Inaugurata la macchina per produzione additiva Laserdyne 795 di Prima Additive presso la centrale Enel di Santa Barbara.
Il macchinario, sviluppato da Prima Additive, è ora in funzione e consentirà a Enel di produrre e riparare componenti metallici destinati al settore della produzione energetica
A Cavriglia, presso la sede di Ingegneria e Supporto Tecnico Enel Produzione di Santa Barbara, Enel e Prima Additive hanno inaugurato ufficialmente la nuova Laserdyne® 795 installata presso la centrale, che consentirà di produrre e riparare componenti metallici.
Laserdyne® 795 è un macchinario con tecnologia Laser Metal Deposition, sviluppato e personalizzato da Prima Additive in collaborazione con Enel, basandosi sulle esigenze del settore della produzione di energia. La scelta di Enel è ricaduta sulla tecnologia direct energy deposition per le possibilità che offre a livello sia di produzione, sia di riparazione. Questo tipo di applicazione permette di ridurre i magazzini, limitare i tempi di fermo di un impianto o parti di impianto e di avere un risparmio per la riparazione dello stesso componente.
A determinare la scelta sono stati casi di studio legati al ruolo che un efficientamento dei componenti e delle parti di ricambio degli impianti energetici riveste nell’efficienza e disponibilità degli stessi, oltre a fattori come reperibilità, numerosità, giacenza media, valore economico e tipologie di danneggiamento.
Questo innovativo macchinario, unitamente alle competenze in ambito metallurgico e di testing presenti presso la centrale di Cavriglia, nonché a quelle di design, simulazione ed esercizio e manutenzione impianti, costituirà una nuova e concreta opportunità per l’attività di Enel Produzione in Italia e nel mondo è per le altre società del Gruppo Enel, contribuendo all’eccellenza in termini di innovazione e tecnologia.
In sostanza, questo strumento, abbracciando i principali concetti di Circular Economy, Industria 4.0 e sostenibilità, permette sia di eseguire riparazioni e revamping su componenti di impianto danneggiati sia di creare forme complesse e re-ingegnerizzate.
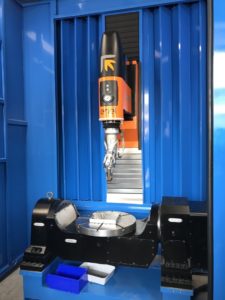
Tra le caratteristiche principali della Laserdyne® 795 vi è la testa laser BeamDirector® a 5 assi, abbinata ad un roto-tilting table, al fine di consentire la realizzazione di parti, utilizzando fino a 7 gradi di libertà. Questo sistema rende possibili due modalità di deposition: la prima prevede la rotazione del pezzo durante la lavorazione, mentre la seconda prevede il movimento della testa laser lungo l’intero profilo dell’elemento. L’area di lavoro è di 1000x1000x1000 mm, uno spazio ideale sia per le necessità di riparazione di grandi pezzi, sia per la costruzione di piccole parti.
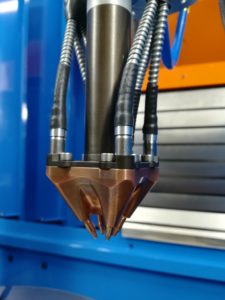
La testa laser è stata sviluppata appositamente per applicazioni di direct energy deposition ed è equipaggiata con quattro ugelli separati, che garantiscono una distribuzione uniforme della polvere nel punto di fusione. Il sistema di alimentazione esterno, inoltre, consente di lavorare fino a due materiali simultaneamente.
Le principali motivazioni che hanno spinto Enel verso la scelta di una soluzione sviluppata da Prima Additive sono state le dimensioni del volume di lavoro, i 7 gradi di libertà in grado di agevolare la riparabilità di alcuni articoli e l’esecuzione di forme complesse (originali o re-ingegnerizzate), la potenza parzializzabile della sorgente laser, i parametri di scansione aperti, un cad-cam customizzato e l’implementazione di due linee separate di adduzione polvere che, unitamente ad aspetti di ingegneria delle polveri, consentono notevole sviluppo delle proprietà meccaniche delle parti prodotte o riparate.
“La Divisione Global Thermal Generation di Enel – ha detto Enrico Viale, direttore Global Generation di Enel – nell’ambito di un ampio programma globale di digitalizzazione di processi e asset, che coinvolge circa 40 impianti termoelettrici dalla Russia al Sud America, ha valutato positivamente l’adozione di questa macchina, collocata a Santa Barbara ma punto di riferimento per l’attività di Enel in Italia e nel mondo. L’internalizzazione è stata scelta per assumere progressivamente piena padronanza dei principali driver tecnologici, dapprima su casi semplici e ripetitivi, evolvendo poi verso la riparazione e la riprogettazione di parti più complesse, per il costante miglioramento di disponibilità degli impianti di produzione”.
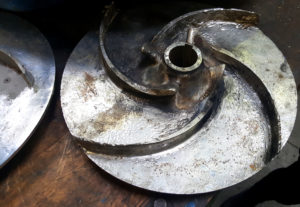
“L’additive manufacturing è una tecnologia Industria 4.0 che si sposa bene con la strategia di digitalizzazione del settore manifatturiero. Come molte tecnologie, ha un range estremamente ampio di applicazioni potenziali, la cui maturazione passa per la sperimentazione e messa in opera in contesti produttivi. – ha dichiarato Paolo Calefati, Vice President Additive Manufacturing Business Development per Prima Industrie SpA– La collaborazione con Enel è un esempio di strategia di open innovation profittevole. Il laboratorio di Santa Barbara è un’eccellenza sul territorio nazionale per quel che riguarda lo studio dei componenti utilizzati nel settore energia e generazione termica. La sinergia tra le competenze di Enel e quelle di Prima Industrie nella meccatronica e nella laser based manufacturing, sono alla base di questa collaborazione, finalizzata alla realizzazione di una macchina laser per deposizione diretta per il mercato del repairing e fabbricazione di componenti per il settore energia. Questa collaborazione è per Prima Industrie una crescita importante per la realizzazione delle macchine di additive manufacturing direct deposition e per lo sviluppo di applicazioni di repairing.”