Realizzare anche in co-design e/o in co-engineering con il cliente componenti e assiemi complessi, di piccole-medie dimensioni, prevalentemente in acciaio inossidabile, stampati in milioni di pezzi, laddove richiesto accuratamente lavati con tecnologia a ultrasuoni, ed eventualmente anche saldati e assemblati. È questo un esempio di tipica fornitura gestita da I.M.A. Industria Meccanica di Arosio, qualificato partner per la lavorazione della lamiera di importanti clienti nazionali e internazionali, attivi in svariati settori tra cui l’automotive e quello dell’edilizia industrializzata.
«Per il settore automotive – spiega l’amministratore delegato, ing. Luca Redaelli – annoveriamo tra i nostri clienti aziende al primo livello della catena di fornitura dei costruttori di veicoli, per i quali realizziamo stampi per esempio per lo stampaggio, sempre al nostro interno, di componenti per turbocompressori, per serrature auto, oltre a elementi destinati a tutta la parte di power-train. Nel settore dell’edilizia industrializzata serviamo clienti specializzati nel settore dei fissaggi e dei sistemi di sicurezza antincendio. A questi si aggiungono poi anche altre forniture per il settore dell’arredamento ad aziende attive a livello mondiale nel contract per uffici, piuttosto che realtà operanti nei settori degli articoli tecnici per la general industry, per il mondo dell’elettrodomestico e quello delle attrezzature sportive».
Denominatore comune e trasversale nei vari settori rimane in ogni caso la complessità dei pezzi, di varia tipologia e impiego, che spaziano da assiemi assemblati (anche fino a 80 componenti) a semplici tranciati di precisione in spessori che, a seconda delle necessità, variano da 0,25 a 8 mm. In questo contesto know-how, competenza e approccio innovativo guidano in I.M.A. l’utilizzo di un ampio portafoglio di tecnologie interne all’azienda.
«Per la tranciatura – precisa l’ing. Redaelli – disponiamo di più di una cinquantina di presse, con tonnellaggi da 20 a 800 tonnellate, di svariate linee di saldatura robotizzata Mig/Mag e laser, oltre a linee specifiche completamente automatizzate e sviluppate totalmente al nostro interno per le fasi di assemblaggio».
Tra le citate presse ci sono anche tre macchine progettate e realizzate da Oti Presse di Desio (MI), una delle quali è una performante 800 tonnellate, completa di transfer elettronico Di.Gi.Emme.
Migliore qualità in fase di stampaggio
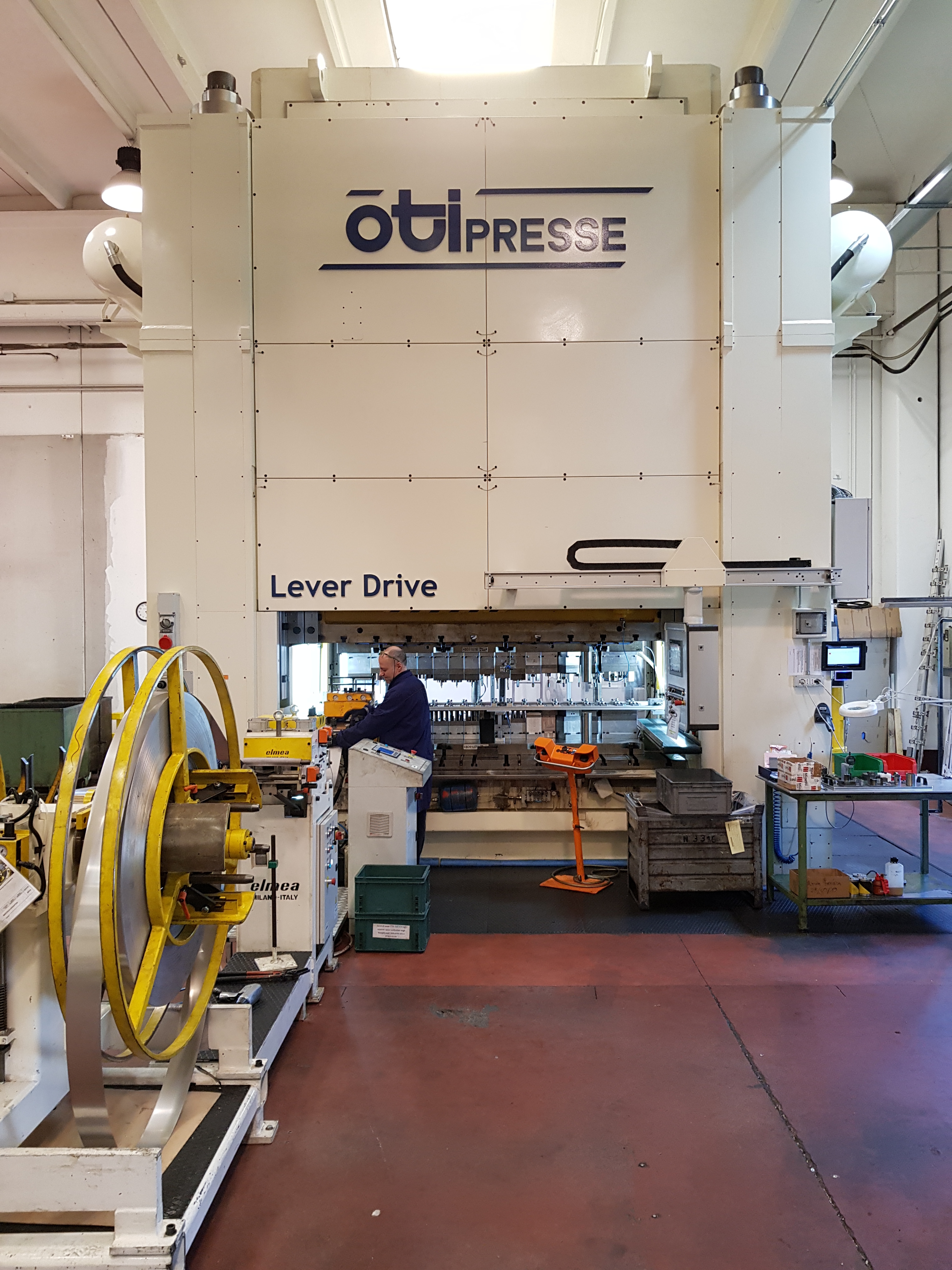
«La necessità di integrare la pressa Oti da 800 tonnellate – osserva l’ing. Redaelli – risponde alle richieste avanzate soprattutto dal comparto automotive, ovvero di disporre di un impianto di backup per alcune produzioni ritenute critiche, per dare continuità anche in caso di stop momentanei».
Motivo per cui è stata ordinata la macchina, con piano di lavoro di dimensioni abbastanza generose, tipiche per alcune commesse destinate al mondo automotive, con stampi finanche di 2,5 m di lunghezza ma che devono rispondere a precisioni molto elevate.
«Attualmente – continua l’ing. Redaelli – la macchina è in produzione continua con uno stampo di basetta per dissipatore di calore per microprocessore di comando cambio auto. Un componente caratterizzato da una coniatura importante che deve soddisfare una planarità di 7 centesimi».
Precisione e migliore qualità in fase di stampaggio garantita dal movimento rallentato, ovvero dal sistema “Lever Drive”, della pressa transfer studiata da Oti Presse e completa di transfer elettronico Di.Gi.Emme con piano di lavoro 3.000 x 1.500 mm e corsa regolabile fino a 300 mm. Le presse con rallentamento permettono infatti di ridurre la velocità della slitta prima del contatto con la lamiera, apportando significativi vantaggi: migliore qualità del prodotto tranciato/imbutito; aumento della produttività con particolari che richiedono un impatto lento a causa della formazione di bave o stiramenti sul materiale; maggiore durata degli utensili; riduzione della rumorosità e delle vibrazioni con conseguente possibilità di aumentare il numero di cicli al minuto.
Sostanziale aumento di produttività
Come già menzionato, in I.M.A. sono presenti tre presse fornite da Oti Presse. Oltre alla 800 ton ci sono due altre macchine progettate e realizzate dal costruttore: una pressa da 300 ton, piano di lavoro 2.100 x 1.000 mm con cambio corsa automatico 20-300 mm, colpi 20 – 75 al minuto, anche questa completa di transfer elettronico Di.Gi.Emme; una pressa, tra l’altro l’ultima installata in ordine di tempo, con potenza da 120 ton, a corsa fissa 30 mm, 30 – 230 colpi al minuto, con apertura rapida della slitta di 80 mm per permettere l’ispezione stampo.
«Una pressa, quest’ultima – sottolinea l’ing. Redaelli – molto compatta, pensata specificatamente per una tipologia di prodotto destinato al mercato dell’edilizia industrializzata. Mi riferisco all’imbutitura con uno stampo a 9 figure di una sorta di rondella che ha la particolarità di avere la tranciatura del foro interno dal basso verso l’alto. Ciò perché la rondella stessa non abbia bava nella parte in cui appoggia».
Una rondella che in 15 anni è stata prodotta da I.M.A. in ben 1,5 miliardi di pezzi.
«Rispetto alla produzione effettuata sulla precedente pressa – rileva lo stesso ing. Redaelli – oggi con i 220 colpi garantiti dalla nuova macchina di Oti Presse abbiamo praticamente raddoppiato il processo, ovvero dimezzato i tempi, potendo arrivare a ben 200 milioni di rondelle stampate all’anno».
Soddisfatta delle presse fornite da Oti Presse, l’azienda ha molto apprezzato anche la disponibilità e capacità del costruttore nel riuscire a recepire i precisi requisiti tecnici, proponendosi talvolta anche con soluzioni fuori standard e non convenzionali.
«Ritengo tutt’altro che scontata – conferma l’ing. Redaelli – la disponibilità nell’esser riuscito a dimensionare in modo adeguato la pressa da 800 ton, per fornire le prestazioni richieste, riuscendo nel contempo a contenerne l’ingombro secondo i nostri spazi in altezza. Andando dunque a realizzare su misura anche tutta la struttura. Altrettanto fondamentale e apprezzata è l’assistenza e il supporto repentina in caso di manutenzione o in caso di improvvise anomalie, peraltro molto rare nonostante gli anni e l’intenso e continuo funzionamento».
Qualità ai massimi livelli
Tutti i processi tecnologici e produttivi sono gestiti in I.M.A. secondo i requisiti della specifica tecnica automotive IATF 16949, ovvero con una qualità di processo e di prodotto che giocoforza rappresentano un “must sinergico” che accompagna ogni commessa: dall’analisi di fattibilità iniziale alla presentazione dell’offerta, dalla realizzazione delle attrezzature allo stampaggio.
«In questo – osserva l’ing. Redaelli – giocano un ruolo fondamentale anche gli evoluti software di simulazione e di gestione di cui siamo dotati e che ci aiutano in un’ottica 4.0 sempre più spinta».
Anche le nuove presse acquisite da Oti Presse sono collegate in rete, per un controllo della produzione evoluto secondo i termini richiesti da Industria 4.0, ma l’azienda è già da molti anni che ha sviluppato una propria metodologia operativa orientata all’efficienza e alla maggiore competitività.
«Cerchiamo di far leva su tutti quegli elementi – conclude l’ing. Redaelli – che possano differenziarci sul mercato, renderci sempre più competitivi. Ed anche l’attenzione alla qualità ci aiuta. Qualità di prodotto stampato, confermato dal nostro preposto reparto dove vengono testati i più svariati parametri dimensionali, di resistenza, trazione ecc. Da sottolineare che anche lo scorso anno siamo riusciti a mantenere il limite di 3 ppm, ovvero 3 parti non conformi per milione di pezzi consegnati, che per il mondo della lamiera rappresenta un obiettivo molto impegnativo e sfidante».
Attenzione alla qualità che coinvolge non solo la fase di tranciatura ma anche le fasi successive come l’assemblaggio e l’eventuale lavaggio. A questo proposito I.M.A. vanta anche un laboratorio dedicato all’analisi della pulizia dei componenti. I nuovi requisiti che interessano i prodotti impiegati in ambito motore sono infatti sempre più spinti. Motivo per cui servono non solo adeguate tecnologie di pulizia, ma anche procedure di controllo per confermare se i livelli di purezza siano quelli attesi. Pulizia che l’azienda garantisce sino a 200 micron con tre performanti macchine di lavaggio a ultrasuoni.
Articolo a cura di Gianandrea Mazzola