Un sistema Industrial IOT di telemetria rivolto al settore dello stampaggio di materie plastiche e gomma, grazie al quale gli stampi diventano “smart”. Per saperne di più abbiamo intervistato il general manager di Mycros, Virginio Tartaglino.
Sviluppato da Mycros, TMold è un sistema Industrial IOT di telemetria degli stampi utilizzati nell’industria dello stampaggio di materie plastiche e gomma. Progettato per gestire la vita dello stampo, programmare le manutenzioni, gestire gli allarmi, controllare l’efficienza, ridurre i fermi, ridurre i costi di produzione, migliorare la progettazione e geolocalizzare gli stampi, questo sistema è inoltre predisposto per raggiungere gli obiettivi previsti per la Fabbrica 4.0. Gli stampi diventano dunque “smart” con l’applicazione dei sensori TMold, che comunicano con il sistema in cloud in modalità radiofrequenza, senza richiedere alcun cablaggio in officina. Di questo innovativo sistema e delle diverse dinamiche coinvolte ci ha parlato Virginio Tartaglino, general manager di Mycros.
Riflettori su obiettivi e finalità
«Lo stampo – esordisce Virginio Tartaglino – è un elemento basilare per poter produrre qualcosa di stampato, senza il quale cioè non si realizzerebbe nulla, invece è sempre stato un po’ “dimenticato”. Parlo della difficoltà di conoscere quante ore ha lavorato, quanti pezzi ha prodotto, che tipo di manutenzioni sono state eseguite e quando, con quale successo ha lavorato e se ha effettivamente risposto alle prerogative per cui è stato costruito, in termini di cadenza produttiva e di qualità del prodotto rilasciato». Su queste considerazioni di base si è quindi innestato il processo che ha portato Mycros a concepire e realizzare il sistema TMold. Tutto parte dal presupposto che se le informazioni non sono adeguatamente strutturate e archiviate non sono utilizzabili correttamente come dovrebbero. «Anche perché un obiettivo che va emergendo fortemente da quando finalmente si è compreso lo spirito della Fabbrica 4.0, che punta a far sì che le aziende abbiano interconnesso tutto ciò che utilizzano in produzione, è che le informazioni raccolte possano essere utilizzate per comprendere i punti critici delle fasi produttive». Un’operazione come quella dello stampaggio, che richiede una pressa, uno stampo, materiali e persone competenti, vede quale risultato della produzione la somma di tutte queste risorse che convergono nel momento dello stampaggio. Dunque avere sotto controllo lo stampo vuol dire avere effettivamente sotto controllo l’andamento dell’operazione di stampaggio nel suo complesso. «E questo – sottolinea Tartaglino – ci sembrava un obiettivo fondamentale da raggiungere».
Un altro sostanziale obiettivo che il sistema TMold si prefigge è quello di rendere sempre nota l’esistenza e l’ubicazione dello stampo. «Abbiamo constatato che nel caso dell’utilizzo degli stampi in più reparti o in diverse sedi dell’azienda, magari all’estero, capita spesso che non vi sia l’esatta conoscenza del luogo in cui gli stampi sono dislocati, e questo crea non pochi problemi. Con TMold è invece possibile geolocalizzare gli stampi, cioè sapere sempre esattamente dove si trovano in quel determinato momento. Non montiamo un GPS a bordo dello stampo: ci basta sapere, tramite il nostro sistema di comunicazione, prima di tutto se lo stampo c’è e poi se si trova in un reparto piuttosto che in un altro, o in uno stabilimento piuttosto che in un altro. Questo aiuta sostanzialmente nell’inventario, nella ricerca dello stampo e, di conseguenza, nel controllo dello stampo stesso e del suo utilizzo».
Il terzo, ma certo non ultimo, obiettivo fondamentale di TMold è quello della gestione del ciclo di vita dello stampo, potendo intervenire su questo per conoscerne le necessità. «Gli utenti – prosegue Tartaglino –, dal responsabile di produzione nel suo ufficio all’operatore a bordo macchina, al dirigente fuori sede che sta viaggiando in treno, possono accedere ai dati di produzione e inserire le informazioni che servono, perché essendo in cloud accedono con la classica password al nostro portale e possono quindi vedere da remoto come sta andando la produzione. Questo discorso ha un’importanza basilare anche per il manutentore, che è così in grado di sapere a che punto è il lavoro, se è necessario un intervento di manutenzione dello stampo o quanto tempo manca prima di dover fare il prossimo intervento. Certamente, a questo proposito, all’inizio è possibile gestire la manutenzione in forma preventiva e straordinaria, ma man mano che vengono accumulati i dati è possibile predisporre anche una modalità di gestione di manutenzione predittiva».
Dentro le dinamiche del sistema
Quali meccanismi operativi coinvolge TMold e quali prerogative implica la sua applicazione? «Iniziamo col dire che tutto converge in cloud – spiega Tartaglino – perché questo ci consente per prima cosa di non essere invasivi in azienda, ad esempio nel dover stendere cavi o realizzare installazioni a livello locale. Il sensore TMold comunica infatti in radiofrequenza con un gateway da noi fornito, utilizzando canali in radiofrequenza proprietari, che non disturbano altri sistemi di comunicazione aziendale». Non viene quindi utilizzato il Wi-Fi aziendale e non viene arrecato alcun intralcio alla struttura dell’azienda. È sufficiente che il cliente sia collegato in Internet e invii i dati direttamente al cloud di Mycros. «Ciò significa immediatezza e completezza del dato e possibilità di utilizzo in real time, e questa non è cosa da poco trattandosi di prodotti spesso sparsi per il mondo in diversi stabilimenti. Inoltre, noi non ci limitiamo a fornire il sensore, a raccogliere i dati e ad archiviarli in cloud, ma abbiamo completato il sistema TMold con analisi di Business Intelligence fruibile dall’utente». Questi ha infatti a disposizione una serie di widget che gli consentono di vedere lo stato dello stampo, oltre a fornire altre utili informazioni quali ad esempio eventuali allarmi all’operatore. Il sistema TMold, quindi, non si limita a una semplice acquisizione di dati che vengono scaricati su un database in cloud, ma li utilizza e fornisce utili indicazioni all’utente. «Va sottolineato inoltre – continua Tartaglino – che abbiamo impostato il sistema in modo da poter essere appreso e utilizzato facilmente, senza che sia necessario chissà quanto tempo per spiegarlo. Infatti, siamo riusciti a renderlo assolutamente molto intuitivo e prevediamo in tal senso interventi veramente spot, di una o due giornate al massimo, per avviare il tutto. Non per niente è un nostro punto fermo non voler realizzare un manuale d’uso, e questo la dice lunga sulla facilità di apprendimento del sistema».
Ma le opportunità offerte da TMold non si fermano ancora qui, perché possono coinvolgere addirittura il costruttore dello stampo. «Ci siamo resi conto, parlando con i clienti e vedendone l’utilizzo, che il nostro sistema consente anche di raccogliere tutta una serie di informazioni che interessano, oltre all’utilizzatore dello stampo, anche il costruttore. Quest’ultimo, infatti, molto spesso perde di vista lo stampo che ha progettato e realizzato, e qual è il suo comportamento in produzione: con TMold invece anche lo stampista, ovviamente a discrezione del proprietario dello stampo, può essere coinvolto nel conoscere il funzionamento dello stampo e la sua corrispondenza alle specifiche di progetto, giungendo con tutto questo a una logica di miglioramento progettuale ed esecutivo in un ambito più allargato, anche a monte della supply chain».
Non va dimenticato infine che TMold può essere utilizzato anche in forma totalmente integrata con il sistema MES di monitoraggio e controllo della produzione di Mycros. «TMold può essere posto come stand alone – precisa Tartaglino –, ma volendo, ovviamente senza che questo rappresenti obbligo alcuno, può essere integrato con il nostro sistema MES. Quest’ultimo, in tal caso, raccoglie i dati direttamente dalle presse e gestisce anche la programmazione dei lavori che le riguardano. L’intero reparto ha in questo modo una visione completa di tutto quello che sta succedendo e anche di quello che dovrà succedere. Avere un prodotto unico e uniforme è sicuramente vantaggioso per i clienti, non solo in termini pratici e di costi, ma soprattutto perché si ritrovano un unico sistema per la gestione sia della produzione in campo delle macchine sia di quella degli stampi».
Dalle idee ai fatti
Mycros Srl nasce sei anni fa come startup innovativa, con l’obiettivo di sviluppare sistemi avanzati legati all’ambiente della Fabbrica 4.0, argomento in tale periodo ancora sconosciuto a molti. «Siamo partiti con l’idea di realizzare sistemi di Industrial IoT legati al mondo delle aziende manifatturiere e, in particolare, di quelle rivolte allo stampaggio di materie plastiche e gomma – racconta Tartaglino –. Si tratta infatti di un settore che conosciamo bene perché la nostra provenienza di consulenti aziendali ci ha portati a effettuare numerosi interventi in società del comparto». Ben conoscendo quindi le tecnologie e le problematiche legate al mondo dello stampaggio di materie plastiche e gomma, i fondatori di Mycros si sono posti l’obiettivo di utilizzare le moderne tecnologie per poter individuare soluzioni particolari in grado di portare concreti benefici operativi. «Abbiamo studiato a lungo il nostro progetto TMold e ci è voluto del tempo per realizzarlo, ma il risultato ci ha portato grandi soddisfazioni, in un mercato dove lo stampo, nonostante la sua fondamentale importanza, è sempre stato considerato un po’ come la classica Cenerentola. Mycros è dunque partita come startup, con un numero ristretto di persone, ma è riuscita ad arrivare al risultato che si era preposta, con un prodotto di tutto rispetto qual è TMold, adesso pienamente operativo e già in uso presso alcune aziende che se ne dicono totalmente soddisfatte».
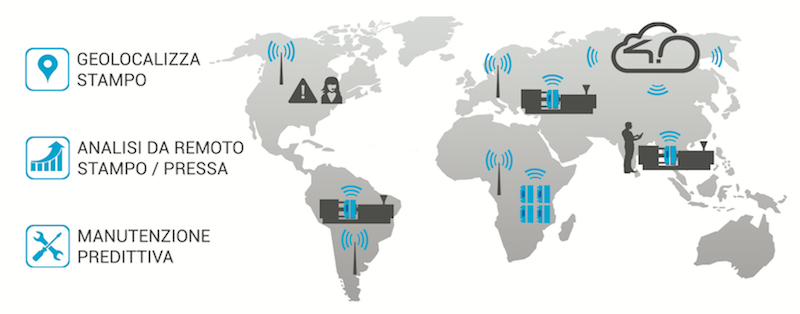
Fabbrica 4.0 e credito d’imposta al 40%
Il sistema TMold, predisposto per raggiungere gli obiettivi previsti per la Fabbrica 4.0, è stato appositamente costruito in questa ottica. «Abbiamo fatto in modo – chiarisce Tartaglino – che sia l’applicazione di TMold sia tutto ciò che vi è collegato potesse rientrare nei parametri di richiesta della Fabbrica 4.0, tant’è che il nostro prodotto è certificato come conforme, sia per la parte hardware sia per quella software, ai requisiti previsti dal Piano Calenda e può usufruire quindi dell’iperammortamento al 270%». Ma non solo. Anche gli stampi, grazie alla dotazione del sistema TMold, possono rientrare in tali benefici. «Benché lo stampo in sé non sia iperammortizzabile – conclude Tartaglino –, adottando il nostro sistema può diventarlo. Infatti, installando il sensore sullo stampo questo diviene parte integrante del processo produttivo ed è quindi interconnesso con il sistema di fabbrica: è così che, automaticamente, anche lo stampo è iperammortizzabile».
di Carla Casartelli