Gli ingranaggi conici e ipoidi sono molto diffusi in applicazioni automobilistiche, industriali, marine e aeronautiche permettendo la trasmissione della potenza tra assi incrociati. I trend mostrano come il mercato sia alla costante ricerca di ingranaggi conici e ipoidi a elevate prestazioni e pesi ridotti. La capacità di carico è quindi un aspetto fondamentale da tenere in considerazione durante il processo di progettazione. Questo studio fornirà una panoramica della modalità di cedimento nota come frattura del fianco, con particolare riferimento al caso di ingranaggi conici e ipoidi. Inoltre, verrà spiegato nel dettaglio un metodo di calcolo semplificato di recente sviluppo per la determinazione della capacità di carico a frattura del fianco sulla base della geometria di un ingranaggio cilindrico virtuale secondo la norma ISO 10300 (2014).
Gli ingranaggi cilindrici cementati e gli ingranaggi conici sono elementi di macchine altamente sollecitati utilizzati per la trasmissione di potenza in un’ampia gamma di applicazioni. I trend di mercato mostrano come si sia sempre più alla ricerca di prestazioni aumentate e pesi ridotti. Pertanto, un aspetto importante durante la fase di progettazione degli ingranaggi è la loro capacità di carico per quanto riguarda tutte le modalità di cedimento. Oltre ai tipici cedimenti per fatica come pitting [27] e rottura del piede per flessione [12], che sono il risultato di cricche nucleate sulla o appena sotto la superficie, gli ingranaggi temprati mostrano spesso cricche che nucleano a profondità maggiori. Queste nuceano sotto la superficie del fianco attivo e si propagano in direzione del piede scaricato del dente. Questa modalità di cedimento è nota come frattura del fianco. La frattura del fianco si verifica in modo particolarmente frequentemente sugli ingranaggi conici a spirale ed ipoidi dato che queste tipologie mostrano raggi di curvatura relativa maggiori rispetto agli ingranaggi cilindrici a denti dritti o elicoidali [23]. Di conseguenza la massima sollecitazione di taglio si genera ad una profondità maggiore, dove il materiale mostra una resistenza ridotta (il trattamento termico non arriva a cuore). La frattura del fianco porta solitamente alla rottura totale del cambio in modo improvviso ed inaspettato poiché l’inizio e la propagazione della frattura avvengono al di sotto della superficie del dente e non possono pertanto essere identificati con ispezioni visive. In Figura 1 è mostrato un esempio di cedimento del fianco in un pignone conico.
La forma dei breakout per questa modalità di cedimento è caratteristica ed indipendente dalle dimensioni dell’ingranaggio. Si osservano le linee di spiaggia tipiche per i cedimenti a fatica nonché piccole aree di rottura finale. Un esempio breakout è mostrato in Figura 1 a destra.
FZG / Hertter [16] ha rilevato che potrebbe propagare anche una cricca secondaria in aggiunta a quella primaria. Questi risultati derivano da cambiamenti locali della rigidezza del dente causati dalla separazione interna del materiale per la frattura primaria. A partire dalla superficie, le cricche crescono parallelamente alla punta del dente e con un numero crescente di cicli di carico propagano verso l’interno del dente, dove possono raggiungere la fessura primaria e quindi arrestarsi. Cricche secondarie sono state osservate soprattutto in ingranaggi aventi larghezza elevata e grandi dimensioni.
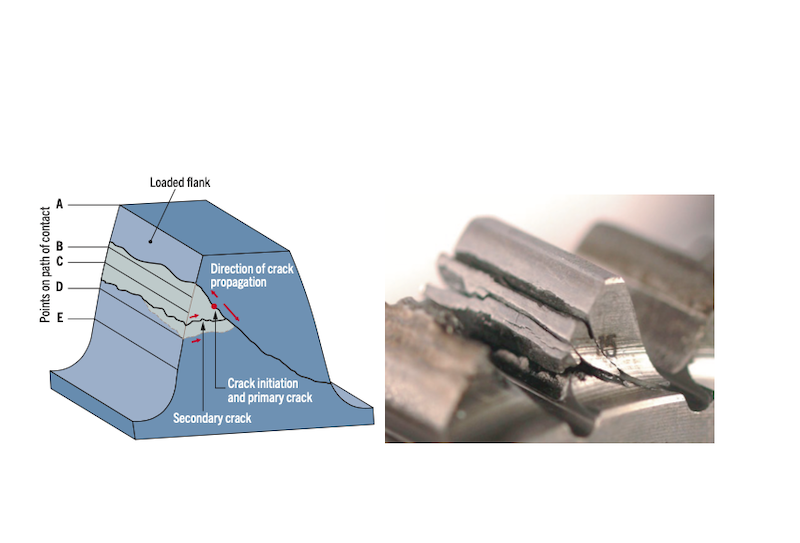
Frattura del fianco
Modalità di cedimento
I cedimenti per frattura del fianco del dente sono noti da diverse applicazioni come ingranaggi industriali [8] o ingranaggi appositamente progettati per indagini sperimentali [13, 25, 29].
La frattura del fianco è un cedimento tipico per fatica che si manifesta su diverse tipologie di ingranaggi a partire dalla nucleazione di una cricca sub-superficiale per le elevate sollecitazioni di taglio causate dalla pressione di contatto Hertziana. La cricca propaga dalla superficie del fianco attivo verso il piede del fianco opposto [20]. In Figura 2 è mostrato un esempio di cricca su un ingranaggio cilindrico. La propagazione della cricca avviene in modo analogo anche sugli ingranaggi conici e ipoidi.
Secondo FZG / Annast [7] la nucleazione della cricca sugli ingranaggi conici ed ipoidi si ha, nella maggior parte dei casi, al centro della larghezza di fascia a circa metà dell’altezza del dente. La cricca parte principalmente da inclusioni non metalliche che causano un aumento locale delle sollecitazioni e propaga poi verso il raccordo del fianco scarico. Nella direzione della larghezza di fascia, la cricca si propaga rimanendo parallela alla faccia stessa o leggermente inclinata verso la punta del dente [26].