Oggigiorno la richiesta di superfici piane e curve in grado di trasmette forze per attrito è in continuo aumento. Un loro impiego tipico si ha, ad esempio, nelle trasmissioni a ingranaggi dove si è alla continua ricerca di sempre nuove soluzioni economicamente vantaggiose e, al contempo, funzionali e con buoni fattori di sicurezza. Soluzioni come layer diamantati, rivestimenti diamantati e accoppiamenti di forma, tutte relativamente costose, sono state ampiamente studiate negli anni. Le caratteristiche funzionali necessarie per questo tipo di accoppiamento possono essere ottenute mediante tecnologia laser che, grazie all’elevata densità di potenza del fascio, risulta in grado di modificare la superficie. La lavorazione delle superfici tramite laser è ormai una tecnica assodata. Questo studio mostrerà nel dettaglio il laser e i rispettivi aspetti tecnologici, tribologici, senza tralasciare alcuni esempi di connessioni ad attrito. In estrema sintesi, come arrivare a produrre in modo snello anche pezzi piuttosto complessi.
Layout delle superfici di contatto tramite adesione
La produzione di superfici per connessioni ad attrito fa sempre più spesso ricorso alla tecnologia basata sul laser. Le superfici vengono lavorate in modo da ottenere microgeometrie ottimizzate in grado di trasmettere elevati carichi contenendo al contempo i costi di produzione. L’obiettivo è quello di riuscire a ottenere un aumento dei carichi trasmissibili agendo sul coefficiente di attrito. Il sistema dovrà operare assicurando che il contatto rimanga di tipo statico, ovvero che non vi sia moto relativo tra le parti. Come mostra la Figura 1, il massimo del coefficiente di attrito statico va aumentato il più possibile. Il controllo del tipo di attrito è stato fatto su un banco prova apposito attraverso test specifici ed ha permesso di individuare il valore del coefficiente appena prima dell’inizio dello scorrimento.
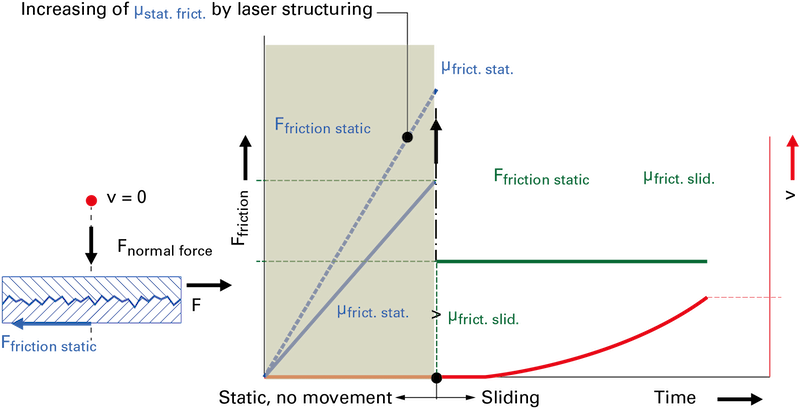
Le principali caratteristiche del sistema ad attrito adesivo sono mostrate in Figura 2. Strutture lavorate ed indurite sono confrontate direttamente con superficie lisce sottoposte ad un carico di 80 kN per 60 secondi fino ad un angolo di torsione di 4°. La curva di coppia è presa come termine di confronto. Le aree di contatto (di = 15 mm, da = 30 mm) sono pulite e non lubrificate. Nel passaggio tra contatto adesivo e radente si ha il massimo nel valore di adesione. Sono state testate due strutture con profili differenti: 8 micron (V1) e 15 micron (V2). Si è poi provata una terza struttura (V3, 15 micron).
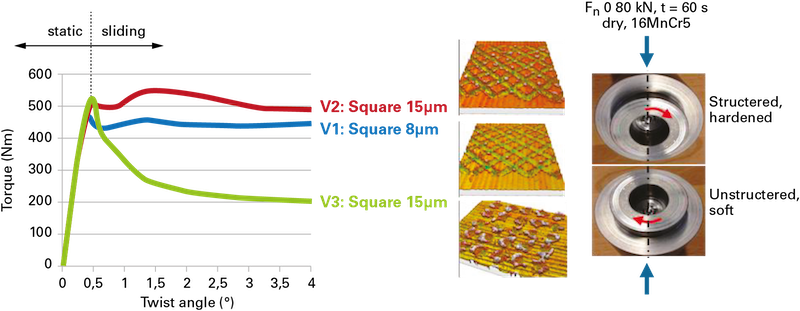
I test di torsione permettono di avere un confronto quantitativo diretto tra le differenti soluzioni. Differenti strutture possono così essere confrontate ed è possibile una loro ottimizzazione. Le misure potrebbero essere fatte, anziché su provini specifici, anche sul componente finale. Ogni superficie funzionale ha potenzialmente una forma differente con dei contorni specifici che possono influenzare la capacità di trasmettere carico. Tipicamente la superficie lavorata viene premuta contro una superficie non lavorata. In questo contesto sono state testate differenti trame superficiali ottenute mediante lavorazione laser. Queste permettono di aumentare il coefficiente di attrito. Al di là delle elevate caratteristiche meccaniche e della densità strutturale, è la durezza della superficie a giocare il ruolo fondamentale. A causa della rapida esposizione ad una fonte di calore (laser), si ottiene una modifica della durezza superficiale. Il rapido raffreddamento porta ad avere una struttura martensitica. In funzione della composizione chimica del materiale, si possono ottenere valori di durezza differenti. Oltre al test di torsione, è possibile effettuare anche test di taglio.
Le immagini SEM (Figura 3) mostrano differenti rugosità. La struttura può (a) mostrare solamente picchi senza valli al di sotto della quota nominale. Questo si ha quando il materiale viene fuso in modo uniforme e si ha una solidificazione omogenea.
Vi sono casi in cui le linee della struttura sono equidistanti e parzialmente sovrapposte (b). Le strutture (a) e (b) sono ideali per la trasmissione della coppia nei collegamenti forzati (albero-mozzo). Le linee della struttura sono ortogonali e tangenziali alla direzione del carico. Tra le creste (c) spesso si hanno valli causate dal trasferimento del materiale.
Questo tipo di struttura è caratterizzato da meandri profondi con micro-bave laterali. Queste giocano un ruolo importante nella trasmissione della coppia negli accoppiamenti frontali. Il profilo (d) mostra una struttura squamosa con micro-recessi. È indicata per l’accoppiamento di materiali a substrati differenti.
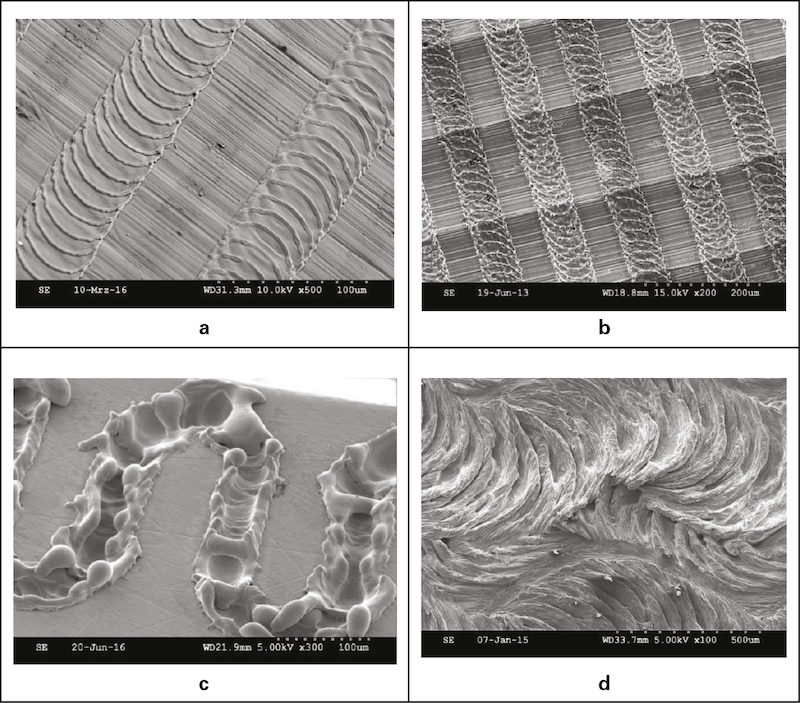
La creazione di trame superficiali rappresenta un metodo alternativo a soluzioni autobloccanti o a collegamenti ad attrito con layer diamantato interposto. L’adesione ottenibile dipende dall’altezza delle asperità, dalla geometria della trama, dalle proprietà della struttura martensitica, dalle forze normali e dalla presenza o meno di lubrificante. Il valore del coefficiente di attrito per superfici non trattate oscilla tra 0.05 e 0.15 mentre nel caso di lavorazione può aumentare fino a 0.6 – 0.9. Tipicamente però l’utilizzatore è più attento alla funzionalità del componente che non al valore del coefficiente di attrito.
La Figura 4 mostra differenti esempi di connessione soggetti a torsione. Un accoppiamento per interferenza (a) di una camma sul relativo albero in cui una superficie viene lavorata mediante laser risulta essere una soluzione efficace per una produzione in serie. Una trama superficiale ottenuta mediante tecnologia laser è di più facile realizzazione rispetto a una godronatura lavorata di broccia. Nell’esempio (b) sono collegate due superfici tramite morsetto. Ogni altro modo di collegamento risulterebbe più costoso. In questo modo è possibile realizzare qualsiasi tipo di accoppiamento per interferenza o di forma mediante superfici lavorate laser a elevato attrito. È ad esempio possibile migliorare gli accoppiamenti conici. La lavorazione del piede di biella assicura invece un esempio di fissaggio dell’anello esterno di un cuscinetto. Nella produzione convenzionale, l’attrito necessario è garantito grazie a lavorazioni di levigatura grossolane. Grazie alla tecnologia laser, invece, si vanno a lavorare aree localizzate aggiungendovi un’opportuna trama superficiale.
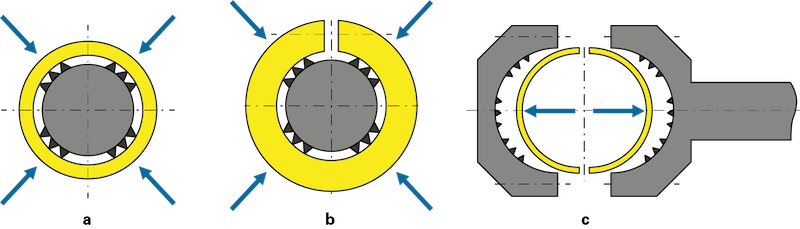
In linea di principio è possibile aggiungere una trama sia sulla superficie esterna dell’albero che sulla sede del foro. Sebbene sia più semplice lavorare una superficie esterna, è fondamentale considerare la durezza superficiale dei due materiali accoppiati. Pertanto, potrà essere lavorata la camma indurita o l’albero temprato. La scelta andrà fatta in modo tale che la rugosità indotta tramite laser riesca a penetrare il materiale tenero con sui si accoppia.
Inoltre, bisogna assicurare che la trama superficiale non venga danneggiata eccessivamente dallo scorrimento in fase di montaggio. Le superfici andrebbero assemblate con soli movimenti normali alle superfici stesse. Un gioco sufficiente o un morsetto apribile sono accorgimenti utili.
Le superfici a contatto dovrebbero lavorare preferibilmente a secco e in assenza di grasso. Questo permette di massimizzare la capacità di carico della connessione.
Un’altra categoria di connessioni per attrito è rappresentata dagli accoppiamenti piani come mostrato in Figura 5. La superficie viene lavorata (a) in modo tale da favorire un auto-allineamento. In questo modo è possibile evitare l’impiego di costose soluzioni aventi stessa funzione o inserti diamantati o interlayer al silicio per aumentare il coefficiente di attrito.
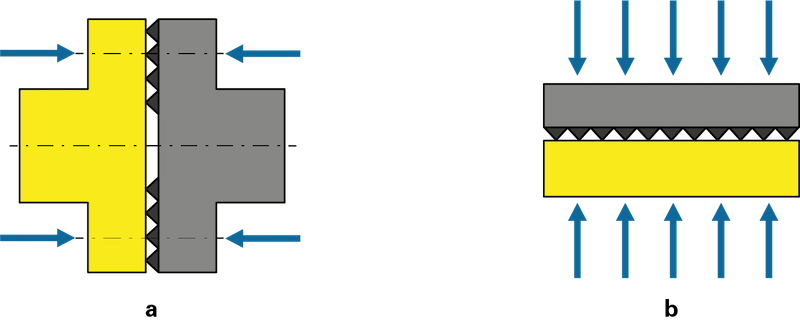
Questa soluzione può essere favorevolmente impiegata in applicazioni automotive. Le connessioni tipo (b) possono anche essere sfruttate per stabilizzare il posizionamento dei componenti in fase di montaggio.