Evoluzione tecnico-funzionale di componenti meccanici tradizionali grazie al “Design for Additive Manufacturing”. Il caso di una testa di fresatura.
Nel corso degli ultimi anni, la manifattura additiva (AM) sta progressivamente trovando ampi margini di applicazione rispetto alle tradizionali tecniche sottrattive nella realizzazione di componenti meccanici. I motivi risiedono in molteplici punti di forza di questo metodo produttivo: riduzione dei tempi fra progettazione e prototipazione, standardizzazione della catena di approvvigionamento, maggiore flessibilità e customizzazione del prodotto, possibilità di realizzare componenti complessi svincolati di limiti dei processi tradizionali. Infine l’introduzione di specifiche funzionali importanti quali riduzione delle masse mediante ottimizzazione topologica.
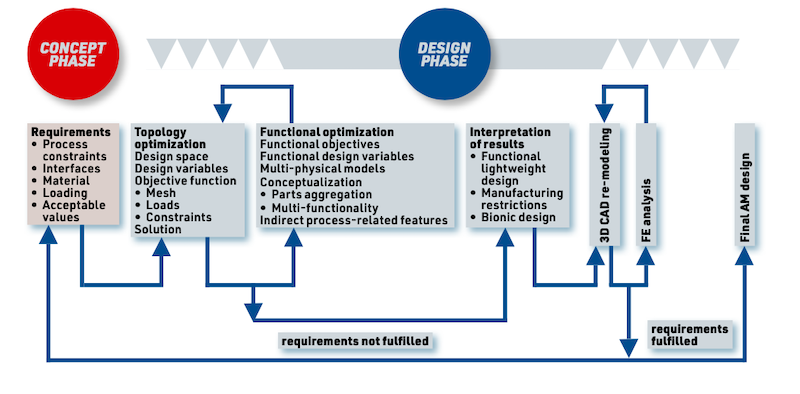
Il sistema composto da fresatrice, utensile e componente da lavorare è caratterizzato da interazioni reciproche che determinano direttamente molti parametri funzionali quali precisione, ampiezza o frequenza delle vibrazioni, frequenze naturali, velocità di taglio massime e consumo energetico.
Le specifiche di progetto legate alla precisione degli utensili e alla gestione delle vibrazioni sono storicamente risolti mediante soluzioni ad elevata rigidezza e inerzia delle teste di taglio, proprietà entrambe proporzionali alla massa. Una massa elevata fornisce elevata resistenza strutturale e inerzia dinamica. Tuttavia, teste di taglio pesanti comportano spiacevoli inconvenienti in termini di velocità di fresatura, consumo di energia per accelerazione o decelerazione dell’utensile, oltre a complicazioni nella movimentazione (manuale o automatizzata) degli utensili durante gli attrezzaggi. Tali limitazioni sono in contrasto con i recenti trend di ricerca e sviluppo del settore. Di conseguenza, aziende e centri di ricerca stanno proponendo alcune varianti avanzate di teste di fresatura a massa ridotta. Occorre sottolineare però che, a differenza dei classici esercizi di ottimizzazione topologica, gli utensili da taglio per fresatrici sono componenti complessi in cui coesistono elementi di tipo strutturale e di tipo funzionale (si pensi ad esempio al sistema di lubrificazione interno all’utensile). I primi sono responsabili della rigidezza torsionale, del livello di sollecitazione, dell’entità delle deformazioni e della massa complessiva. I secondi provvedono, invece, alle opportune funzioni di lubrificazione, raffreddamento, allineamento e stabilizzazione degli inserti diamantati… Per la progettazione di parti così complesse, l’uso di algoritmi iterativi di ottimizzazione topologica basati sul metodo degli elementi finiti (FEM) è poco pratico e talvolta inefficace [4-5]. Infatti, se l’identificazione della funzione obiettivo può essere relativamente semplice (per esempio la minimizzazione della massa), le variabili di progetto sono estremamente complicate da definire e formalizzare per l’iterazione algoritmica.
Facciamo un esempio: la forma ottimizzata dei canali di lubrificazione necessita di modelli fluido-strutturali separati che non sono inclusi nell’algoritmo di ottimizzazione topologica. Quindi saranno da trattare separatamente con modelli teorici del tutto differenti [6-7]. Ciò nonostante, canali e camere di lubrificazione contribuiscono alla funzione obiettivo nominale. La distribuzione dei canali partecipa inoltre al bilanciamento delle masse e alle simmetrie del pezzo, indispensabili per la riduzione delle vibrazioni autoindotte durante la rotazione. Infine, la definizione dei cosiddetti spazi di “design” e di “non design”, usate dai software per controllare le regioni da ottimizzare topologicamente, può ostacolare la fusione di parti separate aventi, nel progetto originale, interazioni reciproche o funzioni combinate.
In conclusione, quando il componente da riprogettare ha un’elevata complessità geometrica e funzionale combinata, come nel caso degli utensili da taglio, gli algoritmi di ottimizzazione appaiono poco efficaci e devono essere integrati dall’intervento espero del progettista.
Design e motivazioni
L’approccio utilizzato per la riprogettazione si ispira al metodo di ottimizzazione per AM proposto da Emmelmann et al. [8] basato su due fasi: ideazione e progettazione, riportate in Figura 1.
Nel caso specifico della testa di fresatura è stata inserita l’ottimizzazione funzionale in modo tale da tenere in considerazione anche le caratteristiche di progettazione funzionale e le relative variabili funzionali coinvolte. La necessità di calcoli paralleli (come le simulazioni multifisiche), infatti, renderebbe poco pratica la combinazione parallela di tutte le variabili di progetto coinvolte nell’ottimizzazione.
La testa di fresatura ha un diametro di 125 mm, un’altezza di 58 mm e otto inserti contenenti altrettanti taglienti diamantati PCD (polycrystalline diamond tools).
Nella versione originale, la testa è composta da due parti separate, corpo principale e coperchio, accoppiate da un collegamento filettato lungo l’asse di rotazione. Gli otto inserti sono montati a 45° di distanza angolare lungo il perimetro mediante bloccaggi conici autocentranti. La massa complessiva del componente è di 1941,3 g.
L’utensile nella sua conformazione originale è rappresentato in Figura 2a e nel disegno di Figura 3.
Prendendo come modello di riferimento una fresatrice dalle prestazioni medie (36 kW), le condizioni di lavoro tipiche sono: velocità massima di rotazione 10.000 giri/min (3926 m/min velocità di taglio massima), spessore di fresatura massimo 0,2 mm (0,127 mm in media), area di fresatura massima 2,394 mm2, forza di taglio massima 1600 N su tagliente singolo (1104 N in media), forza media per giro di 555 N su tagliente singolo e coppia media per giro di 34,69 Nm su tagliente singolo. Il materiale della testa di taglio è titanio grado 5 (Ti6Al4V).
Il sistema di lubrificazione, nella sua configurazione originale, prevede otto canali radiali diretti verso le frese perimetrali e quattro assiali diretti verso la superficie superiore, come riportato in Figura 3. I primi consentono il raffreddamento della temperatura dei taglienti mediante lo spray lubrificante prodotto all’uscita dei canali, mentre i secondi contribuiscono alla rimozione dei detriti. Tutti i canali partono da un serbatoio ad anello, di forma piatta, situato all’interno della testa che funge da serbatoio e riduce le oscillazioni del flusso di lubrificante nelle diverse condizioni operative. Il canale principale di alimentazione della lubrificazione della macchina, situato all’interno dell’albero portatesta, alimenta il serbatoio dall’alto.
La riprogettazione della testa di taglio si basa sugli otto passaggi intermedi riportati in Figura 4. I dettagli di ogni passaggio di progettazione includono i vincoli del processo additivo, quali supporti temporanei, orientamento della parte in macchina, sovrametalli e gestione-estrazione della polvere. Viene applicato il metodo di ottimizzazione topologica, in cui la funzione obiettivo è la minimizzazione della massa complessiva.
Come già accennato in precedenza, gli algoritmi di iterazione implementati nei software commerciali non forniscono un’ottimizzazione soddisfacente di proprietà strutturali e funzionali. È richiesto l’intervento diretto del progettista a causa della complessità del componente per definire tutti i dettagli che coinvolgono la conoscenza del processo produttivo e l’impiego dell’utensile. Questi dettagli includono, ad esempio, lo spessore ammissibile delle pareti nelle diverse zone, il sovrametallo attorno ai fori filettati, la distribuzione e la forma dei canali, la capacità autoportante delle superfici interne durante la stampa… Per questi motivi, tutte le varianti intermedie di Figura 4 sono state progettate calcolando ad ogni passaggio la distribuzione delle sollecitazioni all’interno del componente, rimodellando la parte rispetto allo step precedente e rimuovendo le regioni meno sollecitate di materiale. Ad ogni passaggio si effettua la verifica a snervamento e alla deformazione. Allo stesso tempo, la valutazione diretta del progettista prevede il rispetto di tutti i requisiti funzionali per ogni passaggio intermedio, che altrimenti non verrebbero considerati da algoritmi automatici. Nella versione finale, si ottiene la riduzione del 25% della rigidezza torsionale originale, in accordo con le proprietà degli utensili di fresatura disponibili in commercio [9].
Dopo la riprogettazione, il volume del componente viene ridotto del 33,9%. La fusione del corpo centrale e del coperchio elimina la possibilità di perdite di lubrificante attraverso le superfici accoppiate. Il re-design è stato diretto prevalentemente verso la parte interna dell’utensile, preferendo mantenere pressoché inalterata la forma esterna del componente. Tale scelta deriva dalla necessità di preservare le superfici di accoppiamento esterne originali con i taglienti e con la macchina fresatrice.
La fabbricazione basata su processi additivi consente di realizzare cavità e canali interni durante la crescita del componente [10, 11], motivo per cui il corpo principale e il coperchio vengono fusi insieme per creare un’unica parte.
La geometria dell’utensile di taglio modificato è riportata in Figura 2b e in Figura 3. Le cavità prodotte all’interno della testa comprendono un serbatoio centrale, i canali e alcuni volumi liberi utilizzati per la riduzione della massa complessiva. La nuova configurazione dei canali è riportata in Figura 3. Il nuovo serbatoio di lubrificante deriva dalla fusione di corpo e coperchio, che consente un volume più elevato del 10,4% e una forma più arrotondata che accrescono l’inerzia del fluido all’interno del serbatoio e migliorano l’attenuazione delle oscillazioni della portata. Il numero di canali assiali è portato da quattro a otto per aumentare la capacità di rimuovere i trucioli dal pezzo. L’asse dei canali laterali, originariamente rettilineo, diventa di forma parabolica per aumentare la velocità di estrazione del lubrificante sfruttando l’effetto centrifugo. Il sistema di lubrificazione modificato fornisce flusso e pressione più uniformi e una maggiore velocità radiale in uscita del lubrificante, come accertato dalle simulazioni riportate nel seguito.