L’utilizzo di tecniche di processo nuove, come anche la diffusione di materiali più flessibili rendono i prodotti in fibra di carbonio sempre più competitivi. In questa evoluzione continua un ruolo essenziale è rivestito dagli stampi. Per rendere evidente la loro importanza per il raggiungimento degli obbiettivi di competitività sul mercato, in questo articolo si descrive la procedura di “formatura” più diffusa per elementi in fibra di carbonio. Detto in altri termini, come si trasforma un’idea di forma in un prodotto commerciale? Di solito attraverso 5 passaggi, che coinvolgono 2 modelli, 2 stampi e tanta tecnologia.
La fibra di carbonio rappresenta il materiale del presente come anche una delle sfide tecnologiche più interessanti per il futuro. Si tratta di un polimero che assume la forma di grafite, uno dei vari stati del carbonio puro. Nella grafite gli atomi di carbonio sono disposti in anelli esagonali aromatici, legati tra loro a formare grandi piani. Il loro aspetto è quello di una “rete metallica”. Le fibre di carbonio hanno la forma di sottili fogli di grafite, lunghi e stretti, come nastri. Questi nastri di grafite si raccolgono in fasci, a formare le fibre, dalle quali deriva il nome di fibre di carbonio. Queste fibre, benché durissime, sono troppo fragili per essere utilizzate da sole, mentre risultano perfette per rinforzare materiali polimerici, come le resine epossidiche o altri materiali termoindurenti. Le fibre agiscono come “rinforzo” su una “matrice” di materiale di base. Questi materiali rinforzati prendono il nome di “compositi” proprio per evidenziare la presenza di più di un componente. Tra le tante combinazioni di matrice e rinforzo, i compositi rinforzati con fibra di carbonio sono particolarmente apprezzati per la loro elevata resistenza “specifica” (ossia in rapporto al proprio peso). Sono spesso più “forti” dell’acciaio, ma anche molto più leggeri. Per questo motivo si sono affermati come valida soluzione per sostituire i metalli negli utilizzi più impegnativi: dalla realizzazione dello Space Shuttle a quella dei moderni aerei, dalle autovetture di Formula 1 e fuoriserie più prestigiose (es. Lamborghini e BMW), fino alle motociclette da competizione del MotoGP. Ma negli ultimissimi anni la fibra di carbonio sta rapidamente invadendo ogni settore, fino agli oggetti più comuni, quali racchette da tennis, bici e mazze da golf, grazie al progressivo miglioramento nei processi realizzativi. L’utilizzo di tecniche di processo nuove, come anche la diffusione di materiali più flessibili, anche in forma di semilavorati, consentono di superare progressivamente le varie barriere tecnologiche, riducendo il costo e rendendo i prodotti in fibra di carbonio sempre più competitivi. In questa evoluzione continua un ruolo essenziale è rivestito dagli stampi, elementi essenziali in vari fasi del processo produttivo. Per rendere evidente la loro importanza per il raggiungimento degli obbiettivi di competitività sul mercato, in questo articolo si descrive la procedura di “formatura” più diffusa per elementi in fibra di carbonio.
Detto in altri termini, come si trasforma una idea di forma in un prodotto commerciale? Di solito attraverso 5 passaggi, che coinvolgono 2 modelli, 2 stampi e tanta tecnologia.
Dall’idea al prototipo
La prima fase riguarda la trasformazione di una idea di prodotto in un modello reale e tangibile. Se siamo di fronte a qualcosa di veramente originale, il tutto parte da schizzi fatti a mano libera. Questi disegni (“sketch”) devono essere in grado di descrivere, almeno a livello di concetto, la proposta progettuale, e sono di solito accompagnati dai primi dimensionamenti. A partire da questa idea di prodotto, attraverso l’utilizzo di uno dei tanti applicativi CAD presenti sul mercato, si sviluppano le geometrie di dettaglio (fig. 1).
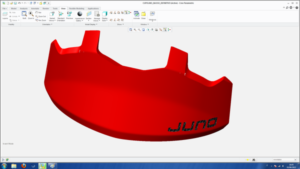
Questi strumenti di disegno assistito consentono la modellazione tridimensionale delle superfici, ma anche la loro ottimizzazione funzionale. In realtà, molto spesso l’obbiettivo della progettazione non è quello di “inventare” qualcosa di nuovo, ma piuttosto di riadattare e migliorare prodotti già esistenti (sia propri che della concorrenza!). In questo caso, diventa particolarmente comodo ricorrere a tecniche di “ingegneria inversa”: strumenti laser, ottici o meccanici consentono di acquisire la geometria dell’oggetto in modo rapido e preciso. L’acquisizione avviene “per punti”, ma specifici algoritmi consentono di modellare le superfici ricostruendo le forme. Qualsiasi sia la strada che porti a disegnare il modello “virtuale” tridimensionale, a questo punto si è pronti per passare alla creazione del modello “fisico”. A questo risultato si arriva di solito utilizzando una tecnica di prototipazione rapida, tra le tante ormai disponibili. La lavorazione dal pieno attraverso macchina utensile è una soluzione sempre meno utilizzata per ragioni di tempo e costi. Nella prototipazione rapida apposite “testine” costruiscono il prototipo aggiungendo, strato dopo strato, uno speciale materiale (es. ABS, resine fotopolimerizzanti). Il prototipo è poi ripulito (es. tramite sabbiatura) dagli eventuali residui del processo. Al termine, è trattato superficialmente (es. verniciatura) per rendere le superfici più levigate ed adatte alle fasi successive (fig. 2).
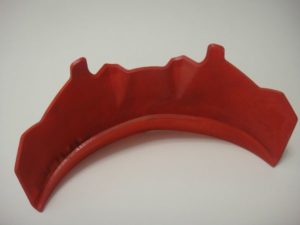
Dal prototipo allo stampo
Il prototipo cambia sede. Si sposta ora in un laboratorio dove operatori specializzati “spalmano” la “vetroresina” sulla sua superficie e la lasciano indurire in ambiente per creare uno stampo (fig. 3).
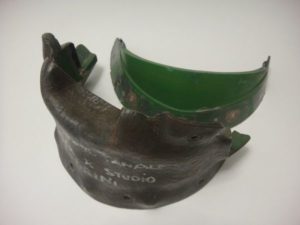
La vetroresina è il secondo materiale composito che incontriamo, dopo la fibra di carbonio. Qui il rinforzo è dato da filamenti di silicio, in forma di fibre di vetro, annegate in una matrice di resina termoindurente. Questi due compositi, con fibre di vetro oppure di carbonio, possono apparire simili, ma sono profondamente diversi. Persino in quei casi in cui si utilizzano resine della stessa famiglia come matrice, le differenze chimico-fisiche e meccaniche tra i due compositi restano marcate. La vetroresina è, di solito, “laminata” a mano: gli operai stendono un tessuto di fibra di vetro e la riempiono di resina, che lasciano poi solidificare. La polimerizzazione, avvenuta a “freddo”, è avviata da un catalizzatore chimico. L’arbitrarietà di questa procedura resta molto elevata. Per la fibra di carbonio, si utilizzano, invece, di solito, tessuti impregnati di resina, che sono stesi sulle superfici, ma possono polimerizzare solo applicando forti pressioni e temperature. Questa polimerizzazione “spinta”, realizzata di solito grazie ad una autoclave, fornisce ai compositi con fibra di carbonio una maggiore consistenza e resistenza. Messa a confronto, quindi, la vetroresina rappresenta un materiale semplice da produrre ed economico, ma anche “povero” in termini di prestazioni. Tornando al nostro processo, la scelta di passare attraverso la realizzazione di un stampo in vetroresina (invece che di altri materiali) consente di costruire un negativo del modello in modo rapido ed economico. Inoltre, evita al modello in prototipazione di passare in autoclave, come avverrebbe nel caso volessimo usarlo per costruire uno stampo in fibra di carbonio, ma dove verrebbe immediatamente distrutto. Allo stesso tempo, neppure la vetroresina è adatta ad essere utilizzata in autoclave nella realizzazione della normale produzione, dove le temperature possono arrivare oltre i 130 °C e le pressioni a diversi bar. Basterebbero pochi cicli, e quindi pochi componenti prodotti, per cominciare a deteriorarsi perdendo la precisione geometrica. E’ necessario quindi aggiungere un passaggio intermedio.
Dallo stampo al modello
Sullo stampo in vetroresina sono stesi alcuni tessuti di fibra di carbonio, “pre-impregnati” da resina, e infilati in autoclave per seguire i cicli di “post-cura”. Sul mercato esiste una varietà enorme di tessuti e di pre-impregnanti. Ogni tessuto si differenzia per numerose caratteristiche tra le quali, le più ovvie sono lo spessore complessivo del tessuto, la densità di carbonio, lo spessore e lunghezza dei singoli filamenti, la disposizione geometrica delle fibre (“trama”). Anche la scelta della corretta resina impregnante resta un elemento fondamentale del processo, se non tanto per definire le caratteristiche di resistenza meccanica di stampi e parti, quanto per fornire sostanza al materiale e per tutto quanto riguarda la polimerizzazione. E’ principalmente la resina, infatti, a delineare i parametri da utilizzare nel trattamento termico, definendo non solo temperatura e pressione massime, ma anche le rampe di raffreddamento. Inoltre, è sempre la resina ad avere un ruolo fondamentale nel caratterizzare il comportamento termico di stampi e modelli, permettendo di aggirare problematiche talvolta complesse di gestione delle dilatazioni termiche.
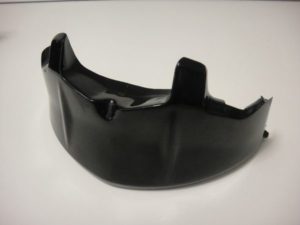
A conclusione di questo processo di “cottura” e raffreddamento, lo stampo in vetroresina viene aperto e ne esce un modello (detto “master”) di composito in fibra di carbonio (fig. 4). Siamo ad oltre metà del processo, ma ancora lontani dal termine.
Dal modello allo stampo
Sul modello appena realizzato sono stesi alcuni tessuti di fibra di carbonio pre-impregnati. Il procedimento è lo stesso di quello utilizzato per realizzare in modello in fibra di carbonio, ma è ora indirizzato a costruire un nuovo stampo (fig. 5); anche i materiali sono di solito identici.
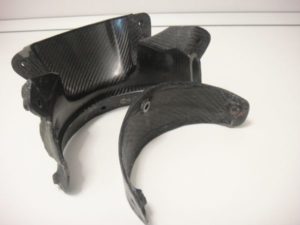
Il processo in autoclave è molto simile, anche se i parametri di temperatura, pressione, tempistiche di attesa e di raffreddamento non dipendono solo dai materiali utilizzati, come indicato in precedenza. Diventa fondamentale anche il valore di spessore delle parti (stampi o componenti) che si stanno trattando. Per ottenere i migliori risultati la polimerizzazione deve essere sempre completa ed omogenea. Il calore deve entrare in profondità e deve restarci un periodo ragionevole. Allo stesso tempo, la massima attenzione deve essere rivolta a non “bruciare” gli strati (“pelli”) più esterni dei componenti. Ne consegue che tanto più spessi sono i materiali da trattare, tanto più a lungo dovrà essere mantenuta la cottura e bassa la temperatura.
In aggiunta, è abbastanza evidente come uno stampo risulti, di solito, molto più “massiccio” del pezzo che andrà a costruire. Questo è legato innanzitutto alla sua maggiore dimensione (dovendo necessariamente circondare il pezzo) che si porta dietro, di solito, un maggiore spessore, necessario a dare una certa stabilità e rigidezza geometrica allo stampo. Ma è soprattutto legato alla necessità di realizzare uno stampo molto resistente, in grado di produrre un numero elevato di pezzi. Nel mondo dei compositi queste considerazioni sono ancora più pertinenti e portano sia a stampi che a modelli “master” molto più massicci dei componenti in composito che si andranno a realizzare. Mentre questi componenti saranno apprezzati soprattutto per la loro leggerezza (e quindi, anche, bassi spessori), i loro stampi e modelli dovranno al contrario risultare robusti e resistenti. Il risultato pratico è che, mentre le cotture in autoclave per i pezzi finali possono essere fatte persino a 140 °C, limitandoci alle 3 ore di processo, in quelle per stampi e “master” si è costretti a scendere a 70-80°C, prolungando così i trattamenti per non meno di 12-14 ore.
Dallo stampo al componente
Dopo quasi una giornata in autoclave il nostro ultimo stampo è pronto. In realtà, per ogni modello si andranno sempre a costruire almeno 2 stampi, uno per ciascuna delle superfici necessarie a racchiudere il modello. Per modelli particolarmente complessi, il numero di stampi sale come anche la complessità legata alla loro progettazione e realizzazione. Non se è parlato in precedenza, ma resta evidente come ogni stampo andrà progettato con molta cura a partire, ovviamente dalle geometrie del componente che andrà a realizzare e del processo produttivo necessario a produrre il componente. Ma, e qui interviene la peculiarità della produzione di parti in compositi, lo stampo dovrà essere progettato tenendo conto soprattutto delle particolarità del processo produttivo che sarà utilizzato proprio per realizzare lo stampo. Detto in altri termini, anche se in modo molto semplificato, quando si progetta uno stampo da realizzarsi in alluminio tramite fresa, è sufficiente preoccuparsi di verificare che l’utensile da taglio riesca a raggiungere certe zone. Quando si tratta di uno stampo in fibra di carbonio, bisogna stare attenti persino a proporzionare gli spessori con le temperature di cottura e con la direzione delle fibre.
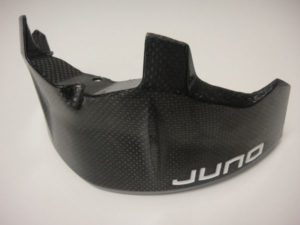
Tornado a parlare del nostro processo, su questa ultima coppia di stampi, si stendono i tessuti di fibra di carbonio pre-impregnata e si infila di nuovo in autoclave. Dopo un ciclo “standard”, stavolta limitato ad alcune ore, si arriva in fine al primo componente. Ovviamente, non è sostenibile pensare di realizzare un componente da vendere per ogni ciclo di autoclave. Di conseguenza, dal modello “master” saranno stati realizzati un numero significativo di stampi in fibra di carbonio e, quindi, al termine di ogni “infornata” ci troveremo già a disporre di un piccola serie di componenti (fig. 6).
LE RISPOSTE ALLE DOMANDE PIU’ FREQUENTI
Esaminando la complessità di questo processo nasce spontaneo il dubbio che alcune fasi sono ridondanti. Ma nella realtà non è così. O, almeno, non lo è nella generalità dei casi. Alcune spiegazioni di questo sono state già fornite in precedenza, ma vale forse la pena di ripeterle ora in modo organico, inserendo anche quei chiarimenti mancanti
Si potrebbe..
- utilizzare la prototipazione rapida per produrre, non il prototipo, ma direttamente lo stampo?
NO, perché i materiali di prototipazione non resisterebbero alle temperature e alle pressioni previste nell’autoclave.
- produrre direttamente uno stampo in carbonio a partire dal prototipo in prototipazione?
NO, per la stessa ragione: il carbonio ha bisogno dell’autoclave per polimerizzare mentre il prototipo proprio non può andarci.
- utilizzare direttamente uno stampo in vetroresina in autoclave?
NO, sia perché la vetroresina si deteriorerebbe rapidamente e sarebbe da sostituire, sia perché le dilatazioni termine differenziali tra i due diversi compositi (con fibra di vetro o di carbonio), alle temperature previste nei processi ordinari (anche 140°), non garantirebbero la precisione geometrica delle parti.
- realizzare parti funzionali, direttamente in prototipazione?
Certo che SI, ma non garantirebbero neppure lontanamente le prestazioni della fibra di carbonio. Sarebbero poco resistenti (p.es. circa 50MPa per le resine fotopolimerizzanti), molto pesanti, fortemente sensibili a temperatura, umidità ed invecchiamento (es. aumento di fragilità), quindi, in sostanza, inutili.
Ed estendendo l’orizzonte della tecnologia includendo anche le lavorazioni di taglio, si potrebbe…
- realizzare stampi per compositi in alluminio?
TALVOLTA SI, ed è infatti una soluzione adottata con successo da tantissimi anni. Ma, a fronte di numerosi importanti vantaggi, che la rendono talvolta “la più competitiva” tra quelle disponibili, presenta diversi punti a suo sfavore che la relegano sempre più spesso in secondo piano. Uno stampo in alluminio (o altri metalli), realizzato dal pieno per asportazione di truciolo, costa generalmente molto di più di uno in carbonio. Non si ripaga se non a fronte di larghissime produzioni, sempre meno frequenti sui mercati moderni dove si richiedono prodotti in rapida evoluzione. Inoltre, la finitura degli stampi, specie per le parti più interne, che sono di solito riprese a mano, rappresenta un lavoro estenuante, oltre che critico per i suoi impatti sulla sicurezza del personale e dell’ambiente
- utilizzare un materiale alternativo all’alluminio per gli stampi?
FORSE. Talvolta si usa rifinire mediante fresatura i prodotti in vetroresina ed il processo di taglio risulta anche relativamente efficiente. Ma rappresenta tutto un altro discorso l’ipotesi di produrre uno stampo in vetroresina a partire dal pieno. Costi, tecnologie rendono questa via solo teorica. Come è anche inimmaginabile pensare di “scavare” la fibra di carbonio, sia perché costerebbe troppo, data la “nobiltà” del materiale, sia perché le superfici intagliate sarebbero troppo grossolane per ogni successiva applicazioni. Senza contare i problemi non ancora veramente affrontati dei rischi associati alle emissione in ambiente delle fibre tecnologiche (vetro, carbonio, ecc.). Esistono altri materiali molto più adatti da essere fresati e diventare stampi (es. silicone, lavorabile con piccolissime frese di precisione), ma ancora non ne emerge nessuno idoneo ad essere utilizzato in autoclave, al contatto con la fibra di carbonio: di solito, a quelle temperature perdono rigidezza e forma.
- realizzare il modello “master” direttamente alla macchina utensile, in modo che poi lo stampo venga comunque realizzato in fibra di carbonio?
SI, esistono materiali nuovi (es. UREOL), abbastanza teneri da essere lavorati con semplicità, ma relativamente duri da garantire la precisione dimensionale necessaria per la realizzazione degli stampi. Anche qui, però, si tratta, almeno per ora, di una soluzione parziale, adatta solo in particolari condizioni (es. determinate tirature e geometrie). In particolare, questi materiali, nonostante siano abbastanza costosi, non riescono a resistere a più di qualche ciclo in autoclave. Di conseguenza, i numero di stampi che è possibile realizzare resta molto inferiore rispetto a quanti se ne possono fare con il processo finora descritto, passando attraverso un “master” in fibra di carbonio.
di Cristiano Fragassa, Gian Luca Monti