Vediamo come un’officina toscana ha sviluppato gli stampi per la produzione di uno stendipanni a partire da materiale riciclato.
Più o meno a tutti capita di stendere i panni ad asciugare su uno “stendino” di plastica. Non a tutti, però, viene spontaneo porsi la domanda: “Com’è stato costruito questo stendipanni?” Noi di Stampi ce lo siamo chiesti e, a tal fine, abbiamo fatto la conoscenza di un’officina toscana che opera con successo da anni nel settore dei casalinghi, la SP Costruzioni Stampi S.r.l. di Montelupo Fiorentino (FI), realtà guidata dai fratelli Andrea e Alfonso Pascale e specializzata nella costruzione di stampi a iniezione per materiale termoplastico destinati a svariati settori industriali.
Un caso concreto
Alfonso Pascale ci propone un esempio concreto e di particolare interesse, trattandosi di un manufatto progettato per essere realizzato in maniera specifica con plastica riciclata: «Lo stendipanni in questione, chiamato “Raffaello”, è stato da noi sviluppato e disegnato per un cliente che opera nel settore dei casalinghi e che del prodotto che voleva realizzare ci aveva consegnato solo alcuni spunti progettuali. Proprio perché partivamo da zero, il lavoro di modellazione e di definizione delle matematiche è stato piuttosto laborioso: è durato all’incirca due settimane, ed è stato svolto ovviamente sotto la supervisione del cliente».
La parte più ostica del progetto ha riguardato senza dubbio la stabilità dello stendipanni. Andrea Pascale entra nel dettaglio: «Un oggetto del genere deve avere la caratteristica di costare poco all’utilizzatore finale ma al tempo stesso quella di essere un prodotto di qualità, il che significa, nello specifico, che deve essere facilmente ripiegabile, resistere al peso dei panni, avere un design che trasmetta solidità ed essere realmente stabile». Come anticipato, fu scelto di utilizzare un materiale un polipropilene caricato riciclato. Alfonso Pascale spiega: «Il motivo della scelta è presto detto: un materiale riciclato presenta alcune problematiche di lavorazione che potrebbero ripercuotersi sul numero di scarti e sulla qualità del prodotto finale. Tuttavia, ha un costo notevolmente inferiore, che può essere pari anche alla metà di quello di un materiale vergine. Per l’oggetto in questione, che non necessitava di precisioni spinte, ci sembrò la scelta migliore».
Plastica riciclata: pro e contro
Qual è il comportamento della plastica riciclata, rispetto a quella vergine, in fase di stampaggio? Andrea Pascale afferma: «Innanzitutto la qualità del prodotto finito, che è inferiore nel caso in cui si utilizzi un materiale riciclato. All’interno della nostra divisione di stampaggio, lo sfrido, cioè la quantità di pezzi che non rispecchia le tolleranze di progetto, si aggira intorno all’1% qualora venga adoperato materiale vergine. Nel caso del materiale riciclato, invece, questa percentuale può variare di molto e raggiungere anche valori del 10%». Perché? «Perché la plastica vergine è in genere un materiale perfetto, di prima scelta, che viene controllato e testato prima della distribuzione sul mercato; le plastiche riciclate, probabilmente, sono costituiti da un mix di materiali in percentuali variabili, non ben definite, e che non è detto che leghino tra di loro in maniera perfetta». Le proprietà chimico-fisiche, dunque, possono variare di volta in volta, in base alla “catena del riciclo”; del resto, è noto che esistano migliaia di famiglie di materiali termoplastici sul mercato, e ognuna di esse presenta caratteristiche e qualità differenti; non è detto dunque che mettendo insieme tipi di famiglie solo all’apparenza uguali si ottenga un prodotto omogeno. «Questa disomogeneità – riprende Alfonso Pascale – si ripercuote sulla qualità del prodotto finale, ecco perché le plastiche da riciclo sono indicate per prodotti in cui è necessario “calmierare” il costo di produzione e per i quali non è richiesta una precisione spinta». Al fine di rendere tali materiali utilizzabili anche per applicazioni più tecnologiche occorrerebbe che a valle dell’attuale catena del riciclo vi fosse un’ulteriore e più accurata fase di cernita, in modo da assemblare prodotti il più possibile simili e ottenere quindi materiali più raffinati e legati. «Tuttavia – aggiunge – tale operazione implicherebbe un aumento dei costi che forse renderebbe non così conveniente l’utilizzo delle plastiche riciclate. Insomma, è un discorso complesso che andrebbe affrontato ai maggiori livelli».
Poiché il materiale riciclato ha un comportamento non completamente stabile in fase di stampaggio, come si deve comportare lo stampista nella progettazione e della costruzione di uno stampo per plastiche da riciclo? Andrea Pascale sottolinea: «La differenza fondamentale riguarda l’ingresso del materiale fuso all’interno dello stampo. Nel caso del materiale vergine, l’iniezione avviene in maniera diretta, semplice e veloce; nel caso delle plastiche riciclate, invece, occorrono delle accortezze. Il materiale termoplastico fuso riciclato presenta nello specifico delle impurità che nel tempo, a determinate temperature, possono non solo abradere, cioè usurare precocemente i canali di iniezione ma anche tappare fori e canali». Per tale ragione, è necessario dotare lo stampo di canali e ugelli “a flusso libero”, cioè canali e ugelli aggiuntivi (o meglio, di servizio) senza testina, che permettano al materiale fuso di penetrare all’interno dello stampo con una portata maggiore; ciò al fine di superare gli “intoppi” determinati dalle impurità. Alfonso Pascale afferma: «Insomma, quando si costruisce uno stampo, è importante che a monte della progettazione il cliente scelga il materiale con il quale il pezzo finito deve essere realizzato, perché questo impone scelte costruttive diverse».
Una progettazione intelligente
Nel caso dello stendipanni Raffaello, come detto, fu scelto di utilizzare un materiale riciclato e di progettare e costruire gli stampi necessari a realizzare le diverse parti dello stendipanni utilizzando canali e ugelli a flusso libero attorno alle diverse figure. Per la definizione dei progetti e per la programmazione delle macchine utensili, i tecnici della SP Costruzioni Stampi dispongono di due stazioni con software CAD/CAM VISI della Vero Project, le quali sono collegate alle macchine a CNC mediante connessioni di rete. In merito alla progettazione, Alfonso Pascale entra nel dettaglio: «Dovemmo progettare gli stampi con il vincolo che sarebbero stati installati su presse del cliente da 1.200 tonnellate. Poiché, per dimensioni e tipologia di stampo, si tratta di una forza di chiusura non particolarmente elevata, dovemmo aumentare i punti di iniezione al fine di garantire il perfetto e completo riempimento di tutte le figure». La fase di progettazione durò all’incirca 10 giorni; successivamente, per maggiore sicurezza e per non avere problemi durante lo stampaggio presso il cliente, fu anche eseguita, in collaborazione con uno studio specializzato, una simulazione del riempimento all’interno degli stampi mediante il software VISI Flow della Vero Project. «La simulazione – prosegue Andrea – validò i nostri calcoli iniziali. Questo ci permise di passare alla fase di costruzione degli stampi con buona sicurezza circa il risultato finale».
Foratura profonda con punte a cannone
«Nel nostro stabilimento – informa Alfonso – lavorano macchine grazie alle quali fabbrichiamo stampi di medie e grandi dimensioni, fino a 10 tonnellate, e di elevato livello tecnologico». In particolare, nello stabilimento di Montelupo Fiorentino operano sette evoluti centri di lavoro a controllo numerico con mandrini ad alta velocità di marchi quali Soraluce, FIL, OMV e MZero. Sono presenti anche una fresatrice con struttura a portale gantry costruita dalla RCR di Firenze, diverse macchine di elettroerosione a filo e a tuffo, alcune delle quali della ONA e della Mitsubishi, e macchine più tradizionali quali fresatrici, torni, trapani e rettifiche…
Andrea Pascale specifica: «Per realizzare stampi come quelli richiesti per lo stendipanni Raffaello, occorrono praticamente tutte le macchine a nostra disposizione. Innanzitutto, si spianano le piastre, che in questo caso sono state realizzate in acciaio 1.2738, dopodiché si passa alle lavorazioni più impegnative, come per esempio le forature profonde o l’esecuzione delle zone in sottosquadra, per le quali adoperiamo le macchine a tre assi». La particolarità degli stampi in esame è che furono scomposti in due elementi porta-maschi, entrambi da inglobare nei portastampi e di dimensioni tali da poter essere lavorati sulle macchine per elettroerosione a tuffo eseguendo le varie nervature di rinforzo e i diversi dettagli. Sia gli elettrodi in grafite sia i sistemi di movimentazione furono realizzati da fornitori specializzati esterni su disegno della SP Costruzioni Stampi. Un’ulteriore peculiarità della costruzione fu l’esecuzione dei canali di iniezione, decisamente delicata, trattandosi di fori profondi fino a 1.000 mm e per i quali furono utilizzate punte a cannone sui centri di lavoro.
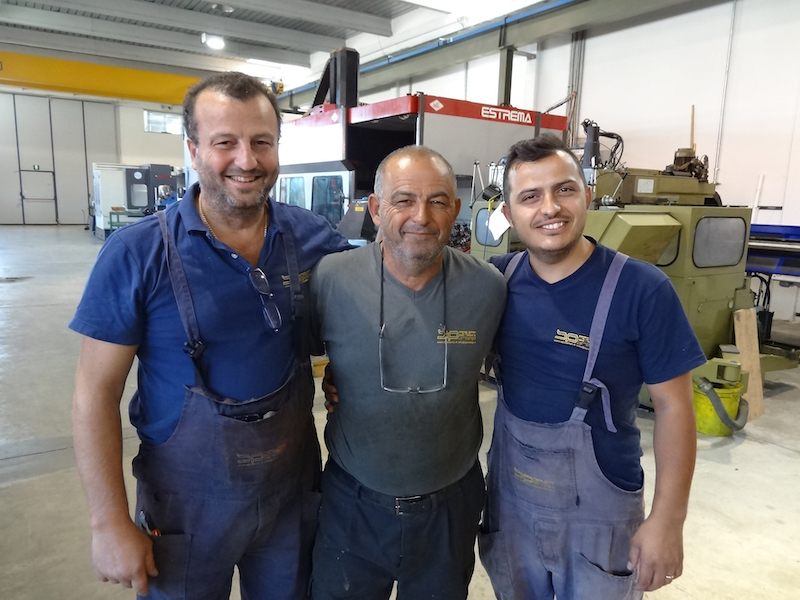
Da Raffaello a… Donatello!
Le lavorazioni meccaniche e le attività di assemblaggio durano complessivamente tre mesi, dopodiché si passò alla di regolazione degli stampi sulle presse del cliente. Alfonso Pascale conclude: «Fu necessario un altro mese per la messa a punto degli stampi su pressa, dopodiché si passò alla produzione vera e propria dello stendipanni Raffaello. Il cliente rimase talmente soddisfatto del nostro lavoro che seguirono altri ordini. Alla fine sviluppammo altri modelli di stendipanni, diversi per dimensioni, forma e funzionalità, l’ultimo dei quali prese nome di Donatello!».
Carta d’identità degli stampi
Pezzo finito: Stendipanni in polipropilene caricato riciclato Raffaello.
Costruttore: SP Costruzioni Stampi di Andrea e Alfonso Pascale s.n.c., via Tosco Romagnola Sud, 1, 50056 Montelupo Fiorentino (FI); tel.:+39 055 255043; sito internet: www.spstampi.it.
Cliente finale: confidenziale.
Materiale delle matrici: acciaio 1.2738.
Software CAD/CAM e simulazione: pacchetto VISI di Vero Solutions.
Tecnologie di produzione: centri di lavoro a 3-5 assi Soraluce, FIL, OMV, MZERO, RCR; elettroerosioni a filo e a tuffo ONA e Mitsubishi; macchine tradizionali.
Stampi “made in Toscana”
La SP Costruzioni Stampi S.r.l. di Montelupo Fiorentino (FI) è attiva dal 1994 nella produzione di stampi a iniezione per materiale termoplastico destinati al settore motoristico, ottico, idraulico, dei casalinghi e degli elettrodomestici. L’impresa conta su un ufficio tecnico che ha il compito non solo di disegnare e progettare gli stampi a partire da prototipi o dalle matematiche del pezzo finale, ma anche, all’occorrenza, di assistere il cliente nella fase di sviluppo prodotto. Dispone inoltre di un’attrezzeria assai evoluta e dotata di un significativo parco macchine, composto da centri di lavoro a CNC, elettroerosioni e macchine più tradizionali; si avvale inoltre di due presse da banco per l’attività di prova e di collaudo degli stampi. SP Costruzioni Stampi, che svolge anche un tempestivo servizio di assistenza e di manutenzione degli stampi in produzione, in modo da garantirne sempre e comunque il perfetto funzionamento, si avvale anche della collaborazione della consociata SPG Plast per attività di stampaggio, la quale dispone di 11 presse a iniezione con forza compresa tra 30 e 900 tonnellate, e opera con stampi realizzati sia dalla casa madre, sia da clienti esterni.
di Vittorio Pesce