Di recente SKF ha introdotto il modello generalizzato di durata (GBLM, Generalized Bearing Life Model) per i cuscinetti volventi [1]. Da allora il lavoro è proseguito focalizzando l’attenzione su cuscinetti destinati ad applicazioni specifiche e sulla convalida sperimentale del modello. Un’applicazione ottimale di questo modello è il calcolo della durata teorica dei cuscinetti ibridi, ossia cuscinetti con anelli in acciaio e corpi volventi in materiale ceramico a base di nitruro di silicio (Si3N4).
I cuscinetti ibridi si utilizzano in condizioni estreme, ad esempio in applicazioni con scarsa lubrificazione e/o livelli elevati di contaminazione [2], [3]. A causa della maggiore rigidezza del materiale ceramico l’area di contatto hertziano è leggermente più piccola in un cuscinetto ibrido; di conseguenza la pressione di contatto e la sollecitazione sub-superficiale sono maggiori rispetto a quelle di un cuscinetto interamente in acciaio con una geometria equivalente. In linea di massima, questo dovrebbe causare una riduzione della durata a fatica del cuscinetto. Tuttavia, si è osservato che in applicazioni tipiche i cuscinetti ibridi hanno una durata maggiore. Come si spiega questo strano comportamento? Come modellarlo? Questo articolo risponde ai suddetti quesiti e dimostra anche che il GBLM può modellare e spiegare le osservazioni sul campo. Il GBLM SKF per cuscinetti ibridi sta per essere reso disponibile.
I cuscinetti ibridi hanno anelli in acciaio e corpi volventi in nitruro di silicio (Si3N4, Figura 1). Il nitruro di silicio è un materiale ceramico (ossia non metallico) caratterizzato da durezza elevata, modulo di elasticità elevato, resistenza alle alte temperature e agli agenti chimici, bassa densità e conducibilità e duttilità ridotte. Poiché il materiale ceramico a base di nitruro di silicio è un eccellente isolante elettrico, i cuscinetti ibridi si possono utilizzare per isolare in modo efficace l’alloggiamento dall’albero sia nei motori in c.a. e c.c. sia nei generatori elettrici. I cuscinetti ibridi offrono ottime prestazioni in condizioni di scarsa lubrificazione e in presenza di particelle di contaminante solide rispetto ai cuscinetti interamente in acciaio, anche se con lo stesso carico (a causa della più elevata rigidezza dei corpi volventi in ceramica) le sollecitazioni da contatto sono maggiori.
Inoltre, i cuscinetti ibridi presentano capacità di velocità più elevate e, nella maggior parte dei casi, offrono una maggiore durata di esercizio nelle stesse condizioni operative rispetto a cuscinetti interamente in acciaio delle stesse dimensioni. I cuscinetti ibridi offrono ottime prestazioni anche in condizioni di accelerazione, vibrazioni o oscillazioni elevate. Per applicazioni ad alta velocità come i turbocompressori e i mandrini delle macchine utensili, potrebbero essere necessari cuscinetti con geometria interna specifica. Si auspica che questa tendenza continui e che molte altre applicazioni industriali moderne scoprano e traggano vantaggio dalle capacità uniche offerte dai cuscinetti ibridi.
L’impiego di materiali ceramici fu proposto per la prima volta negli anni ‘60 per cuscinetti utilizzati a temperature estreme in applicazioni aerospaziali. Mediante test di fatica dei componenti è stato dimostrato che il nitruro di silicio pressato a caldo presenta le migliori caratteristiche di fatica da contatto di rotolamento rispetto ad altri materiali ceramici. Si sono riscontrate variazioni significative nelle prestazioni a fatica in lotti di produzione di sfere in nitruro di silicio apparentemente identici. Negli anni ‘80 Lorösch et al. (1980) [4] hanno eseguito dei test di durata a fatica di cuscinetti obliqui a sfere ibridi. Utilizzando sfere in nitruro di silicio della migliore qualità disponibile, hanno scoperto che la resistenza a fatica da contatto di rotolamento dei cuscinetti ibridi è paragonabile a quella dei cuscinetti interamente in acciaio sottoposti allo stesso carico, nonostante l’aumento del 12% della pressione di contatto presente nei cuscinetti ibridi. Tuttavia, con un altro test eseguito su un secondo lotto di sfere in nitruro di silicio si è ottenuta una durata a fatica ridotta, che evidenzia la criticità della qualità delle sfere in ceramica nel raggiungere prestazioni di durata a fatica ottimali.
Negli anni la qualità e l’affidabilità dei corpi volventi in ceramica sono migliorate in modo significativo. L’introduzione di metodi di valutazione non distruttiva (NDE, Non-Destructive Evaluation), in combinazione con il miglioramento continuo della purezza del materiale a base di nitruro di silicio e della tecnologia di sinterizzazione, ha infine consentito agli ingegneri di ottenere prestazioni a fatica da contatto di rotolamento affidabili e costanti per le sfere in nitruro di silicio, Galbato et al. (1992) [5]. Grazie a questo, negli anni ‘90 si è registrato un notevole incremento nell’impiego di cuscinetti ibridi nei mandrini delle macchine utensili ad alta velocità, con vantaggi considerevoli in termini di massime velocità raggiungibili e di precisione di questi componenti meccanici, Cundill (1993) [6]. La Figura 2 mostra il miglioramento della resistenza a fatica della ceramica, Cundill (1990) [7], attribuibile al migliorato processo di pressatura isostatica a caldo (hot-pressing sintering) e alla continua riduzione delle porosità e dei difetti superficiali in tutto il processo di lavorazione (ora controllabile mediante test non distruttivi).
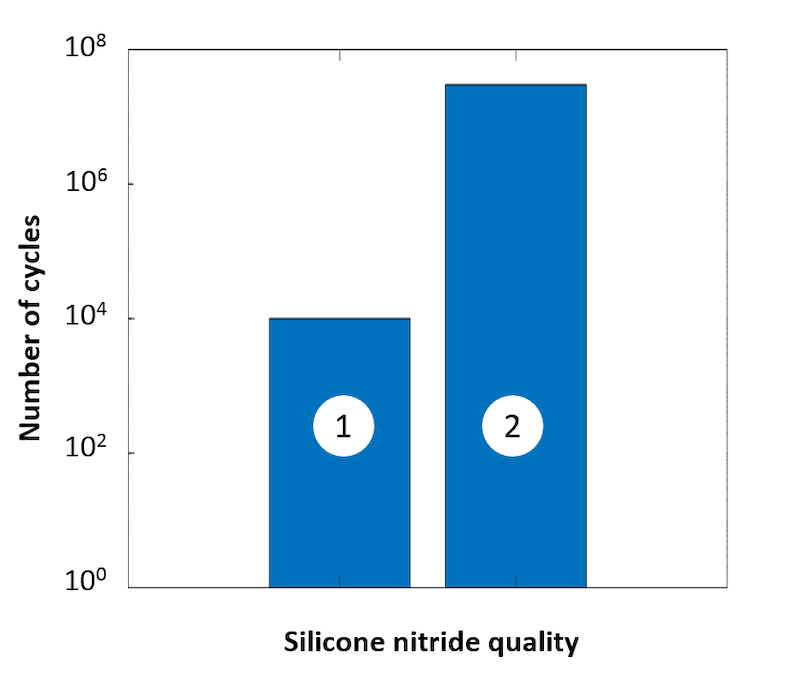
Obiettivo dello studio
Analizzando il processo di sviluppo dei cuscinetti ibridi è emerso che la resistenza a fatica del nitruro di silicio per cuscinetti ha fatto progressi straordinari negli ultimi 20 anni. Fin dai primi anni ‘80 le prestazioni della fatica da contatto di rotolamento (RCF) delle sfere in nitruro di silicio hanno registrato un incremento di due ordini di grandezza. I test di durata a fatica dei cuscinetti ibridi hanno dimostrato in modo inequivocabile che l’elemento volvente in ceramica è il componente più affidabile del sistema cuscinetto. Tuttavia, l’impatto dell’aumento del 12% della pressione di contatto presente nei cuscinetti ibridi è una caratteristica che si può osservare in condizioni operative in cui la fatica da contatto sub-superficiale è il meccanismo di danneggiamento predominante nelle prestazioni del cuscinetto.
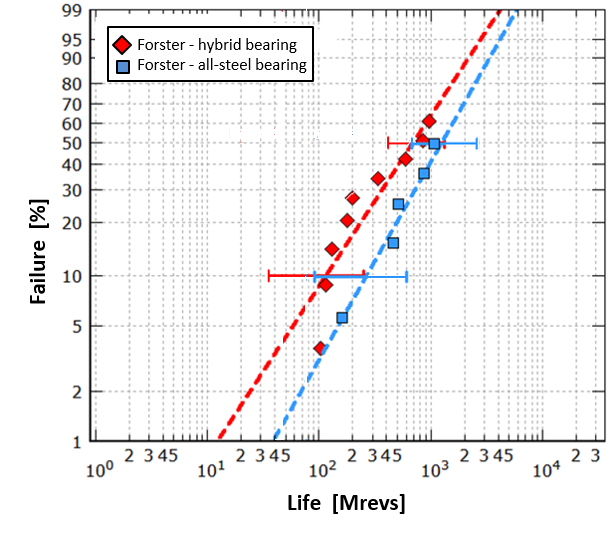
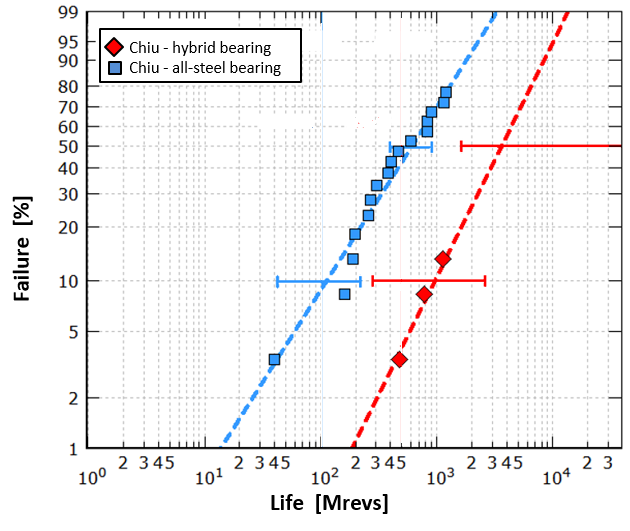