Leggerezza, conducibilità termica ed elettrica, resistenza… sono solo alcune delle caratteristiche che rendono attrattivi l’alluminio e le sue leghe.
Come importanza, a livello mondiale, è secondo solo all’acciaio. È impiegato con successo pressoché in ogni settore. È l’alluminio. O, più precisamente, si tratta dell’alluminio e delle sue leghe, che vantano specifiche qualità tecnologiche, fra cui spiccano la leggerezza e la conducibilità termica ed elettrica. Proprio queste caratteristiche rendono questo materiale particolarmente attrattivo per l’aerospace e l’automotive, dove leggerezza, durata e resistenza sono fondamentali.
Fra l’altro, l’alluminio è, a tutti gli effetti, un materiale infinito: poiché è quasi completamente riciclabile, può essere rifuso all’infinito, a favore della sostenibilità ambientale, sia da un punto di vista dello smaltimento rifiuti che per il consumo energetico legato alla sua produzione.
La produzione dell’alluminio può derivare dalla raccolta del minerale in miniere, che in genere sono a cielo aperto, a cui segue un trattamento in celle elettrolitiche, che permettono di ottenere il metallo puro al 99,5%. La produzione in celle elettrolitiche comporta un consumo di energia elettrica di circa 15 Wh/Kg. Per contro, l’alluminio che deriva da processi di riciclo, costa circa il 40% in meno.
Quindi il riciclo, oltre ad evitare l’estrazione di bauxite, permette, allo stesso tempo, di risparmiare il 95% dell’energia richiesta: per ricavare 1 Kg di alluminio partendo da bauxite occorrono circa 14 kWh, mentre ne bastano circa 0,8 se si parte da rottame.
Già ai primi del ‘900, il riciclo era una pratica comune, ma era considerata un’attività di basso profilo; a partire dagli anni ‘60, con l’avvento massiccio di lattine, e il boom dell’impiego delle leghe d’alluminio nei più disparati settori, il riciclo è diventato sempre più importante, tanto che oggi è una componente strategica nell’industria di questo materiale.
Aspetti metallurgici e caratteristiche
Nel linguaggio comune si dice alluminio, ma in realtà si fa quasi sempre riferimento ad una lega, dove l’alluminio è il componente principale, ma di cui fanno parte anche altri elementi di alligazione. In natura sono pochi gli elementi in grado di formare tante leghe quante ne permette l’alluminio, leghe che sono anche molto diverse fra loro, e che si differenziano, oltre che per le caratteristiche meccaniche, ma anche quelle estetiche.
Seppur differenti, tutte le leghe di alluminio contengono almeno 60% di materiale puro, hanno un peso specifico notevolmente inferiore a quello dell’acciaio, resistono bene a corrosione e vantano un’eccellente conducibilità elettrica e termica. Anche se esistono più di mille leghe diverse, la produzione massiva, con uno spiccato interesse a livello industriale, si concentra su circa 20. Resta comunque il fatto che la scienza dei materiali, spinta dalle richieste del mercato, studi sempre con interesse nuove formulazioni, sia per migliorare leghe già conosciute, sia per svilupparne di nuove, in linea con le moderne esigenze. È il caso delle leghe base litio, che sono ormai giunte alla terza generazione, oggi caratterizzate da interessanti miglioramenti sia per le proprietà meccaniche più bilanciate, che per la migliore formabilità e lavorabilità per asportazione di truciolo, oltre che per l’eccellente resistenza a corrosione. Se le proprietà delle leghe di alluminio presentano numerosi vantaggi, non vanno comunque dimenticati gli aspetti negativi, che, in alcuni casi, possono rappresentare una criticità nell’utilizzo, se non attentamente valutati. Si tratta essenzialmente dei costi di produzione, che sono circa tre volte quelli dell’acciaio, gli elevati consumi energetici per la produzione e la scarsa saldabilità delle leghe.
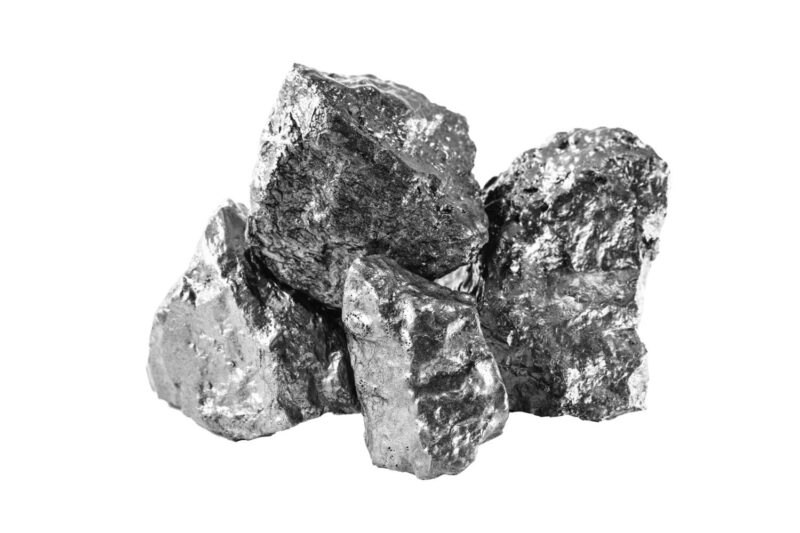
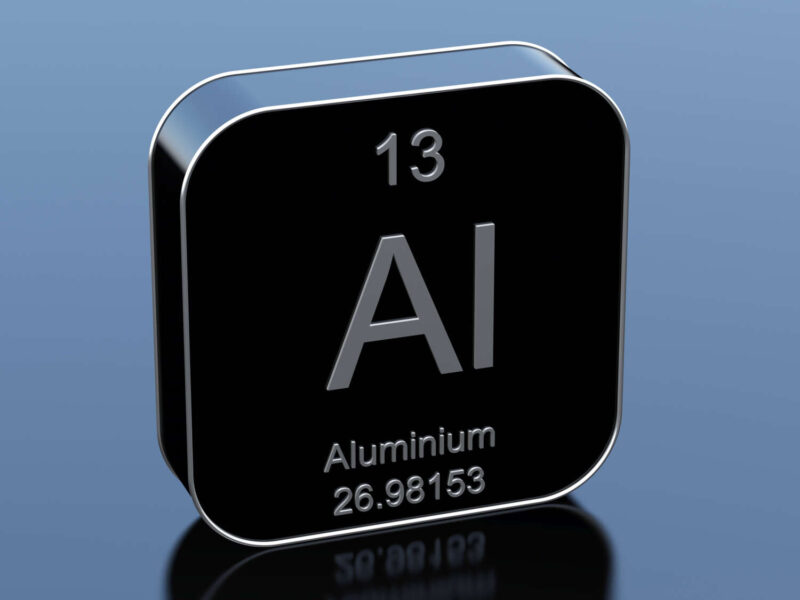
Le leghe e la classificazione
Tutte le leghe di alluminio hanno delle caratteristiche comuni:
• Bassa temperatura di fusione (510 ÷ 650°C)
• Basso peso specifico (2,66 ÷ 2,85 g/cm3)
• Elevata conducibilità termica ed elettrica
• Alto tenore di alluminio
Oltre a queste proprietà, che si potrebbero definire standard, altre variano in maniera significativa in funzione degli elementi in lega, che possono essere suddivisi in primari e correttivi.
Gli elementi primari sono Cu, Si, Mg, Zn, Mn, che formano le leghe madri, con caratteristiche meccaniche base. In particolare, gli effetti degli elementi primari sono:
– Rame: aumenta resistenza meccanica a caldo
– Silicio: aumenta colabilità e riduce coefficiente di dilatazione
– Magnesio: aumenta resistenza a corrosione in ambiente alcalino e in mare
– Zinco: aumenta resistenza meccanica, sopratutto se associato a magnesio.
– Manganese: aumenta resistenza meccanica e alla corrosione
Gli elementi correttivi sono tutti quegli elementi chimici, come Ni, Ti, Zr, Cr, Bi, Pb, Cd, Sn, Fe, introdotti in lega per esaltare determinate caratteristiche meccaniche, in funzione delle prestazioni richieste al manufatto. Un caso a parte riguarda Fe, che è comunque sempre presente come impurezza e, in linea di massima, è un elemento indesiderato.
I criteri di suddivisione delle leghe di alluminio sono diversi, ma essenzialmente riconducibili a due macro famiglie:
• leghe da fonderia
• leghe da lavorazione plastica, destinate a subire variazione di forma mediante lavorazione per asportazione di truciolo
La classificazione internazionale, secondo lo standard ASTM, prevede sistema di numerazione in 4 cifre, dove la prima indica l’elemento principale, quindi:
– 1000: Al con purezza minima 99%
– 2000: Al – Cu
– 3000: Al – Mn
– 4000: Al – Si
– 5000: Al – Mg
– 6000: Al – Mg – Si
– 7000: Al – Zn
– 8000: Al – altri elementi. È considerato un gruppo con leghe miste, con elementi non presenti negli altri gruppi
– 9000: sono leghe ancora in fase sperimentale
Una classificazione parallela, si riferisce ai nomi commerciali delle principali leghe in utilizzate a livello industriale:
• Avional, Duralluminio: leghe Al – Cu
Corrisponde alla serie 2000:
• Peraluman: leghe Al – Mg
Corrisponde alla serie 5000:
• Anticorodal: leghe Al – Si – Mg – Mn
Corrisponde alla serie 6000:
• Ergal: leghe Al – Zn
Corrisponde alla serie 7000 (utilizzata in industria aereospaziale):
• Al-Li: leghe Al – Li, incluse quelle di terza generazione
• Nambè: lega di alluminio sperimentale, con altri 7 elementi in lega
• Magnox: lega Al – Mg (utilizzata per centrali nucleari)
• Zamak – Zama: lega Al – Zn – Mg – Cu (lega da pressofusione)
• Silumin: lega Al – Si
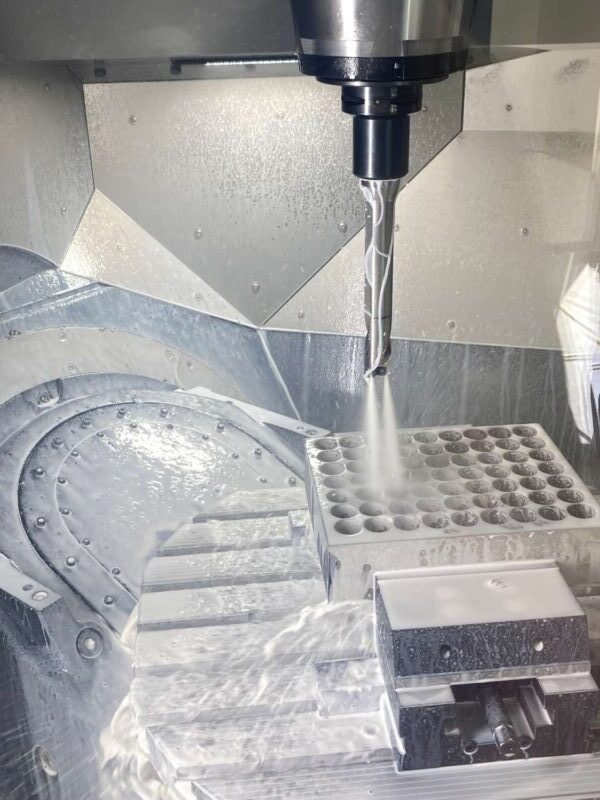
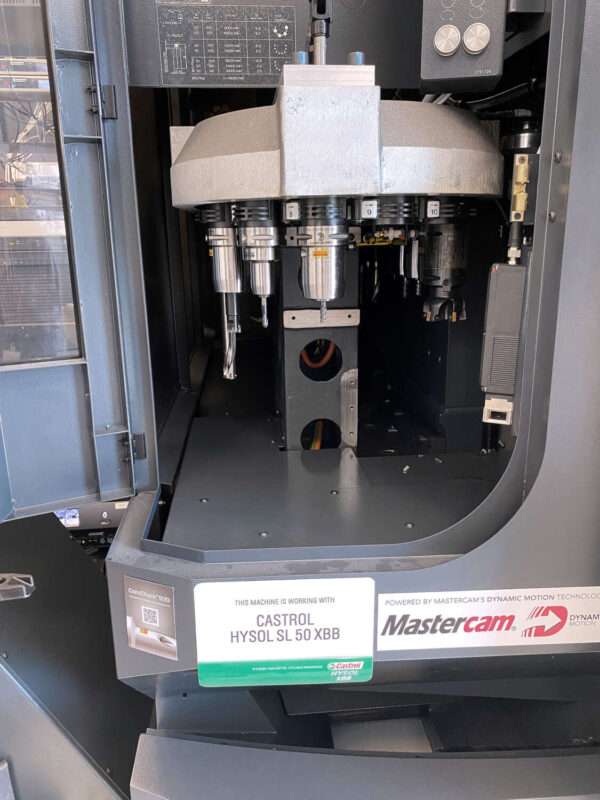
Lavorabilità
Le leghe di alluminio si prestano molto bene alla lavorazione per asportazione di truciolo anche se, per rendere performante ed efficiente il processo, occorre tenere presente come le diverse leghe possono avere comportamenti molto differenti durante la lavorazione e, di conseguenza, occorre adottare tecniche opportune, che permettano al sistema macchina utensile di lavorare al meglio. Come prima cosa va sottolineato ogni processo produttivo per asportazione dell’alluminio avvenga per taglio e non, come nel caso dell’acciaio, per deformazione, con una forte influenza del grado di durezza della lega. Questo incide sulla formazione di truciolo, tenace e fluente o fragile e rigido: in funzione della durezza andrà individuata l’opportuna geometria dell’utensile, in modo da evitare la formazione di battiture e intasamenti che potrebbero compromettere la vita dell’utensile e la qualità del pezzo. Una lavorazione all’utensile delle leghe di alluminio che risponda ai moderni standard di performance richiede macchine utensili veloci e potenti, in grado di ridurre i tempi di produzione. Naturalmente una macchina che consenta un elevato numero di giri al mandrino, deve essere rigida, in modo da consentire una ottima finitura, ma, maggiori sono i giri, più la macchina è delicata e richiede una attenta gestione da parte dell’operatore. Le velocità di taglio elevate sono possibili in quanto il truciolo non riscalda l’utensile a un livello tale da abbassarne la durezza anche se, la temperatura raggiunta è sufficiente a ridurre la resistenza a deformazione del materiale. Dato che è tutto il sistema macchina utensile a decretare lo stato di una lavorazione, un occhio di riguardo va dato anche ai sistemi di presa pezzo: l’alluminio è un materiale delicato che, se relativamente facile da lavorare, può essere critico da bloccare a causa della sua tendenza a deformarsi. Questo significa che un bloccaggio efficace, può esserlo solo “apparentemente”, in quanto può indurre deformazioni tali da obbligare a riprese, chiaramente a scapito dell’efficienza.
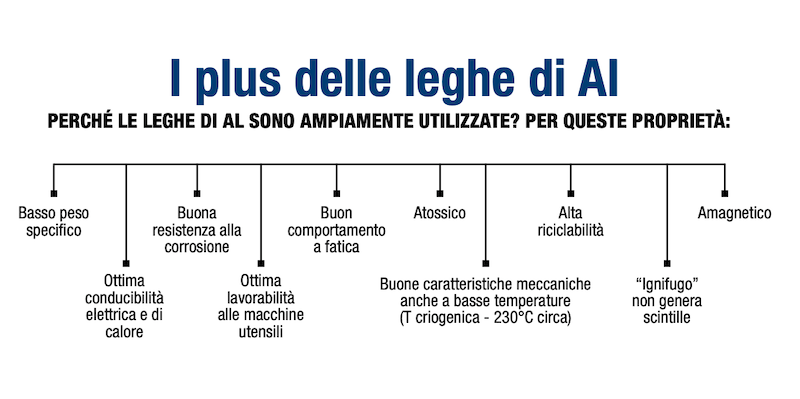
Bagnato o non bagnato?
Il sistema macchina utensile non può non considerare la lubrorefrigerazione, ma qual è la situazione quando si lavorano le leghe di alluminio?
Innanzitutto va sottolineato come le leghe di alluminio possano facilmente essere macchiate dagli oli e quindi l’area di lavoro richiede una grande pulizia. Se la pulizia della cabina è affidata ad efficienti sistemi di lavaggio, in grado di tenere molto pulita la zona di lavoro e le guide, la lavorazione vera e propria richiede un fluido da taglio che sia sempre pulito ed efficiente, opportunamente filtrato e disoleato, con metodi tradizionali o con sistemi più sofisticati ed evoluti, capace di raggiungere gradi di filtrazione anche molto spinti, eliminando sia le micro particelle che gli oli estranei. Al termine della lavorazione, il lavaggio con detergente adeguato esegue una pulizia profonda, per “non lasciare testimoni”, eliminando eventuali bave e microsfridi. Le leghe di alluminio possono esser lavorate anche a secco, a patto che non siano particolarmente dure, gli utensili siano in perfetta efficienza e i parametri di taglio non siano esasperati. In genere si preferisce però l’utilizzo di emulsioni che abbiano ottima stabilità e capacità detergente, anche nell’ottica di prevenire la macchiatura. Il fluido da taglio, che, per i moderni centri di lavoro, è in alta pressione (attenzione al filtraggio!), deve essere impiegato con abbondanza sia sulla punta dell’utensile che su tutto il pezzo, in modo da contenere la temperatura, senza provocare shock termico, cui le leghe di alluminio sono particolarmente sensibili.
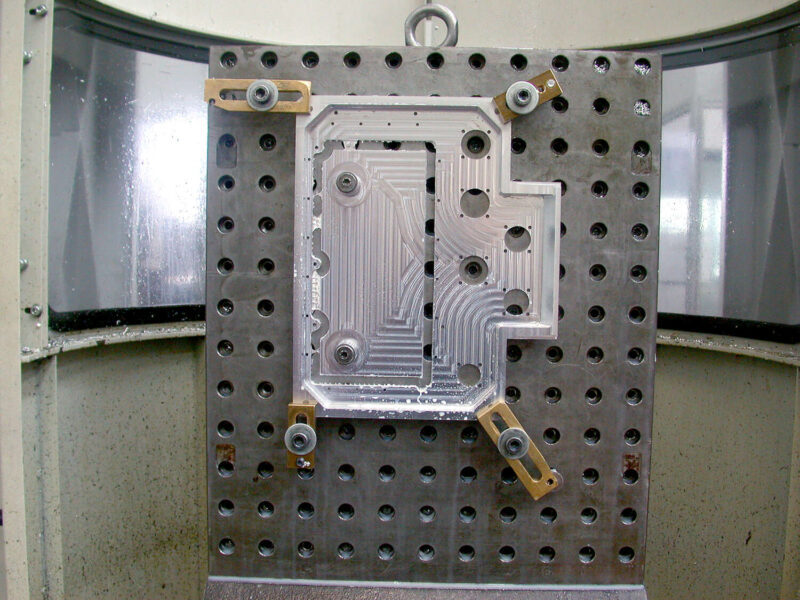
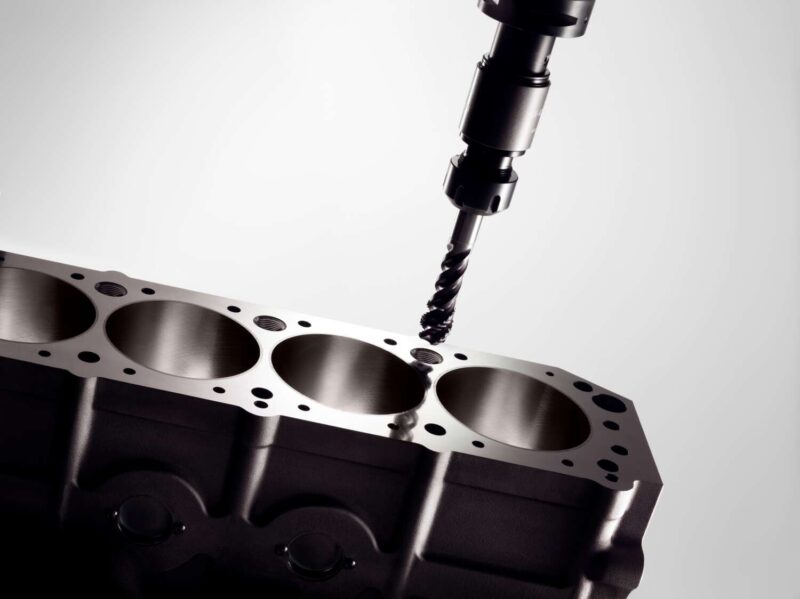
Solo coincidenze?
Nel 1886 l’americano Charles Martin Hall scoprì il primo metodo elettrolitico pratico per produrre l’alluminio. Ma nello stesso anno, anche un giovane scienziato francese, Paul Heroult, lavorando in modo indipendente, mise a punto un processo identico a quello dell’americano: fra i due non c’era stato alcun contatto e neppure erano a conoscenza dei rispettivi studi ed esperimenti.
Ma il caso aveva legato i due scienziati: erano nati lo stesso giorno, brevettarono le loro scoperte contemporaneamente, e morirono lo stesso giorno!
Hall ricevette il brevetto, e il diritto di sfruttamento, negli Stati Uniti, ed Herault in Francia. Oggi al metodo viene dato il nome congiunto di Hall-Herault, e, con le dovute modifiche e migliorie, continua ad essere ampiamente usato per la produzione di alluminio.
Un elemento abbondante
In natura, l’alluminio è l’elemento più abbondante sul pianeta e costituisce circa l’8.6% della crosta terrestre. Non lo si trova allo stato libero, ma sotto forma di silicati e ossidi: il caolino è fra i silicati più conosciuti, mentre il minerale che contiene l’ossido, per il 50%, è la bauxite. A causa delle difficoltà sia estrattive che produttive, l’alluminio è a lungo stato considerato solo un “materiale da laboratorio”: i costi di processo, estremamente elevati, nettamente superiori a quelli dell’oro, non ne permettevano la diffusione.
Nel 1825 H. C. Oersted riuscì, per la prima volta, a produrre alcune gocce di alluminio, anche se è solo a metà dell’800 che si riuscirono a produrre piccole lamine, che permisero di valutarne la malleabilità e la leggerezza. Sul finire dell’800, gli studi di Hall e di Herault portarono allo sviluppo di un processo in grado di ottenere forti quantità a costi contenuti, e, in tutto ciò, un ruolo importante spetta al progresso nella produzione di energia elettrica, diventata più accessibile economicamente e più accessibile. Un’evoluzione del procedimento messo a punto da Hall ed Herault, noto oggi come processo Hall-Herault, è ancora adesso ampiamente impiegato.
Oggi è noto che sono pochi gli elementi in natura con la possibilità di costituire un gran numero di leghe come è il caso dell’alluminio: ogni lega va a modificare, in senso migliorativo, le caratteristiche meccaniche, ma anche quelle estetiche, del metallo allo stato puro.
Vorresti sempre leggere articoli come questo? Iscriviti a Click the Gear. Ogni martedì riceverai notizie di ricerca, materiali, tecnologie, attualità e eventi dal mondo manifatturiero. Clicca qui per iscriverti