La formatura incrementale eredita e potenzia l’arte dei battilastra, unendo la versatilità di un processo sartoriale alla ripetibilità del CNC.
Lo stampaggio della lamiera viene normalmente realizzato a freddo con l’uso di stampi dedicati. In questo processo, l’intero pezzo viene deformato simultaneamente e in tempi molto brevi. Come ci insegna la fisica, molta energia in poco tempo si traduce in tanta potenza.
Per questo motivo le presse richiedono elevati tonnellaggi: il lavoro meccanico della deformazione, cristallizzato nel pezzo, è concentrato in un breve lasso di tempo. Il costo elevato dello stampaggio è legato all’alta complessità degli stampi, che richiede l’uso di macchine utensili precise per la loro produzione e l’uso di materiali costosi. Lo svantaggio dei metodi tradizionali di stampaggio è infatti la necessità di produrre utensili unici per la forma dell’elemento. Per questo motivo, l’uso di metodi di stampaggio convenzionali è limitato alla produzione su media e larga scala.
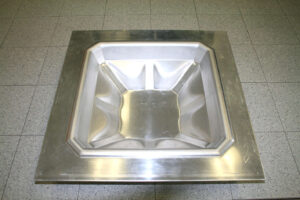
La necessità di una tecnologia flessibile relativamente veloce per le piccole e medie imprese ha portato allo sviluppo della tecnologia SPIF (Single Point Incremental Forming, o formatura incrementale a punto singolo). È definita anche come formatura a controllo numerico senza stampi, per distinguerla dalla formatura manuale da sempre usata dai battilastra. La similitudine non è campata per aria, visto che entrambe permettono di ottenere pezzi di forme diverse senza cambiare utensili. Il processo di formatura incrementale è stato inizialmente sviluppato per le esigenze del settore automotive, ma è ora utilizzato da molte altre industrie, come quella medicale, aerospaziale e nautica.
I metodi SPIF hanno trovato applicazione nella produzione di pezzi di forma complessa e per la produzione rapida di prototipi. L’uso di varianti moderne e più evolute di SPIF permette una riduzione significativa del time-to-market per la produzione di un nuovo prodotto e la riduzione dei costi di produzione.
Grazie alla sua alta formabilità, l’alluminio è il materiale più usato nella formatura incrementale. Molto usate anche le leghe di alluminio della serie 2000 e 7000. Meno diffuse le leghe di titanio e quelle di magnesio, perché richiedono un riscaldamento del pezzo con i modi che vedremo.
Cos’è la formatura incrementale
Il processo di formatura incrementale della lamiera consiste nel modellare il pezzo con un utensile che si muove lungo una traiettoria specifica utilizzando una macchina CNC o un braccio robotico.
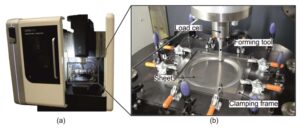
Nel processo SPIF, la lamiera viene bloccata a un telaio, mentre l’utensile di formatura la sagoma gradualmente eseguendo un movimento continuo intorno al bordo, unito ad un movimento di spinta perpendicolare alla superficie. Pertanto, una macchina utensile CNC deve essere controllata in almeno tre assi. L’essenza del processo è il contatto localizzato dell’utensile di formatura con la lamiera e la capacità di controllare il grado di deformazione della lamiera nei punti esposti al movimento di formatura.
L’uso di sistemi CAD/CAM integrati permette di progettare efficacemente la traiettoria dell’utensile su una macchina CNC sulla base di un modello tridimensionale del prodotto.
Le prime ricerche relative alla SPIF sono state effettuate su fresatrici CNC a tre assi a causa della loro elevata rigidità, la possibilità di generare facilmente il percorso dell’utensile utilizzando un software CAM, così come la possibilità di applicare la velocità controllata del mandrino all’utensile. A partire da queste fresatrici CNC sono state costruite macchine SPIF dedicate che avevano forze superiori. Recentemente sono stati condotti diversi studi sull’uso di robot industriali nella fabbricazione di pezzi con SPIF.
Anche se i robot industriali hanno una rigidità inferiore rispetto alle macchine dedicate o alle fresatrici CNC, offrono alla SPIF un’elevata flessibilità grazie al maggior numero di gradi di libertà. In ogni caso, vanno scelti robot molto solidi, con portata al polso di almeno 500 kg.
La tecnologia nel dettaglio
L’utensile usato nella formatura incrementale solitamente è dotato di una punta in carburo di tungsteno o metallo duro, con forma a semisfera, conica, o bombata. In alcuni casi può essere dotato di una sfera libera di ruotare (simile alla punta di una penna biro) rivestita in teflon. Con questo tipo di utensile la finitura superficiale è migliore ed è richiesto uno sforzo meno intenso alla macchina, ma il tempo di lavorazione si allunga.
Nella maggior parte delle applicazioni l’utensile percorre la traiettoria determinata dal CAM, senza però ruotare attorno al proprio asse. In alcuni casi, tuttavia, l’utensile esegue anche un movimento di rotazione forzata con una velocità di rotazione nell’intervallo 200-800 giri/min. La velocità lineare di avanzamento dell’utensile, come per la velocità di rotazione, dipende dalla specifica geometria e tecnologica del processo ed è solitamente nell’intervallo di 300-2000 mm/min.
La velocità di penetrazione dell’utensile va impostata in relazione alla dimensione della punta dell’utensile per evitare la formazione di scanalature cicliche nella superficie del pezzo. I lubrificanti usati nella SPIF corrispondono a quelli usati nello stampaggio convenzionale e sono principalmente adattati ai valori delle pressioni, al tipo di materiali, alla coppia di attrito, alla temperatura di formatura e alla velocità di lavoro dell’utensile.
Nella formatura incrementale comunemente utilizzata si utilizza un solo utensile, e per questo è definita Single Point Incremental Forming (SPIF). Utilizzando una contropunta dal lato opposto del pezzo è possibile realizzare curve più complesse: è la cosiddetta formatura incrementale a due punti (Two Point Incremental Forming, TPIF). Questo sistema richiede però un secondo robot, che si muove in sincrono con il primo.
Il supporto del pezzo può essere fornito anche da un controstampo parziale, di forma semplificata, che fornisce un appoggio nei punti più critici.
Per migliorare ulteriormente la precisione è possibile utilizzare una matrice completa, con la forma esatta del pezzo da realizzare.
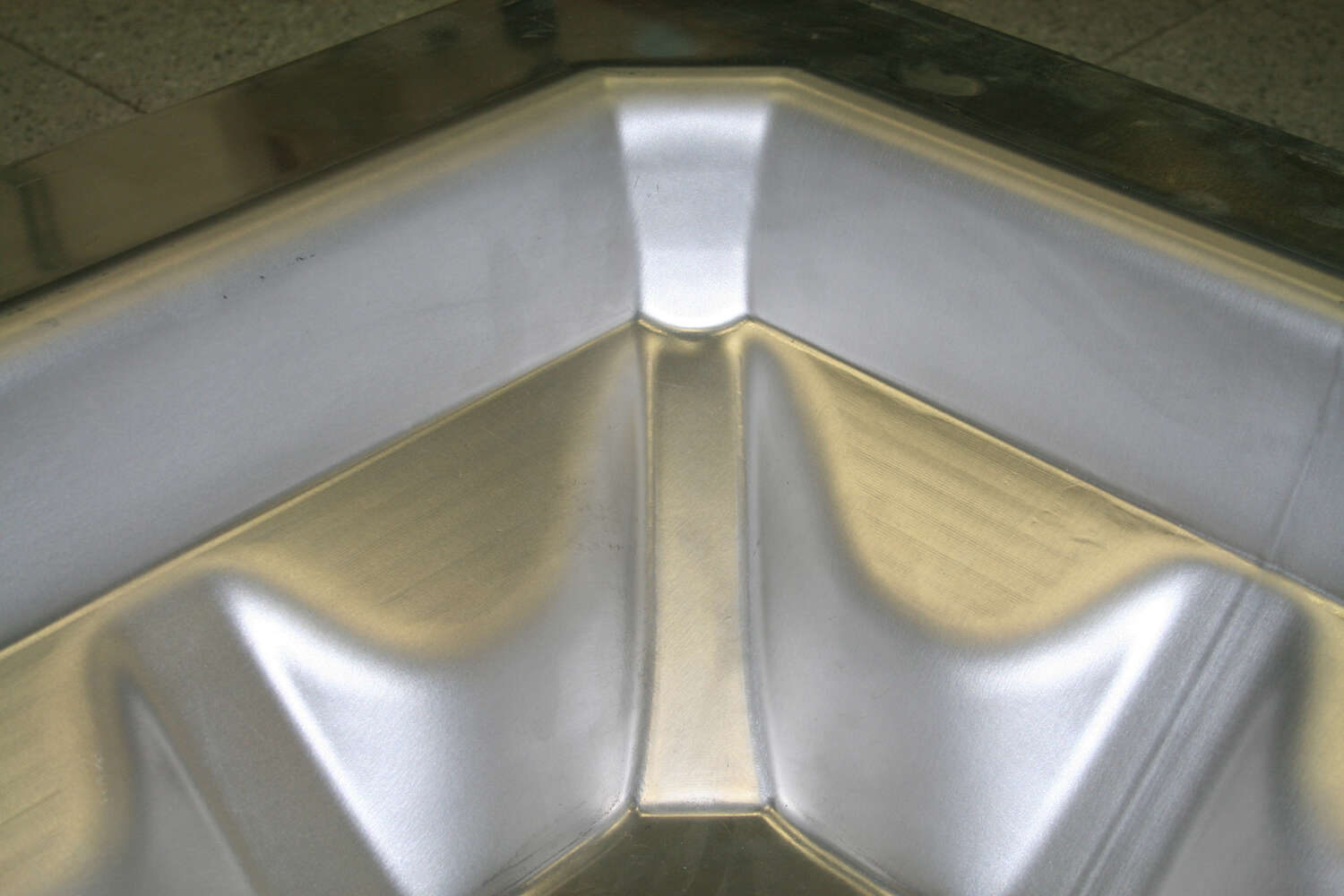
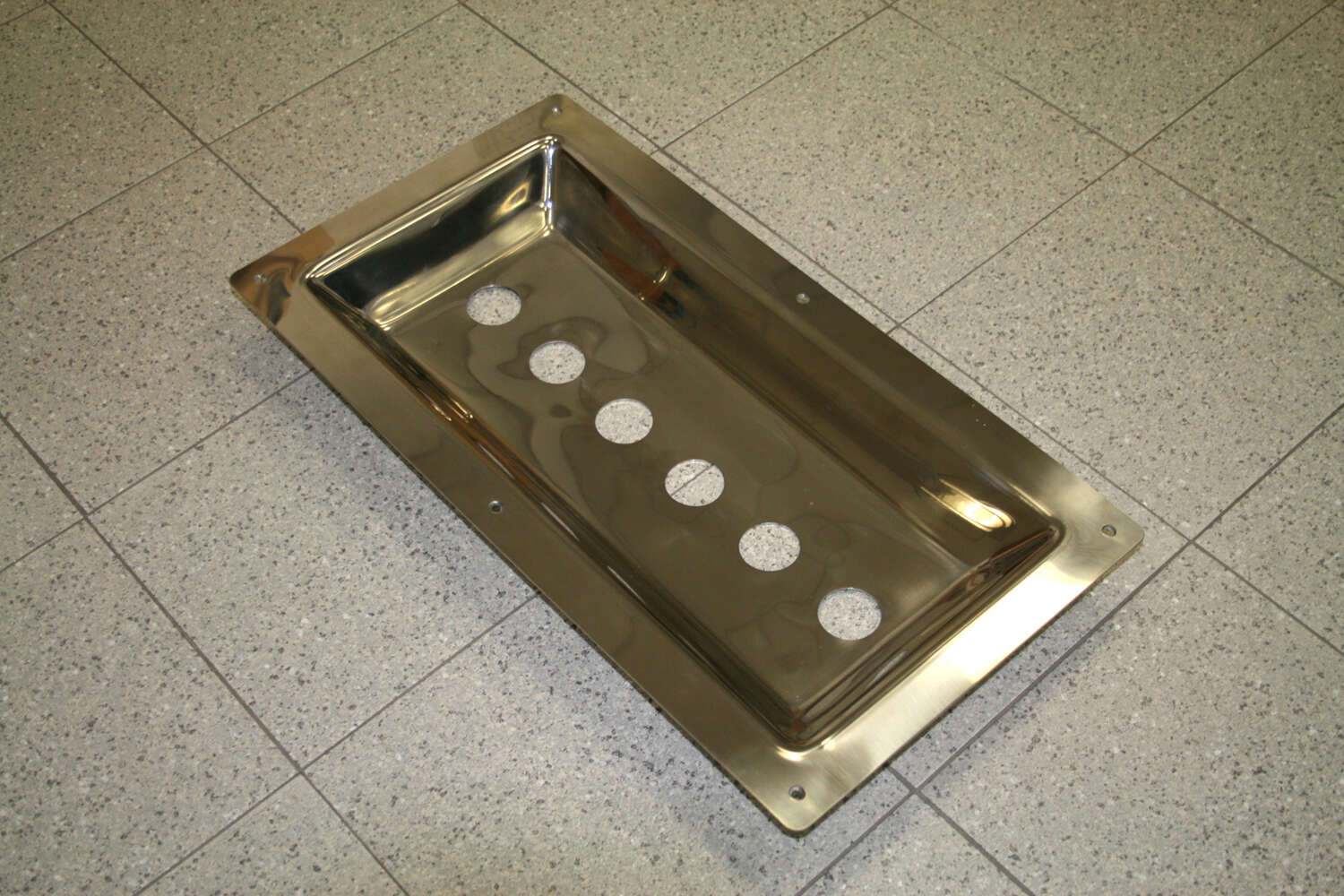
Come anticipato, alcuni metalli non sono lavorabili a temperatura ambiente senza andare incontro a snervamento e lacerazioni. È quindi necessario riscaldare il pezzo fino a renderlo duttile e quindi in grado di accettare le deformazioni richieste. Con la formatura incrementale si possono utilizzare vari metodi:
La lamiera viene fissata ad un telaio, con la parte posteriore chiusa a realizzare una camera che viene riscaldata tramite afflusso di aria calda. In alternativa, la camera può essere dotata di una resistenza elettrica che mantiene il pezzo caldo per irraggiamento. Un terzo metodo prevede il riscaldamento non dell’intera lamiera, bensì del solo punto in lavorazione. A questo scopo viene installato un collettore elettrico direttamente sull’utensile, con l’altro polo fissato al pezzo. Il passaggio di corrente riscalda il metallo nel punto di contatto, diminuendo lo sforzo necessario. Per contro, tra utensile e pezzo si possono formare scintille che vanno ad erodere il punzone e rovinare la finitura superficiale della lamiera.
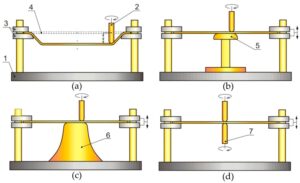
Lo sviluppo più recente prevede invece l’uso di un laser, posizionato con un sistema a tre assi posto sul retro del pezzo. Il fascio riscalda in maniera puntuale la lamiera, ma senza introdurre difetti superficiali.
Le sfide tecnologiche della SPIF
Tra i molti fattori che influenzano l’applicabilità del metodo ISF e la precisione del pezzo formato, vanno citati i parametri tecnologici (tra cui le dimensioni dell’utensile, il valore del passo di penetrazione, la velocità di rotazione dell’utensile, il lubrificante utilizzato), i parametri del materiale del pezzo (incrudimento, anisotropia del materiale, modulo di Young) e i fattori derivanti dal processo di progettazione (spessore della lamiera, geometria del pezzo finale).
Il fenomeno dell’attrito tra il pezzo e l’utensile gioca un ruolo significativo nella deformazione del materiale e nella finitura superficiale dei componenti finiti.
Coefficienti di attrito e parametri di formatura non correttamente selezionati possono portare a un aumento eccessivo della temperatura nelle aree di contatto, riducendo così l’efficacia del lubrificante. Le cattive condizioni di attrito possono essere fonte di graffi e danni alla superficie dei componenti. Questo fenomeno è particolarmente rilevante quando la SPIF viene eseguita su alluminio e titanio e le loro leghe: questi materiali sono particolarmente soggetti all’usura adesiva e al grippaggio. Allo stato dell’arte, ottenere corrette condizioni di attrito richiede lubrificanti di nuova generazione, la scelta di una strategia di formatura efficace, e l’ottimizzazione modifica della superficie dell’utensile.
Vantaggi e svantaggi della formatura superficiale
Il processo SPIF ha dimostrato di ottenere una maggiore formabilità del componente rispetto allo stampaggio convenzionale; tuttavia, questo processo è ancora in fase di studio all’approcciarsi a materiali difficili da formare. Effetti come la temperatura del processo, il ritorno elastico e i meccanismi di deformazione non sono ancora completamente compresi. La formatura incrementale di materiali come acciaio, rame, e alcune leghe di alluminio è sufficientemente collaudata: questi processi non richiedono trattamenti tecnologici speciali, e quindi vengono solitamente eseguiti in condizioni di lavoro a freddo. La SPIF di materiali difficili da deformare, che comprende, per esempio, le leghe di alluminio della serie 5000 e 7000, le leghe di titanio e le leghe di magnesio, richiede per contro molta più attenzione. Queste leghe sono spesso considerate le più difficili da lavorare, e generalmente hanno caratteristiche di formatura meno prevedibili delle comuni lamiere strutturali. Nonostante il costo relativamente basso degli strumenti, i metodi ISF sono convenienti solo nella produzione di piccoli lotti, a causa dei lunghi tempi di formatura rispetto allo stampaggio convenzionale.
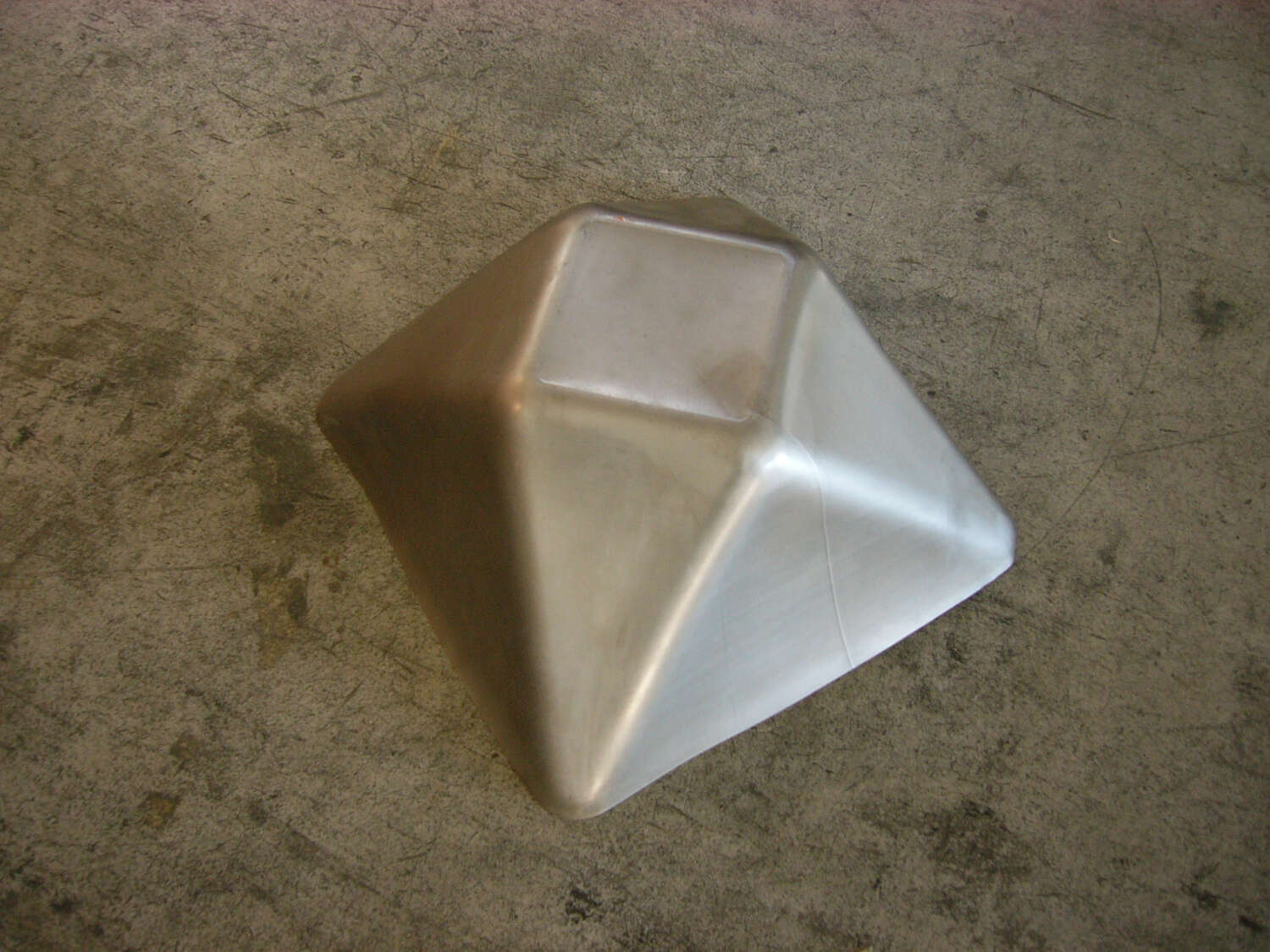
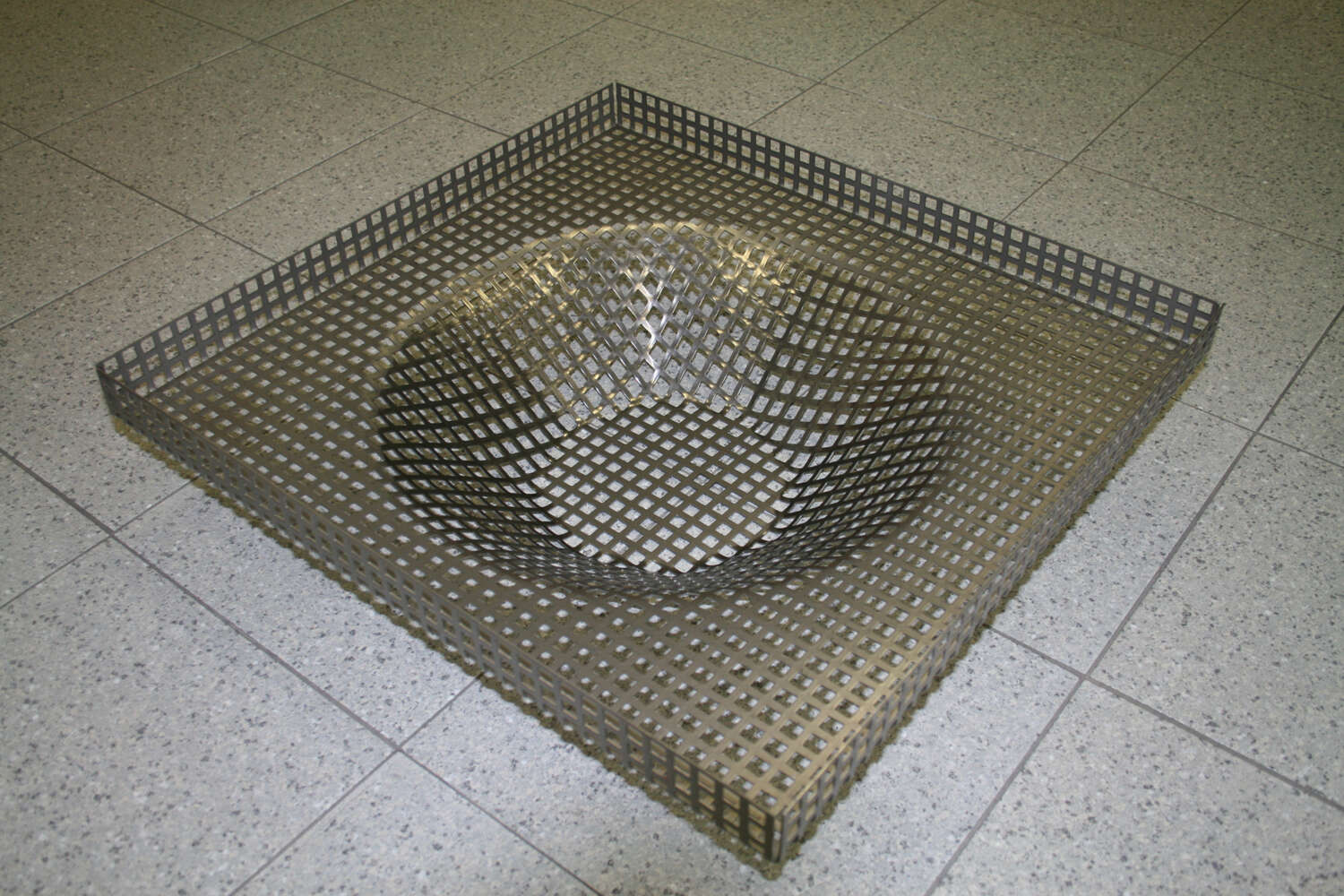
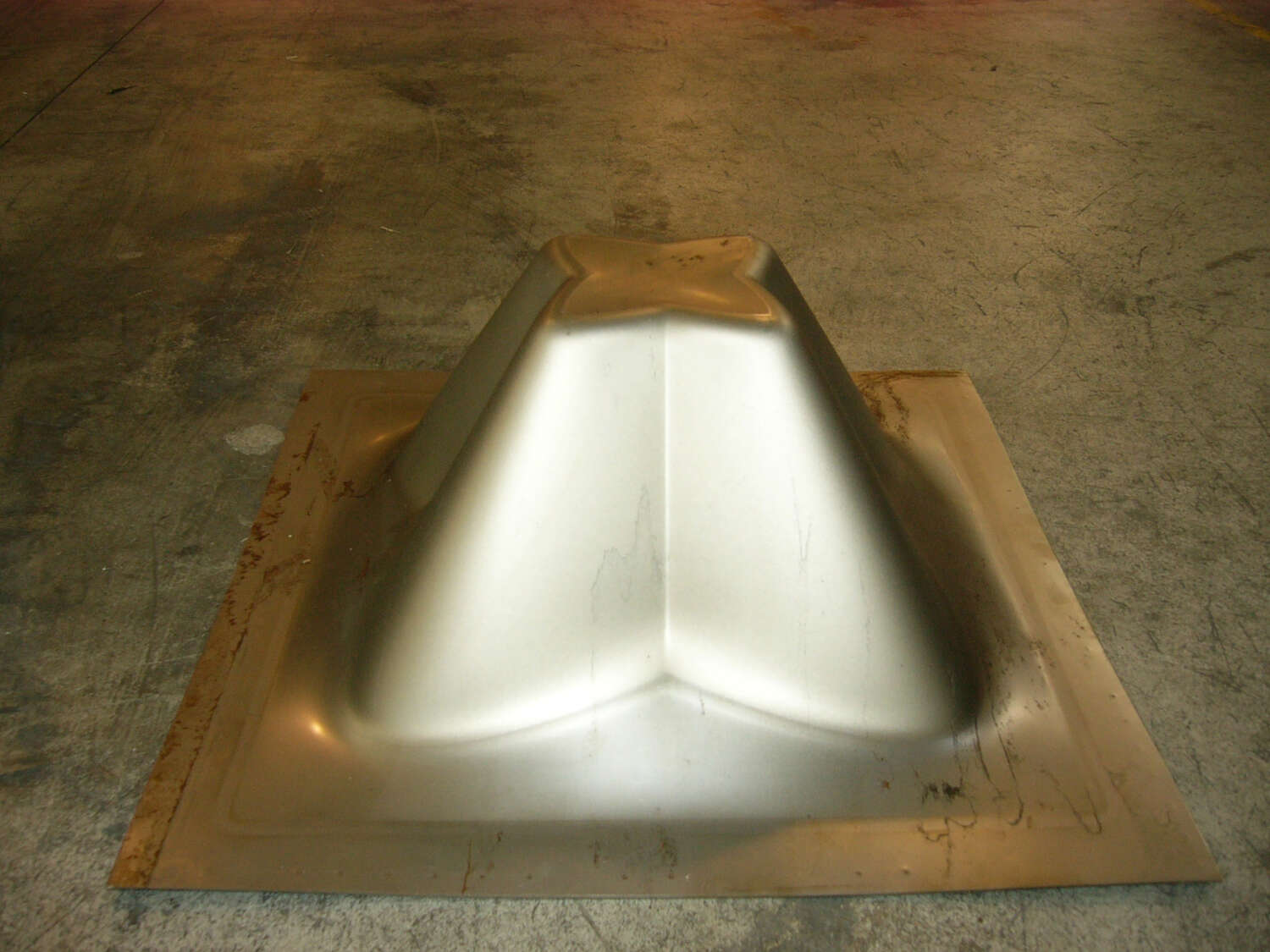
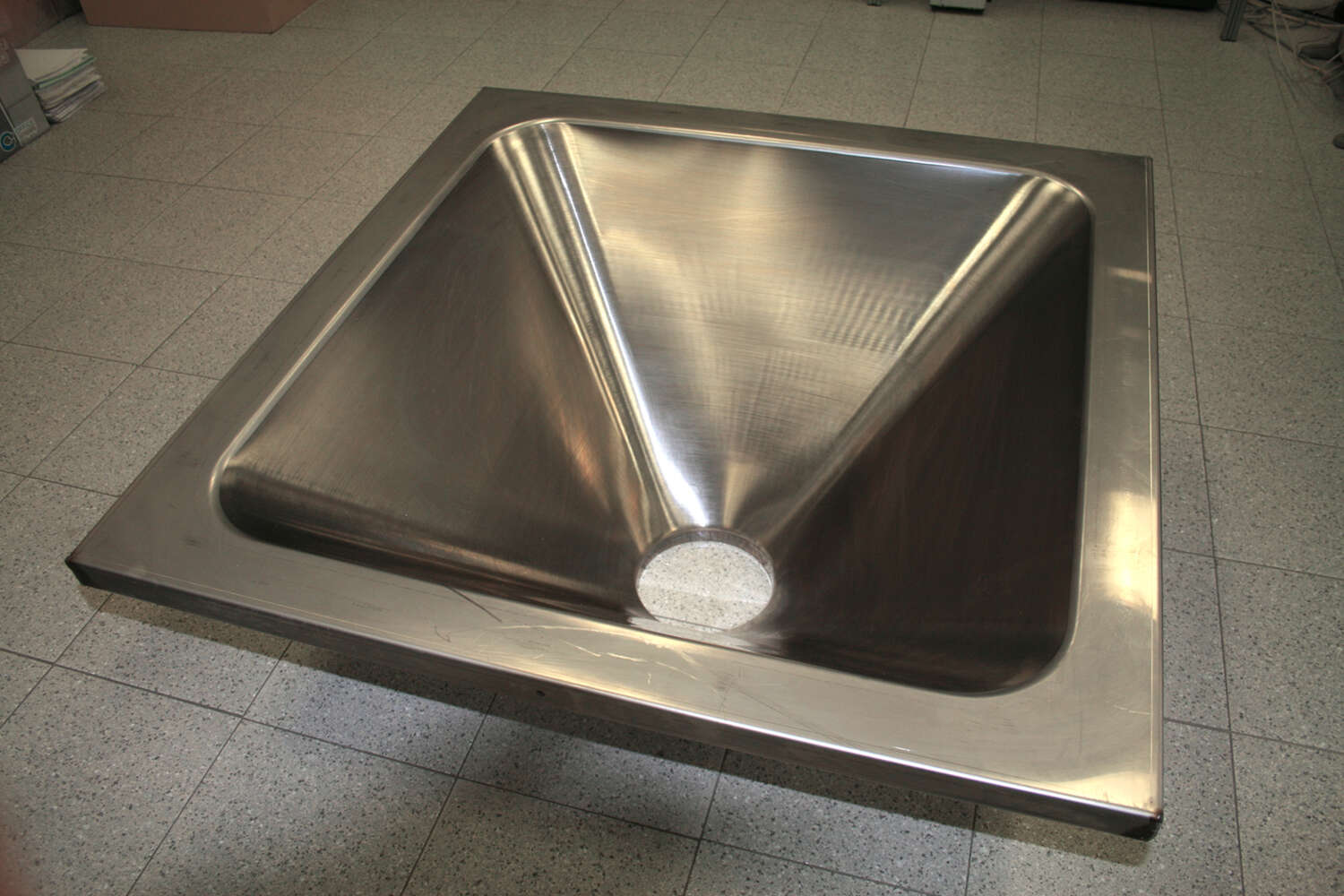
A causa del contatto localizzato dell’utensile con il pezzo in SPIF, le forze di formatura sono inferiori: distribuendo il lavoro di deformazione su più punti singoli, e in un arco di tempo maggiore, la potenza istantanea richiesta dal processo è minore. Altri svantaggi sono la riduzione della precisione geometrica dei prodotti, specialmente in punti con raggi ridotti e un significativo ritorno elastico del materiale; anche questi aspetti possono essere gestiti e compensati utilizzando utensili speciali e algoritmi appropriati che correggono il percorso. In generale, il raggio minimo dipende dalla forma dell’utensile, ed è comunque maggiore rispetto a quanto ottenibile con lo stampaggio. Per contro, le deformazioni limite sono maggiori rispetto ai processi convenzionali. È importante, come per altre lavorazioni come la tornitura in lastra o l’imbutitura, tenere conto dell’assottigliamento del materiale. Già con angoli di sformo di 30° lo spessore della parete è dimezzato. Con angoli inferiori a 20°-25° l’assottigliamento è ancora più importante e può portare alla rottura del materiale.