Nuovi materiali per ridurre i costi dei motori per veicoli elettrici
I materiali ad alte prestazioni possono aumentare l’efficienza del motore elettrico e ridurre i costi? Viene analizzata nel dettaglio la progettazione del sistema di isolamento della macchina sincrona a magneti permanenti (PMSM).
All’aumentare delle vendite di veicoli elettrici (EV) i produttori di motori elettrici (“e-motor”) per veicoli elettrici sono sotto pressione per sviluppare motori con una densità di potenza superiore e ingombri ridotti in modo economicamente vantaggioso. In questa ricerca la maggior parte dei costruttori di motori ha scelto di utilizzare la macchina sincrona a magneti permanenti (PMSM), in quanto questo tipo di motore ha una maggiore efficienza e occupa meno spazio rispetto ad altri tipi di motori elettrici – in parole povere, è più piccolo e più efficiente dal punto di vista energetico. Inoltre, se la densità di potenza è definita come potenza per unità di volume, la PMSM offre una densità di potenza relativamente elevata rispetto alle alternative.
Tuttavia, la PMSM ha alcune limitazioni. La potenza elettrica può essere limitata da perdite meccaniche nei cuscinetti, negli avvolgimenti e nel nucleo, dove possono verificarsi correnti parassite, isteresi e riscaldamento per effetto Joule. La PMSM è progettata anche per disattivarsi a temperature che minacciano di danneggiare il suo isolamento interno, quindi la gestione termica è un fattore prestazionale cruciale per i motori elettrici dei veicoli elettrici – la configurazione del sistema di isolamento è, chiaramente, strumentale.
La PMSM pone anche limitazioni sui costi, in particolare perché utilizza magneti realizzati con terre rare (TR), che tipicamente rappresentano il 50-55% dei costi delle materie prime. Ridurre la quantità di TR utilizzate ridurrà significativamente il costo di una PMSM – e contribuirà a risparmiare preziose risorse.
Un modo per farlo è quello di migliorare l’isolamento interno della PMSM attraverso l’uso di resine impregnanti e carte per l’isolamento di fase. Per le macchine con avvolgimento distribuito, il rivestimento della cava e la resina impregnante offrono notevoli opportunità per migliorare la gestione termica e il loro utilizzo, a sua volta, aumenterà l’efficienza del motore. Tipicamente, i materiali isolanti utilizzati nella cava sono carta meta-aramidica in forma laminata, con un film polimerico al centro. È possibile utilizzare una gamma di film polimerici, a seconda delle prestazioni e delle esigenze di costo.
Come dovrebbe essere il materiale di rivestimento ideale per le cave?
Il materiale di rivestimento ideale per le cave è affidabile in caso di carichi di picco e ha migliori proprietà meccaniche, riducendo il rischio di difetti dell’avvolgimento e aumentando la resistenza alla perforazione, il che consente quindi un aumento della densità del rame e del rapporto di riempimento cava. Il sogno del progettista è quello di avere un rivestimento più sottile a parità di tensione di breakdown, con temperature di avvolgimento ridotte grazie all’uso di un materiale isolante con una conducibilità termica superiore a quella della carta meta-aramidica. L’isolante deve essere affidabile anche in ambienti difficili e in grado di resistere all’idrolisi e ad agenti chimici aggressivi.
Alla ricerca del “sogno” di un isolante di cava, gli ingegneri della Victrex hanno effettuato una simulazione sostituendo un materiale isolante per cave in laminato PET- carta meta-aramidica da 250 micron con un Film APTIV da 150 micron. Lavorando in collaborazione con Motor Design Ltd., specializzata in software di simulazione in grado di aiutare a migliorare le prestazioni dei motori elettrici e ottimizzare il loro raffreddamento, è stato simulato un test su un modello 2012 Nissan Leaf, utilizzando una PMSM da 80 kW.
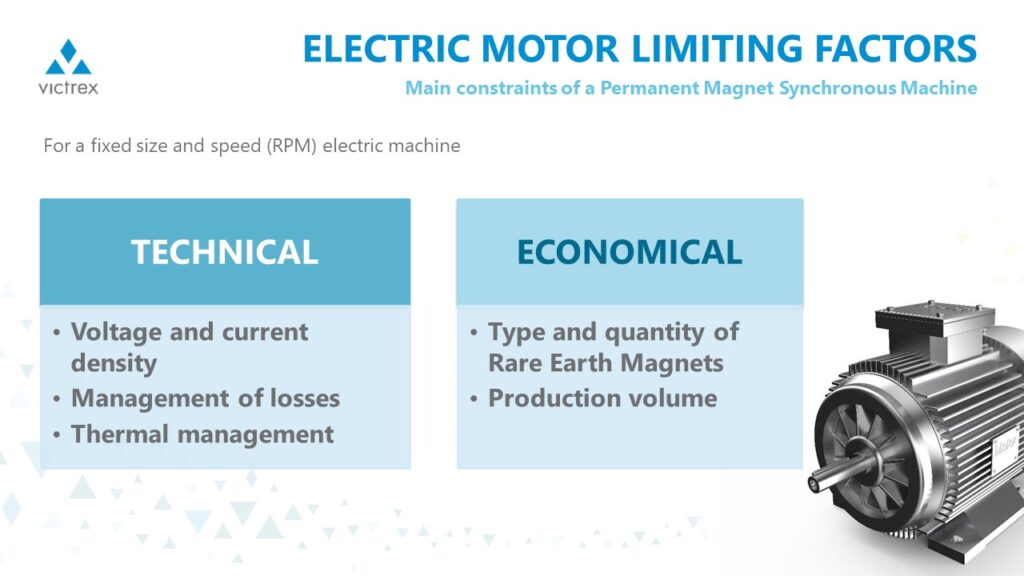
La soluzione: film APTIV
- L’utilizzo di un film termoplastico e termicamente conduttivo più sottile del 40% per l’isolamento delle cave consente un migliore flusso termico dei fili degli avvolgimenti verso il ferro dello statore e del sistema di raffreddamento a camicia d’acqua.
- L’eccellente conducibilità termica del film APTIV™ consente una migliore gestione termica e la riduzione delle temperature di picco dell’avvolgimento di 2-3°C, rispetto ai laminati tradizionali, e aiuta il raffreddamento del motore elettrico.
- Con una migliore gestione termica e con rivestimenti più sottili per le cave, c’è un potenziale aumento della densità del rame (cioè il fattore di riempimento cava) del 2%.
- C’è stato un aumento del 5% della coppia di uscita – questo si traduce in una maggiore potenza in uscita per una macchina a parità di dimensioni.
Risparmio sui costi grazie a una nuova soluzione di rivestimento per cave
Certo, il film APTIV™ è un isolante più costoso rispetto a una tipica carta meta-aramidica. Ma c’è un potenziale di riduzione dei costi quando le stesse prestazioni sono ottenute da una macchina più piccola, poiché la lunghezza assiale può essere ridotta senza compromettere la coppia continua in uscita o l’affidabilità. Ciò consente una riduzione dei costi della distinta base dei materiali del motore elettrico, in quanto è possibile ridurre il volume di ferro e magneti in TR, diminuendo il peso della macchina e, in ultima analisi, il veicolo stesso, riducendo potenzialmente i costi del carburante.
Inoltre, con un modello di calcolo dei costi basato su uno studio congiunto della Newcastle University e della Jaguar Land Rover (JLR), la simulazione Motor design Ltd. ha concluso che ci potrebbe essere una riduzione dei costi di 6,0 dollari per singolo motore.* In altre parole: l’utilizzo di un materiale isolante termoplastico di maggior valore, in questo caso il film APTIV™ della Victrex, può consentire un miglioramento delle prestazioni della macchina, permettendo un risparmio totale sui materiali di ogni singolo motore – e porre così fine alla ricerca del materiale di rivestimento ideale per le cave.
Maggiori dettagli su Vantaggi dei sistemi di isolamento a film APTIV™ nei motori elettrici
© Victrex plc. 2018. Tutti i diritti riservati.