Anche in Italia la cultura del riciclo della plastica si sta consolidando e il recupero di materiali usati si tramuta in una risorsa in più a favore delle imprese che ne sposano la logica, sia per ragioni economiche, sia per pura sensibilità ambientale. Lo stesso vale per il bio: il settore degli stampi ne dà dimostrazione.
Parlano chiaro i dati presentati nel rapporto “L’Italia del riciclo 2019“, redatto dalla Fondazione Sviluppo Sostenibile. Nel 2018 – anno al quale fanno riferimento le rilevazioni più recenti – «la filiera degli imballaggi in plastica ha registrato un incremento del 7% delle quantità avviate a riciclo aumentando del 3% il tasso di avvio al riciclo rispetto all’immissione al consumo (45%)». Fra il 2017 e il 2018 è salita anche la mole di materiali provenienti dalla raccolta differenziata (+9,6%). Crescono in particolare, in termini di volumi indirizzati al riuso, i contenitori per liquidi (Cpl) e i prodotti a base film. «I prodotti della famiglia Cpl (Contenitori in plastica per liquidi) a base PET e HDPE sono prodotti dalla qualità consolidata – ha sottolineato la Fondazione nel suo report – e hanno applicazioni solide, diffuse e affidabili. Le nuove tecnologie e l’esperienza ultradecennale nel riciclo rendono il mercato delle materie ottenute (scaglie e granuli pronti per la messa in macchina) ormai imprescindibile (…). Il riciclato da CPL a base PET trova impiego anche nelle tecnologie per la produzione di imballaggi a uso alimentare (vaschette e bottiglie). L’industria del riciclo ha sviluppato processi di decontaminazione e di recupero delle caratteristiche tali da rendere questi materiali di riciclo sicuri per il consumatore pure nel caso di un impiego a contatto con alimenti». Mentre le potenziali destinazioni dei polimeri rigenerati sono pressoché illimitate, «nella pratica entrano in gioco tre fattori fondamentali: disponibilità (quantitativi effettivamente ottenibili dai processi di selezione e riciclo), prestazioni (qualità e caratteristiche dei polimeri di riciclo) e costi». Resta il fatto che «l’utilizzo di polimero di riciclo è considerato una strada da percorrere per ridurre il costo della materia prima, spesso in alternativa alla miscelazione con polimeri vergini fuori specifica».
Allo stesso tempo ha acquistato slancio anche la supply chain delle bioplastiche, che, secondo le stime dell’Osservatorio di Assobioplastiche, «è rappresentata da 252 aziende (+4% fra 2017 e 2018), suddivise in produttori di chimica e intermedi di base (5), produttori e distributori di granuli (20), operatori di prima trasformazione (162), operatori di seconda trasformazione (65)». Nel complesso sono state protagoniste di un progresso medio annuo dell’11% e sono arrivate a totalizzare un fatturato pari a 685 milioni di euro contro i 370 soltanto del 2012. Entrambe le tipologie di materiale – si veda il dettaglio tecnico nel riquadro di pagina xx – stanno attraendo a vario titolo e in diversa misura anche le società votate alla costruzione di stampi e allo stampaggio. Le motivazioni che le guidano e le orientano in direzione del riutilizzo sono tanto di natura economica – determinate per esempio dalla costante disponibilità di commodity derivanti magari dagli scarti di lavorazione – quanto ispirate dalla sincera fedeltà al modello della circular economy. I casi illustrati di seguito sono quelli di brand o realtà della ricerca che danno testimonianza di come una manifattura sostenibile sia possibile e vantaggiosa per tutti, pianeta Terra in primis. Non mancano le opportunità di mercato; non manca – come si avrà modo di osservare – l’attenzione interessata dei committenti più strutturati e innovativi, pronti ad aprirsi una strada verso il futuro.
La plastica da riciclo sale a bordo
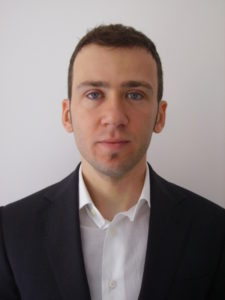
Il polo alessandrino di ricerca e innovazione sulla plastica Proplast è organizzato nella forma di un consorzio cui partecipano 181 soci aziendali e 11 accademici; sei associazioni e una fondazione. Oggi è fra gli altri impegnata nel progetto paneuropeo Plasticircle la cui denominazione allude già di per sé all’economia circolare e al quale aderiscono venti organizzazioni di diverso tenore da tutto il vecchio continente. «È focalizzato sull’ottimizzazione della gestione degli imballaggi in plastica recuperati attraverso i canali della raccolta differenziata – hanno riferito a Stampi Marco Monti, responsabile tecnico del progetto, e Andrea Romeo, a capo del laboratorio di Progettazione avanzata –, e noi vi siamo coinvolti in sede di valorizzazione dei materiali tratti dalla selezione urbana insieme al Centro di ricerche Fiat». L’obiettivo è «utilizzare plastiche riciclate nelle applicazioni tecniche» partendo dalla messa a punto di «composti polimerici nei quali le plastiche derivanti dal riciclo degli imballi vadano a sostituire alcuni gradi di polimeri». Per esempio, ricorrendo al polipropilene da riciclo anziché a quello vergine, addizionato se necessario con talco o altri elementi in modo da raggiungere le caratteristiche richieste dai capitolati FCA. Analogamente, «il PET derivato da bottiglie è stato riformulato in maniera tale da poter rimpiazzare la poliammide 66 nella realizzazione di parti sotto-cofano di un’automobile».
Se Plasticircle è atteso alla conclusione entro il prossimo biennio, già all’inizio del 2020 dovrebbero avere luogo le prime prove-stampo sotto l’occhio attento e interessato del costruttore. «Stiamo lavorando per superare le criticità date in fase di stampaggio dal componente prodotto in PET anziché con la classica poliammide – hanno proseguito Monti e Romeo –, che è generalmente più semplice da lavorare. La sfida è duplice: da un lato la necessità è di contenere al massimo i tempi-ciclo; dall’altro bisogna dimostrarsi competitivi a livello di costi». Certamente vantaggiosi sono da questo punto di vista i materiali e la carbon-footprint; mentre sugli oneri di processo e soprattutto i procedimenti di essiccazione si dovranno compiere ulteriori stime. «Si dovrà poi dimostrare – hanno osservato Monti e Romeo – che le prestazioni sono equivalenti». Le prime esperienze di test sono incoraggianti ma per creare un componente stampato in tutto e per tutto identico a uno standard già esistente e disponibile è stato e sarà necessario superare alcune criticità. Quelle legate alla cristallizzazione del compound e alla già menzionata essiccazione, in primo luogo. Poi, quelle rappresentate dalla imprescindibile costanza della temperatura-stampo (130 gradi centigradi) e dalla revisione dei punti di iniezione. «Vogliamo dimostrare che un’industria sostenibile è possibile – hanno dichiarato gli intervistati –. D’altra parte nel corso degli anni (Proplast è stato avviato nel 1998, ndr) abbiamo preso parte ad altre iniziative orientate al riciclo, per esempio per l’uso del polverino da pneumatici e altre plastiche rigenerate, sempre con Fiat. E da qualche mese è partito il progetto Reciplast, finanziato dalla regione Piemonte, che ha l’ambizione di creare, accanto agli aspetti più tecnologici legati al riciclo chimico e meccanico della plastica, una rete strutturata di aziende università e centri di ricerca che accetti e superi le nuove sfide di ecosostenibilità richieste dalla società. Infine, il progetto Prime contempla la collaborazione con il Centro di Ricerche Fiat di Orbassano e con Novamont, per la sostituzione delle plastiche tradizionali con bioplastiche, mentre con Newpack, Proplast si concentra sulla produzione di imballaggi al 100% da fonte rinnovabile e biodegradabile. Per le applicazioni tecniche, una delle frontiere che verranno affrontate, in Reciplast cosi come in Prime, sarà quella di curare sì le applicazioni tecniche per l’auto con materiale riciclato o bio-based, dando attenzione però ai dettagli estetici».