In questo articolo verranno analizzati processo, vantaggi, limiti, applicazioni e produttori della tecnica additiva di Selective Laser Sintering, una delle più importanti tecnologie di stampa 3D utilizzate nel campo dei polimeri.
Il processo basato sul letto di polvere fu sviluppato intorno agli anni ’80 dall’Università di Austin (grazie alla partnership con la società DTM) e la società tedesca EOS. Il termine “Sintering”, ad oggi, è improprio in quanto non c’è contributo di pressione oltre a quello di temperatura. In passato, invece, le polveri venivano compattate tra di loro grazie ad una mutua azione di pressione e temperatura. La fusione viene effettuata da un fascio laser (meno potente di quelli per le polveri metalliche, viste le temperature di fusione dei polimeri molto più basse). In questo processo non bisogna raggiungere la temperatura di degrado del materiale, pertanto uno dei parametri di processo più importanti è basato sul capillare controllo della potenza del laser. Solitamente vengono usati laser a CO2, con potenze massime attorno ai 200 W (così alte solo per aumentare la produttività della macchina).
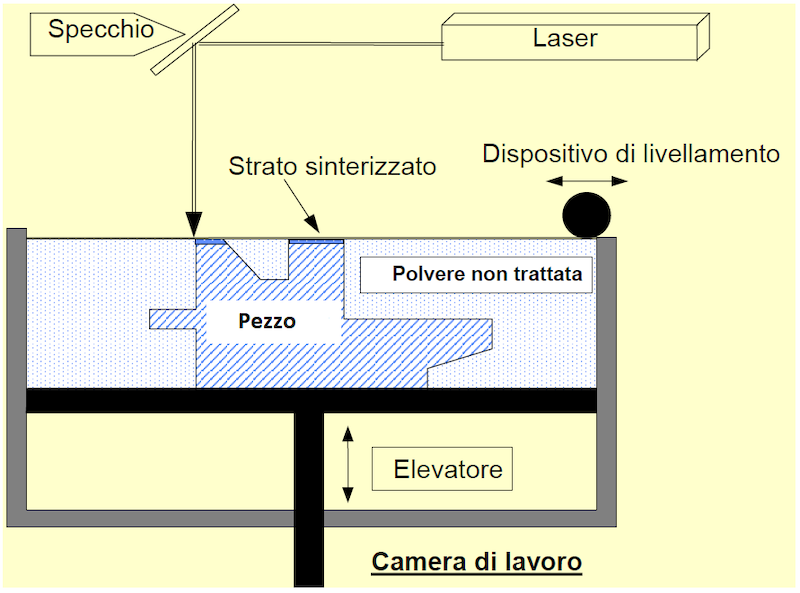
Il processo
Lo schema di funzionamento del Selective Laser Sintering è mostrato in Figura 1. Nel caso dei polimeri termoplastici la sorgente porta a fusione la polvere e realizza l’intera sezione, facendola aderire allo strato precedente. La camera di lavoro è mantenuta ad una temperatura prossima a quella di fusione della polvere per minimizzare i ritiri di solidificazione: maggiore è il ΔT tra il letto di polvere e le polveri solidificate, maggiori saranno i ritiri. Tale ΔT, inoltre, è fondamentale per fondere gli strati tra di loro e garantire una perfetta adesione di un layer con il precedente (layer inferiore) e il successivo (layer superiore).
Il sistema opera in copertura di azoto per evitare l’ossidazione delle polveri (non bisogna avere delle bombole esterne, ma vi è un sistema interno alla macchina che raccoglie l’azoto dall’aria). È necessario, quindi, prevedere dei sistemi di areazione nel posto in cui si trova la macchina. Non sono necessari i supporti, in quanto si lavora a camera calda. Al termine del processo, i pezzi sono immersi nel letto di polvere. Il blocco di polvere contenente i particolari realizzati deve essere fatto raffreddare in aria prima di estrarre i pezzi per evitare deformazioni degli stessi. La polvere non trattata può essere riutilizzata in combinazione con quella vergine. Non è necessario eseguire post trattamenti a parte la pulizia della polvere. Questa tecnologia additiva è molto utilizzata nell’ambito del termoplastico, poiché assicura prestazioni molto elevate, sia in termini di caratteristiche meccaniche che in termini di design.