Vediamo tre esempi in cui il gas può ridurre il pericolo di formazione di difetti.
Le saldature possono rappresentare le criticità maggiori nella realizzazione di manufatti d’acciaio e leghe. Non è infatti preventivamente calcolabile con esattezza il livello di tensioni che un giunto saldato sarà in grado di supportare, ciò può infatti avvenire solo in seguito, mediante prove empiriche. I valori di resistenza e tenacità del giunto saldato possono essere influenzati negativamente dai cosiddetti “difetti di saldatura”, nonché inneschi di rottura e intensificatori di sforzi che sia nel breve che lungo periodo causano la frattura della saldatura. Al fine di prevenire – per lo meno in linea teorica – difetti di saldatura, vengono stillate le WPS (Welding Procedure Specification), che fissano le variabili di saldatura in range ristretti che l’operatore deve rispettare al fine di rendere la saldatura il più possibile simile a quella campione e quindi risultare allineata ai calcoli progettuali. Il gas o le miscele gas di protezione sono una variabile fondamentale descritta nelle WPS ed essi non possono essere variati (nel caso delle miscele, variazioni delle percentuali di componenti sono ammesse all’interno dei range stabiliti dalla normativa UNI ISO 14175). La scelta del gas o miscela di protezione deve perciò essere fatta a monte della convalida delle WPS. La decisione dovrebbe essere oculata, nella consapevolezza che la variazione di percentuali di gas o l’aggiunta di elementi come elio e idrogeno possono aumentare le performance del processo (maggiore velocità), migliorare le caratteristiche meccaniche del giunto e allontanare il pericolo di formazione di difetti di saldatura.
Cricche
Le cricche sono forse il difetto più problematico, perché, a seconda delle dimensioni e delle sollecitazioni a cui il giunto sarà sottoposto, possono essere la causa di una futura rottura, rappresentando una discontinuità all’interno del materiale metallico. A seconda della causa che le genera, vengono divise in cricche a caldo o a freddo.
Le cricche a caldo sono originate da una elevata presenza di impurezze contenute negli elementi che concorrono al processo di saldatura (materiale di base, d’apporto e gas). In riferimento al gas è perciò importante garantire un elevato grado di purezza (si utilizzano gas puri fino al 99,995% a seconda della delicatezza del processo).
Ma come possiamo sapere con certezza se il gas che stiamo utilizzando è sufficientemente puro? Esiste, come in tutti gli ambiti, una normativa di riferimento (nel nostro caso la già citata UNI ISO 14175), che per ogni tipo di miscela gas stabilisce delle impurezze massime ammissibili. È perciò fondamentale che il fornitore di gas possa certificare che i gas e le miscele che stiamo utilizzando rispettino questa normativa.
Le cricche a freddo, invece, sono causate dell’influenza di idrogeno nel bagno di saldatura.
Soprattutto ad alte temperature, l’elevata solubilità dell’idrogeno consente allo stesso elemento di diffondersi nel metallo. Quando questi atomi di idrogeno si ricombinano in minuscole cavità della struttura metallica per formare molecole biatomiche di idrogeno, generano una pressione dall’interno della cavità. Questa pressione può aumentare fino a conferire al metallo una ridotta duttilità e resistenza a trazione, fino al punto in cui si origina una cricca. Grazie al tempo necessario all’idrogeno per ricombinarsi nel dannoso idrogeno molecolare, la criccatura da idrogeno può insorgere anche 24 ore dopo la fine della saldatura.
Per evitare le cricche a freddo, è bene eseguire il preriscaldo dei componenti da saldare, evitare raffreddamenti troppo rapidi e nel caso di saldatura MIG/MAG o TIG, verificare l’assenza di umidità sui lembi. Gli acciai ad alta resistenza e quelli bassolegati, le leghe di nichel e di titanio sono i metalli più colpiti dal fenomeno. Gli acciai con basso carico di rottura e durezza non sono solitamente soggetti al fenomeno.
Gli acciai inossidabili austenitici, l’alluminio e le sue leghe, il rame e le sue leghe (ad esempio il berillio rame) sono immuni da infragilimento all’idrogeno insieme con pochi altri metalli, per questo motivo l’idrogeno può addirittura essere utilizzato (in percentuali solitamente fino al 7%) come gas di protezione, implementando le caratteristiche del giunto saldato grazie alle sue proprietà fisiche e chimiche come conducibilità termica e azione riducente.
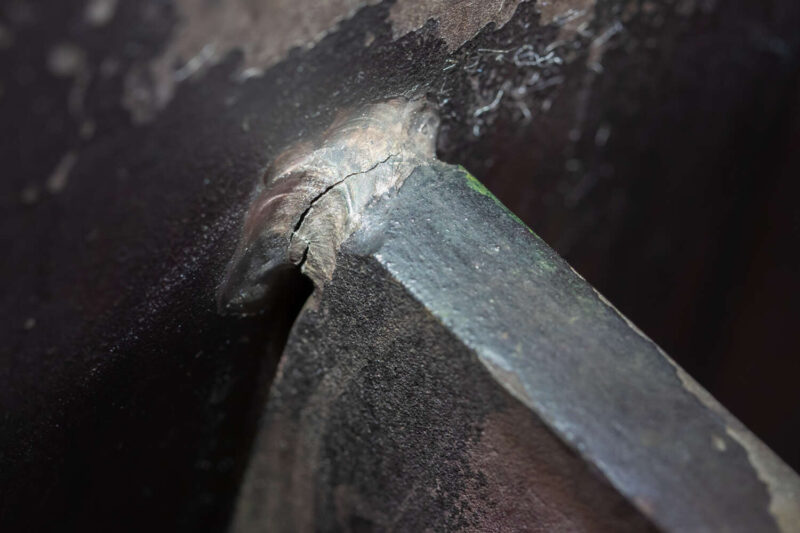
Mancanza di fusione e di penetrazione
Sappiamo per definizione che la differenza tra la brasatura e la saldatura è che in quest’ultima, anche il materiale di base viene fuso assieme al materiale d’apporto. Al venire meno di questa condizione si ha la mancanza di un requisito fondamentale del processo di saldatura (incollature), ma anche imperfezioni minori come penetrazioni incomplete danno origine a cordoni di saldatura non accettabili. Le incollature spesso si verificano quando tra il lembo e la zona fusa si interpone uno strato di ossido.
È un difetto tipico dell’acciaio saldato con tecnica MAG, saldatura ad arco con metallo sotto protezione di gas attivo, o con saldatura ossiacetilenica. È presente anche nelle saldature delle leghe di alluminio, facilmente ossidabili. Questo tipo di difetti si verifica più facilmente in presenza di geometrie complesse, oppure quando la passata è troppo veloce o ancora la corrente di saldatura troppo bassa. Oltre a queste discriminanti, anche il gas influenza il risultato. Per esempio, non è possibile – fatta eccezione per leghe di alluminio – saldare con processi a filo senza l’aggiunta di percentuali di gas attivo (CO2 o ossigeno), in quanto si incorrerebbe nella difettologia chiamata “cordone a testa di chiodo”. La sola energia dell’arco elettrico tende, infatti, a concentrarsi nella parte centrale del bagno di saldatura, non consentendo una penetrazione uniforme.
È perciò solo grazie all’aggiunta di questi gas attivi che riusciamo a garantire una penetrazione più omogenea e possiamo addirittura influenzare la penetrazione complessiva, incrementandone la percentuale.
Un ulteriore upgrade in questo ambito può essere costituito da miscele ternarie (con 3 gas diversi), contenenti percentuali crescenti di elio o idrogeno, al crescere dello spessore. Questi gas riescono ad incrementare la conducibilità termica all’interno dell’arco elettrico e dare una spinta ulteriore all’efficacia di penetrazione senza incrementare il contenuto di CO2 o ossigeno (eccessivi livelli di gas attivi causano un’eccessiva ossidazione del cordone di saldatura e potenziali difetti collegati).
Difetti di forma, dimensione e spruzzi
Esistono vari difetti di forma o di dimensione che possono condizionare in modi diversi la tenuta della saldatura oltre che non soddisfare i requisiti estetici richiesti in alcune lavorazioni. Per esempio, l’eccesso di sovrametallo, ovvero quando il cordone di saldatura è troppo alto, può essere causato principalmente da corrente troppo elevata o da una incorretta preparazione del giunto. Al contrario, il riempimento incompleto è causato da insufficiente apporto di materiale. Del riempimento incompleto fa parte il difetto specifico delle incisioni marginali, causate tecnicamente da corrente eccessiva o da un utilizzo inadeguato della torcia. Diverse miscele gas possono intervenire per attenuare questi fenomeni, nella fattispecie miscele argon-elio o argon-idrogeno possono aumentare la conducibilità termica nella zona in cui avviene il trasferimento dell’arco elettrico.
Ciò può favorire una miglior fusione e una deposizione del materiale più ampia e uniforme. Benefici in tal senso sono maggiormente riscontrabili in miscele ad alta performance contenenti elio in quanto a differenza dell’idrogeno, non essendo infiammabile, può essere utilizzato in percentuali maggiori.
In ultimo gli spruzzi, che in saldatura sono dei depositi di materiale fuso dispersi sulla superficie del metallo base lungo il cordone. Questi possono inoltre diventare un facile innesco per fenomeni corrosivi oltre che fare apparire l’esecuzione del manufatto non “a regola d’arte”.
Essi vengono causati principalmente da eccessiva corrente, mancanza di pulizia del materiale di base ed eccessivo utilizzo di gas attivo. Esistono tuttavia miscele ternarie contenenti gas attivo dove l’influenza primaria ottenibile dai vari gas come penetrazione (CO2) e fluidità del bagno (ossigeno) vengono combinate in maniera ottimale al fine di poter garantire penetrazioni efficaci e riduzione degli spruzzi. L’utilizzo di miscele argon-ossigeno-CO2, danno ottimi risultati su saldature MAG di acciai al carbonio, in quanto – non contenendo elementi più costosi come idrogeno ma soprattutto elio – risultano essere perlopiù economiche e compatibili con il tipo di lavorazione.
di Nicola Sala