La dentatura di ingranaggi conici richiede l’impiego di vari tipi di utensili, che, nel corso degli ultimi decenni, sono stati oggetto di uno sviluppo tecnologico che ha coinvolto geometrie, materiali, macchine e software. Come è accaduto presso miniToolsCoating (www.minitoolscoating.com).
Gli ingranaggi conici spiroidali di piccolo e medio diametro sono dentati con frese integrali a dentatura frontale alternata in acciaio rapido (HSS), mentre per gli ingranaggi con medi e grandi diametri si usano sia frese integrali sia barrette in metallo duro (carburi sinterizzati) montate su corpi speciali. Quando i volumi di produzione sono elevati si privilegia l’impiego delle barrette in metallo duro.
L’uso di barrette (stick blades) rappresenta un grande progresso dal punto di vista della velocità di dentatura e del costo complessivo dell’utensile per pezzo dentato.
L’utilizzo delle macchine a controllo numerico che usano barrette in metallo duro ha permesso un aumento notevole delle velocità di taglio e, quindi, una drastica riduzione dei tempi ciclo.
Attualmente le frese integrali sono ancora prodotte in HSS perché sìussistono notevoli difficoltà tecniche nella costruzione di questi utensili in carburi sinterizzati.
Pur avendo le barrette un grande vantaggio rispetto alle frese integrali in acciaio – dovuto essenzialmente alla possibilità di eseguire sistematicamente il rivestimento PVD dopo ogni riaffilatura, oltre che al numero delle affilature possibili e quindi al numero totale dei pezzi eseguibili con una serie di barrette – le frese integrali sono ancora diffusamente impiegate in tutto il mondo.
Sono in funzione numerosissime macchine che usano frese integrali, perché – oltre ad essere utilizzate per ingranaggi di piccole dimensioni – la loro sostituzione con macchine moderne richiede forti investimenti.
Nell’impiego delle barrette oltre a costo della macchina dentatrice bisogna considerare che, per essere autonomi, bisogna dotarsi di una affilatrice speciale e di appositi apparecchi di controllo, nonché di opportuni software, che vanno incidere non poco sul costo totale dell’investimento.
Ma è evidente che con il passare del tempo il numero di macchine che usano barrette è destinato ad aumentare. Esistono diversi tipi di barrette con diversi profili di affilatura e diverse dimensioni dello stelo.
In linea di massima ciò è dovuto al fatto che le due principali aziende che producono macchine per dentare ingranaggi conici, cioè Gleason e Klingelnberg (Oerlikon), usano tecnologie diverse.
Le barrette della Gleason, attualmente utilizzate, hanno la sezione del corpo pentagonale, mentre quelle montate sulle macchine Klingelnberg hanno il corpo con sezione rettangolare.
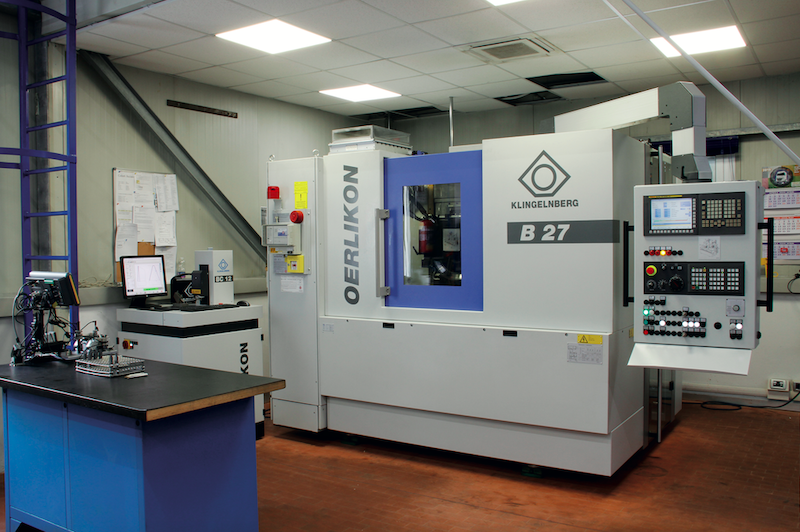
Diversi tipi di barrette
Chi acquista le barrette può scegliere tra diverse opzioni, e precisamente:
a) barrette senza profilo che è la scelta più comune. L’utilizzatore finale eseguirà il profilo sul corpo rettificato, secondo le proprie necessità, impiegando la speciale affilatrice di cui deve necessariamente essere provvisto. Questa operazione richiede un tempo generalmente molto lungo e la macchina è molto sollecitata perché è necessario asportare una grande quantità di materiale dallo stelo grezzo;
b) barrette con profilo sgrossato: L’utilizzatore finale può risparmiare molto tempo nella realizzazione dei profili rendendo disponibile la costosa affilatrice per le normali riaffilature.
Il fornitore delle barrette sgrossate deve disporre del “summary” di affilatura, cioè dell’elenco dei dati che definiscono il profilo da eseguire;
c) barrette con profilo finito e rivestite con processo PVD se richiesto. L’utilizzatore finale può montare le barrette direttamente sulla testa porta lame. Il fornitore delle barrette finite deve disporre in questo caso, del “summary” di affilatura e di una barretta master.
Questa ultima condizione non è sempre necessaria per fornitori altamente qualificati come può essere per esempio la miniToolsCoating di Padova.
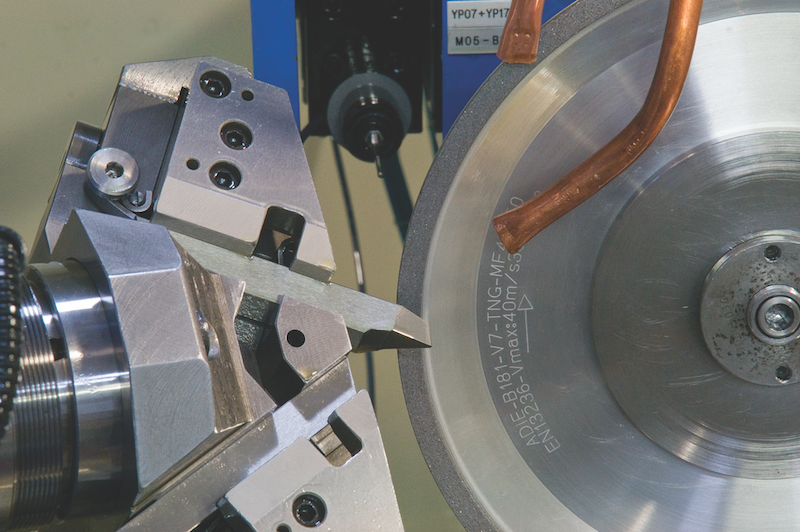
Un centro di servizio per la fornitura di barrette finite
La possibilità di usufruire di un centro di servizio altamente specializzato, in grado di fornire barrette finite pronte per il montaggio sul corpo porta lame, con assoluta ripetibilità del profilo, è un grande vantaggio per chi non possiede una affilatrice speciale, ma anche per chi vuole svincolarsi del tutto o in parte dall’impegno di affilare le barrette in proprio.
Tanto più che un notevole incremento delle prestazioni delle barrette si ottiene con un ricoprimento PVD, operazione questa fattibile dal centro di servizio dopo l’affilatura.
miniToolsCoating ha acquisito macchine, apparecchi di controllo e software che la posizionano in un livello di eccellenza in questa tecnologia.
Il sistema di punta attualmente operativo in azienda consiste in un’affilatrice Klingelnberg (Oerlikon) B27 abbinata a un apparecchio di controllo BC12 e al software Kimos5. Si tratta di uno delle più complete suite con cui le coppie coniche vengono progettate, a partire dalle caratteristiche geometriche principali per arrivare alla definizione di tutti i piazzamenti dei diversi macchinari di produzione e degli apparecchi di controllo che vengono impiegati, includendo anche la definizione dell’utensileria. Con questo strumento vengono dimensionate coppie coniche sia Gleason sia Klingelnberg.
La differenza sostanziale tra i software della Gleason e della Klingelnberg è che i primi si avvicinano al risultato teorico con un algoritmo iterativo fino alla precisione desiderata, con un approccio quindi pratico, soprattutto per quanto riguarda il setup finale della dentatrice.
Il software usato dalla Klingelnberg prevede l’elaborazione dettagliata di ogni singola fase del processo di progettazione e produzione, con un approccio quindi totalmente teorico prima di ogni attività meccanica.
In questa situazione i dati forniti dall’utilizzatore alla miniToolsCoating per l’esecuzione del profilo finito delle barrette permettono di ottenere profili e setup direttamente applicabile senza aggiustamenti su macchine Gleason solo per progetti nuovi, mentre per lavorazioni già in atto il profilo esatto può essere ottenuto solo attraverso l’utilizzo di una barretta master.
Per le macchine Klingelnberg, invece, i profili e i valori del setup derivati dai dati di progettazione sono precisi e direttamente applicabili senza ulteriori modifiche anche senza l’utilizzo di barrette master.
Kimos5 permette inoltre di simulare l’ingranamento tra utensile e ingranaggio mettendo in evidenza eventuali difetti di progettazione.
Nella Figura 4 è possibile vedere che la simulazione di ingranamento di un utensile con profilo suggerito dal cliente, mette in luce un errore di overlap, con la formazione di uno scalino sul fondo dente, mentre con il profilo corretto, l’unione dei due fianchi della fresa produce un fondo dente senza scalini. È evidente che un corretto dimensionamento aumenta il rendimento della fresa.
L’affilatrice Klingelnberg B27 è a oggi una delle affilatrici per barrette tecnologicamente più avanzate al mondo.
Il potente controllo numerico Fanuc Series 31i A5 è in grado di gestire 9 assi con precisione quasi assoluta.
Il caricatore automatico è integrato nella macchina ed è composto da un magazzino di 24 cassette che possono contenere al massimo 18 barrette cadauna, cioè un totale di 432 barrette.
Ogni cassetta può essere caricata con una diversa tipologia di barretta e quindi il controllo numerico cambierà automaticamente il programma di affilatura in accordo con il tipo di barretta presente in ogni singola cassetta.
La macchina monta una mola diamantata elettrodeposta di 400 mm di diametro (brevettata) e specifica per questa macchina e per questo tipo di lavorazione.
Dopo ogni pezzo eseguito, un sensore controlla l’usura della mola e, se è il caso, il controllo numerico modifica la sua posizione per mantenere costanti i parametri di affilatura previsti dal programma.
Per limitare la possibilità di errori, la sgrossatura viene eseguita con una parte della mola, mentre per la finitura viene impegnata una superficie diversa. In questo modo si limita l’usura della parte di mola che stabilisce la precisione di affilatura e inoltre si possono ottenere superfici con rugosità inferiore a Ra = 0,1 µm. La macchina è abbinata all’apparecchio di controllo Klingelnberg BC12.
I dati del profilo controllato vengono confrontati con quelli teorici e, in caso di scostamento, il controllo numerico esegue automaticamente le opportune correzioni. In pratica il sistema funziona con il metodo closed loop, garantendo una assoluta precisione su tutte le barrette affilate in modo automatico senza intervento dell’operatore.
Lo scostamento dalle quote teoriche sul totale delle barrette caricate in macchine è dell’ordine del micrometro.
È quasi superfluo osservare che la precisione del profilo della barretta affilata è una condizione essenziale per avere una fresa che tagli correttamente e che generi un ingranaggio con minimi errori di profilo e di divisione.
Non solo: le nuove tecnologie di taglio a secco con barrette in metallo duro prevedono una precisione esasperata nel montaggio delle lame nel disco, e questa operazione è possibile solo impiegando barrette realizzate con tolleranze geometriche e dimensionali strettissime, sia per quanto riguarda la realizzazione del corpo lama che dei profili attivi.
Bisogna poi mettere in evidenza che se l’utilizzatore affila in proprio le barrette e non dispone di mezzi di prima qualità, come nel caso descritto di miniToolsCoating, difficilmente otterrà le stesse precisioni, e in più dovrà in ogni caso spostare le barrette per eseguire i rivestimenti PVD.
A questo proposito, l’esperienza di miniToolsCoating in questo campo suggerisce che i migliori risultati si ottengono con il rivestimento Silicut (AlTiSiN nanolayer), se si lavora con olio; mentre se si lavora a secco è preferibile adottare il GearCut (AlCrN monoblock).
di Gianfranco Bianco