Si presenta un nuovo processo produttivo, basato sulla fabbricazione additiva, in grado di “annegare” sensori e altri dispositivi elettronici all’interno di componenti in lega metallica. Questa innovazione, messa a punto presso il Politecnico di Torino, è dedicata a supportare la progettazione di sistemi “smart” interconnessi e mira a una nuova frontiera del monitoraggio strutturale.
Con l’avvento dell’Industria 4.0 e dell’Internet of Things (IoT), la condivisione dei dati è divenuta un tema centrale nell’innovazione industriale. In quest’ambito stanno nascendo nuove tipologie di componenti meccanici cosiddetti “smart”, ovvero in grado di interagire con l’ambiente circostante per misurare e condividere parametri di vario tipo [1]. Fra i dati di maggiore rilevanza ci sono la misura di carichi, accelerazioni, temperature e vibrazioni, insieme a parametri più complessi per la predizione dei guasti. Tali informazioni possono essere utilizzate per valutare lo stato di salute complessivo delle strutture, per confrontare i carichi effettivi con i carichi di progetto, o per rilevare le condizioni di funzionamento operative.
Fino a poco tempo fa, la sensorizzazione di componenti meccanici si avvaleva di metodologie tradizionali, basate su alcune tecniche precise fra cui l’installazione del sensore sulle superfici esterne, ad esempio mediate adesivi o collegamenti filettati, e l’installazione interna mediante operazioni di foratura o fresatura. I limiti di questi metodi di integrazione fra sensore e componente sono evidenti: nel primo caso, il sensore rimane esposto a urti meccanici, disturbi ambientali e contaminazioni di vario genere, oltre a rimanere generalmente distante dal punto di misura di reale interesse. Nel secondo caso, fori o canali devono essere realizzati secondo forme molto limitate, perlopiù cilindriche e comunque rettilinee.
Da queste considerazioni nasce il processo messo a punto presso il Dipartimento di Ingegneria Meccanica e Aerospaziale del Politecnico di Torino, sotto la guida del Prof. Giorgio De Pasquale, in collaborazione con il gruppo BeamIT. Il processo consente di “annegare” sensori e circuiti elettronici all’interno del componente.
Questo particolare processo di additive manufacturing trae spunto dalle tradizionali tecniche di microfusione di polveri metalliche (Laser Powder Bed Fusion, LPBF, o Selective Laser Melting, SLM), ai quali sono state introdotte sostanziali modifiche per renderli idonei allo scopo. Il risultato consiste nella possibilità di fabbricare componenti metallici in materiali diversi, all’interno dei quali posizionare elementi elettronici “nativi” ovvero presenti fin dalla creazione dei componenti stessi.
Il processo produttivo messo a punto unisce i vantaggi della sensorizzazione interna dei componenti alla versatilità della fabbricazione additiva. Il sensore risulta quindi perfettamente integrato nel metallo (senza giunzioni o interruzioni di sorta nel materiale), protetto, inalterabile e riparato dalle contaminazioni. La posizione del sensore non è vincolata a canali generati per asportazione di truciolo, pertanto può essere libera all’interno del volume. Nel caso di collegamenti cablati, il cavo stesso può seguire percorsi curvilinei all’interno del componente [2, 3].
Il particolare processo è stato finora validato per alcune famiglie di materiali, fra cui acciaio 17-4PH, Inconel In718 (Ni 53.2%, Cr 18.6%, Nb 5.34%, Mo 3.2%, Ti 1.0%, Al 0.5%, granulometria polvere 45 μm) e lega di alluminio AlSi10Mg (Si 9.21%, Fe 0.15%, Cu 0.001%, Mn 0.006%, Mg 0.27%, granulometria polvere 28 μm). A questi materiali sono stati inoltre applicati trattamenti termici post-processo di tipo diverso, comprendenti invecchiamento, solubilizzazione e tempra per l’ottimizzazione delle proprietà meccaniche.
Oltre ai vantaggi relativi all’integrazione dei sensori all’interno dei componenti, non si devono trascurare i plus legati alla fabbricazione additiva. Una progettazione dedicata del componente è necessaria per ottimizzare il rapporto resistenza/peso, per sfruttare la libertà di forma in applicazioni di scambio termico, per integrare più parti in un unico componente, per impiegare leghe più performanti e trattamenti termici di post-processo più efficienti [4, 5].
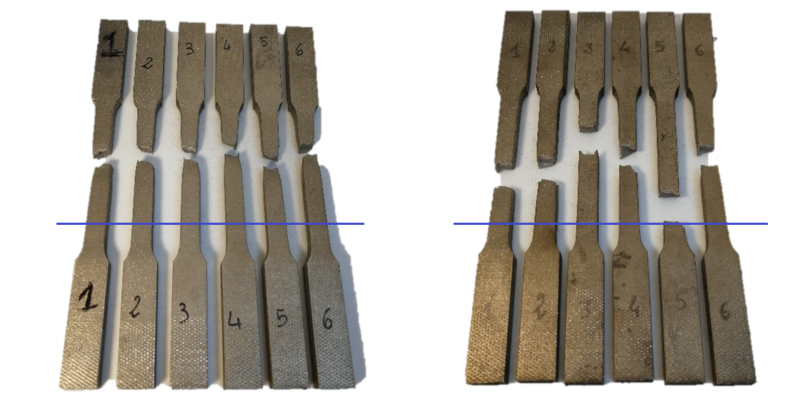
Interruzione del processo
Alla base del processo di integrazione dei sensori è la temporanea sospensione della microfusione delle polveri. Questa interruzione è normalmente considerata un evento accidentale indesiderato nella fabbricazione additiva LPBF dovuto per lo più ai seguenti fattori: a) mancanza di alimentazione elettrica, di gas inerte o di materiale; b) collisione della racla contro il componente in costruzione; c) guasto alle componenti del laser; d) blocco per malfunzionamento dei motori o dei filtri della macchina.
L’interruzione comporta inoltre l’apertura della camera e conseguentemente la perdita dell’atmosfera inerte, con relativa ossidazione della polvere e della superficie del componente, il raffreddamento della camera e del pezzo, un notevole allungamento del tempo di produzione (ripristino temperatura e atmosfera), la perdita di allineamento tra piano e racla, la comparsa di difetti estetici sul pezzo al livello della interruzione, il notevole abbassamento delle proprietà meccaniche al livello della interruzione. In modo particolare, il raffreddamento del pezzo ne comporta un ritiro per contrazione termica che non è sempre possibile recuperare con il ripristino della temperatura di regime. La perdita dell’atmosfera inerte porta all’ossidazione dello strato appena fuso e delle polveri presenti in macchina con il probabile aumento delle porosità. Oltre a tutto ciò bisogna considerare che non tutti i materiali sono inerti in aria: le leghe di titanio e alluminio, ad esempio, sono molto reattive sopra una certa temperatura se esposte all’atmosfera.
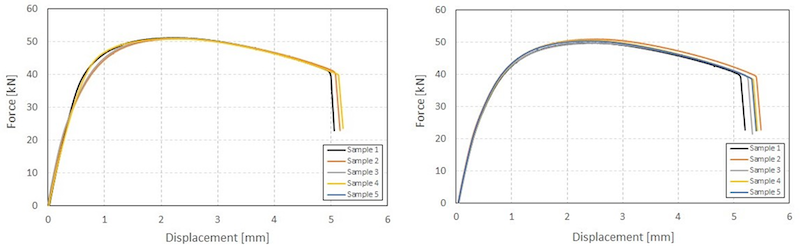
Il titanio ha una forte propensione all’ossidazione mentre le leghe di alluminio contengono discrete percentuali di manganese che, oltre a presentarsi come vapore tossico durante il processo di fusione, è pure molto reattivo in aria. La dimensione minuscola dei grani di polvere determinano una superficie di contatto con l’ossigeno estremamente elevata, che aumenta ancora di più la reattività.
Visto che l’interruzione del processo è solitamente un evento indesiderato, non sono presenti indagini significative in letteratura in merito ai suoi effetti [6]. Si è quindi reso necessario procedere a un’estensiva campagna di analisi del processo di microfusione per comprendere gli effetti dei parametri di macchina sulle proprietà finali di un componente sottoposto a sospensione temporanea della sua crescita. Per queste analisi sono stati stampati provini di trazione a sezione rettangolare e circolare secondo la normativa UNI EN 10002 con differenti orientazioni di crescita, per i quali il processo è stato sospeso temporaneamente (Figura 1). Al termine della campagna di indagine, determinati i parametri salienti del processo, è stato possibile ridurre al minimo gli effetti della sospensione della crescita sulle proprietà meccaniche finali, confermando quindi la possibilità di integrare componenti elettronici all’interno del materiale. Ulteriori fasi peculiari di questo processo innovativo, la cui proprietà intellettuale è stata oggetto di protezione, sono comunque necessarie.
In merito ai risultati ottenuti, a titolo di esempio, si riporta in Figura 2 un insieme di provini (In718) in cui la superficie di rottura susseguente alla prova di trazione risulta in modo evidente distante dalla linea di sospensione del processo di crescita. Questo è un primo significativo indicatore della non-sensitività delle proprietà meccaniche del materiale all’evento di sospensione. Un secondo indicatore della ottimizzazione del processo con sospensione si ricava dal confronto delle curve stress-strain del provino rispetto a un identico provino stampato senza interruzione, come si evidenzia in Figura 3.
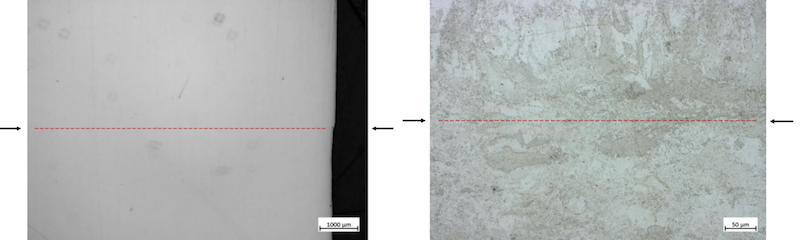
Infine, da ultimo, la definitiva conferma è fornita dall’analisi micrografica del materiale in corrispondenza della linea di sospensione del processo riportata in Figura 4. In questo caso si sono utilizzati specifici provini di dimensione 15x15x20 mm3 separati dalla piastra con elettroerosione a filo, lucidati, inglobati in resina e trattati in superficie con acqua regia sulle superfici da analizzare. Come si vede, la densità del materiale in corrispondenza dell’interruzione del processo è prossima al 100%, non evidenziandosi porosità o difetti di sorta. Allo stesso modo, l’ingrandimento più elevato non evidenzia discontinuità evidenti nei grani cristallini e in generale nella struttura cristallografica del metallo.