Le soluzioni per il riscaldamento domestico La Nordica-Extraflame sono progettate e realizzate dal gruppo vicentino esclusivamente in Italia. Grazie ad accurate ricerche sul fronte costruttivo ed ecologico, sono in grado di assicurare basse emissioni e minimo inquinamento, nonché la miglior resa e un grande risparmio economico. Prerogative, queste ultime, che caratterizzano anche gli impianti Salvagnini, coi quali vengono realizzate in lamiera parti estetiche, interne e funzionali di svariate tipologie di stufe, cucine, caminetti e caldaie.
Sono oltre 200 i modelli che oggi compongono la proposta di prodotto del gruppo La Nordica-Extraflame, tra stufe, cucine, caminetti e caldaie a legna e caldaie a pellet. Una diversificata gamma di soluzioni sempre più efficienti e all’avanguardia in termini di elevate prestazioni e basse emissioni, frutto del know-how di oltre cinquanta anni di attività ed esperienza di settore. Tanti ne sono passati infatti da quando, nel 1968, i fratelli Silvano, Giannino e Giorgio Dal Zotto hanno iniziato questa avventura imprenditoriale che oggi la famiglia porta ancora avanti con grande dedizione, investendo in tecnologia e innovazione. Dagli anni 60 ad oggi la produzione si è trasformata da artigianale a industriale ma l’amore e la passione sono rimasti invariati.
Un cammino che nel tempo ha portato il Gruppo a conquistare un mercato internazionale in oltre 50 paesi nel mondo, con un’offerta sempre più hi-tech, totalmente Made in Italy, per la produzione di energia per il riscaldamento domestico a biomassa. «Una produzione – spiega il Technical Manager, Robert Dal Zotto – costantemente rinnovata e aggiornata, che richiede una grande attenzione per la sua pianificazione, vista la moltitudine di varianti e l’impossibilità di attuare una elevata standardizzazione». Una delle parti complesse del ciclo di sviluppo di prodotto risiede proprio nella gestione dei semilavorati e della componentistica in lamiera, realizzata con diversi sistemi Salvagnini. Il layout produttivo è composto da un magazzino automatico, una punzonatrice, un laser, una pannellatrice e cinque presse piegatrici, cui sovraintende un performante ambiente software proprietario integrato, a cui viene affidata tutta la parte di gestione della programmazione, della pianificazione e della produzione, sempre sviluppato dal costruttore veneto.
Piegatura in batteria a garanzia della flessibilità
Presso gli stabilimenti di La Nordica a Montecchio Precalcino (VI) sono in funzione sin dal 2009 alcuni impianti Salvagnini. Il magazzino automatico a vassoi MV è il cuore pulsante del sistema: in grado di gestire sia per pacchi di lamiera su pallet di legno sia senza pallet, consente di coordinare e realizzare automaticamente e just-in-time il trasferimento di tutti i flussi di lamiera necessari alle diverse lavorazioni, incrementando l’efficienza globale del layout produttivo riducendo tempi e costi operativi. Il magazzino MV alimenta un laser L5 – di cui parleremo in seguito – e una punzonatrice-cesoia S4 per lavorare lamiere con misure massime di 3.048 x 1.650 mm, dotata di disimpilatore automatico da pacco PD e di impilatore automatico IA. Una volta punzonate le lamiere possono essere nuovamente stoccate a magazzino o scaricate per alimentare le stazioni di piegatura a valle. Del 2009 è anche la pannellatrice P4 2116, che oltre alle dotazioni standard delle pannellatrici Salvagnini è equipaggiata con CLA – lame ausiliarie, componibili in lunghezza e disponibili sia in positivo che in negativo, per la realizzazione di alette e pieghe più corte dell’intera lunghezza della lamiera.
Il modello installato in La Nordica è dotato anche di HPT, un dispositivo di carico/scarico semi automatico su cui l’operatore posiziona il foglio di lamiera. La pinza alimentatrice preleva il foglio, lo introduce nel campo di lavoro e, alla fine del ciclo di piegatura, lo riposiziona nuovamente su HPT. Risale invece al 2020 un nuovo, importante investimento: il magazzino MV è stato asservito anche ad un nuovo impianto di taglio laser fibra L5, con sorgente da 4 kW e campo di lavoro da 3.048 x 1.524 mm, completo di automazione di carico/scarico ADLL e di sistema di sorting automatico MCU. Ma non è tutto, perché La Nordica si è dotata anche di una batteria di ben 5 presse piegatrici B3 da 3 metri e 100 ton. «L’acquisizione delle 5 presse piegatrici – rileva Dal Zotto – nasce dalla precisa esigenza di far fronte a volumi produttivi significativi pur mantenendo massima flessibilità operativa, per essere più veloci nella gestione del cambio ordini e per assecondare le esigenze di un mercato oggi sempre più dinamico. Proprio per questo motivo il reparto di piega è posto fisicamente di fronte all’impianto laser, con una logistica che agevola il flusso di lavoro. Dall’altro lato lo stesso laser va invece ad alimentare anche la punzonatrice-cesoia e la pannellatrice».
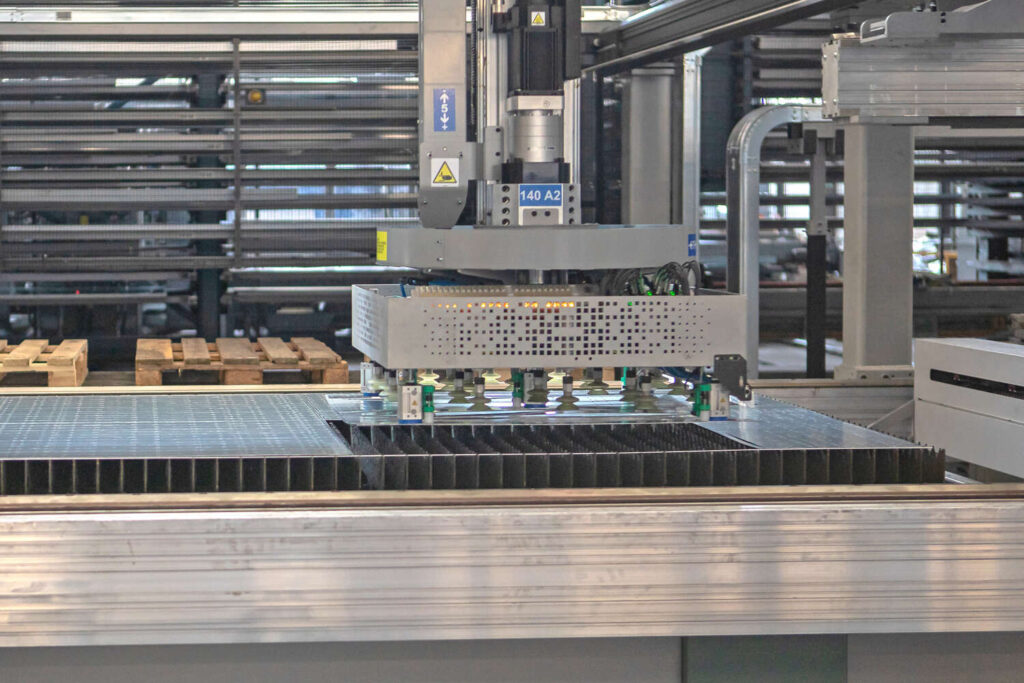
Taglio laser e piega perfetti per parti estetiche, interne e funzionali
La lamiera lavorata trova applicazione nei vari prodotti del gruppo La Nordica-Extraflame come parti estetiche, parti interne e parti funzionali. «Le lamiere da noi lavorate – precisa Dal Zotto – sono di diverse tipologie di materiale, dallo zincato, all’inox, alle lamiere smaltabili, in spessori che vanno normalmente dagli 8/10 ai 30/10 di mm. Ci avvaliamo anche di qualificati e selezionati partner esterni per la fornitura di alcuni manufatti, e per la realizzazione di tutti i trattamenti superficiali necessari come le verniciature e le smaltature». Entrando più nel dettaglio del processo di taglio, l’impianto L5 Salvagnini in La Nordica vanta un campo di lavoro da 3.048 x 1.524 mm, sorgente laser a fibra ad alte dinamiche da 4 kW. È connesso al magazzino MV grazie ad un dispositivo ADLL, che automatizza il carico delle lamiere e lo scarico delle lastre lavorate, con tempi ciclo molto rapidi, ed elimina le fasi intermedie di manipolazione. Ma è dotato anche di un dispositivo di sorting automatico MCU. Quest’ultimo rappresenta la soluzione automatica sviluppata dal costruttore vicentino per impilare agilmente parti con geometrie, dimensioni e pesi differenti. Oltre alla strategia di sorting standard, MCU può lavorare in modalità multigripping, permettendo di prelevare in sequenza più parti con lo stesso organo di presa, o double picking, consentendo la discesa contemporanea dei due organi di presa per prelevare due parti indipendenti riducendo di oltre il 25% i tempi destinati al prelievo dei pezzi. MCU ha pochi limiti: è in grado di prelevare spessori tra 0.5 e 12 mm e pesi fino a 65kg per ciascun manipolatore, che diventano 130kg quando i due organi di presa lavorano in coppia. La flessibilità e l’estrema mobilità dei manipolatori, che possono ruotare sull’intero arco dei 360°, annulla i vincoli geometrici e consente di prelevare qualsiasi parte, indipendentemente dalla sua forma e dimensione massima.
La gestione di MCU è demandata al software Salvagnini CM, che permette la definizione automatica delle prese dei pezzi, la generazione automatica delle sequenze di scarico ed il posizionamento delle pile di parti nelle aree di scarico. L’interfaccia è semplice da usare e permette interazioni ed affinamenti manuali. CM può essere utilizzato sia in ufficio che a bordo macchina. Le 5 nuove presse piegatrici installate in La Nordica fanno parte della gamma B3 Salvagnini: sono progettate per combinare le caratteristiche e i benefici operativi delle soluzioni elettriche e idrauliche, e sono ideali per produzioni dinamiche. Sono 17 i modelli disponibili, con forza da 60 a 400 ton, corsa da 300 a 450 mm e lunghezze utili di piega comprese tra un minimo di 2.040 e un massimo di 6.100 mm. Quelle scelte da Nordica sono delle B3 100/3000, macchine da 100 ton su 3.060 mm di lunghezza utile, 2.640 mm di distanza tra le spalle, 435 mm di profondità incavo. «Il magazzino automatico centrale – sottolinea il Technical Manager – svolge un ruolo chiave nella logica dei diversi flussi, fungendo da buffer, da polmone proprio per riuscire a massimizzare la produttività dei vari reparti».
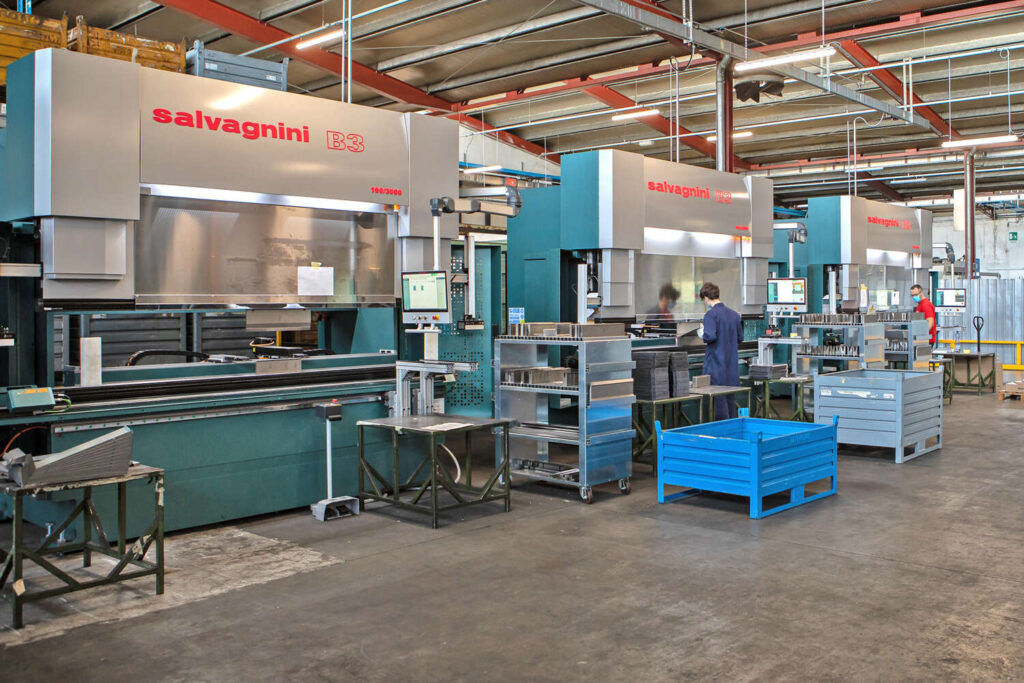
Integrazione 4.0 tra ERP, CAM tecnico e bordo macchina
«L’intero parco macchine acquisito da Salvagnini – afferma lo stesso Dal Zotto – incluse le più datate, viene gestito in 4.0 grazie agli applicativi della suite STREAM per la parte di programmazione e al software OPS per la gestione della produzione. Quest’ultimo è stato implementato nella sua versione più completa, al servizio dell’intero layout produttivo, proprio per massimizzarne l’efficienza e per raggiungere la piena integrazione tra ufficio tecnico e produzione». OPS, acronimo di Order Processing System, è un ambiente software modulare in grado di connettere perfettamente tra loro ERP, CAM tecnico e bordo macchina, gestendo il ciclo di produzione nella sua interezza senza problemi o imprevisti, anche nel caso di una complessa aggregazione di sistemi come quelli presenti in La Nordica.
Tale software proprietario, a seconda della configurazione scelta, è in grado di ricevere gli ordini di produzione direttamente dal gestionale di fabbrica, di analizzarne i parametri come quantità, priorità di produzione, codici, tempi di consegna, e, infine, di lanciare la produzione delle singole parti.
E lo fa interfacciandosi con il software CAD/CAM e ottimizzando programmi ad hoc per il layout produttivo disponibile.
Per come è pensato, sviluppato e costantemente migliorato, OPS si propone di ridurre i tempi di lavoro effettivi, i tempi di attesa e il lead time totale, ma è soprattutto capace di azzerare il rischio di errore: l’automatizzazione dei processi esclude tanto gli errori di digitazione di codice quanto quelli legati alla lavorazione di materiali errati.
Passione e duro lavoro segnano il passo dell’eccellenza made-in-Italy
La Nordica-Extraflame rappresenta bene quello che nel nord-est italiano è una caratteristica distintiva, differenziante e vincente: la passione e il duro lavoro.
Nato nel 1968, il Gruppo ha affrontato in questi anni un impegnativo aumento della gamma passando dalle “semplici” stufe a prodotti evoluti e diversificati ad alto contenuto tecnologico, adatti a tutti i gusti ed esigenze di mercato.
«Un’evoluzione – sostiene con orgoglio Andrea Santambrogio, Direttore Marketing dell’azienda – cui sottende però la precisa volontà di mantenere intatta tutta la nostra identità italiana e veneta che ci contraddistingue, visto che ogni nostro prodotto viene progettato, realizzato e testato esclusivamente nei nostri stabilimenti vicentini». In questo contesto il Gruppo crede fermamente nel made in Italy e nella grande capacità di fare innovazione, quale frutto di importanti e ingenti investimenti in attività di ricerca e sviluppo e di processo, sia sul fronte costruttivo che ecologico. «Ciò – rileva Santambrogio– al fine di assicurare alle nostre soluzioni per il riscaldamento domestico, basse emissioni e minimo inquinamento, nonché la miglior resa e un grande risparmio economico. La sfida è infatti quella di riuscire ad affrontare al meglio un mercato che si dimostra sempre più competitivo, potendo contare su tutti gli strumenti a disposizione, sia di produzione come gli impianti Salvagnini che di know-how». Un mercato che per il Gruppo vicentino è ormai sostanzialmente mondiale, visto l’export verso oltre 50 paesi.
«Un export certamente importante – conclude Santambrogio– supportato anche dal non secondario aspetto che tutti i nostri prodotti sono certificati dalla maggior parte degli enti preposti: una garanzia tanto per il cliente finale, quanto per i nostri partner commerciali».
di Fabio Boiocchi e Gianandrea Mazzola