Il trattamento di shot peening, o pallinatura, è tra i più comunemente utilizzati per migliorare il comportamento a fatica dei componenti meccanici. Oltre che a incrudire gli strati superficiali di materiale e ad introdurre negli stessi uno stato di sforzi residui di compressione, grazie ai quali si ottiene il miglior comportamento meccanico, un effetto non desiderato è l’aumento della rugosità, che può in parte ridurre i benefici del trattamento. Nelle righe che seguono si descrive un approccio a elementi finiti finalizzato alla previsione della rugosità indotta dalla pallinatura e che può essere utilizzato in sede di definizione del trattamento per una efficace scelta dei parametri da utilizzare.
La pallinatura, o shot peening, è uno dei trattamenti meccanici più utilizzati per migliorare il comportamento meccanico degli organi delle macchine e degli elementi strutturali. In particolare, questo trattamento viene comunemente utilizzato per incrementare le prestazioni degli elementi sollecitati ciclicamente e soggetti, quindi, al danneggiamento per fatica. Tuttavia, la pallinatura viene utilizzata anche in altre situazioni, come il fretting, la corrosione sotto sforzo e la fatica da contatto.
Notevoli sono, in termini quantitativi, gli incrementi del limite di fatica: grazie a una corretta impostazione dei parametri di trattamento è possibile migliorare il limite di fatica di un pezzo intagliato anche di più del 50%. La pallinatura consiste nel fare impattare la superficie del pezzo di interesse da un flusso di sfere (metalliche o ceramiche) di piccole dimensioni (il diametro varia comunemente da pochi decimi di millimetro a un paio di millimetri) scagliate, con un’attrezzatura pneumatica oppure con macchine centrifughe, ad elevata velocità in modo da indurre una deformazione plastica non uniforme sulla superficie. In tal modo il trattamento, grazie al ritorno elastico degli strati sottostanti, genera uno stato tensionale residuo di compressione negli strati superficiali del pezzo, che aiuta a prevenire la formazione di cricche di fatica e ne ritarda la propagazione. Un altro effetto della pallinatura è l’incrudimento degli strati superficiali di materiale, che pure contribuisce al miglior comportamento meccanico dei pezzi trattati.
Parametri di pallinatura e suoi effetti
Tali benefici possono essere ottenuti solo grazie a una corretta impostazione die parametri di trattamento, descritti dall’intensità Almen e dalla copertura. La prima rappresenta un indice sintetico dell’energia associata al trattamento; si tratta, infatti, della freccia residua lasciata su una sottile piastrina di dimensioni note e materiale assegnato (un acciaio per molle) e vincolata con viti su una base assegnata, dopo l’esecuzione della pallinatura su un solo lato. La copertura, espressa in termini percentuali, il tempo di trattamento utilizzato rispetto a quello necessario per ottenere l’intensità voluta: coperture del 200%, per esempio, indicano che il trattamento si protrae per un tempo doppio rispetto a quello necessario a ottenere un’intensità pari a quella desiderata. Risulta evidente che coperture minori del 100% non sono consigliabili, in quanto si rischia di avere una parte della superficie non pallinata.
Un ulteriore effetto, questa volta non voluto, del trattamento è la modifica della finitura delle superfici trattate; in particolare, il ripetersi degli impatti delle sfere causa un aumento della rugosità superficiale, fattore che, come è noto, peggiora la resistenza a fatica dei materiali. Tale effetto, quindi, rischia di ridurre i benefici ottenibili con la pallinatura, soprattutto nel caso in cui si trattino elementi costruiti con materiali non induriti superficialmente con trattamenti termici o termochimici (si pensi, per esempio, agli ingranaggi), per i quali il problema è meno sentito. In questi casi una scelta non adeguata del tipo di sfere e dei parametri di trattamento (tipicamente l’intensità Almen e la copertura) può indurre valori di rugosità che possono, in maniera più o meno marcata, ridurre l’aumento delle prestazioni legato all’incrudimento superficiale e allo stato tensionale indotto.
Da quanto detto, risulta evidente che la corretta impostazione dei parametri di trattamento è determinante per l’efficacia del trattamento. Al fine della loro corretta determinazione e, al tempo stesso, per ridurre i costi legati alla sperimentazione ad essa legati, risulta importante la definizione di approcci di simulazione capaci di riprodurre in maniera realistica il trattamento di pallinatura e tali da permettere di definire un legame tra effetti indotti e parametri utilizzati.
Diversi sono le proposte che sono state elaborato negli ultimi anni (si guardino i lavori citati in bibliografia). Tuttavia, quanto sviluppato fino ad oggi è finalizzato alla determinazione del campo di sforzi residui e alla sua relazione con i parametri con cui la pallinatura viene eseguita.
In questo contributo, invece, si pone l’attenzione sulla rugosità e sulla definizione di un approccio, basato su analisi a elementi finiti, per la previsione della rugosità che si ha a seguito del trattamento di pallinatura. A tal fine si è sviluppata una particolare procedura di elaborazione dei risultati delle analisi a elementi finiti che permette di estrarre i principali parametri che definiscono la rugosità di una superficie. Il confronto con alcuni risultati sperimentali ha fornito indicazioni positive sulla correttezza del modello sviluppato.
Definizione dei parametri di rugosità
Lo stato della finitura di una superficie è usualmente caratterizzato da profili ottenuti con appositi strumenti in grado di misurare il profilo della superficie in determinate direzioni o, direttamente sulla superficie. Diversi sono i parametri definiti per quantificare e caratterizzare la rugosità misurata. Tra questi si menzionano i più utilizzati nella pratica costruttiva: Ra, la media aritmetica della deviazione del profilo valutato rispetto a una superficie liscia è di gran lunga il più parametro estesa e più usato.
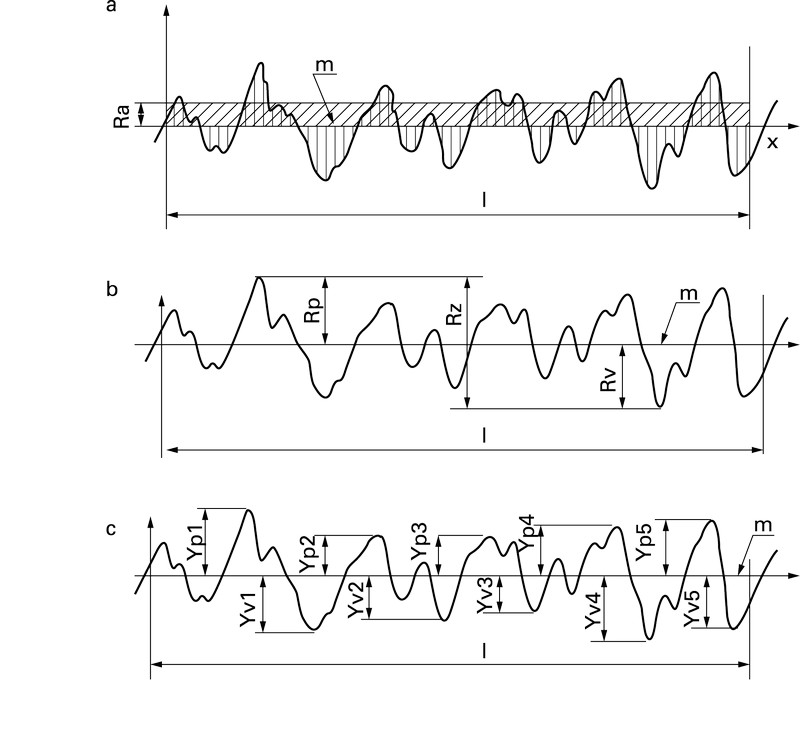
Definizione dei parametri di rugosità, Ra, Rz e Rc
Y = f (x) rappresenta le altezze all’interno del tratto di campionamento, come illustrato in Figura 2a.
Tuttavia tale parametro non è sufficiente a definire completamente la finitura superficiale, per cui altri parametri sono utilizzati. Tra questi, un altro ben noto parametro di superficie che è comunemente utilizzato è Rz, altezza massima del profilo, definita come somma delle altezze grande profilo di picchi (Rp) e il più grande profilo valle profondità (Rv) entro un tratto di campionamento, noto anche come picco valle (PV) (vedi fig. 2b). Secondo la sua definizione, Rz è un valore estremo caratteristico della topografia della superficie:
Rz=Rp+Rv
L’altro parametro di rugosità considerato in questo studio è RC, media aritmetica dei cinque maggiori picchi superficiali e dei cinque maggiori avvallamenti (Figura 2c).
Il materiale e i trattamenti eseguiti
Il materiale considerato nel presente lavoro è un acciaio 39NiCrMo3, sula quale sono state eseguite prove di trazione statiche e prove cicliche per ricavare le grandezze che ne definiscono il comportamento meccanico: si è ottenuto un modulo elastico di 195GPa, uno sforzo di snervamento ciclico di 360 MPa.Il materiale è stato sottoposto a due differenti trattamenti di pallinatura: il primo, indicato nel seguito come SP1, ha previsto un’intensità Almen pari a 5A, ottenuta con sfere di diametro pari a circa0.3 mmlanciate con una velocità di circa 30 m/s, il secondo (SP2) corrisponde a una intensità di 10 Almen, ottenuta con sfere
di 0.5 mm di diametro lanciate con una velocità di 80 m/s. In entrambi i casi la copertura è del 100%. Le sfere utilizzate sono di acciaio fuso e sono ottenute per atomizzazione.
Il modello a elementi finiti
Si è sviluppato un modello tridimensionale per simulare i molteplici impatti che definiscono il processo di pallinatura. Si è modellata una piastra piana nella cui parte centrale è localizzata la superficie sede degli impatti simulati. Le facce laterali del modello sono state circondate con i cosiddetti elementi infiniti, che evitano la riflessione delle onde elastiche che derivano dall’impatto delle sfere con la piastra. La piastra è stata modellata con più di 500000 elementi solidi esaedrici a otto nodi, integrazione ridotta (un solo punto di integrazione) e controllo dei modi di deformazione cosiddetti “a clessidra” (hourglass), che possono inficiare i risultati ottenuti. Il materiale è modellato Il modello costitutivo del materiale è quello con incrudimento non lineare di Chaboche (C=196823, g=501.9). Tale modello non considera l’effetto della velocità di deformazione sulla risposta del materiale, tuttavia, precedenti studi hanno mostrato la sua capacità di ben descrivere il fenomeno e di mostrare una soddisfacente corrispondenza con i risultati sperimentali.
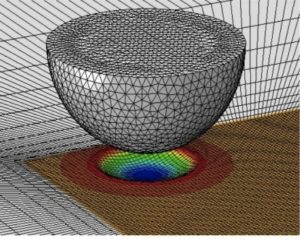
Le sfere sono state modellate a metà (pur rispettando i loro parametri inerziali), con elementi tetraedrici a 4 nodi, ipotizzando un materiale elastico lineare. Le simulazioni hanno considerato un angolo di impatto di 90° rispetto alla superficie della piastra. In Figura 3 è illustrato un dettaglio del modello della piastra e di una delle sfere che impatta. Il modello così sviluppato è stato utilizzato per eseguire numerose simulazioni al variare dei parametri di pallinatura, secondo un piano fattoriale che ha consentito di distinguere l’effetto dei differenti parametri (diametro delle sfere=0.3-0.45-0.6 mm, velocità delle sfere=30-60-90 m/s, copertura=100-200-300%) e di evidenziare la loro influenza sullo stato finale della superficie.
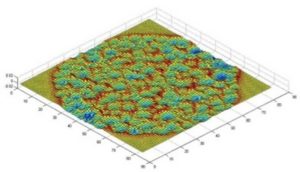
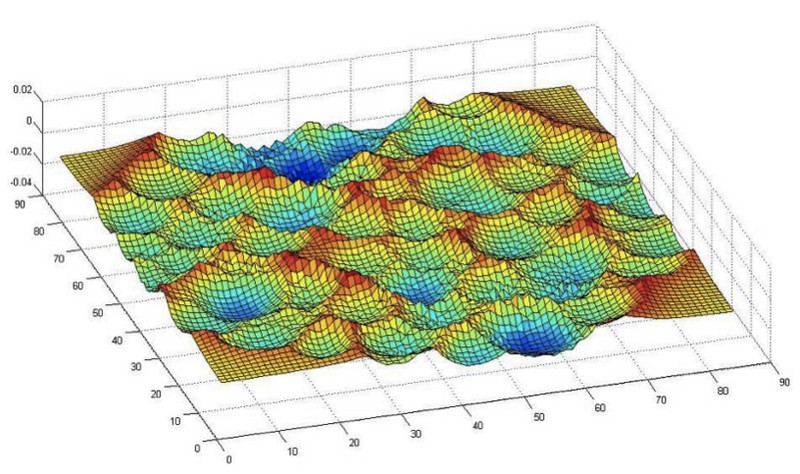
Nella Figura 4 sono illustrate le superfici deformate di tre delle simulazioni eseguite che si riferiscono a ben distinte condizioni di pallinatura.
Elaborazione dei risultati
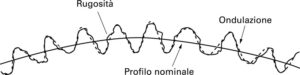
Una volta eseguite le simulazioni a elementi finiti è stato necessario elaborare i risultati in modo da ottenere dati utilizzabili per il calcolo dei parametri di rugosità in accordo con gli standard di riferimento (ISO 4287). Tale standard specifica termini, definizioni e parametri per la determinazione della finitura superficiale (rugosità, profilo primario, ondulazione).
Seguendo tale norma, il profilo superficiale è categorizzato in tre componenti: quelle ad alta frequenza definiscono la rugosità, quelle a media frequenza l’ondulamento e quelle bassa frequenza la geometria nominale (vedi Figura 5).
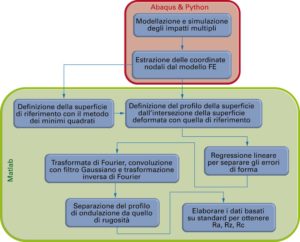
L’elaborazione die risultati delle analisi a elementi finiti per ottenere tali componenti è stata eseguita grazie allo sviluppo di una routine scritta in Python (che non viene descritta per non appesantire la trattazione e per limiti di spazio) e di una in Matlab, che hanno consentito di ricostruire la superficie deformata e di calcolare i diversi parametri caratterizzanti la superficie impattata. Il diagramma delle operazioni eseguite dalle routine è mostrato in Figura 6.
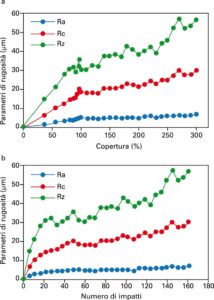
Risultati
L’evoluzione dei parametri di rugosità di una superficie pallinata in funzione della copertura/numero di impatti per le simulazioni relative a sfere con diametro pari a0.6 mm e velocità di 90 m/s è illustrati in Figura 6. Simili grafici sono stati ricavati per le altre condizioni di simulazione eseguite. Si nota che i diversi parametri di rugosità hanno lo stesso andamento, anche se presentano un tratto iniziale in cui hanno un aumento lineare con la copertura. Tuttavia, mentre Ra si stabilizza per valori di copertura superiori al 100%, Ra e Rc continuano ad aumentare linearmente, anche se con pendenza differente rispetto al primo tratto. Questa è un’indicazione d’interesse nell’impostazione dei parametri ottimali di pallinatura. Un’altra indicazione importante è che la rugosità aumenta con il diametro delle sfere utilizzate e con la loro velocità: il trend in questo caso è simile per i tre parametri e mostra, un aumento, a pari velocità e pari copertura, di circa il 50% raddoppiando il diametro della sfera e, a pari sfera e pari copertura, di circa il 100% raddoppiando la velocità.
Il confronto con i dati sperimentali a disposizione, riportato in Tabella 1, nella quale si riporta anche la rugosità dei provini non pallinati (NP), ha consentito di validare l’approccio proposto.
Conclusioni
La conoscenza della rugosità indotta dalla pallinatura già in fase di definizione del processo è un dato importante al fine della corretta impostazione dei parametri di trattamenti in funzione dell’applicazione del pezzo trattato. L’approccio sviluppato costituisce un utile strumento in tal senso, fornendo indicazioni accurate in tal senso e in accordo con i dati sperimentali di confronto a disposizione.
Un approfondimento del lavoro è in corso e mira a estendere l’applicabilità di quanto elaborato anche ad altre famiglie di leghe metalliche.
Bibliografia
[1] S. Siegmann, C.A. Brown, Surface texture correlations with tensile adhesive strength of thermally sprayed coatings using area-scale fractal analysis, in: 2nd United Thermal Spray Conference, Düsseldorf, D, 1999, pp. 355–360, ISBN/ISSN: 3-87155-653-X. [2] K. Dai, J. Villegas, Z. Stone, L. Shaw, Finite element modeling of the surface roughness of 5052 Al, Alloy subjected to a surface severe plastic deformation process, Acta Mater. 52 (2004) 5771–5782. [3] S. Bagheri, M. Guagliano, Review of shot peening processes to obtain nanocrystalline surfaces in metal alloys, Surf. Eng. 25 (2009) 3–14. [4] M. Klemenz, Th. Hochrainer, L. Delonnoy, V. Schulze, O. vohringer, P. Gumbsch, Similarity rules for the shot peening process based on finite element simulations, in: International Conference of Shot Peening ICSP, vol. 9, 2005, pp. 94–99. [5] H.Y. Miao, S. Larose, C. Perron, M. Lévesque, On the potential applications of a 3D random finite element model for the simulation of shot peening, Adv. Eng. Softw. 40 (10) (2009) 1023–1038. [6] S. Bagherifard, R. Ghelichi, M. Guagliano, A numerical model of severe shot peening (SSP) to predict the generation of a nanostructured surface layer of material, Surf. Coat. Technol. 204 (24) (2010) 4081–4090. [7] R. Clausen, J. Stangenberg, Roughness of shot-peened surfaces – definition and measurement, The 7th International Conference on Shot Peening ICSP7, Warsaw, Poland, 1999, pp. 69–77. [8] V. Baˇcová, D. Draganovskám, Analyses of the quality of blasted surfaces, Mater. Sci. 40 (1) (2004) 125–131. [9] J. Schmahling, F.A. Hamprecht, D.M.P. Hoffmann, A three-dimensional measure of surface roughness based on mathematical morphology, Int. J. Machine ToolManuf. 46 (2006) 1764–1769. [10] J. Raja, B. Muralikrishnan, Sh. Fu, Recent advances in separation of roughness, waviness and form, Precis. Eng. 26 (2002) 222–235.