Come definire la lavorazione del titanio? Sfidante, viste le tante difficoltà da superare.
Titanio: ottimo rapporto resistenza/peso, elevate proprietà meccaniche alle alte temperature. Queste, ma non solo, le proprietà che rendono le leghe di titanio estremamente interessanti quando peso e caratteristiche sono fondamentali, con manufatti che possono (o devono) lavorare in condizioni estreme.
Alle interessanti proprietà si contrappongono esigenze di lavorazione complesse: rispetto ad altri materiali, come ghisa o acciaio inossidabile, le caratteristiche metallurgiche e le proprietà del titanio hanno una maggiore influenza sull’azione del taglio.
Questa è certamente una sfida, a cui si può rispondere solo con conoscenze applicative specifiche e utensili ottimizzati proprio per la lavorazione di questi materiali, così da rendere l’asportazione di truciolo performante ed efficiente.
Dalle premesse…
Parlare di titanio significa riferirsi alle sue leghe, perché sono queste che hanno un effettivo interesse a livello industriale:
• Leghe Alpha (α): caratterizzate da aggiunte di Al, O e/o N che stabilizzano la fase α
• Leghe Beta (β): caratterizzate da aggiunte di Mb, Fe, V, Cr e/o Mn che stabilizzano la fase β
• Leghe miste (α+β): in cui è presente una combinazione di entrambe le classi
Le α+β, caratterizzate da una resistenza medio-alta, sono attualmente le più utilizzate, e trovano largo impiego nella produzione di laminati, trafilati per produzione di telai, forgiati o getti per motori e parti di aerei.
La Ti6Al4V rimane la qualità più comune per uso generale, non solo per il settore aerospaziale ma anche negli altri settori, e viene considerata come lega di riferimento. Le leghe α sono quelle più facilmente lavorabili all’utensile, mentre le leghe β sono quelle più difficili da lavorare.
… alla sfida
Perché le leghe di titanio sono generalmente considerate (e a ragione) difficili da lavorare all’utensile? La risposta si trova nelle particolari caratteristiche meccaniche e chimiche:
• bassa conducibilità termica: il calore, che si genera durante il taglio, non viene dissipato velocemente e resta “nell’utensile”, concentrato sul tagliente e sul petto dell’utensile. Il rischio di scheggiatura del tagliente è molto alto;
• alta reattività chimica: causa dell’incollamento del truciolo sul tagliente, con conseguente comparsa di craterizzazione e prematura usura dell’utensile;
• basso modulo di elasticità: in genere interessante per il manufatto, ma fonte di problemi in lavorazione. L’elasticità del materiale, sotto la sollecitazione esercitata dall’utensile, tende ad “allontanare” il materiale dalla zona di taglio; nel caso di spessori sottili, che quindi possono subire deformazione (deflessione) possono nascere vibrazioni indesiderate, con conseguenti ricadute su qualità della lavorazione e durata dell’utensile.
Dunque la lavorabilità del titanio è giustamente rinomata per essere scarsa, con una finestra di lavorazione piccola, motivo per cui è necessaria un’attenta riflessione su più fattori, oltre che sull’utilizzo del semplice utensile.
Se l’obiettivo è garantire una lavorazione di successo, è indispensabile focalizzare l’attenzione su:
• pressione e volume del fluido da taglio;
• tecniche di programmazione;
• requisiti della macchina;
• utensili e relativi portautensili.
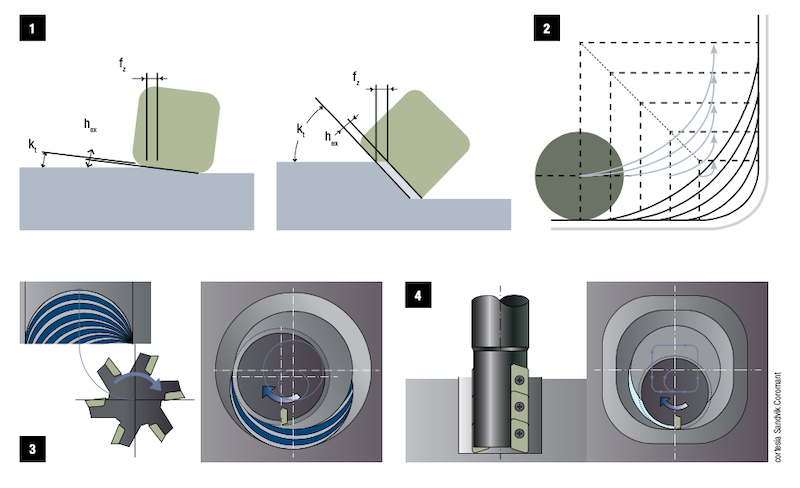
Il fluido da taglio
Per le leghe di titanio, la scarsa conducibilità termica rappresenta una delle principali sfide.
Buone prestazioni di taglio non possono quindi sottovalutare la questione “raffreddamento”, specie se si considera che, a pressioni elevate, o temperature superiori a 300°, reagendo con carbonio, ossigeno e azoto), il titanio inizia a prendere fuoco.
Questo rischio è ancor più elevato se la lubrorefrigerazione si interrompe, motivo per cui una best practice, è lubrificare sempre quando si lavora il titanio, in grandi quantità e, se possibile, ad alta pressione.
Infatti, l’utilizzo di fluido da taglio ad alta pressione raddoppia la durata degli utensili, rispetto a un impiego a pressione standard, evitando, fra l’altro, la rimacinazione dei trucioli che danneggia l’utensile, dato che l’alta pressione favorisce l’allontanamento.
La tipologia di lubrorefrigeranti per le lavorazioni di asportazione sulle leghe di titanio devono avere delle caratteristiche di elevata lubricità.
L’elevata lubricità, insieme al potere refrigerante fornito dalla massa del fluido nella zona di taglio, devono consentire la massima asportazione del calore di lavorazione, che si accumula sull’utensile, evitando così fenomeni di grippaggio e rottura.
Il tipo di lubricità necessaria è di tipo “polare”, cioè molto “bagnante”, che si “aggrappa” alle superfici metalliche pezzo/utensile e, in questo modo, si rende possibile la buona lavorazione di questo tipo di metallo.
La realizzazione di lubrorefrigeranti a elevata “polarità” è una sfida che racchiude un concetto di lubricità non convenzionale, basato su una grande affinità tra fluido e materiali coinvolti nelle zone di taglio.
Tutto ciò si dimostra molto efficace nelle operazioni di taglio delle leghe di titanio che, per loro natura, “rifiutano” l’azione lubrificante convenzionale.
Le tecniche di programmazione
Una programmazione ottimizzata può aumentare del 50% la produttività, in combinazione con una durata tagliente più lunga e una maggiore sicurezza del processo.
Ottimizzare completamente un programma richiede molto tempo, certamente di più rispetto all’usare gli esistenti cicli fissi dei sistemi CAM, ma, se l’obiettivo fosse realizzare soltanto un pezzo, il recupero dell’investimento avrebbe poco valore, ma quando i pezzi dovranno essere prodotti per molti anni, allora fare una programmazione corretta fin dalla prima volta permette di raggiungere un’elevata produttività.
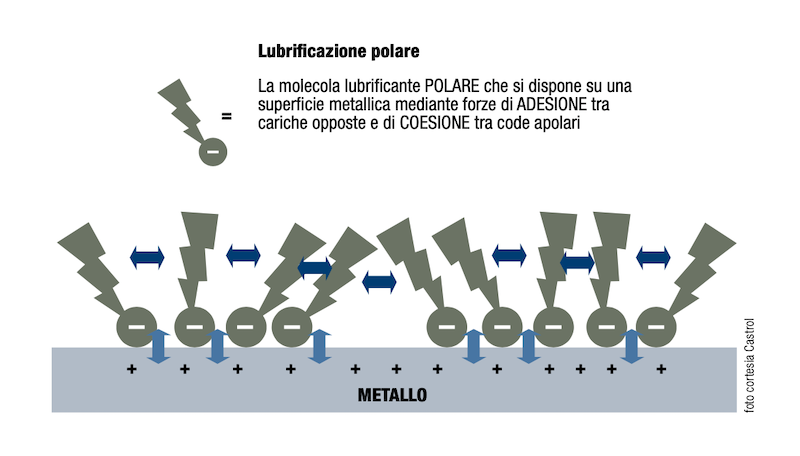
La macchina utensile
Il ruolo della macchina utensile è fondamentale e, in particolare quando si lavorano le leghe di titanio, l’influenza sulla produzione è altissima. L’ampia combinazione fra velocità di rotazione, potenza e coppia devono garantire il risultato in ogni tipo di applicazione.
E’ fondamentale che venga assicurata un’adeguata rigidità di tutto il sistema, macchina utensile, mandrino, portamandrino e utensile, andando a compensare l’elasticità del materiale, evitando al massimo l’instaurarsi di vibrazioni.
In linea generale possono essere delineate alcune raccomandazioni:
• Potenza e coppia. Per una sgrossatura efficace a basse velocità di taglio: potenza 30 kW, coppia 1000 Nm a 350 giri/min.
• Velocità di rotazione del mandrino. Per la finitura con utensili di piccolo diametro è consigliata una velocità di 6000giri/min.
• Interfaccia stabile. Per garantire rigidità alla flessione e alla pressione di bloccaggio, con particolare attenzione nel caso di frese a candela con tagliente lungo.
• Buona dinamica della macchina. Per gestire rapidi cambiamenti di direzione nei raccordi delle tasche, oltre ad elevati avanzamenti tavola, specie in finitura dove sono richieste sia flessibilità che velocità.
Gli utensili
La scelta degli utensili è un gioco di compromessi per raggiungere il giusto equilibrio fra angolo di approccio, numero di denti e velocità di asportazione truciolo.
In linea di massima, le frese con inserti rotondi garantiscono la migliore produttività e durata tagliente, grazie all’angolo di attacco e all’effetto di assottigliamento del truciolo, spiraliforme e più facilmente evacuabile.
Le frese a elevati avanzamenti sono largamente impiegate su macchine di piccole dimensioni per un’azione di taglio veloce e leggera. La piccola profondità di passata, ma fino a 1 mm di avanzamento per dente, costituisce un buon ritmo di asportazione truciolo.
Le frese a candela con tagliente lungo, in genere con geometria appositamente studiata per la lavorazione del titanio, garantiscono una buona asportazione: il posizionamento degli inserti può vantaggiosamente essere ottenuto nella parte inferiore, in modo da prevenire lo spostamento e consentire elevati volumi di truciolo asportato con elevata sicurezza.
La fresatura a tuffo è un metodo alternativo quando la lavorazione laterale non è possibile a causa della tendenza alle vibrazioni. In questo processo il taglio viene eseguito all’estremità dell’utensile anziché in periferia, con una vantaggiosa trasformazione delle forze da radiali ad assiali.
E’ consigliata una ragionevole larghezza di taglio. Come indicazione generale, taglienti positivi consentono al truciolo di scorrere più velocemente sul petto, limitando quindi l’effetto di incrudimento.
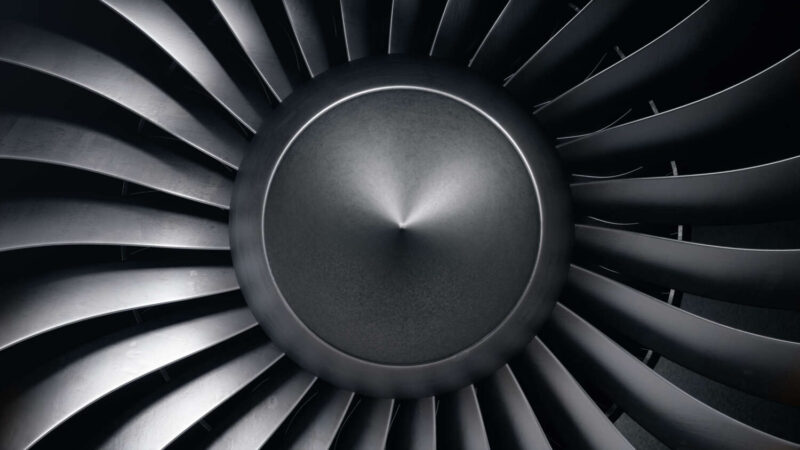
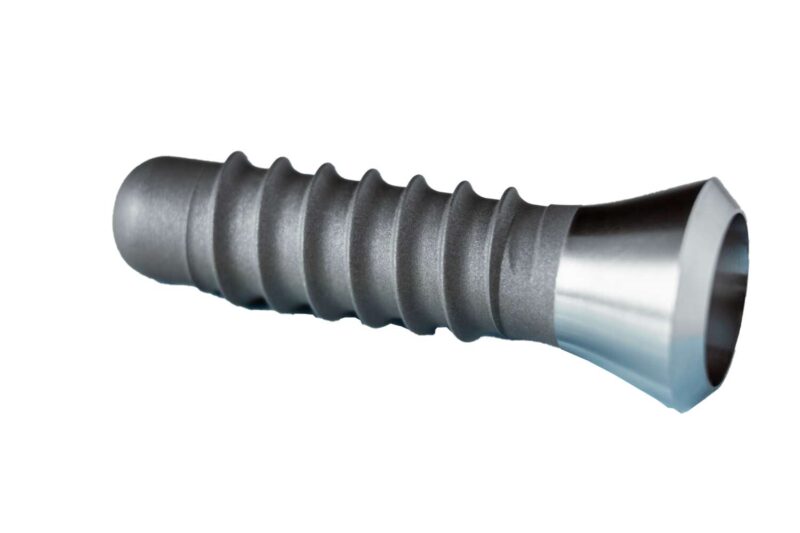
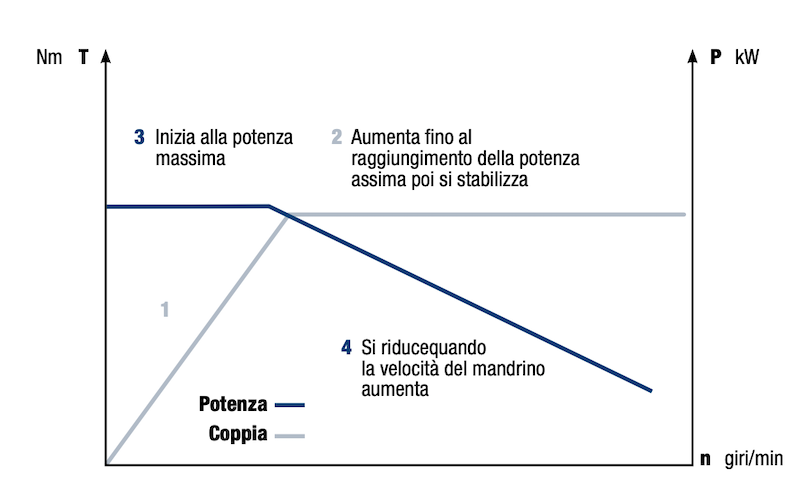
Anche il fluido da taglio va… omologato
Quando si parla delle leghe di titanio si pensa subito a un settore merceologico ben definito. Come l’aerospace, dove il fluido da taglio ha un ruolo centrale e strategico.
Per quale motivo? Perché lavorare una lega esotica destinata a questo delicato comparto presuppone che anche il lubrorefrigerante venga testato e omologato per tale utilizzo.
Infatti i test vengono svolti da enti di riferimento internazionali, certificati, che sottopongono il fluido a un iter di prove mirate a verificarne la completa compatibilità con i materiali ritenuti standard aeronautici, quali le leghe di titanio.
La certificazione viene dichiarata mediante un numero di protocollo, accessibile come banca dati alle aziende del settore, che, di conseguenza, possono inserire il lubrorefrigerante prescelto e certificato nel proprio ciclo produttivo, con garanzia di completa compatibilità con le leghe aeronautiche.
Questa attività è basilare per la sicurezza del processo di produzione, che deve garantire pezzi prodotti in completa assenza di fenomeni ossidativi, seppur minimi, conformemente a quanto richiesto e preteso dall’aerospace.
La lubricità polare
La realizzazione di refrigeranti a elevata “polarità” è stata una sfida che Castrol ha intuito sin da subito nel mondo delle operazioni metalworking proprio perché offre il vantaggio di avvolgere completamente, in modo “magnetico”, le superfici metalliche in contatto, garantendo così un regime di lubrificazione resistente alle sollecitazioni termiche e fisiche presenti nella zona di taglio.
Si viene a formare un cuscinetto antiattrito di notevole capacità lubrificante che consente tangibili vantaggi sulla durata degli utensili, oltre che sull’aspetto e qualità dei particolari prodotti.
E’ un concetto di base che Castrol ha sviluppato pionieristicamente nel settore delle lavorazioni dei materiali “esotici” e che, visti i riscontri, si è esteso sia per i lubrorefrigeranti integrali sia per quelli solubili.