La purezza è una qualità molto ambita: così come l’acqua, anche un fluido da taglio deve essere puro. Cioè microfiltrato.
L’acqua è il bene più prezioso per la vita così come lo è il lubrorefrigerante nella maggior parte delle lavorazioni per asportazione di truciolo. Se l’uomo ha bisogno di acqua “pura”, lo stesso può dirsi per la macchina utensile che vuole un fluido da taglio purificato, cioè opportunamente filtrato. Per arrivare alla purificazione dell’acqua si ricorre all’osmosi inversa, cioè un processo che consente di rimuovere dall’acqua la quasi totalità delle sostanze in essa presenti, sia sospese che disciolte: l’acqua, fluendo attraverso una o più membrane semipermeabili, viene liberata dagli inquinanti che, concentrati, vengono poi scartati. Oltre alla purificazione, il grande vantaggio di questo processo è la continuità di passaggio dato che la membrana semipermeabile non viene intasata da particelle o inquinanti in quanto il flusso di acqua le trascina con sé, lasciando la membrana sempre pulita, a garanzia della continuità del potere filtrante. Se la purificazione dell’acqua avvenisse per microfiltrazione, ciò avverrebbe attraverso un processo che si avvale di elementi filtranti dapprima grossolani e poi sempre più sottili, fino ad arrivare a qualche micron: il problema riguarda gli inquinanti chimici presenti nel liquido, ma soprattutto gli elementi filtranti, che si intasano e vanno sostituiti spesso. Sfruttando l’analogia acqua-lubrorefrigerante, è evidente come in una macchina utensile che usa fluido da taglio, siano presenti sia particelle solide, che elementi chimici e batterici. Per quanto sia evidente che nessuno berrà mai un lubrorefrigerante, alcune domande dovrebbero però sorgere spontanee, prima fra tutte…
… a cosa serve la microfiltrazione? I costi giustificano il beneficio?
Dopo 1 o 2 mesi di circolazione all’interno di una macchina utensile, come sarà il lubrorefrigerante? Certamente sarà “ricco” di dispersioni, fra cui, solo per citare le evidenze macroscopiche, spiccano:
• trucioli di varie dimensioni
• oli estranei derivati sia da lavorazioni precedenti che da oli dispersi dalla macchina utensile; vernici, grafite e altri materiali leggeri che entrano all’interno dell’area di lavoro
• sabbie derivate dai carburi dei pezzi laminati o stampati
• pulviscolo metallico generato dal contatto fra utensile e materiale lavorato
• polveri ambientali, normalmente presenti negli ambienti di lavoro, che si depositano sulle macchine e vengono lavate dal fluido di processo
Parlando di dimensioni delle dispersioni, è evidente come si arrivi anche al micron, e sono proprio i micron che rappresentano un’insidia nascosta, ben nota agli addetti alla macchina utensile.
La tendenza è quella di agire su trucioli e oli, cercando di porre rimedio a situazioni caratterizzate da dimensioni grossolane ma problematiche: si intasano le pompe di rilancio, gli utensili, e gli oli degradano rapidamente il lubrorefrigerante. Al problema macroscopico si cerca da sempre di porre rimedio con sistemi basati su filtri a carta, cartucce filtranti, sistemi bypass e disoleatori che però non bloccano le particelle più piccole o microscopiche, che quindi circolano liberamente. Il risultato? Dopo 6/8 mesi le pareti e il fondo delle vasche sono ricoperti da uno strato di inquinanti, che non si riesce a eliminare. Al tatto, questo miscuglio si presenta come un abrasivo, il che suggerisce che si tratti di particelle, con granulometrie diverse e di materiali diversi che, se osservati al microscopio, si presentano estremamente frastagliati. Queste particelle, effettivamente abrasive, hanno una durezza che può variare da 30 a 70 HRC, e hanno dimensioni che normalmente sono compre- se fra 7÷8μm e 20μm.
«Se spostiamo l’attenzione all’interno della zona di lavoro della macchina utensile, è evidente che si sta utilizzando una miscela abrasiva – spiega Enrico Battistutta, ceo di RBM –. Pensiamo all’utensile che sta lavorando con una miscela abrasiva piuttosto dura al posto di un lubrificante e che più alziamo la pressione di lavoro, più il fenomeno diventa aggressivo; pensiamo al pezzo che potrebbe essere finito direttamente in macchina, ma siamo costretti a riprenderlo su rettifica per problemi di rugosità superficiale; pensiamo a come si possano aumentare i parametri di taglio, seguendo le indicazioni del costruttore dell’utensile, se non si riescono a ottenere le condizioni richieste di lubricità sull’utensile… Facendo proprie queste riflessioni, se le si valuta dal punto di vista dell’impatto economico, allora è chiaro perché i costi di una microfiltrazione, giustifichino il beneficio».
Un dato interessante viene dall’analisi gravimetrica, che indica quanti grammi di miscuglio abrasivo sono presenti per litro di lubrorefrigerante: in genere l’ordine di grandezza è di 0.15÷030 grammi/litro in aumento per ogni mese di ritardo nella pulizia delle vasche. Una microfiltrazione come quella di RBM, che lascia in circolazione 0.06÷0.08 grammi di abrasivo per ogni litro di emulsione, con particelle di dimensioni non superiori a 6÷7 μm, può chiaramente fare la differenza. E la differenza è riscontrabile nella maggior durata dell’utensile, del lubrorefrigerante e della macchina utensile, oltre che nella qualità della lavorazione.
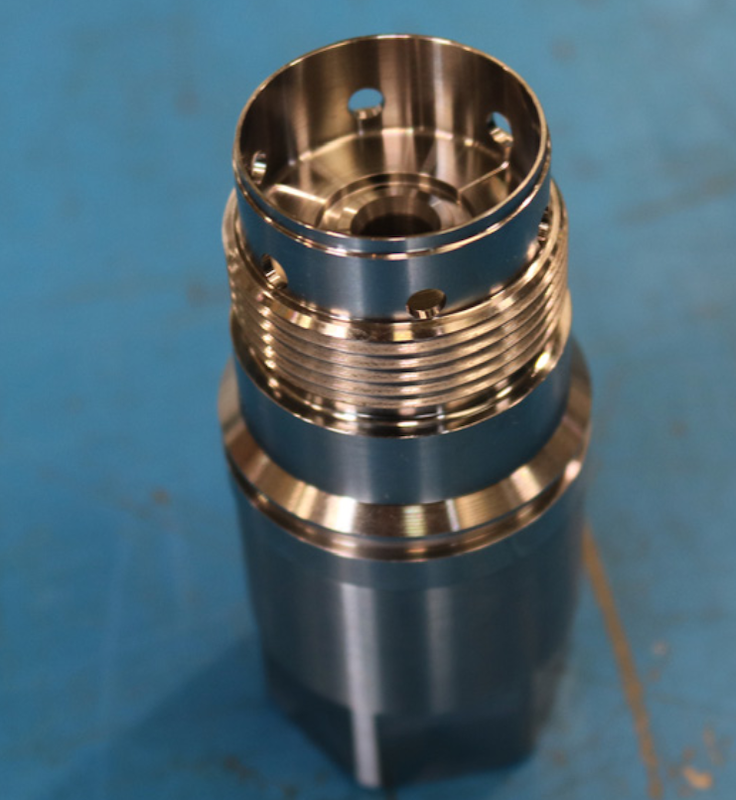
Una questione di cultura
Perché la microfiltrazione non è largamente diffusa? Una prima risposta riguarda la poca chiarezza riguardo la differenza fra filtrazione e microfiltrazione: microfiltrazione significa filtrare sotto 5÷7 μm, oltre è filtrazione. Si parla invece di nanofiltrazione se si è sotto il micron. Un’altra risposta è legata al potere filtrante dei più diffusi supporti, che, a causa della loro natura, si intasano progressivamente, arrivando a bloccare la lavorazione: una scelta largamente diffusa porta a scegliere una filtrazione “a maglie più larghe”, riducendo quindi il grado di filtrazione e rinunciando ai benefici di una microfiltrazione pur di poter lavorare.
«In RBM abbiamo ascoltato le richieste di tante officine, sia piccole realtà che importanti aziende internazionali, e abbiamo sviluppato una serie di sistemi che vanno contro corrente perché non utilizzano elementi filtranti – prosegue Battistutta –. Nello specifico mi riferisco ai sistemi IFDR e Core, dove la nostra tecnologia si comporta nei confronti del lubrorefrigerante come l’osmosi inversa con l’acqua potabile: fornisce un flusso di fluido microfiltrato e disoleato continuo, adeguato alle esigenze della macchina, senza consumabili, senza fermi macchina, lasciando cioè liberi di migliorare realmente le prestazioni sia della macchina che degli utensili».
Dove si applica la microfiltrazione?
Quando ha senso impiegare questa tecnologia? Quali sono le realtà o le applicazioni che hanno beneficiato dei vantaggi della microfiltrazione?
La dimensione dell’azienda è relativa: la vera discriminante sull’applicazione è il materiale lavorato, o anche il processo, che impone delle scelte specifiche per ottenere il risultato desiderato. «Nell’industria meccanica abbiamo realizzato applicazioni di microfiltrazione sia nell’ambito della fresatura che della tornitura. Ottimi risultati sono stati raggiunti nella fresatura di materiali compositi, dove vengono aggregati strati di materiali diversissimi mediante incollaggio. Abbiamo fresato a 5 assi materiali aggregati particolari, marmo e fibra di carbonio, per pezzi destinati all’industria del lusso; abbiamo applicazioni per la produzione di componenti ceramici in ambito elettronico; e abbiamo varie applicazioni di lavorazione di grafite per la realizzazione di elettrodi nel mondo degli stampi – proseguono da RBM –. Ma abbiamo case history che riguardano anche la tornitura per esempio nel campo dei sensori per il settore aereospaziale, dove il materiale, per via dei componenti e della durezza, produceva un truciolo paragonabile a polveri ad alta durezza ed estremamente abrasive. L’esigenza di microfiltrare sta iniziando a essere molto sentita ed è aumentata la sensibilità verso i problemi a essa collegati che devono trovare una soluzione altamente efficiente. La nuova linea di impianti IFDR Precision va proprio in questa direzione: dare una risposta economicamente adeguata che, guardando al futuro, possa permetter di lavorare in macchina con pressioni anche nell’ordine di 150÷250 atm, dando alle lavorazioni ulteriori vantaggi, vantaggi non raggiungibili senza una microfiltrazione che salvaguardi la macchina, le pompe, gli utensili e il pezzo in lavorazione».
I plus della soluzione IFDR Precision
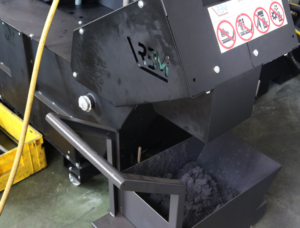
Come tutti i sistemi IFDR, anche la versione Precision è omologata alla Direttiva Macchine ed è certificata CE come macchina, e presenta diverse interessanti caratteristiche, fra cui:
• è un sistema brevettato di filtrazione inferiore a 5 μm;
• è un sistema integrato di disoleazione dinamica;
• permette una gestione efficace ed efficiente del fluido da taglio in alta pressione verso il mandrino;
• riduce il volume totale di fluido impiegato;
• riduce i costi di manutenzione grazie all’assenza di elementi filtranti;
• favorisce l’incremento della vita utensili grazie alla riduzione della granulometria inquinante presente nel fluido e alle condizioni di pressione e portata prescritte dal costruttore.
di Daniela Tommasi