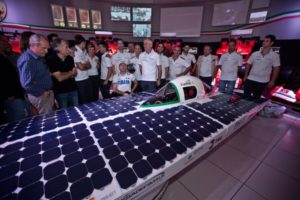
Il progetto è di quelli ambiziosi: portare un veicolo solare italiano al prossimo World Solar Challenge e magari competere alla pari in quella che può essere considerata la “Mille Miglia del Futuro”.
Tremila chilometri tra le dune
Si tratta di una competizione estenuante per mezzi e piloti: oltre 3.000 chilometri nel deserto australiano con partenza da Darwin ed arrivo ad ,. Si tratta di una strada lunga ed infuocata, da percorrere in meno di 7 giorni. Una gara dal forte potere attrattivo che per l’edizione 2013 vedrà scontrarsi 47 team di 26 diverse nazioni. A sventolare il nostro tricolore sarà Emilia III, un veicolo nato dal grande impegno del team Onda Solare composto dai tantissimi appassionati che partecipano a vario titolo nell’iniziativa. Un contributo tecnico è arrivato dall’Università di Bologna e dal CNR soprattutto nella realizzazione della parte elettrica e strutturale della vettura.
Telai da competizione
La prima volta per il team italiano è stata nel 2005 quando a competere fu Emilia I, una bicicletta a tre ruote con pedalata assistita da un motore elettrico alimentato da pannelli solari. Un primo esperimento che riuscì a guadagnare il terzo gradino del podio soprattutto grazie alla forza impressa sui pedali da un’energica squadra ciclistica interamente al femminile. Due anni dopo, nel 2007, arriva la prima auto interamente solare, Emilia II, che si lancia nell’avventura australiana. Nonostante abbia mancato il podio, monopolizzato dai grandi colossi dell’industria internazionale, ha lasciato nei suoi costruttori la voglia di riprovarci. E’ così che nel cuore dell’Emilia Romagna, in quella parte di territorio che può definirsi la Motor Valley d’Italia, accende il suo motore elettrico la nuova Emilia.
Solidità come parola d’ordine
Quest’auto solare tutta “Made in Italy” affronta una sfida in cui nulla può essere lasciato al caso. Leggerezza e resistenza sono requisiti indispensabili per questo veicolo: concetti progettuali che si ritrovano nella parte strutturale dell’auto, plasmata interamente con compositi in fibra di carbonio. Ma non solo: l’esigenza di resistere alle condizioni più estreme e di risultare perfetta in ogni minimo dettaglio ha spinto i costruttori ad adottare la fibra di carbonio anche per le parti non strutturali [Fig. 2].
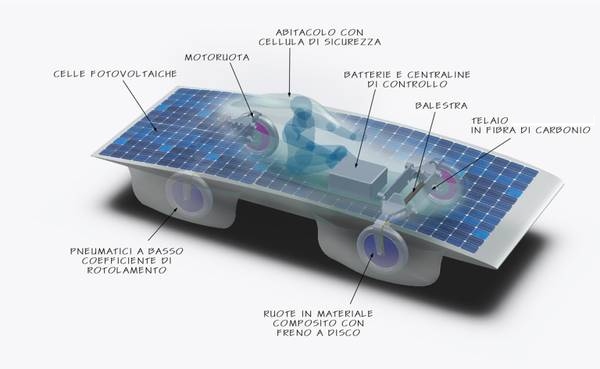
A sostenere questa scelta costruttiva sono state sia le proprietà tecniche offerte dalla fibra di carbonio, sia la grande padronanza del team nella realizzazione di stampi e parti in composito.
100% fibra di carbonio
Il veicolo è realizzato praticamente tutto in fibra di carbonio. La progettazione e costruzione di un prototipo in composito passa doverosamente per una conoscenza approfondita delle caratteristiche tecniche del materiale utilizzato e dei processi realizzativi. Per prima cosa bisogna tener presente che si tratta di un materiale anisotropo ed è quindi necessario disporlo in modo tale che le fibre lunghe lavorino prevalentemente a trazione. Quest’accortezza consente di sfruttare al massimo il rapporto peso/rigidezza tipico della fibra di carbonio. Il team ha potuto quindi ottimizzare ogni minimo dettaglio senza sottostare alle limitazioni proprie dei materiali metallici. Centinaia di particolari, anche di forme complesse, sono stati progettati e costruiti arrivando a variare tutti gli spessori in base alle esigenze specifiche. In questo modo il peso di ogni elemento è stato ridotto al minimo. In carbonio sono stati realizzati i tubi del telaio, la scatola guida, i ceppi dei freni, i giunti sferici che vincolano i movimenti della sospensione, la molla a balestra degli ammortizzatori e molto altro ancora.
Resistente con sicurezza
Alleggerire senza indebolire è stata l’idea centrale. Ed è su questa filosofia che nel tessuto in fibra di carbonio è stato inserito un 5% di sottilissimi filamenti di titanio. Una scelta che potenzia la resistenza della struttura nel caso di urti, infatti tutto lo sviluppo è partito da scelte strutturali precise, la più importante delle quali ha riguardato il telaio. Alla soluzione in monoscocca, che avrebbe comportato aumenti significativi in peso e costi a fronte di dubbi vantaggi in termini di prestazioni o sicurezza, si è preferito il più tradizionale telaio di tubi, anche questo caso, in fibra di carbonio.
Una “palestra” per gli stampi
Il cantiere di Emilia III si è trasformato quindi, a detta dei suoi stessi costruttori, una “palestra tecnologica”. Durante il suo sviluppo sono state introdotte alcune delle tecniche più innovative ed avanzate che si conoscano per la produzione di componenti in composito. Anche componenti apparentemente secondari hanno richiesto l’utilizzo di stampi dalle forme abbastanza complesse, per i quali è stato pressoché impossibile ricorrere a soluzioni commerciali. Inoltre bisogna considerare che esiste una stretta correlazione tra il manufatto e lo stampo che lo realizza, soprattutto se si tratta di compositi. La costruzione di questo veicolo ha portato quindi alla necessità di progettare e realizzare un numero enorme di stampi, tutti tra loro diversi.
Stampi in carbonio
Affinché i pezzi finali presentino le caratteristiche dimensionali volute è necessario che anche gli stampi siano realizzati con estrema attenzione, a partire dalla prima e più importante valutazione, quella relativa alla scelta del materiale con cui realizzarli: la fibra di carbonio. Sebbene attualmente possa essere considerato ancora un settore di nicchia, legato prevalentemente ai produttori stessi di elementi in composito, l’uso dei materiali compositi per gli stampi, in sostituzione a quelli metallici, trova sempre più spazio nell’ambito dell’industria meccanica specializzata. L’impiego di questi nuovi materiali fornisce agli stampi vantaggi considerevoli soprattutto dal punto di vista funzionale. Permettono, per esempio, di riprodurre geometrie e forme complesse. Presentano poi proprietà chimiche-fisiche del tutto comparabili con l’oggetto finale, assicurando al pezzo tolleranze dimensionali specifiche e precisione geometrica.
Dilatazioni differenziali contenute
In questo senso, particolare attenzione va posta al coefficiente di dilatazione termica causato dal problema dei ritiri differenziali tra modello e stampo. Il fenomeno fisico della dilatazione termica si verifica quando un corpo aumenta di volume all’aumentare della temperatura. Per questo il pezzo su cui viene costruito uno stampo in composito deve avere un coefficiente di dilatazione termica comparabile con il carbonio affinché i due oggetti a contatto, sotto effetto della temperatura del processo di polimerizzazione, si dilatino in egual misura. La pari dilatazione impedisce che si creino tensioni residue, per effetto del ritiro dimensionale, all’interno dello stampo durante la fase del raffreddamento. Le tensioni residue interne sono, in genere, indesiderate poiché abbassano il limite elastico e causano la tendenza del componente a deformarsi durante le seguenti applicazioni. Volendo scendere nello specifico ed analizzare le caratteristiche della fibra di carbonio, si scoprirà che tale materiale ha un coefficiente di dilatazione termica 50 volte inferiore a quello dell’alluminio (4.6*10-6 carbonio C-1, 2.3*10−5 C-1 alluminio), un dato che evidenzia come la miglior scelta tecnica sia quella che utilizza stampi in composito per costruire manufatti in composito, poiché solo così viene garantita la precisione dimensionale nella fase di stampaggio del componente finale.
Nascita di uno stampo in composito
Il punto di partenza per la costruzione di uno stampo in composito è il modello originale che dovrà essere realizzato in grandezza naturale, identico al pezzo che si desidera ottenere. Su questo modello si costruisce lo stampo femmina in composito. Il modello dovrà essere rifinito con estrema cura, altrimenti qualsiasi minimo difetto verrà riprodotto nello stampo e, a seguire, nel pezzo finito. E’ più semplice porre cura nel rifinire il modello, che è in positivo, piuttosto che intervenire poi nello stampo lavorando sul negativo. Il trattamento della superficie dello stampo parte dall’applicazione di agenti sigillanti che hanno lo scopo di chiudere tutte le microporosità della superficie. Si passa poi all’applicazione del distaccante che crea uno strato antiaderente e permette il distacco, senza danni, dello stampo dal modello. Il distaccante va scelto in base alle caratteristiche della superficie. Di seguito, si passa alla “stratificazione”, che consiste nell’applicare sulle superfici del modello diversi strati di fibra di carbonio [Fig. 3].
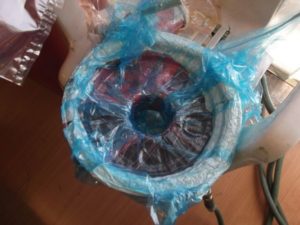
Questa fibra è amalgamata con resina polimerica a formare un tessuto preimpregnato. Questi tessuti sono sovrapposti manualmente fino a raggiungere lo spessore desiderato. Per la “polimerizzazione” della resina è indispensabile programmare un ciclo di “cura” sottovuoto in autoclave, che segue una rampa di temperatura prestabilita. Il materiale risulta ora catalizzato. Dopo raffreddamento a temperatura ambiente, lo stampo è estratto con l’ausilio di cunei, facendo particolare attenzione ad evitare di graffiarlo. A questo punto, va ripulito dell’eventuale residuo di distaccante, “carteggiato” ed è di nuovo pronto all’uso.
Spessori e geometrie
Durata e resistenza dello stampo sono strettamente legate al suo spessore. Generalmente questo spessore è proporzionale alla grandezza del pezzo e si aggira intorno ai 5-6 mm. I tessuti di fibra di carbonio, preimpregnati con resina epossidica sono i materiali che permettono di costruire stampi con un notevole risparmio di tempo. Inizialmente si passa alla stesura sul modello di un paio strati di tessuto a bassa grammatura (valore che esprime il peso in grammi di 1 m2 di tessuto) all’incirca 200 g/m2. Questi tessuti più leggeri, grazie alla loro morbidezza, replicano con massima precisione i dettagli del modello perché si adagiano facilmente intorno alle curve e agli angoli della struttura. Successivamente, si passa alla stratifica di tessuti con grammatura più elevata, 600-800 g/m2, fino a raggiungere le dimensioni dello stampo desiderate. Per velocizzare i tempi di manodopera, si può ricorrere a stuoie, tessuti a grossa trama, spessi 2-3 mm, con i quali lo spessore dello stampo è presto raggiunto.
Precisione e prestazioni
Gli stampi in composito hanno rappresentato un’importante novità nello sviluppo dell’autovettura. Si sarebbero potuti utilizzare i tradizionali stampi in alluminio, certamente più economici e più semplici da realizzare, ma le esperienze precedenti, hanno suggerito che solo stampi in composito permettono di ottenere la precisione richiesta. Questa maggior precisione vuole rappresentare quel guadagno tecnologico che Emilia III dovrà trasformare in prestazioni [Fig. 4].
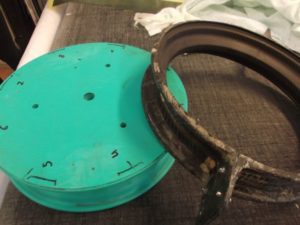
Un esempio in tal senso è dato dal giunto sferico della sospensione [Fig. 5]. Data la modesta potenza motrice, è stato necessario approntare una progettazione del veicolo tale da minimizzare i pesi, gli attriti e tutte le possibili sorgenti di dissipazione energetica. Da questo punto di vista, la sospensione anteriore si è rivelata essere uno dei componenti più critici: deve infatti assicurare stabilità di marcia e garantire ridotte dissipazioni energetiche ma, contestualmente, deve essere caratterizzata da un peso contenuto e da un’elevata affidabilità poiché su di essa grava tutto l’avantreno dell’auto. Il collegamento molla-ruota avviene attraverso un perno di attacco posizionato in un elemento triangolare che serve da collegamento tra ruota-sospensione-smorzatore. Il giunto sferico in carbonio deve garantire che ci sia precisione dimensionale e di accoppiamento, con tolleranze molto ristrette. Affinché venga assecondata la precisione del movimento trasferito dalla sospensione alla macchina, è indispensabile che questo componente abbia una correttezza delle dimensioni strettamente accurate. Quest’obiettivo è stato raggiunto solo grazie all’utilizzo di uno stampo sferico realizzato dallo stesso materiale. Carbonio piuttosto che acciaio oppure alluminio, in grado di offrire il medesimo coefficiente di dilatazione termica il quale, durante il processo di cura in autoclave, non influenza le deformazioni dimensionali del pezzo laminato sopra.
Non solo carbonio
Data questa premessa, si potrebbe pensare che l’autoveicolo sia stato completamente realizzato utilizzando stampi in composito. In realtà, per tutta una serie di criticità che questi stampi portano con sé, nella costruzione del veicolo si è reso necessario anche l’utilizzo di stampi in alluminio.
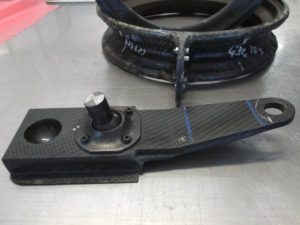
La prima criticità è di certo il costo. Già il carbonio risulta, di per sé, essere più costoso dell’alluminio. Inoltre, la creazione di stampi in composito obbliga ad un doppio passaggio nel centro di lavoro sia per il modello iniziale sia per la finitura. Non va nemmeno sottovalutato il fatto che uno stampo in composito è più soggetto ad usura del suo omologo in alluminio, risultando meno adatto per produzioni su larga scala. Tuttavia, sarebbe scorretto pensare che si tratti di uno stampo monouso.
Né carbonio, né alluminio
Non solo stampi esclusivamente in carbonio o in alluminio. Per la realizzazione delle ruote si è ricorso all’uso di uno stampo combinato carbonio-alluminio. La particolarità della ruota consiste nell’essere di tipo lenticolare, carenata, ovvero piena con una struttura in fibra di carbonio senza la presenza dei raggi o di sostegni dal bulbo [Fig. 6]. Ciò si concretizza nella capacità di questa ruota di rotolare con maggior fluidità, di non produrre vortici, di mantenere il flusso aerodinamico più costante e senza alterazioni. La parte in carbonio dello stampo è stata introdotta come soluzione al perfetto assemblaggio che la ruota deve necessariamente avere all’interfaccia con il motore.
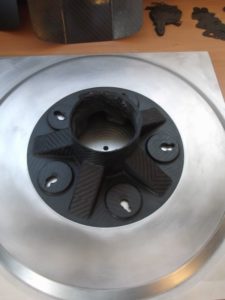
Ringraziamenti
Il progetto Onda Solare è supportato da un numero incredibile di appassionati: da esperti ingegneri, fino a semplici curiosi, piccoli medie e grandi aziende, persino qualche istituzione pubblica o finanziatore privato. Ognuno ci mette quello che riesce per renderlo possibile e sospingere l’autovettura verso il suo arrivo ad Adelaide. Tutti raccolti intorno a Mauro Sassatelli, l’intrepido sognatore, ideatore di questa sfida, e alla sua signora Antonella, la cambusiera che rende possibile ad oltre 20 persone attraversare incolumi il deserto. Continuate a seguire con noi questa avventura all’indirizzo: www.ondasolare.com.