Bonfiglioli e Schaeffler hanno unito le loro competenze e messo a punto una soluzione innovativa per il monitoraggio costante e in real time dello stato degli azionamenti azimutali delle turbine eoliche. Una tecnologia capace di rilevare tempestivamente guasti, al fine di aumentarne l’affidabilità, ridurre i costi operativi, di manutenzione e di inattività.
Bonfiglioli progetta, fabbrica e distribuisce una gamma completa di motoriduttori, motori elettrici, riduttori epicicloidali e inverter, in grado di soddisfare le esigenze più complesse nei settori dell’automazione industriale, del navale, delle macchine mobili e dell’energia rinnovabile. Ambiti operativi che vedono il gruppo bolognese ricoprire un indiscusso ruolo da protagonista per l’innovazione continua che è in grado di generare.
«Sempre nell’ottica di poter innovare nei propri settori di competenza – afferma Gaetano Ciaravella, manager Meccatronica e IoT –. Bonfiglioli ha ormai da tempo individuato anche nella digitalizzazione uno dei punti cardine su cui puntare risorse e investimenti. Non solo dal punto di vista di prodotto, seppur inteso nella sua accezione più ampia, ma cercando anche di generare un differenziante valore aggiunto per i propri clienti ricorrendo anche a sinergie e fattive collaborazioni coi propri partner». Ed è proprio da una di queste cooperazioni che è nato un pacchetto compatto di soluzioni Industry 4.0 per gli azionamenti azimutali delle turbine eoliche. Stiamo parlando di un progetto nato dalla consolidata partnership di sviluppo a lungo termine instaurata dalla stessa Bonfiglioli e da Schaeffler, che ha portato a un innovativo sistema di monitoraggio in real time dello stato del riduttore attraverso la valutazione di alcuni parametri tra cui anche la coppia trasmessa.
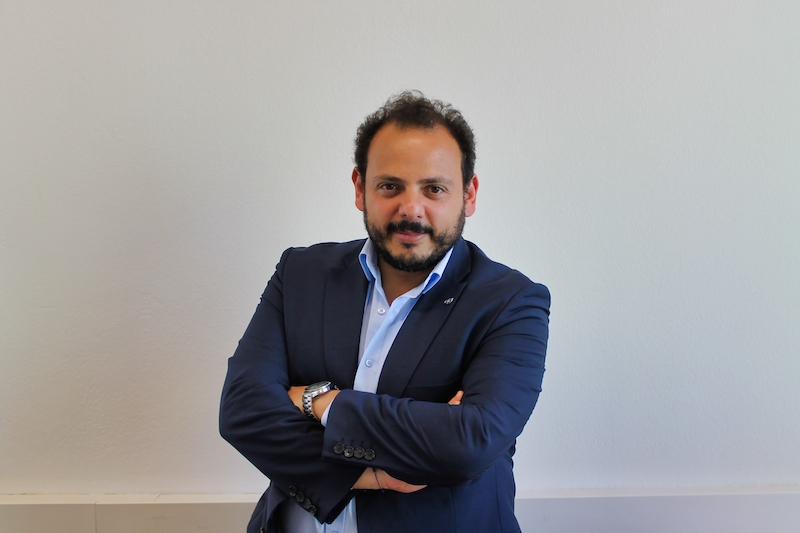
Coppia, velocità, vibrazioni e temperatura in real time
«Riuscire a monitorare costantemente il comportamento di un riduttore – spiega Ciaravella – significa massimizzarne l’affidabilità, a tutto vantaggio di una maggiore efficienza, di una riduzione dei costi operativi, di quelli di manutenzione, minimizzando così i tempi di inattività».
Ciò è reso possibile dai particolari sensori TorqueSense e SmartCheck i quali, applicatti proficuamente al mondo wind dai team di IoT e Meccatronica di Bonfiglioli e Industry 4.0 Schaeffler, registrano istante per istante informazioni su coppia, velocità, vibrazioni e temperatura. Dati, questi, che vengono trasmessi in tempo reale attraverso un gateway, combinati ed elaborati utilizzando algoritmi basati su intelligenza artificiale, sviluppati da Bonfiglioli e basati su un’esperienza di oltre 60 anni nel settore dei motoriduttori e specificatamente dedicati a questa applicazione.
«Tali dati – prosegue Ciaravella – confluiscono su un’apposita piattaforma cloud di Bonfiglioli e restituiti in modo chiaro ed efficace all’operatore attraverso una funzionale dashboard. Un’architettura appositamente sviluppata per interpretare le informazioni fornite dai vari sensori e poter così aver avere un monitoraggio dinamico del ciclo di vita, valutare lo stato del dispositivo, adottare misure di manutenzione in maniera focalizzata e predittiva».
Sulla dashboard Bonfiglioli, l’operatore si trova così nelle condizioni di poter fare un controllo continuo dello stato del motoriduttore in base alla situazione dei dati rilevati, ed è possibile effettuare anche una stima della durata residua dell’azionamento. Il comportamento anomalo dell’azionamento azimutale viene infatti segnalato come condizione critica e, su questa base, gli intervalli di manutenzione possono essere ottimizzati secondo le reali necessità e le riparazioni necessarie possono essere effettuate in tempi accettabili.
«Allo stesso tempo – aggiunge Ciaravella – il controllo dell’azionamento può essere ottimizzato, in modo da evitarne il sovraccarico. Altro risultato importante riguarda la drastica riduzione dei tempi di fermo macchina non pianificati o viceversa, a tutto beneficio di un significativo aumento della redditività globale di un impianto. Il tutto grazie a un pacchetto compatto, conveniente e competitivo, al momento ancora esclusivo e innovativo per l’applicazione stessa».
Con l’aiuto di modesti investimenti, l’adozione del sistema può dunque portare a una riduzione anche molto significativa dei costi operativi (finanche al 50-60%) e, grazie alla possibilità di adattare gli azionamenti elettronici alle condizioni ambientali e di funzionamento (per esempio temperature, ore di vento/anno…), avere oltretutto un effetto diretto e positivo sulla produttività del generatore eolico.
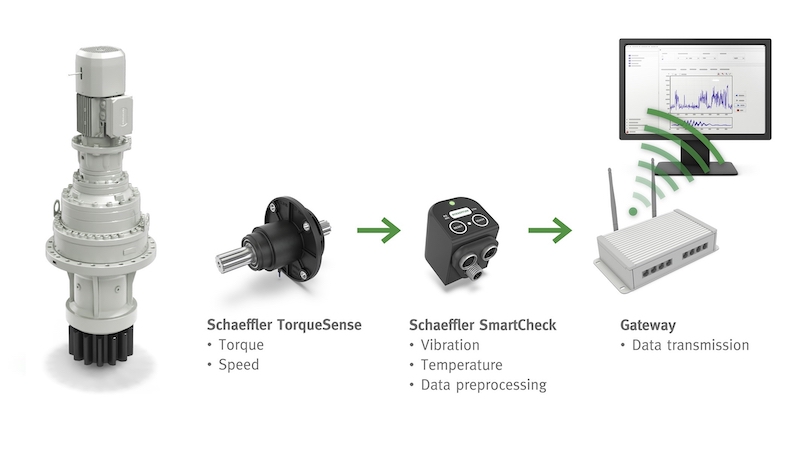
Le competenze migliorano la competitività
Il sistema di monitoraggio sviluppato congiuntamente da Bonfiglioli e Schaeffler funziona in modo indipendente e non è collegato al sistema di controllo della turbina, rendendo molto semplice il retrofit quando i motoriduttori vengono sostituiti.
«Quello delle turbine eoliche – osserva Ciaravella – rappresenta senza dubbio per Bonfiglioli un settore applicativo un fiore all’occhiello, con una quota di mercato di circa il 35% raggiunta attraverso la fornitura di prodotti ai maggiori e più importanti OEM».
Fortemente orientata all’innovazione, la strategia del gruppo bolognese è comunque quella di adottare lo stesso approccio operativo, il know how e le trasversali competenze dei propri dipartimenti di ricerca e sviluppo anche per altri settori. «Tra questi – conclude Ciaravella – mi riferisco per esempio al vasto ed esteso material handling dove sono in corso numerosi test. Fondamentale rimane in ogni caso il denominatore comune, ovvero quello di riuscire a restituire, insieme a un prodotto sempre più affidabile e performante, un ulteriore valore aggiunto applicativo, tecnico e tecnologico, capace di generare maggiore redditività e una più elevata competitività per i nostri clienti».
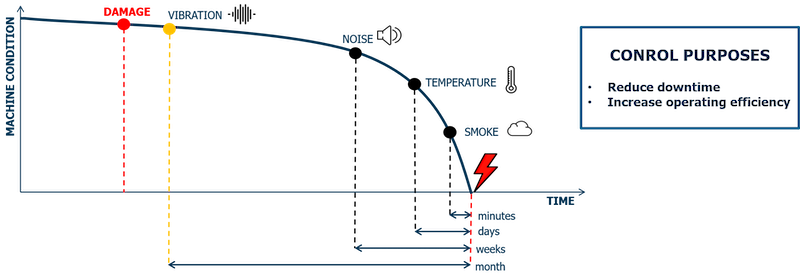
Bonfiglioli è coordinatore di IoTwins, uno dei progetti di Horizon 2020
Big Data, AI (Intelligenza Artificiale) e IoT (Internet of Things) applicati a manifattura e infrastrutture sono alcune delle tematiche affrontate da IoTwins, uno dei progetti europei più importanti, finanziato per un valore globale di 20 milioni di euro nell’ambito di Horizon 2020, di cui Bonfiglioli Riduttori è capofila.
Nato dall’azione congiunta del gruppo bolognese con l’Università di Bologna, Istituto Nazionale di Fisica Nucleare, Cineca, Regione Emilia-Romagna con Art-ER, sarà basato nella Data Valley dell’Emilia-Romagna e sperimenterà nuove tecnologie per la digitalizzazione dei processi e dei prodotti industriali, con il supporto di un partenariato internazionale con oltre una ventina di qualificati. Tra questi spiccano l’istituto Fraunhofer, la più grande organizzazione di ricerca applicata in Europa, la Technische Universitaet di Berlino, il Barcelona Supercomputer Centre, il Barcelona Football Club, Thales, Siemens, il Fraunhofer Gesellschaft zur Foerderung der angewandten forschung di Monaco di Baviera, l’Ecole Nationale Superieure d’arts et metiers e il Centre Techniques des Industries Mecaniques di Parigi.
Più nel dettaglio, sono 12 le piattaforme di test previste dal progetto che realizzeranno “gemelli digitali” per testare impianti di produzione in ambito manifatturiero e strumenti di gestione di infrastrutture, modelli che potranno essere utilizzati anche dalle Pmi. I gemelli digitali sono infatti copie virtuali di processi e di impianti reali che interagiscono tra loro e che, attraverso la raccolta di grandi quantità di dati, riescono a simulare i diversi scenari per definire le azioni correttive e ottimizzare l’efficienza come, ad esempio, diagnosticare le anomalie prima che si presentino. In particolare, 4 test bed verranno realizzati in ambito manifatturiero per la diagnosi predittiva nelle numerose aree di attività in cui operano i partner industriali del consorzio (turbine eoliche, macchine utensili per la produzione di componenti automotive, macchine per la produzione di alberi a gomito, macchine per la produzione di tappi per bottiglie).
Altri 3 test bed saranno incentrati sulla gestione di infrastrutture e, in particolare, verranno applicati all’ottimizzazione della gestione dello stadio di Barcellona, sulle cosiddette smart grid, cioè l’insieme di una rete di informazione e di una rete di distribuzione per gestire la rete elettrica in maniera “intelligente”, per monitorarne la qualità dell’energia e sulla gestione olistica delle infrastrutture di supercalcolo.
I rimanenti 5 test bed, punto di forza e valore del progetto per tutto il sistema industriale regionale, riguarderanno la replicabilità e la standardizzazione dei modelli precedenti per definirne nuovi ambiti di applicazione e sviluppare modelli di business innovativi in ambito manifatturiero e nella gestione infrastrutture.
di Gianandrea Mazzola