Da sempre usata in ambito artigianale, la tornitura in lastra è ora riscoperta dall’industria per piccoli lotti, la prototipazione e i pezzi speciali.
La tornitura in lastra è un processo di lavorazione della lamiera tramite deformazione plastica, ovvero senza asportazione di materiale. Si ottiene facendo ruotare un disco di metallo al tornio, opportunamente bloccato da una contropunta folle. Un utensile preme e accompagna la lamiera spingendola contro uno stampo o mandrino sagomato, costringendola ad assumerne la forma. Chiaramente, il processo è adatto a realizzare pezzi con simmetria assiale, dai profili più semplici fino a quelli più complessi. È in realtà possibile produrre parti a sezione ellittica o asimmetrica, ma servono grande esperienza, capacità, tempo, e una buona dose di pazienza. Frequentemente, alla pura deformazione viene in pratica affiancata l’asportazione di truciolo, allo scopo di rifilare bordi irregolari o per tagliare il pezzo formato in prossimità del tampone premilamiera. Negli ultimi anni questa lavorazione viene effettuata anche tramite laser 3D.
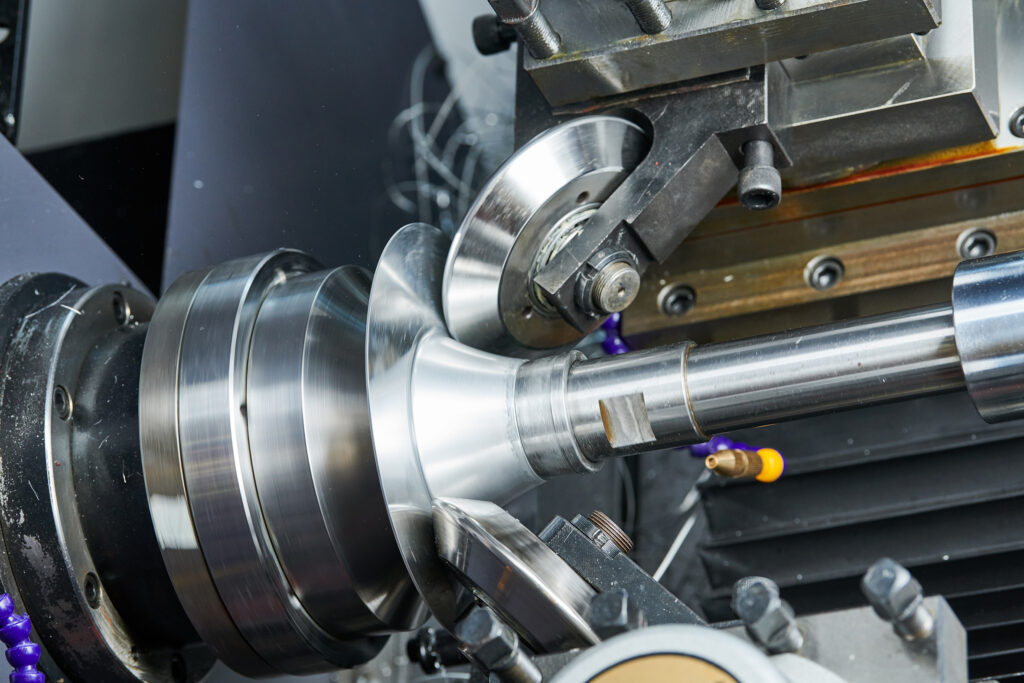
Esistono due tipi di tornitura in lastra: l’imbutitura al tornio e la fluotornitura. Nella prima, il pezzo finito ha all’incirca lo stesso spessore del disco di metallo di partenza, ma la forma finale è molto allungata: il diametro della lastra iniziale può essere anche molto maggiore di quello del prodotto finale. Nella fluotornitura, il diametro del disco di partenza è simile a quello finale del pezzo. La lavorazione redistribuisce il materiale in misura importante, plasmandolo e assottigliandolo per allungarlo fino a ricoprire il mandrino. Nell’uso comune, entrambi i processi vengono identificati con il termine generico di “tornitura in lastra”.
La tornitura in lastra è adatta a piccole e medie serie, dove i costi dei macchinari e degli stampi per imbutitura avrebbero un’incidenza troppo elevata. Anche le tolleranze richieste sono spesso più generose: per queste ragioni le macchine asservite o a controllo numerico non sono diffuse quanto in altri ambiti. Al contrario, la dimensione artigianale – in molti casi artistica – di questa lavorazione la rende ancora territorio delle macchine puramente manuali. Con le macchine a controllo numerico la precisione raggiungibile è nell’intorno del decimo di millimetro. Con gli utensili corretti, un operatore esperto riesce ad ottenere una finitura lucida, quasi a specchio, anche a mano.
Il mandrino è soggetto a sollecitazioni limitate e perciò viene spesso realizzato in legno o plastica, soprattutto per piccole serie. Per ottenere geometrie rientranti il mandrino può essere composto da parti smontabili, assemblate con viti e incastri. In casi particolari, vengono persino usati stampi di ghiaccio. Le forme più semplici non hanno bisogno di mandrino (la cosiddetta “tornitura in aria”) ma la precisione ottenibile è inferiore.
Gli attrezzi utilizzati si differenziano a seconda del tipo di lavorazione. Con i torni tradizionali si utilizzano utensili detti pali; quelli per la sagomatura hanno una punta conica, mentre quelli per la finitura hanno una punta più piatta. Alcuni pali possono essere dotati di un rullo in acciaio montato su cuscinetti a sfere. Rulli di diametro maggiore consentono di ottenere una migliore finitura, mentre quelli più piccoli sono usati per raggi più stretti. I pali sono lunghi circa un metro e sono dotati di un manico in legno, tenuto sotto il braccio. L’appoggio per l’utensile è dotato di perni, che fanno da fulcro all’asta. Man mano che la lavorazione procede, il palo viene spostato sul perno successivo per mantenere una posizione adeguata. L’operatore spinge il palo contro la lastra sfruttando il peso del corpo, usando le mani solamente per controllare la passata e per percepire la risposta del materiale.
La tornitura si ottiene lavorando insieme al materiale, sentendo la sua struttura, la sua grana, la sua durezza, la sua disposizione a muoversi nelle direzioni che si desidera. È fondamentale che l’operatore capisca la propensione del materiale a deformarsi in modo da poterlo sagomare sul mandrino in modo fluido, veloce e, soprattutto, uniforme. Passate lisce e costanti sono la chiave di volta e il segreto per ottenere pezzi di ottima qualità, un po’ come quando si modella un vaso di argilla. Per questo motivo, la tornitura in lastra è una vera e propria arte, relegata a una dimensione artigianale sotto i colpi dello stampaggio e dell’imbutitura.
Esistono anche torni per lamiera a controllo numerico, adatti per le serie di medie dimensioni. Gli utensili sono sempre del tipo a rullo e possono essere rivestiti di materiale ceramico per ottenere una maggiore durata. In caso di spessori elevati o con la fluotornitura, si usano due utensili sui due lati del pezzo per bilanciare le spinte sul mandrino.
La lamiera grezza dovrebbe essere un disco approssimativamente uguale in raggio alla lunghezza della parte desiderata più il raggio per l’80%, seguendo la formula empirica R = (L+R)×0,8.
Ad esempio, per un vaso alto 200 mm e di diametro 300 mm, il diametro del disco dovrà essere circa 560 mm. È fondamentale lubrificare il disco di lamiera per diminuire l’attrito (causa di surriscaldamento, vibrazioni e cattiva finitura), ma anche il mandrino per facilitare l’estrazione del pezzo. Il grasso comune non è adatto, poiché si consuma e schizza via con la rotazione: al suo posto si utilizzano speciali cere e saponi.
I materiali lavorabili
Quasi tutti i metalli disponibili in forma di lamiera possono essere imbutiti al tornio. Gli spessori da 10/10 a 25/10 possono essere torniti con utensili manuali. Le macchine automatizzate e a controllo numerico consentono di lavorare lamiere di spessore fino a 25-30 mm.
Spessori elevati possono richiedere la lavorazione a caldo, oppure passate multiple alternate a ricottura.
L’alluminio è molto elastico e facile da formare, in particolare se non legato. L’alluminio 1100-0 è il migliore, seguito dal 3003 che però non è molto adatto all’anodizzazione. È preferibile l’alluminio ricotto (1100-0, 3003-0 ecc.), mentre sono sconsigliati il 1100-H32 (dove la H sta per Hardened) e il 6061-T6 (dove T sta per trattato termicamente).
L’acciaio inossidabile è ancora più elastico dell’alluminio. Prima di lacerarsi può raggiungere il 50%-68% di allungamento, ma richiede molta più forza. La gamma austenitica (serie 200-300) di acciai inossidabili ha una buona formabilità, con le leghe 201 e 301 che mostrano il maggiore allungamento. Stesso discorso per gli acciai da costruzione, mantenendo basso il tenore di carbonio.
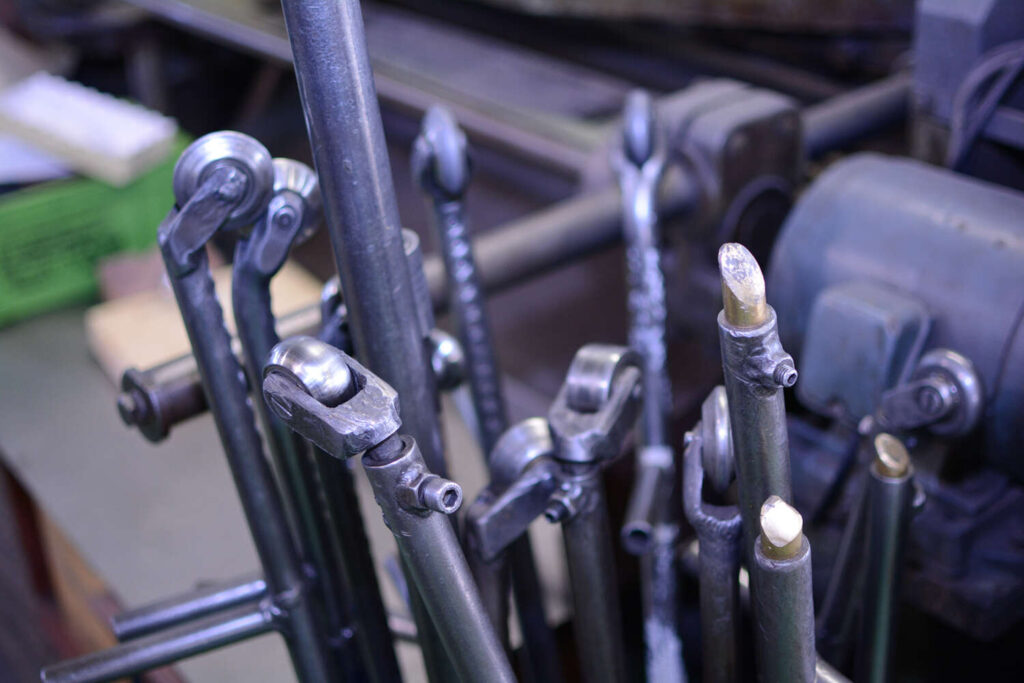
Il rame ha un eccellente allungamento (essendo molto malleabile) e raddoppia la sua resistenza alla trazione quando viene incrudito. Tuttavia, se si indurisce eccessivamente prima che il pezzo sia completato, bisogna procedere ad una ricottura di distensione per evitare la rottura.
L’ottone è una lega di rame e zinco e ha proprietà simili al rame nella sua formabilità, con la differenza che l’ottone si indurisce meno ma richiede più forza. Anche metalli speciali possono essere imbutiti al tornio, ma richiedono attenzioni particolari come, ad esempio, il riscaldamento e la tornitura a caldo.
Oltre alle leghe già citate, possono essere torniti anche:
- gli acciai inossidabili della serie 300 e 400 e quelli PH (Precipitation hardening) come i 17-4PH e 17-7PH;
- le superleghe ferro-nickel (A-286), le Hastelloy® (X, C, B, S) e gli Inconel® (600, 625, 718,X-750), l’N-155, il Nimonic® 263, e il Waspaloy®;
- le leghe a base di cobalto (Haynes® 188, Haynes® 230).
Dimensioni e impieghi
Le dimensioni lavorabili vanno da qualche mm fino a 3 m di diametro per i torni ad asse orizzontale. Sono stati costruiti torni ad asse verticale per realizzare pezzi con diametri fino a 6 metri.
I prodotti che possono essere realizzati in tornitura vanno dai piccoli articoli di ferramenta prodotti in grandi quantità (come tazze e componenti automobilistici) agli articoli per la casa fino ai grandi componenti per applicazioni aerospaziali a tiratura limitata. Alcuni esempi di componenti metallici che vengono torniti sono trofei, bollitori, caldaie, piatti per batteria, fondi di serbatoi, tubi senza saldature, paralumi, parti di centrifughe, recipienti in pressione, venturi, riflettori radar, antenne paraboliche, e cerchioni. In ambito aerospaziale, viene usata per gli ugelli dei motori a razzo e la carenatura delle ogive.
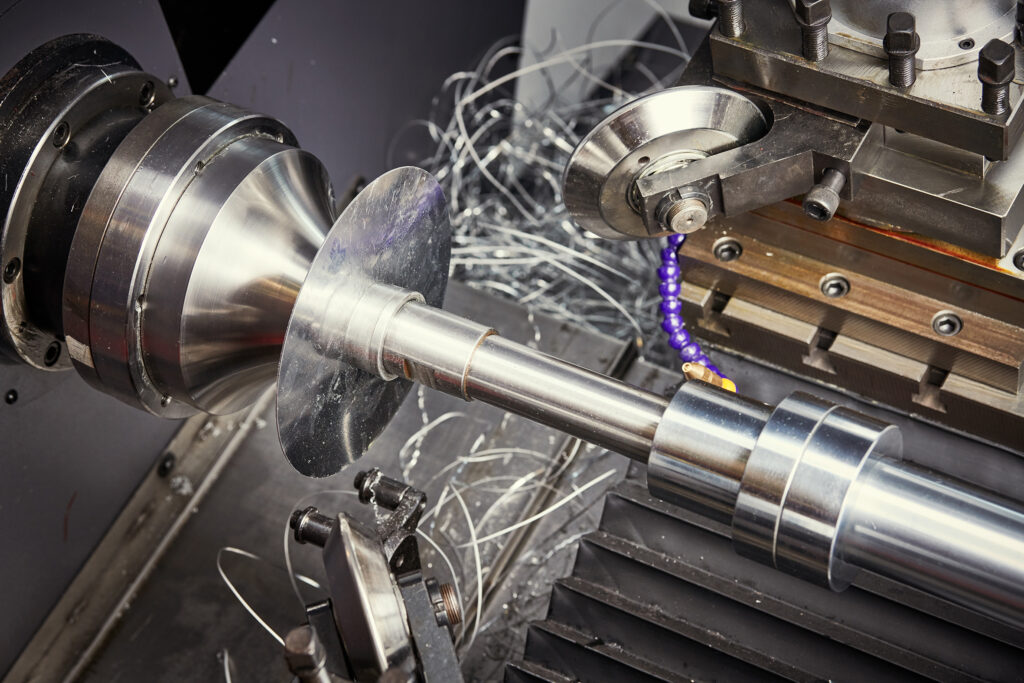
Sebbene la tornitura in lastra abbia tempi più lunghi rispetto allo stampaggio, la flessibilità e il basso costo la rendono il processo ideale per rispondere alle necessità crescenti di prototipazione e lotti a bassa numerosità tipici degli ultimi anni.
I vantaggi della tornitura in lastra
L’imbutitura al tornio offre numerosi vantaggi rispetto ad altri processi di formatura del metallo come la colata, la forgiatura o l’asportazione di truciolo.
L’efficienza dell’uso del materiale aumenta in quanto gli altri metodi come la forgiatura e la colata sono inizialmente prodotti con uno spessore maggiore, poi ridotto con lavorazioni meccaniche successive. La tornitura in lastra parte da una lamiera più sottile e il pezzo tornito solitamente non richiede nessuna lavorazione ulteriore.
I parametri di formatura e la geometria del pezzo possono essere modificati rapidamente, a costi inferiori rispetto ad altre tecniche di formatura del metallo. Anche i costi delle attrezzature e della produzione sono relativamente bassi.
La tornitura in lastra può iniziare come processo manuale ed essere successivamente automatizzata: in questo modo è possibile passare facilmente dalla fase di prototipazione alla produzione in serie. Lo spreco di materiale è ridotto al minimo e le operazioni secondarie sono spesso eseguite in tempo mascherato all’interno del ciclo della macchina, producendo risparmi significativi per il cliente.
Minori costi per gli utensili: i mandrini e i pali sono più versatili, più semplici e meno costosi degli stampi, e sono quindi più convenienti. Molte modifiche al progetto possono essere fatte con un piccolo costo aggiuntivo e senza la necessità di nuove attrezzature. Gli oggetti possono essere costruiti a partire da un solo pezzo, senza saldature. L’assenza di giunture permette di sopportare una maggiore pressione interna o esterna esercitata sulle pareti.
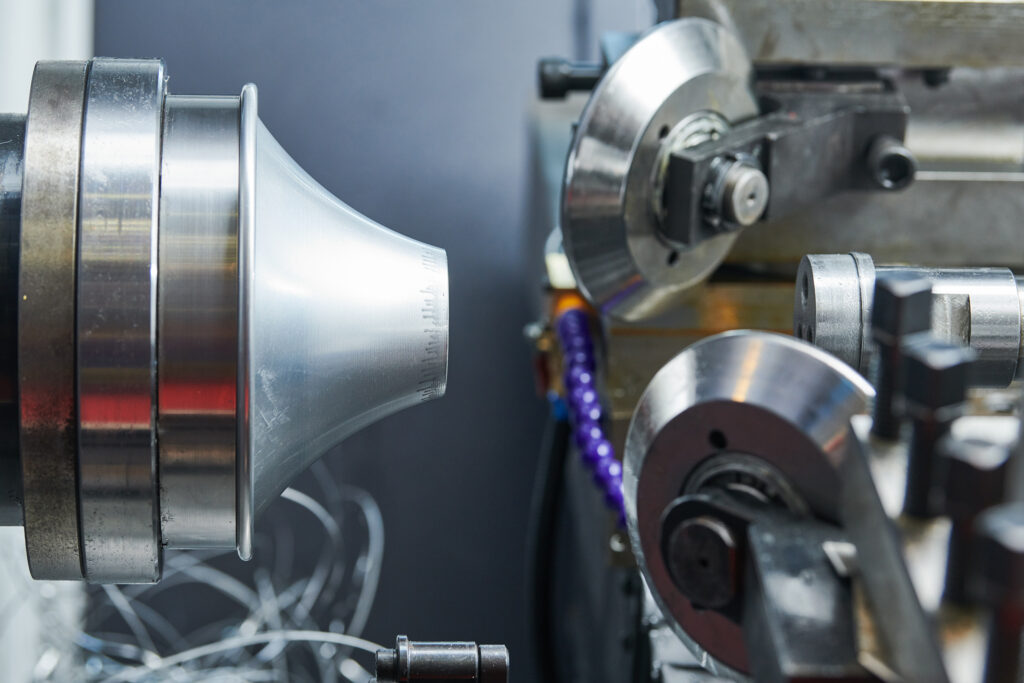
Migliore resistenza alla trazione: le deformazioni subite dal materiale durante la tornitura provocano un incrudimento. In questo modo la resistenza del componente aumenta e permette di ottenere un prodotto più leggero, affidabile e robusto. Tempi di sviluppo più brevi: l’uso di torni CNC, unito alla scelta di materiali certificati e standardizzati, permette alla tornitura in lastra di ridurre considerevolmente il time-to-market sia con i pezzi semplici che con quelli più complessi. Versatilità: la sagoma dei pezzi può essere rientrante ed è possibile realizzare bordi arricciati, tagliati, o sbavati senza rimuovere il pezzo dal mandrino.
Limiti dell’applicabilità
Rispetto allo stampaggio, all’imbutitura e all’idroformatura, la tornitura in lastra ha un tempo ciclo superiore. In compenso, i pezzi torniti hanno una migliore finitura superficiale grazie all’assenza di grinze, graffi e irregolarità e richiedono quindi meno lavorazioni successive.
La componente umana è importantissima: la sensibilità, l’esperienza, e la manualità dell’operatore possono fare la differenza tra un pezzo da scartare e uno perfetto. Con la progressiva riduzione delle competenze artigianali, e la difficoltà nel reperire sul mercato del lavoro manodopera altamente specializzata, la tornitura in lastra rischia di diventare un processo inaccessibile alle aziende.
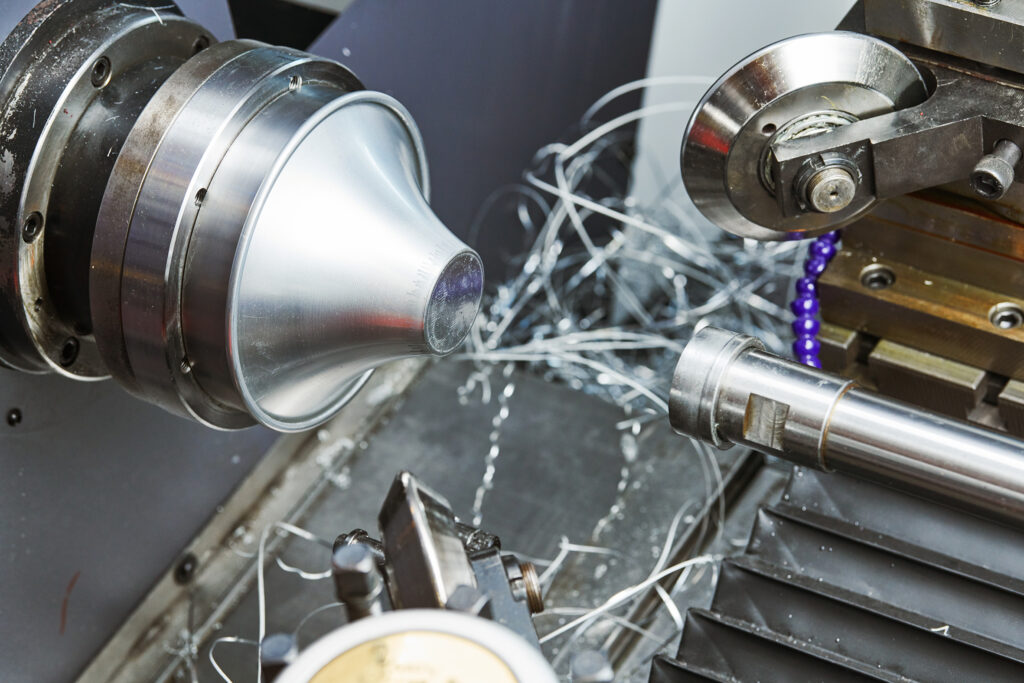
Le grandi deformazioni subite dal materiale, unite all’attrito tra pezzo e palo, possono provocare indurimento fino al punto da rendere impossibile proseguire la lavorazione. Se si arriva a questo punto, è indispensabile ricorrere a una ricottura di distensione.
Se il processo non viene effettuato correttamente, alcuni materiali possono lacerarsi. In questi casi, è quasi impossibile riparare il pezzo che dovrà quindi essere scartato.
di Marco Basso