La magnetoformatura permette la lavorazione a freddo e senza contatto per ottenere forme uniche.
Smart Factory, società di automazione con l’innovazione nel proprio DNA, porta in Italia una tecnologia innovativa dalle potenzialità straordinarie per la formatura di metalli, che consente di ottenere forme uniche e saldature perfettamente resistenti a test all’elio: la magnetoformatura.
Smart Factory è una startup con sede nei pressi di Tortona, in provincia di Alessandria, ed è nata dalla volontà di avvicinare le imprese alla fabbrica 4.0, avvalendosi, fra l’altro, della magnetoformatura, una tecnologia di ultima generazione in cui crede molto, dai risultati sorprendenti proprio perchè lavora i metalli senza contatto e con una precisione pressoché assoluta, basandosi su chiari principi fisici, come il magnetismo e l’elettricità.
Carlo Tagliabue, responsabile meccatronico e co-fondatore dell’azienda, racconta così i vantaggi della magnetoformatura: “In Smart Factory crediamo che l’innovazione tecnologica sia la chiave di volta per rimanere competitivi al giorno d’oggi. La magnetoformatura è una tecnologia che risolve tantissimi problemi nella crimpatura e saldatura di strutture tubolari, difficilmente risolvibili con altre tecnologie, e in generale nella formatura di metalli, consentendo di ottenere forme uniche, diversamente impossibili da realizzare con processi economicamente sostenibili. Il primo approccio con la magnetoformatura è avvenuto nel corso di un processo di ricerca per la decorazione dei metalli, cercando una tecnica che consentisse di realizzare sottosquadri, embossing e debossing ad ampia raggiatura con estrema libertà, anche su superfici coniche, sferiche, cilindriche. Ritenendo industrialmente interessante il processo, abbiamo stabilito una partnership con PST Products, oggi nostro partner strategico e leader mondiale nella produzione di impianti di magnetoformatura con oltre 70 impianti installati in tutto il mondo“.
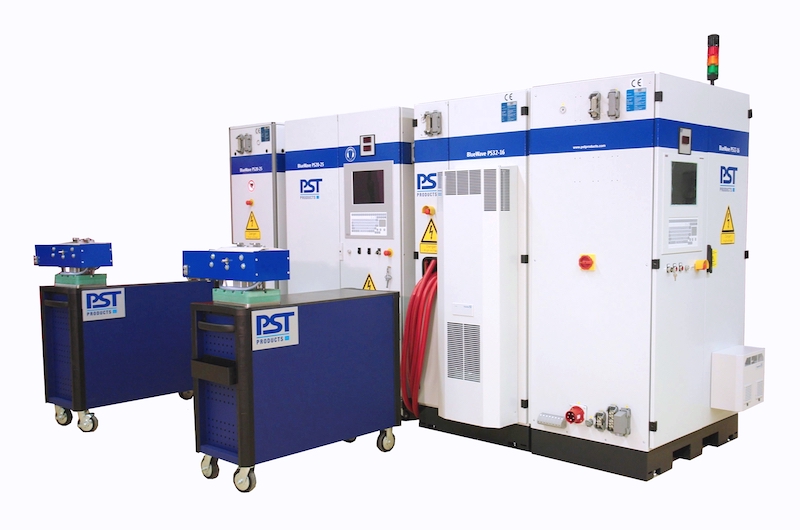
In cosa consiste la magnetoformatura e quali sono i suoi principali vantaggi?
“La magnetoformatura è una tecnologia che sfrutta una proprietà fisica dei metalli, l’elettromagnetismo, grazie al quali, con opportuni procedimenti, è possibile formare o saldare strati di metallo attraverso l’accelerazione meccanica. È innovativa perché permette di formare i metalli unicamente con l’utilizzo di impulsi elettromagnetici, a freddo, senza bisogno di contatto e senza dispersione di calore“.
Come funziona la magnetoformatura?
“Il processo di magnetoformatura si basa sulla generazione di campi magnetici impulsivi generati su metalli conduttivi. Le forze generate sono così alte da accelerare il pezzo fino a centinaia di m/s nel giro di 15 µs causando un impatto tra le superfici da formare e/o saldare. L’accelerazione genera uno stress meccanico fortissimo che rompe gli strati ossidativi del metallo, facendo si che le superfici dei metalli si modellino, o nel caso della saldatura, che si ‘contaminino’ tra loro: i metalli sono spinti uno contro l’altro con una pressione tanto forte da far sì che gli atomi creino una perfetta unione metallica“.
In quali settori trova applicazione ad oggi?
“Nel settore automobilistico viene preferita ad altre tecnologie, soprattutto per la saldatura di parti di telaio, organi per iniettori, ed elementi del cambio perché è in grado di generare delle saldature e crimpature molto più resistenti rispetto a tecnologie tradizionali con costi e tempi di esecuzione ridotti. Anche nel settore degli elettrodomestici e dei sistemi di raffreddamento per quanto concerne gli organi in pressione, in particolare per i gruppi di raffreddamento o comunque con conduzione di liquidi o gas, è utilizzata con successo e preferita ad altre tecnologie proprio perché garantisce una tenuta eccellente e in grado di superare i test di tenuta all’elio. Negli ultimi anni la magnetoformatura ha visto notevoli applicazioni nel campo dell’electromobility grazie all’elevata affidabilità, velocità e mantenimento della purezza soprattutto nella realizzazione di sistemi anodo-catodo. Gran parte dei contatti di potenza anodo-catodo sono caratterizzati dalla saldatura di lamine tra alluminio e rame. Anche il packaging cosmetico o il lettering e logos sono interessati a questa tecnologia, che permette di customizzare le lavorazioni con libertà grazie alla’assenza di stampi o utensili, ottenendo effetti impossibili a spessori ridotti, fino a 0,2 mm. Il tutto in frazioni di secondo. Perfino il taglio di superfici metalliche trae vantaggio da questa tecnologia, nota tecnicamente come EMPT, Electromagnetic Pulse Technology: viene utilizzata una matrice di taglio senza secondo utensile e le superfici risultano assolutamente senza sbavature“.
Parlando dei processi di formatura nella lavorazione di strutture tubolari, quali sono i vantaggi?
“La magnetoformatura nei processi di saldatura consente di superare i limiti imposti da altre tecnologie nella lavorazione di metalli. I principali vantaggi della tecnologia sono legati alla particolarità di essere un processo che dura una frazione di secondo e che è assolutamente pulito: non richiede apporto di materiale e non altera la struttura del metallo. Per la lavorazione di strutture tubolari si utilizza un utensile dedicato, all’interno del quale viene collocato l’oggetto da saldare, formare o crimpare. La forza magnetica può essere inferta dall’interno oppure dall’esterno del pezzo, e per deformazione meccanica data dalla scarica elettromagnetica, va ad effettuare la lavorazione. Uno dei vantaggi più grandi è la possibilità di saldare metalli di leghe diverse, realizzando saldature estremamente affidabili, che superano i test all’elio in pressione, precise e resistenti. Svariate prove dimostrano che le crimpature e saldature realizzate sono addirittura più resistenti dei punti non saldati: nei test di tenuta il metallo si spezza in altri punti, ma mai nel punto di saldatura. Un altro grande vantaggio è che non essendo una lavorazione a caldo, consente, per esempio, la crimpatura di corpi metallici con elementi plastici“.
Quali limiti presenta la magnetoformatura?
“La conduttività del metallo flyer: essendo un processo ad impulsi elettromagnetici, funziona tanto più efficacemente quanto più il metallo che viene accelerato è conduttivo, quindi ben si presta ad alluminio, rame, argento e oro, platino. Sulle crimpature la tecnologia è adatta anche all’acciaio. Per le saldature invece, bisogna fare chiarezza: se si tratta di saldatura tra acciaio e un metallo ben conduttivo e duttile quale è il flyer, la tecnologia da ottimi risultati. Qualora sia necessario fare una saldatura acciaio su acciaio, è necessario adottare un flyer di alluminio che poi risulta in pezzo di scarto, oppure limitarsi alla crimpatura. Anche lo spessore dello strato di metallo va tenuto in considerazione: la magnetoformatura funziona con spessori molto contenuti, da 0,2 mm fino a 30 mm, per una lunghezza anche di svariati metri. Tuttavia, non è una tecnologia che funziona con pezzi pieni. Parlando di saldature di testa, occorre considerare che la magnetoformatura necessita di una superficie di adesione tra i due elementi da saldare. Nel caso sia necessario attuare saldature di testa, la magnetoformatura richiede di intervenire sul design del prodotto per poter creare una opportuna superficie di appoggio sulla quale effettuare la saldatura. Dunque le tradizionali saldature di testa non si prestano a questa tecnologia, se non con una modifica al design“.
I benefici del processo di magnetoformatura
• Consente di saldare leghe metalliche con punti di fusione diversi, non saldabili con metodi convenzionali (rame e alluminio, acciaio e rame, argento e rame…)
• Alta affidabilità e ripetibilità: le saldature hanno una precisione e resistenza unica, tanto impermeabili da passare i test all’elio
• Il processo non genera alcuna dispersione di materiale, non richiede l’aggiunta di materiale e non prevede una modifica delle caratteristiche del metallo
• Elevata efficienza energetica, costi per pezzo bassi, manutenzione minima
• Veloce: 6 millisecondi per la lavorazione
• L’uso del maschio dello stampo può essere omesso con questo processo perché la forza magnetica agisce sul pezzo senza contatto (è richiesto un solo stampo femmina, e non richiede la necessità di allineamenti centesimali tra maschio e femmina)
• Gli effetti del ritorno elastico sono ridotti al minimo
• Distribuzione del materiale sulla superficie perfetta, senza riduzioni di spessore
di Marcello Carboni