L’attività di stampaggio di alcuni manufatti molto complessi richiede scelte spesso innovative, per esempio in termini di automazione.
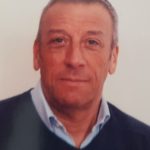
Abbiamo di recente visitato la Cobraplast S.p.A. di Leinì (TO), realtà specializzata nell’ingegnerizzazione e nella produzione di componenti in tecnopolimero, al fine di proporre un esempio concreto di “stampaggio” di pezzi complessi. Nel caso specifico, presentiamo in che modo Cobraplast ha sviluppato un’isola robotizzata dedicata allo stampaggio di un particolare di piccole dimensioni ma tecnologicamente significativo: il rotore di una pompa facente parte del sistema di raffreddamento dei motori elettrici sviluppati da un primario “car maker” europeo. Piercarlo Rizzini, responsabile tecnico costruzione stampi dell’impresa piemontese, illustra il caso: «Il rotore in questione è composto da uno “stack”, cioè da un’armatura inserita in un “involucro” di PPS, materiale termoplastico semicristallino ad alte prestazioni, rinforzato con fibre di vetro al 40%. Lo stack contiene quattro magneti permanenti sfasati di 90 gradi, i quali, una volta attivati dal cliente, determinano il flusso magnetico del rotore nel momento in cui questo è posto in rotazione».
L’automazione? Indispensabile
La produzione di un componente del genere è attività tutt’altro che banale, e Rizzini ne spiega i motivi: «Occorre innanzitutto precisare che non si tratta di un semplice stampaggio ma di costampaggio, in quanto il componente richiede l’immissione all’interno dello stampo sia della fase plastica, sia della fase metallica». Inoltre, per stampare in maniera efficiente un componente di questo tipo, è necessario ricorrere a un’automatizzazione di alto livello.
Rizzini prosegue: «Quando il cliente ci chiese di avviare la produzione del rotore, il nostro ufficio tecnico sviluppò e progettò immediatamente uno stampo adeguato, a due cavità, che poi fu costruito all’interno della nostra attrezzeria. Parallelamente, pensammo di implementare un ciclo di stampaggio che prevedesse un robot capace di inserire gli inserti metallici all’interno delle due cavità in maniera rapida e precisa. Tale soluzione avrebbe garantito produttività elevata, su tre turni di lavoro, qualità costante e scarti nulli, evitando problemi di stampaggi incompleti o di non corretto posizionamento delle parti».
Uno delle criticità principali da superare per avviare la produzione del rotore in questione fu quella dell’armatura metallica, che viene realizzata mediante l’impilamento di apposti lamierini magnetici. Rizzini specifica: «Gli stack, cioè le armature, ci vengono forniti da un ‘azienda molto importante nel settore. Tali armature sono composte da lamierini posti uno sopra l’altro e tenuti insieme da un collante speciale piuttosto delicato. Il numero dei lamierini, tuttavia, non è fisso ma può variare purché l’altezza dello stack rientri all’interno di una determinata tolleranza».
Per ovviare al problema dell’altezza variabile delle armature, i tecnici Cobraplast progettarono e costruirono lo stampo in modo che lo stesso fosse dotato di speciali molle affinché l’altezza della figura risultasse variabile e adattabile a seconda del caso. Rizzini entra nel dettaglio: «Vi era un altro problema. Durante la fase di movimentazione dello stack, il lamierino inferiore poteva staccarsi, per esempio a causa di movimenti troppo bruschi del robot o anche perché il robot non riusciva ad afferrare completamente l’intera pila di lamierini. Ciò determinava l’inserimento all’interno dello stampo di un numero minore di lamierini rispetto al previsto, e quindi la realizzazione di rotori dalle funzionalità non perfette». Per tale ragione, il robot antropomorfo fu dotato di magneti permanenti in grado di afferrare e bloccare in maniera precisa e gli inserti metallici senza che vi fossero errori o problemi di posizionamento all’interno dello stampo. Non solo: fu predisposta una tavola rotante, caratterizzata da 4 piastre, ognuna delle quali dotata di 36 sedi di forma cilindrica; e sul fondo di ogni sede vennero creati alcuni elementi di geometria tale da tenere sollevati i lamierini ferritici rispetto al corpo del rotore. Questo stratagemma non solo consentiva al robot di afferrare tutta la pila di lamierini, ma riduceva anche il rischio di urti, minimizzando il rischio che i lamierini potessero cadere a causa di colpi o movimenti bruschi.
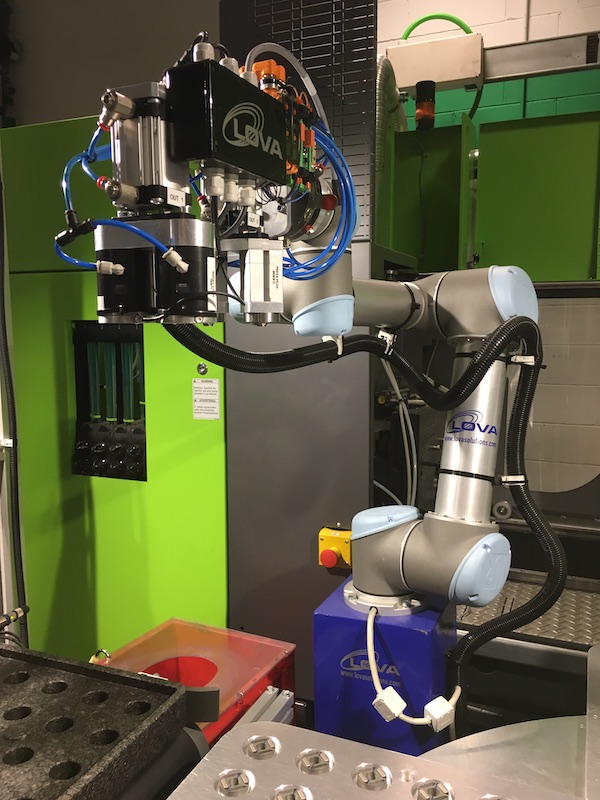
Ciclo ottimizzato e continuo
La soluzione sopra descritta, in uso ormai presso la Cobraplast da oltre un anno, assicura che gli inserti metallici siano inseriti tutti, e in maniera precisa, all’interno dello stampo. Tale “sicurezza” permette di automatizzare in maniera ottimale la fase di stampaggio la quale, dunque, avviene secondo il seguente processo: i componenti metallici vengono preventivamente immessi dall’operatore all’interno delle piastre. Qui sono riscaldati mediante opportune lampade in modo da raggiungere circa 100 °C, cioè la temperatura ottimale e adeguata alla fase di stampaggio. Successivamente, il robot li riconosce e li preleva per portarli alla verifica di una telecamera che controlla la presenza di tutti e quattro i magneti. Terminato il controllo, il robot inserisce, due alla volta, i particolari metallici all’interno dello stampo a due cavità installato su una pressa orizzontale Engel da 28 tonnellate. Qui avviene il co-stampaggio con un tempo ciclo pari a circa 30-25 secondi. Rizzini precisa: «Grazie al robot che effettua non solo le operazioni di carico, ma anche quelle di scarico dei pezzi e il controllo che i manufatti siano completi della parte metallica, lavoriamo in continuo stampando circa 240 rotori all’ora e con uno scarto nullo». Infatti, in presenza di qualsivoglia problema in termini di parametri di stampaggio, manipolazioni dei pezzi, bloccaggi indesiderati… la produzione viene arrestata immediatamente: questo garantisce la conformità totale dei prodotti realizzati.
Occorre inoltre segnalare che durante le fasi di lavoro, il compito dell’operatore è molto contenuto, limitandosi al posizionamento preventivo dei magneti all’interno degli stack: «Il grosso del lavoro – sottolinea Rizzini – viene svolto dal sistema automatizzato che esegue in velocità un elevato numero di attività; ecco perché è stato necessario scegliere un robot antropomorfo e non cartesiano. L’impiego del robot, inoltre, dispensa l’operatore dall’eseguire attività anche di un certo pericolo, come per esempio la movimentazione delle piastre ad alta temperatura, o in cui è facile commettere errori». È importante specificare che l’intera automazione fu progettata direttamente dal team Cobraplast, mentre l’implementazione operativa fu realizzata dalla Lova Solutions S.r.l. di Rivoli (TO).
La “curva di pressione”
Oltre all’automazione, la produzione del rotore in questione ha richiesto lo sviluppo di soluzioni raffinate anche dal punto di vista dello stampaggio. Rizzini osserva: «Il rotore in questione è un componente molto particolare, in cui la parte plastica è esigua, pari a soli 3 grammi, mentre quella metallica è predominante con circa 70 grammi di peso. Dunque, occorre regolare in maniera perfetta i parametri della pressa per evitare riempimenti impropri e formazioni di bave radiali che ne impedirebbero il perfetto montaggio sull’albero di rotazione e ne inficerebbero conseguentemente la funzionalità».
Inizialmente, quello delle bave, in effetti, fu un problema non da poco. «A causa della presenza di un numero variabile di lamierini all’interno delle gabbiette – continua Rizzini –, il nostro ufficio tecnico, come detto, sviluppò lo stampo dotandolo di “molle”. Questa soluzione, benché molto brillante perché permetteva di compensare le differenze in altezza degli stack, presentava tuttavia la controindicazione di generare bave radiali». Difatti, quando la plastica fusa penetrava all’interno dello stampo, tendeva inevitabilmente a riempire tutti gli spazi e le fughe, per esempio quelle generate dalla presenza delle molle, provocando così le bave. Rizzini aggiunge: «Il PPS è un materiale di grande stabilità dimensionale e di elevata resistenza alle alte temperature; inoltre, ha la caratteristica dell’alta fluidità, cioè è in grado di raggiungere giochi e interstizi anche di piccolissime dimensioni». Per superare tale criticità, l’idea fu quella di mettere a punto una “curva ideale di iniezione”, cioè di regolare, durante il ciclo, la pressione di stampaggio in modo che il materiale fuso non avesse la pressione sufficiente per raggiungere i giochi e generare successivamente le bave. «Se avessimo semplicemente ridotto la pressione di stampaggio – riassume Rizzini –, avremmo ottenuto un insufficiente riempimento dello stampo. Variando invece in maniera opportuna le pressioni durante il ciclo di stampaggio, siamo riusciti a ottenere il pezzo perfettamente realizzato e senza bave. Ovviamente, sono serviti diversi test e sperimentazioni, in quanto il PPS è un tecnopolimero “ostico” che richiede parametri di stampaggio decisamente spinti».
Lo sviluppo del pezzo, con sviluppo dello stampo e dell’isola automatica di stampaggio ha avuto inizio del 2017, ricevendo il benestare del cliente nel maggio 2018. Rizzini conclude: «Da allora il rotore è in produzione con grande soddisfazione, tanto che è in studio una seconda generazione che sarà implementata sui nuovi motori elettrici del “car maker” cliente».
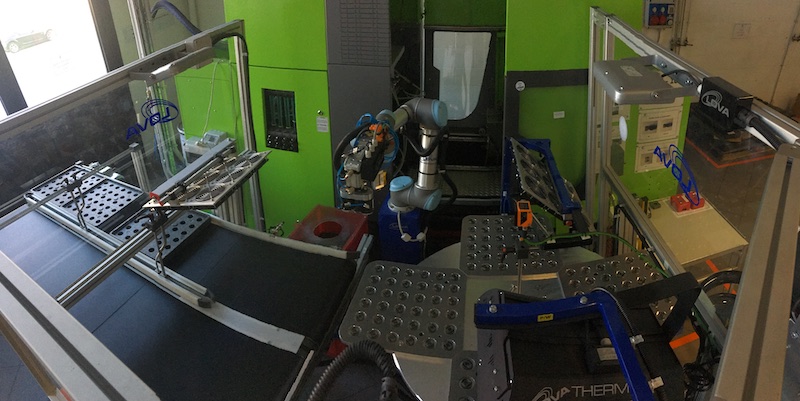
Reparto stampaggio: più di 30 presse

Cobraplast, casa specializzata nell’ingegnerizzazione e nella produzione di componenti in tecnopolimero, è attiva in ambito industriale, agricolo e soprattutto automotive. La società, che fornisce al cliente un servizio completo di ingegneria e di consulenza per la realizzazione di prototipi e di componenti in serie, progetta e costruisce anche relative attrezzature di produzione, e si avvale attualmente di circa 85 dipendenti. Attualmente, opera prevalentemente sul mercato internazionale, con una quota di export pari a circa il 60%. Cobraplast dispone inoltre di un ufficio tecnico e di un reparto Ricerca e Sviluppo molto attivo, che supporta il cliente nella definizione del progetto e nella scelta dei materiali migliori. In attrezzeria sono installate diverse macchine, tra cui due centri di lavoro a CNC, elettroerosioni a filo e a tuffo e rettificatrici di diverso tipo, grazie alle quali vengono costruiti stampi di piccola e media dimensione. Per gli stampi più grandi, invece, Cobraplast si avvale di stampisti esterni di fiducia, per lo più marchigiani. Per quel che riguarda infine la fase di produzione, l’attività dispone di un reparto stampaggio in cui sono installate più di 35 presse con forza di chiusura compresa tra 10 e 1.500 tonnellate.
di Vittorio Pesce