Power skiving, nuovi inserti in metallo duro, PrimeTurning: questi tre nuovi modi di lavorare le trasmissioni possono aiutare i costruttori ad ottimizzare i processi.
Durante la pandemia le officine meccaniche hanno dovuto affrontare grandi variazioni della domanda. Tuttavia, indipendentemente dalle circostanze, la riduzione dei costi continua a rappresentare una priorità.
Prendiamo ad esempio la lavorazione degli ingranaggi. I costruttori desiderano una maggiore flessibilità nella lavorazione degli ingranaggi, ma ottenerla e ridurre al contempo i costi non è affatto semplice. Tradizionalmente, i progetti che coinvolgono la lavorazione di ingranaggi fanno affidamento su macchine e processi speciali, soprattutto nella produzione in serie. Questo implica dei limiti – e spesso maggiori costi – nei processi di produzione. Tre nuovi modi di lavorare le trasmissioni consentono di superare tali limiti. I vantaggi che ne derivano vanno anche oltre l’industria automobilistica, in settori come l’ingegneria generale, l’energia eolica, l’aerospaziale e perfino la robotica.
Power skiving e inserti in metallo duro
Il power skiving è una tecnica di taglio rotativo in cui l’utensile si innesta sull’ingranaggio in fase di realizzazione. Il processo di taglio continuo consente di eseguire l’intera lavorazione con un singolo setup. Essenzialmente, coniuga la dentatura a creatore e la formatura in un’operazione in cui l’angolo di intersezione tra l’utensile e gli assi degli ingranaggi e la velocità di rotazione sono decisivi per la produttività.
Il power skiving esiste da oltre 30 anni – quindi perché parlarne in un articolo che riguarda i nuovi modi per lavorare le trasmissioni? Perché il panorama della lavorazione sta cambiando in modi che influiranno su svariati settori, tra cui quello delle trasmissioni per i veicoli elettrici (EV). Entriamo nel dettaglio.
Veicoli elettrici
In precedenza, si riteneva che gli EV non avessero bisogno di marce o trasmissioni. Ma quest’idea è cambiata e case come Tesla e Porsche stanno implementando EV con cambi automatici multimarcia. I motori elettrici raggiungono valori di giri/min (giri al minuto) nettamente superiori alle auto tradizionali, con 20000 giri/min rispetto ai 4000-6000 giri/min dei motori a combustione tradizionali. Quindi, per portare i regimi a un livello gestibile, occorre un riduttore.
Le trasmissioni per i veicoli elettrici devono essere resistenti all’usura per sopportare regimi più elevati e, di conseguenza, sono più difficili da lavorare. Potrebbe essere meno ovvio che, nella produzione di tali componenti, i costruttori devono concentrarsi sulla velocità di asportazione del metallo, che esprime la velocità di lavorazione del pezzo.
Un altro requisito importante per le trasmissioni EV è la minore rumorosità del cambio, dato che il motore non genera rumore. Per farlo è necessario produrre componenti con tolleranze più strette, il che rende la lavorazione più complicata.
Dunque, le officine meccaniche dovrebbero chiedersi: puntiamo a una produttività rapida o a qualcos’altro? Una simile versatilità non è ottenibile con i processi di lavorazione tradizionali. Al contrario, il power skiving consente di lavorare componenti completi in una macchina multi-task o in un centro di lavoro con un singolo setup. Questo riduce i tempi di produzione, migliora la qualità e abbassa i costi di movimentazione e logistica.
I vantaggi del power skiving sono stati dimostrati da Sandvik Coromant quando un grande cliente svedese attivo nell’industria automobilistica ha chiesto nuove soluzioni per la lavorazione di un componente.
Collaborando con il team di sviluppo del cliente, il progetto ha dimostrato che è possibile eseguire il power skiving con due macchine a 5 assi, utilizzando la fresa a inserti multitaglienti per power skiving CoroMill 180 di Sandvik Coromant. CoroMill 180 è progettata per la produzione ad alto rendimento di ingranaggi e chiavette.
Il tempo ciclo raggiunto ha superato le aspettative: il cliente mirava a rimanere entro i 14 minuti per componente, ma ha ottenuto un tempo ciclo inferiore a 1 minuto per componente.
Industria aerospaziale
I vantaggi del power skiving non si limitano all’industria automobilistica, ma si estendono anche ad altri settori, tra cui l’ingegneria generale, le turbine eoliche, l’aerospaziale e la robotica. Tra questi, il settore aerospaziale sta dando particolare priorità alla riduzione dei costi. Gli effetti del Covid-19 sul settore sono stati ingenti, con Airbus che segnala un calo del tasso di produzione di velivoli del 30%.
Come nel caso degli EV, i motori aerospaziali più vecchi vengono aggiornati per fornire maggiori prestazioni ed efficienza, motivo per cui la produzione è destinata a evolversi. La flessibilità del power skiving può tornare molto utile in questi casi, ad esempio nella capacità di lavorare in prossimità di spallamenti, consentendo così una maggiore libertà nella progettazione dei componenti. Poiché i componenti aerospaziali sono realizzati in materiali più tenaci, occorrono anche inserti più tenaci.
A tal fine sono state presentate due nuove qualità d’inserto in metallo duro per la tornitura dei materiali ISO P, GC4415 e GC4425. La loro denominazione fa riferimento ai campi di applicazione ISO P15 e P25, ossia i requisiti che le varie condizioni di lavoro impongono sui parametri di lavorazione. Entrambe sono studiate per migliorare la resistenza all’usura e al calore e per offrire una maggiore tenacità. Gli inserti sono dotati della tecnologia Inveio di seconda generazione, con un orientamento unidirezionale dei cristalli nello strato di rivestimento di allumina. Ciascun cristallo è allineato nella stessa direzione – visibile a livello microscopico – per creare una solida barriera verso la zona di taglio, fornendo all’inserto una resistenza all’usura ancora maggiore e una durata utensile superiore. Come nel caso del power skiving, inserti come GC4415 e GC4425 forniscono un’usura prevedibile e consentono quindi di ottimizzare l’utilizzo delle macchine e risparmiare sui costi. Ancora una volta, i vantaggi non si limitano all’industria automobilistica ma si estendono a settori come l’ingegneria generale, l’energia eolica, l’aerospaziale e la robotica – di fatto, qualsiasi applicazione in cui si lavorino degli ingranaggi.
Indipendentemente dal settore, tra i vantaggi assodati troviamo il miglioramento dei volumi di truciolo asportato, la possibilità di lavorare componenti con un’unica macchina e un solo setup e il migliore utilizzo delle macchine. Secondo i risultati di Sandvik Coromant, un aumento del 20% nell’utilizzo delle macchine può corrispondere a un margine di profitto lordo superiore del 10%.
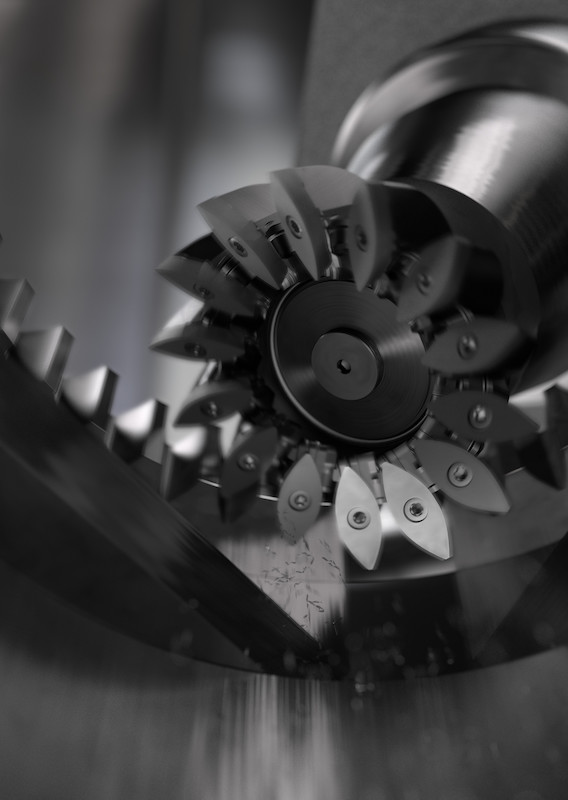
Massimizzare il rendimento con PrimeTurning
Per ottenere simili vantaggi, non è sufficiente utilizzare utensili come CoroMill 180. Occorre un approccio più ampio: ecco dove entra in gioco PrimeTurning.
La metodologia PrimeTurning prevede che l’utensile entri nel componente all’altezza del mandrino, asportando il materiale e muovendosi verso l’estremità del componente – ancora una volta, dando la priorità ai sempre fondamentali volumi di truciolo asportato. Questo consente di lavorare con angoli di registrazione inferiori, angoli di attacco superiori e parametri di taglio più elevati. Inoltre, le operazioni di lavorazione convenzionali possono essere eseguite con gli stessi utensili, quindi le officine meccaniche possono alternare processi tradizionali e innovativi.
Con PrimeTurning, alcune applicazioni potrebbero registrare un aumento della produttività del 50%, anche grazie all’aiuto del nostro software CoroPlus Tool Path, che fornisce codici e tecniche di programmazione per la definizione di parametri e variabili orientati a massimizzare il rendimento.
di Harish Maniyoor, global product manager for automotive Sandvik Coromant