Una nuova «industrializzazione di qualità». È questa secondo i consulenti di Roland Berger la più importante e concreta promessa che gli ecosistemi di produzione intelligente contrassegnati con l’etichetta di Industria 4.0 fanno oggi al settore manifatturiero. L’obiettivo alla portata del sistema economico-produttivo occidentale è, secondo la società attiva per i governi tedesco, italiano e francese, il recupero di competitività, valore aggiunto e occupazione a discapito dei concorrenti. Oggi i Paesi emergenti assorbono infatti il 40% della marginalità complessiva contro il 20% del 1991 e per continuare a giocare da protagonista l’Europa deve tornare a rappresentarne almeno il 20%, contro l’attuale 15, di qui al 2030. Per farlo saranno necessari investimenti che Roland Berger ha calcolato in 90 miliardi di euro annui per i prossimi 15 anni. E serve una direzione: ovvero una decisa accelerazione dell’integrazione delle tecnologie digitali con i processi industriali tradizionali. Il traguardo, fissato da Roland Berger alla fine del prossimo decennio, è un incremento dei posti di lavoro nel comparto, sino alla quota di 31 milioni contro i 25 milioni del 2011. Perché anziché sottrarre risorse umane alle fabbriche il rivoluzionario paradigma ne richiederà di nuove, tutte altamente specializzate. Lungi dall’essere un mero slogan la sigla Industria 4.0 fa riferimento alla quarta rivoluzione industriale, fondata sul concetto di Internet delle cose (Internet of things o Iot) e su macchine, manufatti e operatori che dialogano fra loro grazie ad ambienti di rete sempre più affidabili e performanti. Gli analisti della multinazionale della ricerca Frost & Sullivan hanno previsto che nel 2020 saranno ben 12 miliardi i dispositivi interconnessi, in ambito manifatturiero, in una logica di interfacciamento fra macchina e macchina (Machine to machine o M2M). Oggetti a loro volta capaci di dialogare fra loro e trasmettere informazioni potrebbero dare la spinta a inedite forme di servizio, per un business atteso sul breve-medio periodo a un’impennata annua del 20%.
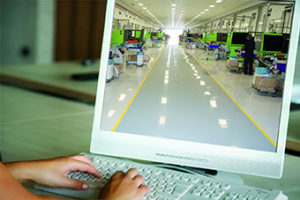
Giunta in tempi relativamente recenti sulle prime pagine, l’idea dell’Industria 4.0 viene in realtà da lontano, essendo sorta nel 2012 in seno alle istituzioni centrali tedesche, in cerca di linee guida con le quali garantire un futuro (e una posizione di leadership) alla produzione locale. Oggi il progetto Industrie 4.0 è componente-chiave dei Future project inclusi nella High tech strategy approntata a Berlino; e dal 2014 anche l’Olanda ha messo a punto una roadmap specifica. Ma per Confindustria Servizi Innovativi e Tecnologici (Csit) l’Unione europea e il governo italiano devono puntare «allo sviluppo di una manifattura 4.0 che permetta di rilanciare la crescita economica, creare occupazione e accompagnare il manifatturiero europeo a creare il 20% del Prodotto interno lordo entro il 2020». Già familiarizzate con soluzioni tecnologiche come big data e il cloud computing sono, nelle stime di Csit, ben 800 mila aziende nazionali, capaci di generare un fatturato totale da 255 miliardi e un valore aggiunto da 110 miliardi: «Imprese che investono nella digitalizzazione della produzione», ha scritto Confindustria in una nota, «e che possono fare il salto di qualità verso un sistema manifatturiero che integri progressivamente servizi, Internet, tecnologie digitali e informatiche nella produzione industriale e che consenta di recuperare slancio e competitività sui mercati mondiali».
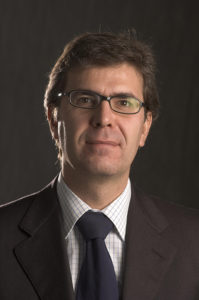
«Così il dato diventa protagonista»
Per il professor Marco Taisch, docente di Advanced and Sustainable Manufacturing presso il dipartimento di Ingegneria gestionale del Politecnico di Milano, l’Italia ha dinanzi a sé opportunità enormi, ma anche qualche pericolo. Sua opinione è infatti che le imprese più grandi e strutturate siano già pronte ad affrontare la trasformazione in virtù del loro bagaglio di conoscenze e dei loro budget; e che le più piccole invece potrebbero trovarsi ad arrancare. Il rischio è allora quello del possibile allargamento del divario digitale che le separa. Mentre la buona notizia è che molte delle soluzioni Ict considerate mission critical per il concretizzarsi dell’Industria 4.0 sono disponibili anche senza investimenti stratosferici e possono essere sviluppate a misura di Pmi. Inevitabile, al contrario, è un radicale cambio di passo e mentalità. «Con il marchio di Industria 4.0 si è etichettata la nuova tappa di un percorso già iniziato con l’ingresso dei personal computer nelle fabbriche», ha detto Taisch, «ma la vera novità è in questo caso rappresentata dalla centralità di Internet e dal suo connubio con altre tecnologie: questo è un elemento di evoluzione essenziale». Fra sensori e chip parlanti come quelli in radiofrequenza (Rfid) potenzialmente applicabili a basso costo su manufatti di qualsiasi natura, «ora il dato è protagonista e le informazioni disponibili sempre, ovunque e soprattutto in tempo reale servono», secondo Taisch, «a migliorare le procedure decisionali e renderle più rapide, grazie a una più efficace e approfondita conoscenza dei processi». Insomma, se sino a ora il manufacturing procedeva a una determinata andatura perché la sua visibilità era limitata, nella riflessione del docente milanese, adesso la visuale è nitida e spingere sull’acceleratore è tutto fuorché un azzardo. «Al di là degli slogan», ha proseguito Taisch, «siamo alle prese con un nuovo modello e con una rivoluzione a 360 gradi. L’Internet delle cose implica prodotti intelligenti e sistemi di produzione che utilizzano l’informatica a loro vantaggio in un’ottica di smart manufacturing. In ambito consumer l’esempio è dato da articoli come i frigoriferi intelligenti o dall’intelligenza di bordo delle auto, ormai trasformatesi in veri oggetti meccatronici. Con Holonix, spin off del Politecnico, realizziamo sensori per la nautica, utili a monitorare lo stato di salute e le performance delle barche a vela, autentici gioiellini da oltre 5 milioni di euro l’uno. Ma la stessa cosa possiamo farla per una ‘semplice’ macchina utensile».
Nei reparti e nelle attrezzerie questo si traduce nell’accessibilità di informazioni in real time sulle attività degli impianti che stanno costruendo un determinato tipo di prodotto, con la possibilità di intervenire in corso d’opera sulle loro caratteristiche e modificarle in maniera quasi istantanea. «Tramite apposite applicazioni», ha detto Taisch, «si potranno ottenere dettagli sul funzionamento di una macchina e la sua eventuale necessità di manutenzione, anticipando la chiamata o la visita del personale di assistenza. Tornando a Holonix, riesce a rilevare velocità e posizione degli scafi mediante una scatola nera creata ad hoc. Ma le architetture di rete permettono a chi le noleggia di scambiare con altri notizie sui luoghi di attracco. E anche questo è un servizio aggiuntivo a valore». Alla luce di queste considerazioni, gli scenari possibili per i costruttori sono molti, e affascinanti: «Già oggi in fabbrica il flusso delle informazioni è digitalizzato», ha osservato Taisch, «ma l’input iniziale è gestito manualmente dagli operatori via terminale. Nel prossimo futuro i dati vivranno e nasceranno direttamente online. È l’automazione cognitiva, in grado di far sì che con informazioni e pc o tablet e tecnologie indossabili si abbiano dati in real time che aiutano a svolgere le operazioni, riducendo i margini di errore ed elevando al tempo stesso il valore delle risorse umane. I ruoli cambiano; e i tornitori del futuro sono ingegneri che sovrintendono ai processi stando in un ufficio».
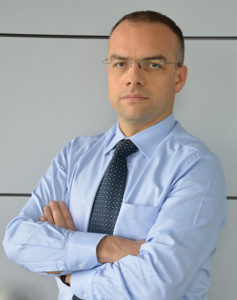
Punto di partenza: l’interconnessione di processi, prodotti, operatori
A calare il concetto di Industrie 4.0 nella realtà italiana e segnatamente in quella degli stampisti ha provveduto Marino Crippa, project leader Industry 4.0 e responsabile vendite per il canale distribuzione ed end user di Bosch Rexroth. La multinazionale tedesca, specializzata in controlli e azionamenti elettrici, oleodinamici, tecnica lineare e di montaggio, rappresenta un esempio concreto di come la filosofia della digitalizzazione possa tradursi in realtà, visto che gestisce fra gli altri 5.000 macchine e 11 impianti nel mondo connessi in cloud. «L’Industry 4.0», ha detto, «è una evoluzione dell’automazione: le tecnologie abilitanti sono mature e ora si tratta di ridisegnare approcci e processi alla luce di paradigmi nuovi, collegando i prodotti all’operatore che li realizza e alle linee di produzione. Tutto questo senza dimenticare che il prodotto realizzato e venduto può dare informazioni utili per produzioni future. I costruttori di automobili, per esempio, grazie ai dati ricevuti dal campo, riprogettano pezzi che scoprono essere stati sovradimensionati, con impatti diretti sull’intera ottimizzazione del ciclo di vita del prodotto». «Pensando alla lavorazione degli stampi», ha aggiunto Crippa, «le tematiche critiche possono essere la gestione di centri di lavoro o delle isole di produzione, la progettazione e prototipazione con l’obiettivo di ridurne i tempi. Gli ambienti 4.0 hanno alla base l’utilizzo dei dati, spesso già disponibili, per ridurre i tempi di decisione e, per esempio, attuare strategie di manutenzione predittiva atte a ridurre i tempi di fermo macchina. Il tema è quindi quello della raccolta e dell’utilizzo dei dati oltre che, ovviamente, equipaggiare le macchine con componenti che nativamente siano in grado di produrre dati. Oggi è ritenuto assodato che un centro di lavoro esegua le lavorazioni per le quali è stato progettato con le massime performance. Richiedere invece che fornisca i dati e la connettività per ottimizzare l’intero processo produttivo, è qualcosa che ancora non accade di frequente».
Alla più recente edizione della fiera Emo è stato presentato un centro di lavoro il cui punto di forza era la possibilità di accedere ai dati dei componenti macchina e renderli fruibili all’operatore in remoto. Per esempio, la misurazione mediante sensori di posizione delle distanze coperte dagli assi, con informazioni precise e disponibili su cloud, sui tablet dei manutentori o nel database aziendale. «L’usura a fatica degli assi diventa così un dettaglio noto e la loro sostituzione o manutenzione diventa programmabile con precisione», ha spiegato Marino Crippa. «Tutte evidenze che rendono possibile predeterminare con pochi margini di errore i tempi di sostituzione dei cuscinetti».
Più numerosi sono gli assi, più numerosi saranno anche i benefici: «Si può immaginare un capannone popolato di centri di lavoro interconnessi e nel quale lo stato di avanzamento delle commesse può essere controllato in tempo reale, anche a distanza, attraverso per esempio, i cellulari che ognuno di noi ha in tasca».
Per Bosch Rexroth la logica dell’Industry 4.0 è da tempo realtà, vista la presenza fitta in portfolio di componenti, motori e valvole forniti di interfaccia digitale che semplifica l’estrazione dei dati e la loro disponibilità, agevolando al tempo stesso i processi decisionali. L’impressione di Crippa è che «rispetto alla Germania la velocità evolutiva delle imprese di casa nostra segna un po’ il passo» ma il 2016 può rivelarsi un anno importante. «Non mancano i progetti», ha concluso, «ma che la tendenza possa consolidarsi è ancora tutto da vedere. I temi sono la flessibilità della produzione e il time to market, insieme alla necessità di creare soluzioni personalizzate. Questi fattori costringeranno le imprese ad accelerare i tempi. La filosofia dell’Industry 4.0 può dare maggiore efficienza e garantire migliori performance alle aziende senza però imporre loro un rinnovamento radicale. Molti impianti vecchi, ma non per questo a fine vita, potrebbero essere oggetto di revamping anche perché uno fra gli aspetti positivi del nuovo ambiente è il suo essere basato su tecnologie mature in grado di portare grandi benefici, a fronte di costi decrescenti. Questo vale per la trasmissione dei dati e anche per la loro messa in sicurezza, aspetto critico e sempre più rilevante anche in ambito industriale».
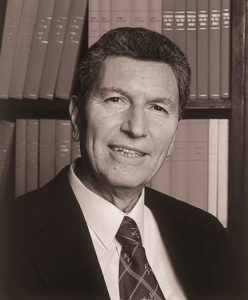
Una Fabbrica digitale alla portata delle Pmi
Di Industria 4.0 si è pronti a parlare anche di Mecspe, fiera internazionale della meccanica e della subfornitura in programma a Parma fra il 17 e il 19 marzo prossimi, con la presentazione di quattro casi specifici, esempio delle diverse facce della digitalizzazione. «Ho cercato di dare a questa fase evolutiva una connotazione precisa, a cominciare dal nome, che vuole caratterizzare un modello italiano», ha detto a Stampi il direttore del salone Fabbrica digitale – Oltre l’automazione, l’ingegner Michele Rossi, «nella convinzione che l’officina tradizionale debba corredarsi di strumenti digitali che si calino nella sua quotidiana realtà con lo scopo di una gestione più efficace e tempestiva dei dati, in tempo reale. Con un più puntuale ed efficiente scambio dei dati le attrezzerie vanno oltre quell’automazione di tipo classico che è associata comunemente alle macchine e agli impianti.
Significa dare all’automazione un significato più elevato, quindi una gestione delle intelligenze che risiedono nelle macchine e un completo controllo dei processi e delle attività.».
Per Rossi «la Fabbrica digitale è un puzzle multi-tecnologico dagli aspetti per alcuni versi futuristici ma ai quali bisogna iniziare a pensare. Mecspe può stimolare la riflessione». Ognuna delle case history presentate avrà «un proprio taglio» perché nel parere di Rossi «la realtà della progettazione e della produzione 4.0 è sfaccettata». «Quello che conta», ha detto, «è la completa integrazione delle fasi e dei processi in un unico ambito di supervisione, in perfetta adesione alla realtà di ogni singola impresa e al suo rapporto con clienti e committenti. I subfornitori devono rispondere alle esigenze di committenti diversi e sono sempre più chiamati a collaborare in condivisione di dati informazioni già nelle prime fasi di sviluppo prodotto. Questo richiede strutture efficienti per lo scambio e la condivisione dei dati critici e la capacità di assicurare un efficace controllo di processo e una tracciabilità, in linea con le richieste di una committenza che segue e valuta anche gli iter interni».
Mecspe traccia la strada ma è difficile dire quanti fra gli imprenditori italiani riusciranno a comprendere da subito la necessità di incamminarvisi. Il rischio di futura emarginazione è forte.
Certo è che il salone Fabbrica digitale – Oltre l’automazione continuerà a tracciare il percorso anche nelle edizioni a venire, nel tentativo di illuminare anche quella maggioranza di aziende che ritiene questo processo evolutivo un’eventualità ancora remota nel tempo oppure al di là delle proprie possibilità. «Gli esempi di avanguardia», ha concluso Rossi, «non mancano, aziende di eccellenza hanno già iniziato qualche anno fa il percorso, ma se il nostro Paese è in parziale ritardo ciò si deve anche a un certo conservatorismo delle Pmi di natura strettamente padronale, dunque alla mancanza di una cultura manageriale diffusa. Per passare alla digitalizzazione 4.0 serve comunque un salto in avanti di tutte le risorse umane coinvolte nella fabbrica. Per andare oltre l’automazione servono macchine, impianti, automazione, componenti hardware e software intelligenti, ma in primo luogo servono gli uomini e una maggior collaborazione e condivisione dei problemi fra le unità funzionali stesse. Necessario è creare uno spirito di collaborazione interno che abolisca le chiusure. Questa è la grande sfida della fabbrica digitale, che richiede professionalità preparate dal punto di vista delle competenze ma anche delle capacità relazionali».
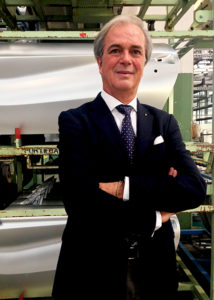
delegato (Chief executive officer)
di Fontana Group
«Da sempre orientati alla digitalizzazione»
Intervista a Walter Fontana, amministratore delegato (Chief executive officer) di Fontana Group.
Come si declina l’idea di Industria 4.0 presso un’azienda come la Vostra, dottor Fontana?
Se parliamo di digitalizzazione dei processi e dei flussi di informazione, il gruppo Fontana è stato, fra gli stampisti italiani e non solo, un autentico pioniere. Il concetto di interconnessione fra dati e macchine è già radicato nella nostra attività sin dall’introduzione dei primi sistemi Cad-Cam e delle tecnologie Ict alla fine degli anni Settanta, col passaggio delle informazioni dagli uffici tecnici alle macchine. Abbiamo attraversato le fasi della digitalizzazione manuale lettera-per-lettera e quella delle bande perforate, sino all’avvento dei controlli numerici. Oltre 35 anni fa trasmettevamo i dati per la fresatura di superficie di una parabola da un computer Olivetti a un controllo numerico, sempre made in Italy. E il nostro stabilimento di Calolziocorte (Lecco) è stato cablato con cavi in fibra ottica già nel 1991. Il cablaggio e la sua messa in sicurezza, anche dal punto di vista elettromagnetico, sono stati vitali per garantire la trasmissione dei programmi e dei dati matematici per la fresatura e l’elettroerosione.
Che cosa è cambiato con la Vostra espansione all’estero e come l’Ict vi ha aiutato a gestirla?
La disponibilità di dati protetti su una intranet aziendale è stata fondamentale in occasione della nostra apertura in Turchia e per fare fronte alla conseguente necessità di connettere tutte le fabbriche fra loro. L’essere riusciti a condividere con i nostri impianti turchi e romeni i progetti in corso in Italia e le relative modifiche, senza possibilità d’errore, è stato un fattore di successo che ci ha consentito di ricevere il Premio per l’innovazione di Confindustria nel 2008. Ma abbiamo anche ottenuto riconoscimenti dal ministero per l’Industria grazie alle capacità dimostrate nella divulgazione della conoscenza; e da quello della Ricerca per l’innovazione dei processi di condivisione delle conoscenze. L’Ict è decisiva per gestire il sapere, in qualunque area del mondo.
Come si svolge il dialogo con le altre Vostre sedi nel mondo e con i Vostri partner industriali?
Con i software di simulazione e di progettazione solida, che Fontana ha adottato già nel 1992, sviluppiamo la certificazione di fattibilità di ciascun pezzo. I dati per passare all’ingegnerizzazione, alla progettazione volumetrica e ai processi Cam viaggiano su una rete Lan in fibra ottica anche verso Turchia e Romania. Utilizziamo Internet dal 1996 ed è da allora uno strumento strategico per il dialogo con le fonderie nostre partner. Ma se i dati sono cruciali per gli ambienti 4.0, allora Fontana è sempre stata all’avanguardia, già anni fa si gestivano dati con un volume da ben otto terabyte. Il nostro cervello è garantito da un backup giornaliero e mensile gestito come quello delle banche. E messo in cassaforte.
Molto più recente è stato invece il passaggio alle architetture cloud: vorrebbe parlarcene?
L’implementazione, così come è accaduto per altre innovazioni recenti, è stata curata dai miei figli, entrambi in azienda ed entrambi in possesso di esperienze di studio e professionali all’estero. La nuvola ci permette di condividere commesse e modifiche in tempo reale con le nostre sedi estere ed è una naturale estensione del nostro modo di fare business. Siamo attenti alla protezione delle informazioni perché lavorando per il settore automotive su componenti di veicoli destinati a uscire fra diversi anni la sicurezza è un elemento estremamente sensibile. Negli ultimi sei mesi abbiamo proceduto con l’aiuto di consulenti del mondo Ibm a una analisi dettagliata del nostro intero sistema informativo per valutare sia le risorse in dotazione sia gli interventi possibili di ottimizzazione. A conferma della centralità che il dato riveste per Fontana, vi abbiamo investito pesantemente. Dobbiamo sempre restare un millimetro avanti rispetto al resto del mercato e l’hi-tech ci permette di farlo, aumentando numero e importanza dei clienti, e condividendo e tutelando il nostro know-how.
La Vostra vocazione all’innovazione è compresa anche dai collaboratori e dai subfornitori?
A volte abbiamo dovuto in certa misura pagare dazio alla nostra natura innovativa e con i terzisti o le piccole e piccolissimi imprese le incomprensioni non sono mancate. Certo, tutto cambia se si guarda invece ai clienti, molto più strutturati e preparati, anche perché spesso di grandi dimensioni. In più, in Paesi come la Romania abbiamo inizialmente scontato le carenze di ordine infrastrutturale, ma alla fine le nostre strategie hanno dato buoni frutti. Siamo da sempre una società 4.0, da 25 anni il nostro mondo è digitalizzato e questo implica dei problemi di sicurezza, gestione, interpretazione e trasmissione dei dati. E se si parlasse poi di una Manifattura 5.0, ci saremo ancora.
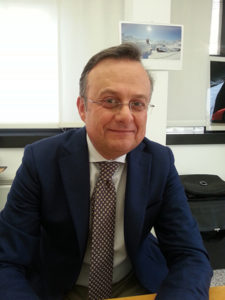
vendite di Engel
«Un’evoluzione che aumenta le complessità e riesce a risolverle»
Intervista a Maurizio Ferrari, responsabile vendite di Engel, produttore tedesco di sistemi e soluzioni per l’iniezione plastica con nove siti produttivi e un fatturato 2014-2015 da 1,07 miliardi.
Che cosa indica il concetto di Industry 4.0 per Lei e per la ENGEL, signor Ferrari?
Indica la quarta rivoluzione industriale, anche se riterrei più appropriato parlare di un’evoluzione dell’industria. Le precedenti tre rivoluzioni hanno portato con sé un incremento di produttività ma anche una maggiore complessità e la quarta non fa eccezione. La differenza è che essa ha in sé le soluzioni per rispondere alla complessità e gestirla. Altri benefici sono visibili dal punto di vista della flessibilità, che con l’Industria 4.0, per la prima volta in oltre 200 anni, potrà essere condotta ben oltre il livello del puro artigianato manuale. Ma sopra ogni altra cosa Industry 4.0 è a mio avviso un’opportunità pressoché unica della quale vogliamo cogliere i benefici, insieme ai clienti.
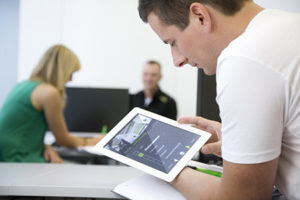
interconnessi, in ambito manifatturiero, in
una logica di interfacciamento fra macchina
e macchina.
Come contate di poter cavalcare quest’onda innovativa di digitalizzazione e interconnessione?
Le istanze dell’Industria 4.0 sono note a Engel da tempo e sono pratica quotidiana in varie aree. La novità è che con il marchio Inject 4.0 stiamo offrendo come pacchetto completo i prodotti e i servizi prima veicolati singolarmente insieme a nuovi sviluppi che abilitano il passaggio alle smart factory. E la fabbrica intelligente è un luogo in cui i processi manifatturieri si ottimizzano, da sé, in modo continuo, grazie al networking e all’integrazione dei sistemi produttivi; al sistematico sfruttamento dei dati di processo e produzione; all’uso di sistemi di produzione adattativi. L’obiettivo è aiutare i clienti a ottimizzare i loro processi per ottenere un aumento significativo della produttività, della qualità e della flessibilità. La fabbrica intelligente fa leva su tre fattori-chiave: macchine smart che potenziano la capacità dei processi e la qualità con sistemi de-centralizzati e auto-adattativi; la smart production in grado di assicurare alti livelli di produttività grazie all’integrazione verticale e orizzontale dei dati; infine gli smart service. Questi migliorano la disponibilità delle macchine in modo efficiente e rapido, grazie anche al ricorso a strumenti per la manutenzione in remoto. Proponiamo una serie di soluzioni modulari mirate per ciascuna di queste voci: iQ Weight Control e iQ Clamp Control sono software di monitoraggio continuo e reimpostazione automatica dei parametri di qualità (smart machine); Engel E-Factory Mes (Manufacturing Execution System) è pensato per le specifiche esigenze della lavorazione plastica con un ottimo livello di integrazione verticale e orizzontale dei dati sino alle singole cavità (smart production) ed Engel E-Connect per un rapido supporto online e la gestione dell’assistenza in remoto, in tema di servizi intelligenti.
Qual è a Suo avviso il livello di interesse che i clienti mostrano nei confronti dell’Industry 4.0?
Nel settore della plastica si tratta di una tendenza importante e i dialoghi intercorsi ad alcune recenti fiere circa l’utilizzo sistematico dei dati, il networking e i sistemi di assistenza intelligenti nel contesto delle nostre soluzioni Inject 4.0 lo confermano. Gli utenti vogliono risposte alle loro domande e strumenti con cui fare fronte a quella che rappresenta sia un’opportunità sia una sfida. Oggi si è in una fase di avvio, i dubbi e le incomprensioni sono numerosi, ma il ricorso a un modello modulare come quello proposto da Engel è un vantaggio. Permette alle aziende di procedere gradualmente, partendo da piccole soluzioni specifiche per ampliarle poi nel tempo.
Ritiene che anche in Italia il settore degli stampi plastica si stia mostrando sensibile al tema?
L’Italia è fra i nostri principali mercati nell’Unione europea ed Engel è stata la prima azienda straniera ad aprirvi nel 1989 una filiale diretta che oggi conta 32 dipendenti e otto agenti, per 5.000 macchine installate delle quali si prende cura un team di 22 tecnici specialisti. E anche in Italia il concetto di Industria 4.0 sta prendendo piede nel segmento della lavorazione plastica, anche se al momento sono i produttori Oem di area automotive e gli stampi tecnici ad averlo recepito come prioritario. Molti però hanno già interfacciato le loro macchine con i computer centrali e i sistemi Erp grazie al nostro E-Factory per avere una panoramica completa della produzione e dei processi di business. Il risultato è la conquista di una maggiore efficienza, una miglior qualità, un aumento di produttività.
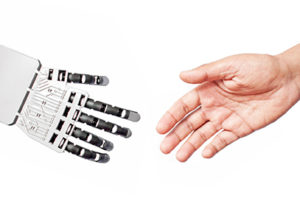
Qual è, in questo contesto, l’importanza di tematiche come la protezione dei dati e il training?
La definizione di standard di sicurezza per lo scambio dei dati è una delle più grandi sfide che lo Industry 4.0 ci pone e su questo stiamo lavorando alacremente come azienda e al livello delle associazioni industriali di settore. Ma il tema porta con sé anche qualche fraintendimento. Va chiarito infatti che solo gli smart service impongono a un fornitore l’accesso a dati specifici dei clienti, rilasciati dai clienti per scopi altrettanto precisi. Produzioni e macchine intelligenti si basano invece su dati che pertengono alla sfera di ogni singolo trasformatore e non devono esser condivisi. Quanto alla formazione, Engel ha già messo a punto programmi dedicati alle soluzioni Inject 4.0.
Contate di cooperare con altri partner nella messa a punto di offerte mirate all’Industry 4.0?
Nessuna azienda può sfruttarne il potenziale autentico da sola: l’Industria 4.0 coinvolge ogni processo di business e produzione e questo è un tema del quale discutiamo con clienti e alleati. È anche grazie alla cooperazione coi partner che offriamo soluzioni altamente integrate e diversificate: macchine, automazione e tecnologie di processo, ma anche stampi e periferiche.