Il rapid tooling (“stampo rapido”) rappresenta un passo in avanti nell’ambito dell’utilizzo delle tecniche di addizione stratificata di materiale per fusione laser (SLS o SLM). Infatti, grazie alle macchine di prototipazione rapida, anziché produrre semplici prototipi è oggi possibile realizzare stampi, o in generale attrezzature, per il processo di stampaggio a iniezione plastica, evitando di ricorrere alla creazione dello stampo mediante asportazione di truciolo. Si tratta di stampi in materiale plastico o metallico che, una volta realizzati, devono essere lavorati e finiti generalmente a mano ma che comunque, entro certi limiti applicativi, consentono di ottenere prototipi stampati o comunque piccole produzioni in tempi ridotti e a costi contenuti. Se lo stampo viene realizzato in materiale plastico, l’elemento da iniettare deve avere punto di fusione più basso e, soprattutto, i parametri dell’intero processo (pressioni, temperature, ecc.) devono essere compatibili con il materiale scelto. Il silicone è un esempio di materiale stampabile per iniezione attraverso uno stampo realizzato in materiale plastico con le macchine di prototipazione rapida. Lo stesso discorso vale per gli stampi realizzati in metallo, i quali, dopo essere stati realizzati e rifiniti (per esempio, lucidati) possono essere utilizzati per stampare qualunque materiale plastico. Ne risulta così ampliato lo spettro applicativo di tale tecnologia. In particolare, le tecniche SLS ed SLM con la sinterizzazione laser delle polveri metalliche permettono la costruzione diretta di stampi a iniezione plastica, ma anche di stampi di estrusione, vulcanizzazione, pressofusione e deformazione della lamiera. Inoltre, consentono la realizzazione di inserti con tutte le caratteristiche necessarie: piani di divisione, movimenti, canali di raffreddamento. Dal punto di vista dei settori di sbocco, attraverso il rapid tooling è possibile produrre prototipi di manufatti medicali, quali protesi, maschere, tutori, ecc., per renderli ancora più “personalizzati”, cioè “adattati” alle reali necessità dei pazienti, evitando di costruire ogni volta uno stampo con le tecniche tradizionali, dunque con costi non sostenibili. Ovviamente, tale tecnica consentirà a breve di realizzare prototipi stampati anche in altri ambiti industriali e renderà possibile ai progettisti testare “dal vivo” geometrie e caratteristiche di pezzi stampati prima della messa in produzione vera e propria. Le imprese che si specializzano in rapid protyping o rapid tooling rappresentano un’avanguardia nel mondo industriale manifatturiero, in quanto non solo offrono servizi di esecuzione prototipi conto terzi, ma ormai eseguono anche veri e propri manufatti funzionali realizzati in piccoli lotti, in tempi rapidi e a prezzi bassi.
Grande varietà tecnologica
Nonostante la prototipazione rapida sia una tecnica piuttosto recente, le macchine e soprattutto i materiali di impiego evolvono continuamente, non a caso la classificazione principale delle tecniche si basa sulla natura (e sullo stato) dei materiali impiegati: polveri, liquidi (resine polimerizzate), solidi. Tra le tante tecniche di prototipazione rapida, facciamo una rapida carrellata su quelle più interessanti dal punto di vista industriale. La SLS o “Sinterizzazione Laser Selettiva” utilizza polveri, termoplastiche, metalliche o silicee, e utilizza un laser per sinterizzare i materiali impiegati per la costruzione del prototipo. È importante sottolineare che l’impiego di polveri sta assumendo sempre maggiore importanza, poiché permette di variare tipo di oggetto utilizzando la medesima macchina.
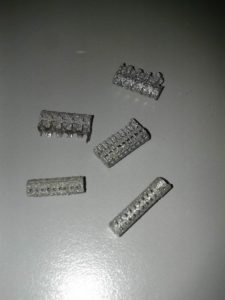
L’SLM o “Fusione laser selettiva” è molto simile alla sinterizzazione laser selettiva, ma se ne differenzia per l’impiego di polveri metalliche integrali, ossia prive di elementi bassi fondenti in ausilio. Ciò significa che il laser è più potente rispetto alla SLS ma che anche le caratteristiche meccaniche del manufatto metallico realizzato sono superiori.
La stampa 3D è simile alla SLS, tuttavia le polveri non vengono sinterizzate ma mantenute insieme da un “collante” spruzzato con una testina.
L’FDM o “Modellazione a deposizione fusa” utilizza fili e barrette di materiale termoplastico, deposto su una tavola da una “testina calda” capace di muoversi lungo 3 assi x, y e z. Poiché non tutte le geometrie sono realizzabili, specialmente quelle con elementi a sbalzo (il materiale “cadrebbe” prima della solidificazione), è spesso necessario formare elementi di appoggio e supporto (a forma di “nido d’ape” affinché non siano troppo pesanti) da rimuovere successivamente. Inoltre, per l’esecuzione di fori o di altri parti cave “difficili”, è possibile ricorrere anche a macchine – ovviamente più costose – capaci di deporre due tipi di materiali, uno dei quali può essere “sciolto” attraverso un bagno chimico successivo. Ciò permette la formazione di particolari anche molto complessi.
Non solo prototipi
Il perfezionamento delle tecniche di addizione stratificata del metallo fa sì che attualmente siano realizzabili oggetti con finiture superficiali eccellenti o comunque di molto superiori rispetto al recente passato. L’affinamento della tecnologia è tale che oggi è possibile ottenere non più solo prototipi, ma anche pezzi “reali” e funzionali impossibili (o quasi) da realizzare in altro modo. La nuova evoluzione della prototipazione rapida è quindi la “produzione rapida” di pezzi “reali” in piccoli lotti o addirittura in esemplari unici: stiamo parlando per esempio di palette molto complesse di turbine per aeroplani o per centrali energetiche le quali, essendo molto lunghe, sarebbe pressoché impossibile o non conveniente realizzare per asportazione di truciolo o per sinterizzazione. Ovviamente, questo tipo di produzione richiede macchine di elevato livello non ancora particolarmente diffuse sul mercato, e diverse ore di lavoro, in quanto il processo è tanto più lento quanto più raffinato è il modello di riferimento e quanto più è quindi complesso l’algoritmo di movimentazione della testina che consente la deposizione del metallo.
Limiti da superare
Come ogni tecnologia, anche la prototipazione rapida “risente” di alcune problematiche e limiti operativi, molti dei quali in fase di studio e di risoluzione. L’introduzione di raffinati strumenti di programmazione software ha comunque migliorato le tecniche di deposizione di materiale, consentendo migliori finiture superficiali rispetto al passato, ed evitando la generazione di “geometrie indesiderate”, di contorni imperfetti (sgretolamenti) e gli sprechi di materiale. Uno degli elementi più importanti delle tecniche di addizione del materiale riguarda il “voxel” (analogo al “pixel” in tre dimensioni), cioè il più piccolo elemento tridimensionale di materiale deposto distinguibile nello spazio. Poiché ogni strato orizzontale, definita “slice”, di materiale deposto è composta da un certo numero di voxel, è naturale che la superficie finale del pezzo presenterà un aspetto “a gradini”. Più i voxel sono piccoli, maggiore sarà la precisione geometrica e superficiale con cui il prototipo sarà realizzato.
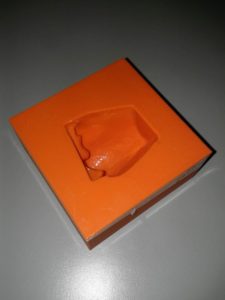
Tuttavia, più i voxel sono piccoli, maggiore è il tempo di esecuzione del particolare e il costo dell’operazione. Sono comunque allo studio nuove tecniche e soluzioni non solo per migliorare la definizione del voxel, ma anche per rendere più resistenti e precise le slice. Un altro elemento da tenere presente – soprattutto nell’ambito della produzione di manufatti funzionali e non di prototipi “estetici” – è quello della resistenza meccanica. Dunque, ogni realizzazione deve essere studiata e testata, soprattutto se il componente realizzato non è un prototipo ma un pezzo funzionale. Nel caso di manufatti in materiale plastico, la resistenza meccanica dipende ovviamente dal tipo di materiale utilizzato; in genere, comunque, il comportamento di un manufatto realizzato per addizione è diverso da quello ottenuto per stampaggio a iniezione, e perciò deve essere preventivamente valutata o testata. Nel caso dell’addizione metallica attraverso laser, il manufatto ha proprietà sicuramente meno elevate rispetto ad altre tecnologie, per esempio rispetto all’asportazione di truciolo o anche alla stessa sinterizzazione. Ciò deriva dal fatto che il materiale viene deposto dalle macchine di prototipazione attraverso micro-impulsi laser che generano sostanzialmente “micro-saldature” e che formano una struttura non omogenea e quindi con proprietà resistenziali inferiori. Quindi, anche in questo caso, l’utilizzo di pezzi realizzati con macchine di prototipazioine deve essere vincolato all’esatta definizione dei parametri di lavoro (potenza del laser, dimensione delle slice, tipo di polvere metallica, ecc.) e alle caratteristiche meccaniche da ottenere. Si tratta perciò di produzioni da eseguire con estrema cautela: vi è ancora molta la strada da fare, esistono molti campi ancora inesplorati, e non a caso imprese e centri di ricerca stanno eseguendo molti studi e approfondimenti specifici per “capire” la consistenza interna e superficiale (micro e macroscopica) di oggetti realizzati con queste tecnologie.
Formatura incrementale della lamiera
Un’altra tecnica di rapid tooling, che tuttavia non comprende la tecnologia di fusione laser e addizione dei materiali, è quella della “formatura incrementale della lamiera”. Si tratta di una tecnologia di deformazione a freddo della lamiera, di recente ideazione, con cui è possibile costruire prototipi o piccole serie in acciaio, anche inossidabile, leghe di alluminio, ottone, rame, ecc. Infatti, essa consente di realizzare componenti senza l’impiego di un’attrezzatura dedicata ma solo di una struttura di fissaggio della lamiera alla macchina e di un utensile, in genere di piccole dimensioni e di geometria piuttosto semplice, quale un punzone di forma emisferica. La formatura si ottiene mediante l’azionamento elettronico dell’utensile che deforma localmente e progressivamente la lamiera grezza in modo da conferirle la forma finale desiderata. La geometria del prodotto finito dipende dal moto dell’utensile rispetto al pezzo oltre che dalla struttura di fissaggio. La formatura incrementale si suddivide generalmente in “single point”, quando la lamiera in deformazione è supportata solo da un supporto inferiore (“backing plate”), e “two points”, quando è presente una matrice o un semi-stampo che la sostiene.
Nonostante si tratti di un processo ancora lento e con alcuni evidenti limiti applicativi (alcune forme e geometrie non sono realizzabili), la formatura incrementale rappresenta un processo molto interessante per colmare il gap, tuttora esistente, tra le metodologie di produzione di massa e la prototipazione di parti: permette di realizzare prototipi e preserie di elementi della carrozzeria di automobili in tempi rapidi senza dover ricorrere a costosissime attrezzature come gli stampi in ghisa.
Si ringrazia il prof. Claudio Giardini, membro di AITeM e docente di Tecnologie e Sistemi di Lavorazione presso il Dipartimento di Ingegneria dell’Università degli Studi di Bergamo, per il materiale fornito.
2 risposte
Buongiorno,
mi chiamo Carlo Michelini, lavoro per una start-up di articoli per la pesca; ho visto dal vostro sito che producete stampi e modelli per metalli; volevo capire se potete realizzare delle forme basandovi su un disegno o su un modello in legno, e se realizzate i prodotti utilizzando alluminio o piombo o zinco e, nel caso, qual’è il vostro quantitativo minimo d’ordine.
In attesa di un vostro riscontro vi auguro buone feste.
Carlo Michelini
signor Michelini, la prego di contattarmi: gdegidio(at)gmail.com
I commenti sono chiusi.