Ridurre la rugosità, ridurre l’attrito, migliorare le performance… la finitura di un manufatto porta in sé molti vantaggi. E se la finitura diventasse superfinitura?
La qualità finale di un manufatto rientra fra le specifiche di progetto che vanno assolutamente rispettate, pena lo scarto o l’eventuale ripresa, se possibile. Il ruolo della finitura superficiale è quindi fondamentale, sia che l’obbiettivo sia funzionale che estetico o, come spesso accade, un mix fra i due: la finitura è quindi quel processo che permette di raggiungere la qualità superficiale desiderata.
In linea generale, il termine finitura ha una accezione positiva ed è visto come un intervento migliorativo della qualità superficiale, anche se, in realtà, questo non sempre è vero. O, meglio, si tratta di un intervento migliorativo, ma non nel senso classico del termine: la preparazione di una superficie che deve subire, per esempio, successive verniciature, può richiedere che sia resa opportunamente scabra, e quindi si va contro l’accezione classica del termine.
Focalizzando l’attenzione sull’innalzamento della qualità superficiale, gli standard qualitativi, e, di conseguenza, il grado di finitura richiesto, è andato modificandosi, grazie allo sviluppo della tecnologia meccanica e dei processi tecnologici: è nata la superfinitura. Secondo la letteratura, la superfinitura è una finitura superficiale spinta, che sposta i limiti della rugosità superficiali, che può arrivare a circa 0,01 µm.
In uno scenario che coinvolge praticamente tutti i settori merceologici, caratterizzato dalla richiesta di gradi di finitura sempre più spinti, c’è una tecnologia che sta riscuotendo sempre più interesse: la “Superfinitura Isotropica“.
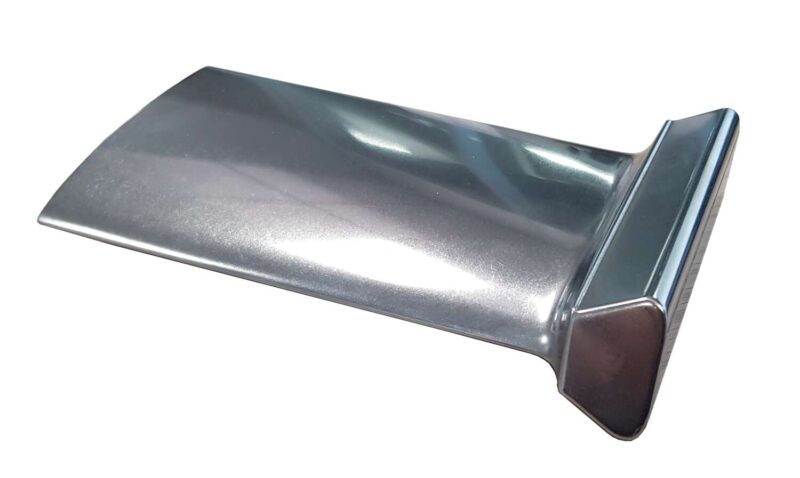
La superfinitura diventa isotropica
Non è un processo di recente invenzione dato che è stato messo a punto e brevettato negli anni ‘80 da REM Chemicals: è l’Isotropic Superfinish Process, noto anche con l’acronimo ISF. L’ISF, conosciuto in Italia come “Superfinitura Isotropica“, non è quindi un processo giovanissimo, ma si tratta di una tecnologia nata dalla necessità, in particolare quella di migliorare le prestazioni ed i rendimenti delle trasmissioni di potenza. I risultati si sono rilevati subito eccellenti e duraturi, motivo per il quale la tecnologia è successivamente stata estesa ad altre applicazioni, anche in ambiti diversi, pur tenendo presente che l’importante beneficio che possono trarne tutti i movimenti di strisciamento e rotolamento del metallo.
Il risultato di un processo ISF è una finitura superficiale che viene comunemente definita “isotropica”, cioè che possiede caratteristiche uguali in tutte le direzioni in cui si effettua la valutazione, il che si traduce in assenza di segni di lavorazione meccanica (superficie non orientata). L’ISF è un trattamento progressivo, ottenuto tramite vibrofinitura, che mantiene inalterata la geometria dei manufatti, senza modificare la dimensionalità; la bassa temperatura a cui avviene la lavorazione, rende praticamente nulle distorsioni o mutazioni dovute al gradiente termico, così come non ci sono stress o tensioni superficiali, dovuti a lavorazioni precedenti, ma si ha una omogeneizzazione delle caratteristiche superficiali. L’assenza di picchi e valli riduce drasticamente anche l’innescarsi del pitting e, più in generale, di tutti i fenomeni di usura.
La “Superfinitura Isotropica” può essere eseguita sul pezzo singolo o su più pezzi contemporaneamente, coprendo un ampio range di dimensioni, dalle piccolissime fino a 5000 mm.
Come funziona
L’ISF è un processo ottenuto tramite vibrofinitura, in massa, assolutamente non aggressiva e con livelli di asportazione controllata, capace di garantire rugosità molto basse, anche ad Ra inferiori a 0,01. Il trattamento dei pezzi è progressivo e pertanto permette di raggiungere i valori desiderati di rugosità, sino ai nanometri per le applicazioni più impegnative, mantenendo inalterata la geometria dei manufatti.
Il processo di “Superfinitura Isotropica“, che si configura come una qualsiasi lavorazione, avviene mediante l’utilizzo di macchine a vibrazione: le vasche vibranti vengono caricate con inserti di lavoro, detti anche media, che sono caratterizzati da un’ampia varietà di composizioni, forme e dimensioni, cui vengono aggiunti prodotti chimicamente acceleranti, per migliorarne le performance di finitura. Durante il processo, i prodotti chimicamente acceleranti vengono inseriti in vasca in maniera graduale e costante, tramite pompe dosatrici; gli inserti più utilizzati sono costituiti da una miscela metallo-ceramica, caratterizzata da un peso specifico apparente superiore a 1,5kg/L, che permette di raggiungere, in tempi ridotti, livelli di rugosità molto bassi.
Tutte le condizioni operative sono scelte in funzione del manufatto da lavorare, alle condizioni di rugosità iniziale e alle specifiche esigenze; come ogni processo di finitura superficiale, anche l’ISF è la lavorazione finale, sia che si tratti di manufatti prodotti con tecnologie tradizionali sottrattive, sia nel caso di produzione additiva. Il processo di “Superfinitura Isotropica” realizzato con prodotti chimicamente accelerati si basa sulla formazione di un sottile strato di conversione sulla superficie metallica da trattare. Questo strato, che è più tenero del metallo base, viene facilmente asportato in corrispondenza delle creste di rugosità superficiali che risultano più esposte al contatto con gli inserti ad alta densità. Ciò permette un’ulteriore reazione di conversione, con successiva asportazione di materiale, ed è la ripetizione di questo meccanismo, che porta ad ottenere un abbassamento progressivo arrivando all’eliminazione dei picchi di rugosità.
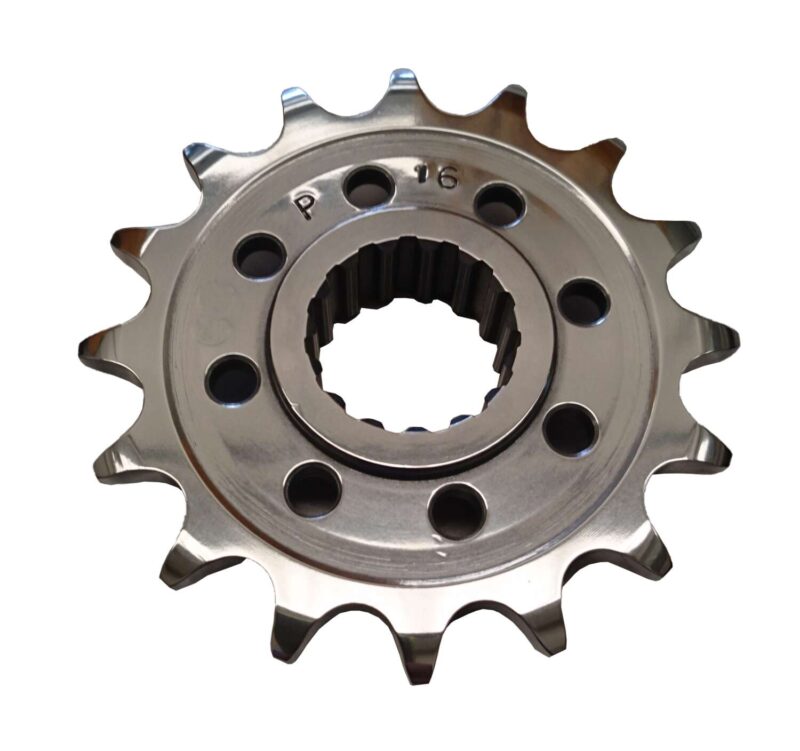
Additive manufacturing e le risposte di test sfruttando l’ISF
La diffusione dell’additive manufacturing ha portato alla generazione di forme complesse, con la presenza di canali e cavità interni sia rettilinei che curvi: è nato quindi il problema della finitura superficiale sia delle superficie esterne che di quelle interne. Per quanto riguarda le parti esterne, vengono richieste, oltre alla rimozione del polverino di rifusione, possono essere richiesti valori di Ra<1, mentre per le parti interne, pur rimanendo vitale la rimozione del polverino, le rugosità solitamente richieste sono inferiori a 4 m.
«Nel nostro laboratorio abbiamo effettuato numerose prove, anche in collaborazione con le università – spiega Marco Bonazzoli di Best Finishing –, che ci hanno portato a concludere che: nel caso di canali interni, con un collegamento ad una pompa, usando prodotti di finitura normali, additivati con abrasivi diversi per composizione e granulometria in funzione del metallo, si possono trattare canali sia lineari che curvi che con dimensioni sino 0,53 mm. Vengono così evitate le macchine a pressione con paste o acidi forti, riuscendo comunque ad eliminare il polverino di rifusione ed allargando i fori fino alla misura richiesta. Questo procedimento, utilizzato su vani turbina e canali di raffreddamento, ha consentito di ridurre la rugosità interna a valori inferiori ad Ra 4 su materiali utilizzati dall’AM, come AlSi10Mg, 316l, Inconel, leghe di titanio, superleghe, leghe di rame; manufatti con solo superfici esterne, anche se questo può valere anche in presenza di canali interni, possono essere trattate successivamente sia in massa, sia in bacini di contenimento, che montate su telai, in funzione del numero di pezzi da trattare, senza limiti di dimensioni, ovviamente se non quelli della macchina utilizzata. Le rugosità che si possono ottenere sono inferiori ad Ra 1. Naturalmente si possono effettuare mascherature in modo da evitare di trattare parti su cui non è richiesto di intervenire».
Tutti questi procedimenti vengono accelerati, come in tutte le reazioni, dalla temperatura, il controllo della quale permette di garantire la costanza e la ripetibilità della lavorazione. Dopo la fase di levigatura viene effettuato un lavaggio, con un normale detergente, in modo da eliminare eventuali residui della lavorazione, cui può far seguito un lavaggio in ultrasuoni, particolarmente utile nel caso siano stati trattati canali interni. Il processo termina con una asciugatura, per evitare gli aloni lasciati dal calcare presente nell’acqua.
Non solo test in laboratorio
Quanto studiato e testato in laboratorio ha portato a sviluppare una lavorazione utilizzata con successo in diversi settori dove vengono richieste finiture non raggiungibili con sistemi tradizionali, oppure laddove nasce un problema di costi, come nel caso di trattamenti che utilizzano sostanze con problemi di smaltimento-depurazione, o dei trattamenti a pressione, con un telaio per ogni singola sagoma, o la difficoltà nel lavare internamente i pezzi per la rimozione delle paste utilizzate: queste, ma molte possono essere le situazioni, spingono a cercare procedimenti alternativi, come la “Superfinitura Isotropica“.
«Tutto ciò che Best Finishing ha messo a punto negli anni, viene oggi utilizzato da primarie realtà, che possono contare su cicli ripetibili e “congelati”, che non richiedono manodopera specializzata, o attrezzature pericolose per gli addetti o per l’ambiente – prosegue Bonazzoli –. Mettiamo a disposizione la nostra esperienza offrendo campionature, anche gratuite, ad ogni azienda che voglia toccare con mano come la “Superfinitura Isotropica” possa fare la differenza. Sotto ogni aspetto».
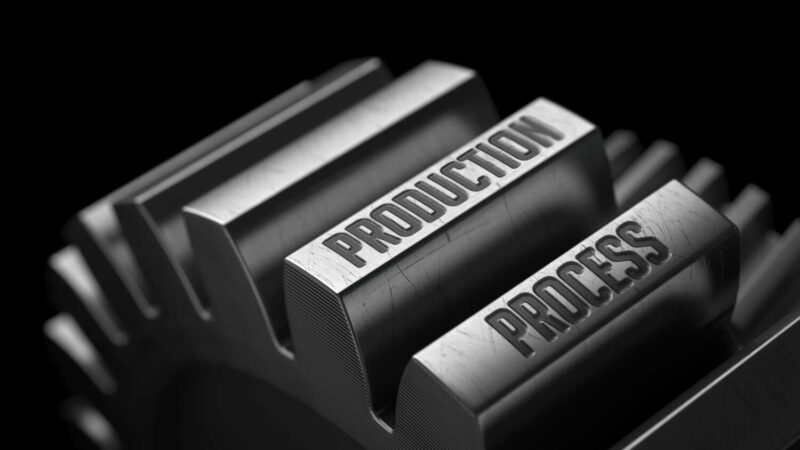
I plus dell’ISF
La “Superfinitura Isotropica” permette di ottenere diversi vantaggi, tutti riconducibili alla bassa rugosità che può essere raggiunta. Tutto ciò è di sicuro interesse da un punto di vista estetico, ma diventa fondamentale quando il ruolo della superfinitura è funzionale, come nel caso di organi in movimento, in quanto si ha:
• riduzione di attriti, della potenza assorbita, della rumorosità, della temperatura di esercizio, con assenza sia di micropitting che di pitting su ingranaggi o organi in contatto e/o sfregamento;
• incremento della vita utile del pezzo trattato, miglioramento della lubrificazione, incremento della microdurezza superficiale;
• abbattimento dei costi di manutenzione;
• miglioramento della resistenza a fatica, con assenza del degrado metallurgico, del degrado geometrica e rispetto delle forme e degli spigoli.
E’ quindi evidente come, in presenza di movimenti sia di strisciamento che di rotolamento metallo su metallo, la “Superfinitura Isotropica” permetta di trarre notevoli benefici, diventando, in alcuni casi, addirittura strategica.
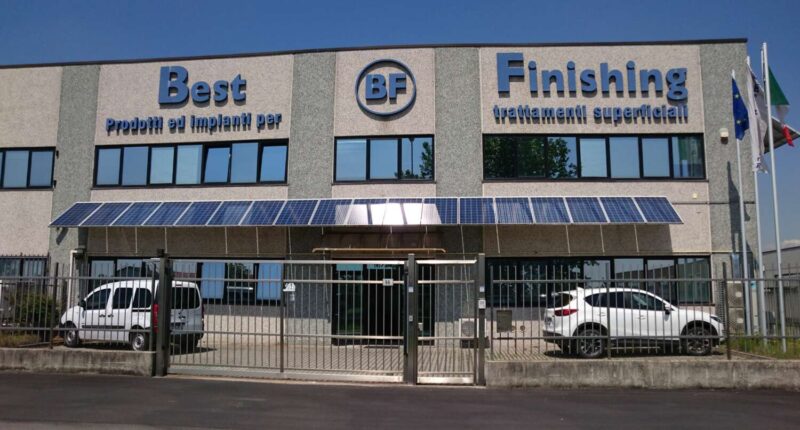
La “Superfinitura Isotropica” con Best Finishing
Oltre 30 anni di esperienza rendono Best Finishing Srl, con sede a Gessate, alle porte di Milano, un punto di riferimento autorevole per quanto riguarda i trattamenti superficiali tramite vibro-finitura fornendo consulenza tecnica, soluzioni e processi, impianti e macchine, prodotti e inserti. Proprio l’interesse sui processi di finitura, che garantissero la piena rispondenza alle specifiche di progetto, ha portato Best Finishing a sviluppare, nel tempo, le applicazioni per il processo di finitura ISF tramite i prodotti di REM Chemicals, di cui è l’agente per l’Italia e distributore.
Best Finishing dispone sia di un laboratorio prove adeguatamente attrezzato che di una sala metrologica, dotata di strumentazione ai massimi livelli, in modo da poter eseguire campionature di trattamento, anche valutative a titolo gratuito, con la misurazione di tutti i parametri qualificanti in modo da valutare il procedere della lavorazione ed il risultato finale.