Ogni superficie non coincide mai con quella teorica ideale e la differenza definisce la qualità del prodotto. Qualità che può essere solo un fatto estetico, ma che, molto spesso, è funzionale.
È noto: le condizioni teoriche sono anche definite ideali perché, che lo si voglia o meno, si discostano dalla realtà. Questo scostamento può essere “corretto” dalle lavorazioni di finitura e superfinitura, potrà essere ridotto a valori accettabili, ma non potrà mai essere annullato. In linea generale, la lavorazione per asportazione di truciolo richiede sempre una finitura che, andando a modificare la superficie, consenta di soddisfare le specifiche.
In meglio o… in peggio?
Il termine “finitura” sembra avere una accezione positiva: si pensa sempre a un intervento migliorativo della qualità superficiale, ma, in realtà, questo non sempre è vero. O, meglio, si tratta di un intervento migliorativo, ma non nel senso classico del termine: la preparazione di una superficie che deve subire, per esempio, successivi rivestimenti, può richiedere se sia resa opportunamente scabra, e quindi si va contro l’accezione classica del termine. Analogamente, nel settore biomedicale, ad alcune protesi sono richieste superfici scabre in modo da garantire una migliore osteointegrazione, così da ridurre il rischio di rigetti.
In definitiva, si può dire che la finitura è quella lavorazione che permette di raggiungere la qualità superficiale desiderata, questo sia che si tratti di un intervento che migliora la qualità superficiale sia che, in senso lato, la peggiori, chiaramente in maniera controllata.
Funzionale o estetica? Uno sguardo alle tecnologie
Gli obbiettivi delle lavorazioni di finitura possono essere sia di tipo funzionale che estetico, come pure misti, dove alla funzione deve essere associato l’aspetto estetico. Per fare chiarezza, l’intervento è funzionale se ha come obiettivo il raggiungimento di determinate performance/proprietà mentre è estetico se risponde a esigenze esteriori, in termini di bellezza, armoniosità…
Nell’era della mass customization e della produzione one of kind, dove la personalizzazione dei manufatti è spinta al massimo, la finitura gioca un ruolo primario in quando permette di differenziare in maniera sostanziale lo stesso manufatto, sia nel caso di fini estetici che funzionali.
Indipendentemente dall’obbiettivo, la finitura desiderata può essere raggiunta mediante processi produttivi diversi, con applicazioni che si basano su concetti tecnologici differenti: dai processi meccanici a quelli chimico-fisici, di cui fanno parte i processi chimici, quelli termici e quelli fisici.
Oltre al requisito estetico, garantire il grado di finitura definito dalle specifiche di progetto, significa assicurare un aumento della resistenza all’usura, sia abrasiva che erosiva, all’indentazione, alla corrosione, ma anche regolazione dell’attrito, riduzione (o aumento) della rugosità.
Oggi la tecnologia additiva si sta sempre più confermando come processo industriale: anche i manufatti prodotti in additive possono richiedere di essere finiti, in generale per rendere meno scabra la superficie.
Se la finitura è all’utensile…
Nella classica lavorazione per asportazione, l’utensile di finitura è detto finitore: adeguati e opportuni parametri tecnologici permettono di ottenere una finitura superficiale che risponda alle specifiche progettuali.
Oggi è sempre più diffusa la cultura delle lavorazioni in alta pressione, che permettono un elevato grado di finitura superficiale, fermo restando la necessità di macchina utensile e utensili che siano in grado di supportarla. Inoltre, lavorare con alta pressione presuppone mantenere il lubrorefrigerante sempre “pulito“, privo di particelle solide dure che, veicolate attraverso il fluido da taglio in pressione, potrebbero avere un’azione abrasiva devastante.
Secondo recenti studi, è possibile raggiungere gradi di finitura paragonabili a quelli ottenuti di rettifica, lavorando in alta pressione con fluido contente particelle di dimensioni inferiori a 5÷10µm.
La finitura superficiale può anche essere una rugosità controllata, o “irruvidimento“, che favorisce l’adesione di un rivestimento successivo. Tradizionalmente si ricorre alla sabbiatura, o a tecnologie simili, ma è possibile ottenere risultati simili anche con appositi utensili, con il grosso vantaggio di ridurre i tempi di attraversamento dato che il pezzo non deve essere spostato dal centro di lavoro, con un conseguente ritorno in termini di performance di processo ed economicità.
Affine, ma più complesso, è il caso delle protesi che, per una buona osteointegrazione, richiedono superfici irruvidite, che favoriscono l’accrescimento dei tessuti. La complessità sta nel dover necessariamente conciliare opposte esigenze: la porosità (o rugosità controllata) del materiale ne inficia le proprietà ma, al tempo stesso, massimizza la fissazione.
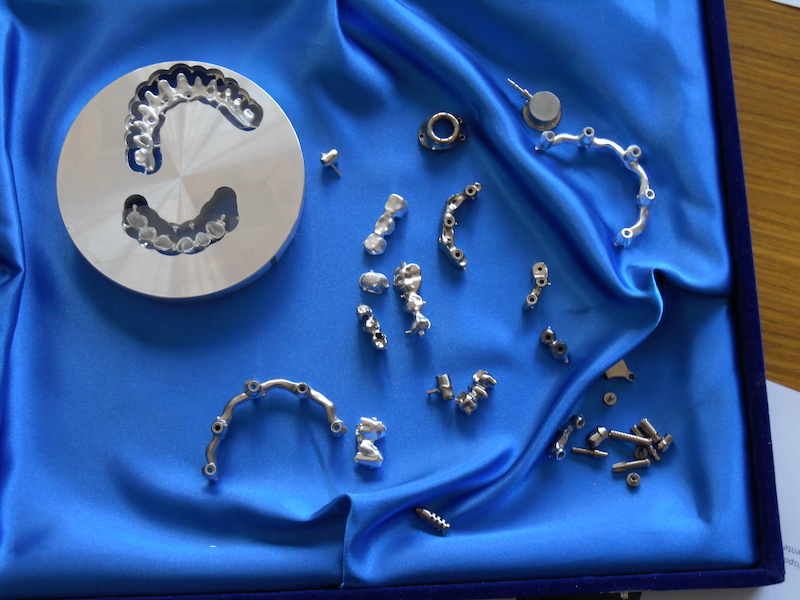
… o con abrasivi
L’uso di abrasivi per migliorare la qualità superficiale è fra le più antiche conosciute. Oggi, si ricorre alla finitura con abrasivi quando non è possibile raggiungere la qualità desiderata, a causa della forma o del materiale del manufatto, mediante la tradizionale asportazione di truciolo con utensili finitori o superfinitori.
L’utensile non ha geometria definita, ma è un abrasivo, cioè un insieme di particelle piccole e molto dure, di forma irregolare e con spigoli affilati, che rimuovono piccole quantità di materiale, formando trucioli di dimensioni molto ridotte, anche sotto forma di polvere, a seconda del materiale lavorato. Gli abrasivi sono utilizzati per la finitura di pezzi molto duri o che hanno subito trattamento termico, ed è in genere l’ultima operazione.
Negli ultimi anni, la finitura con abrasivi e, in particolare, la rettifica, sono state poste sotto osservazione in quanto ritenute potenzialmente rischiose sia per la salute degli addetti che per l’ambiente, proprio a causa del concetto stesso su cui si fonda la tecnologia. Infatti, le particelle taglienti sono dure e friabili, per garantire all’abrasivo l’attitudine a fratturarsi in piccoli pezzi, a garanzia della capacità dell’auto affilamento. Il problema è legato alla dispersione nell’ambiente proprio di queste polveri, dure e taglienti: oltre a inquinare l’ambiente, se inalate possono creare lesioni di varia entità agli organi interni, così come, in caso di contatto diretto con il corpo umano, possono creare abrasioni e lesioni.
Oggi si stanno mettendo a punto impianti di rettifica che riducano drasticamente il rischio per l’uomo e l’ambiente, dato che le mole, in alcuni casi, possono essere l’unica tecnologia possibile. Contemporaneamente si stanno diffondendo tecniche alternative, dalla tornitura dura alle lavorazioni convenzionali in alta pressione, che possono rappresentare una valida alternativa alla finitura per asportazione con abrasivi, riuscendo a garantire buona accuratezza dimensionale, interessante grado di finitura e integrità superficiale.
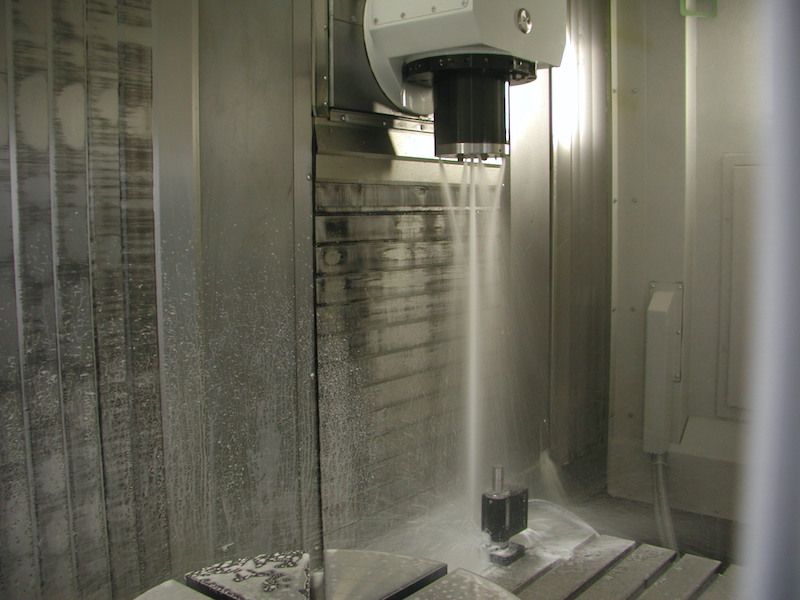
Fra creste e valli
Superfici teoriche, come quelle generate dai modellatori CAD tridimensionali, non coincideranno mai con le superfici reali, indipendentemente dalla tecnologia o lavorazione utilizzata, per quanto ben eseguita. Ogni lavorazione lascia un testimone sulla superficie: un susseguirsi di creste e valli distribuite in modo non regolare a seconda della lavorazione eseguita.
Creste e valli possono essere viste come “alterazioni” della superficie reale rispetto a quella ideale (o teorica) e, per quanto non siano né visibili a occhio nudo né percepibili al tatto, sono sempre presenti. Il susseguirsi di creste e valli rappresenta la scabrosità della superficie e determina la qualità del manufatto, con una ricaduta sulle sue proprietà e sulla funzionalità.
La scabrosità determina il grado di rugosità, che è sempre un dato di progetto considerato che influisce su molti fattori, quali, per esempio, l’attrito, la resistenza alla corrosione, e alle aggressioni chimiche in generale, e la resistenza a fatica.
Tra i principali fattori che influenzano lo scostamento fra superficie ideale e reale (scostamento sempre presente!) si hanno:
• vibrazioni
• truciolabilità (intasamento, macinazione)
• usura dell’utensile
• grado di pulizia del fluido da taglio
Due parole sugli abrasivi
L’uso di abrasivi nelle lavorazioni meccaniche tradizionali è storico, e ha portato, in tempi relativamente recenti, a suddividerli in due macrocategorie: gli abrasivi convenzionali (allumina e carburo di silicio) e i superabrasivi (nitruro di boro cubico e diamante).
Gli abrasivi hanno grani sono di dimensioni molto piccole, legati in forma di mola, grazie a un legante che garantisce il collegamento fra i grani stessi: in questo modo, alla mola viene assicurata la capacità di asportare adeguate quantità di materiale, nel rispetto dell’economia di processo.
La caratteristica di alta friabilità è sinonimo di bassa resistenza alla frattura, quindi il grano abrasivo altamente friabile si frammenta facilmente sotto l’azione delle forze di taglio, garantendo una maggiore durata alla mola, in virtù della maggior capacità di auto affilarsi.
La friabilità è una caratteristica del materiale, ma dipende anche dalla forma e dalla dimensione del grano abrasivo: grani compatti hanno un comportamento simile a quello dell’utensile con spoglia negativa e sono meno friabili dei grani allungati. Il grano di piccole dimensioni ha anche minor probabilità di presentare difettosità, quindi sono più tenaci e meno friabili, rispetto a quelli di dimensioni maggiori.
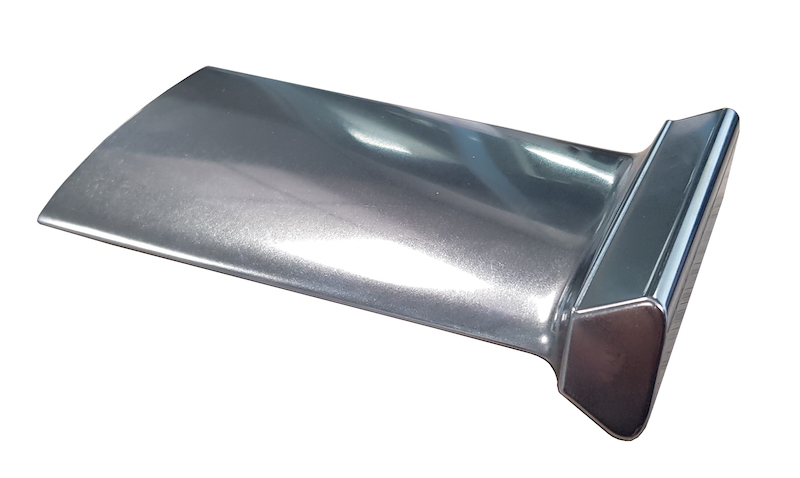
ISF, ovvero la superfinitura isotropica
Isotropic Superfinish Process (ISF), nota anche come superfinitura isotropica, è stata messo a punto intorno agli ’80 per particolari applicazioni nel settore aeronautico, ma oggi il suo campo di utilizzo si è notevolmente ampliato, tanto da essere vantaggiosamente utilizzata in tutti i casi in cui è strategico migliorare prestazioni, durata e affidabilità.
Da alcuni ritenuta un compromesso fra processo e trattamento, tanto da essere considerata di natura mista, meccanico-chimica, non abrasiva, consiste in una lucidatura in grado di raggiungere rugosità molto basse, molto inferiore a quello ottenibile di rettifica, nell’ordine di Ra 0,01 µm o inferiori, con superfici dall’aspetto molto lucido.
È definita “isotropica“, cioè che possiede caratteristiche uguali in tutte le direzioni in cui si effettua la valutazione, il che si traduce in assenza di segni di lavorazione meccanica (superficie non orientata).
L’ISF è un trattamento progressivo, ottenuto tramite vibrofinitura, che mantiene inalterata la geometria dei manufatti, senza modificare la dimensionalità; la bassa temperatura a cui avviene la lavorazione, rende praticamente nulle distorsioni o mutazioni dovute al gradiente termico, così come non ci sono stress o tensioni superficiali, dovuti a lavorazioni precedenti, ma si ha una omogeneizzazione delle caratteristiche superficiali.
La superfinitura isotropica può essere eseguita sul pezzo singolo o su più pezzi contemporaneamente, coprendo un ampio range di dimensioni, dalle piccolissime fino a 5000 mm. Possono essere superfiniti anche manufatti che sono stati torniti, anche con lavorazioni di tornitura dura, rettificati… anche nel caso siano stati trattati con rivestimento antiusura.
di Daniela Tommasi