Il taglio di un materiale, con qualunque tecnologia venga effettuato, comporta sempre una trasformazione, con un interessamento non solo delle superfici di lavorazione, ma anche del volume immediatamente sottostante. Dopo aver affrontato in passato il taglio al plasma e il taglio meccanico (per asportazione di truciolo), sarebbe adesso il momento di considerare le alterazioni metallurgiche indotte dal taglio ossiacetilenico: tuttavia le analisi svolte sui campioni utilizzati per le misurazioni hanno evidenziato interessanti fenomeni collaterali che sono l’oggetto del presente articolo rimandando l’analisi dei consueti aspetti metallurgici ad un prossimo articolo.
Il materiale di partenza e le misurazioni eseguite
In analogia con quanto già pubblicato, anche in questo caso si sono considerati campioni realizzati in acciaio S355 – J2, un acciaio da costruzione di largo utilizzo e spesso ancora riconosciuto con la vecchia denominazione di Fe510D.
Lo spessore utilizzato è stato di 20mm, e la caratterizzazione del taglio è stata effettuata in quattro diversi punti (Figura 1):
a) Superficie di taglio propriamente detta
b) Materiale a fianco del taglio, alla distanza di 2mm dal bordo
c) Materiale a fianco del taglio, alla distanza di 10 mm dal bordo
d) Al centro campione
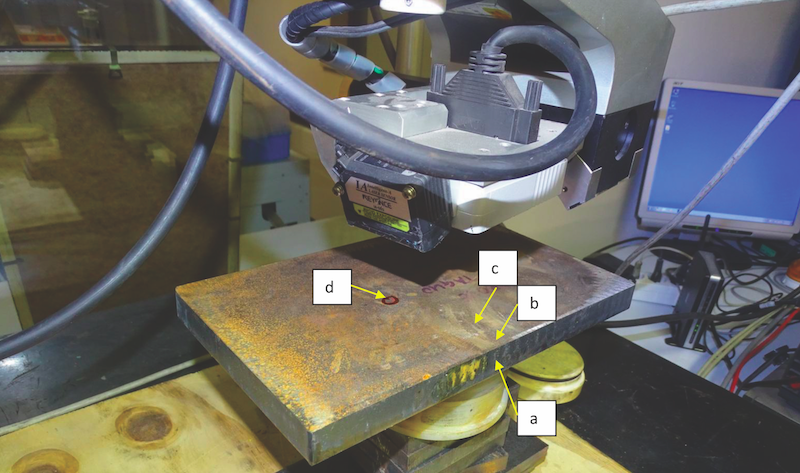
In ogni punto le misurazioni sono state eseguite prima sulla superficie nello stato in cui è stata trovata, e successivamente alla profondità di 200 micron, dopo aver provveduto ad asportare il materiale superficiale per via elettrochimica (Figura 2).
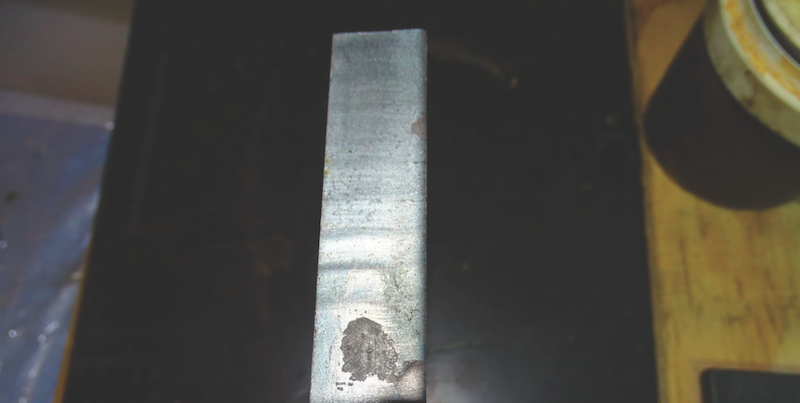
La scelta dei punti non è stata ovviamente casuale, ma è stata effettuata secondo il seguente razionale:
a) La misurazione a centro lastra è stata effettuata per avere valori riferibili al materiale di base
b) Le misurazioni sul fianco lastra alla distanza di 2 mm e 10 mm dal borso sono state eseguite per verificare l’eventuale effetto indotto dal taglio nel volume del materiale, nonché l’estensione in profondità di tale effetto
c) Le misurazioni alla profondità di 200 m (micron) sono state effettuate per verificare la profondità di penetrazione dei vari degradi
Una volta risolto il problema di “dove” misurare, si è considerato “cosa” misurare, e la scelta è stata di caratterizzare il materiale mediante la misurazione delle tensioni residue e la dimensione del cristallite, considerando quest’ultima informazione come un indice complessivo dello stato metallurgico del materiale. La misurazione di tali grandezze è stata effettuata mediante diffrazione dei raggi X , una tecnica che in precedenza abbiamo già ampiamente trattato su queste stesse pagine, e di cui andiamo a riassumere brevemente gli aspetti più salienti.