Si aprono nuovi scenari per il manifatturiero del terzo millennio: gli utensili intelligenti spingeranno la produzione industriale verso il futuro.
Da circa 50 anni la ricerca mondiale si sta sforzando di sviluppare dei sistemi affidabili per il monitoraggio delle lavorazioni meccaniche. La ragione di questo importante sforzo risiede nell’enorme potenziale di queste tecnologie per aumentare la disponibilità dei sistemi di produzione, specie se sofisticati e costosi. Tali tecnologie possono concorrere a migliorare la qualità dei prodotti e generare informazioni avanzate sulle condizioni di lavorazione, al fine di controllarle e ottimizzarle. Queste necessità sono divenute, in anni recenti, ancora più stringenti a causa delle mutazioni in atto nel sistema manifatturiero:
• lavorazione di materiali via via più duri e difficili (acciaio per utensili, carburi metallici, superleghe, compositi…) a partire da semilavorati con soprametalli ridotti;
• lavorazioni ad alta velocità, necessarie per compensare il maggiore costo orario dei sistemi di lavorazione;
• aumento degli standard qualitativi e della precisione;
• migliore pulizia e sostenibilità delle lavorazioni: minori emissioni e scarti.
In questi anni di ricerca e sviluppo industriale sono state moltissime le tipologie di soluzioni sensoriali implementate, con sistemi che sono ormai divenuti degli standard industriali.
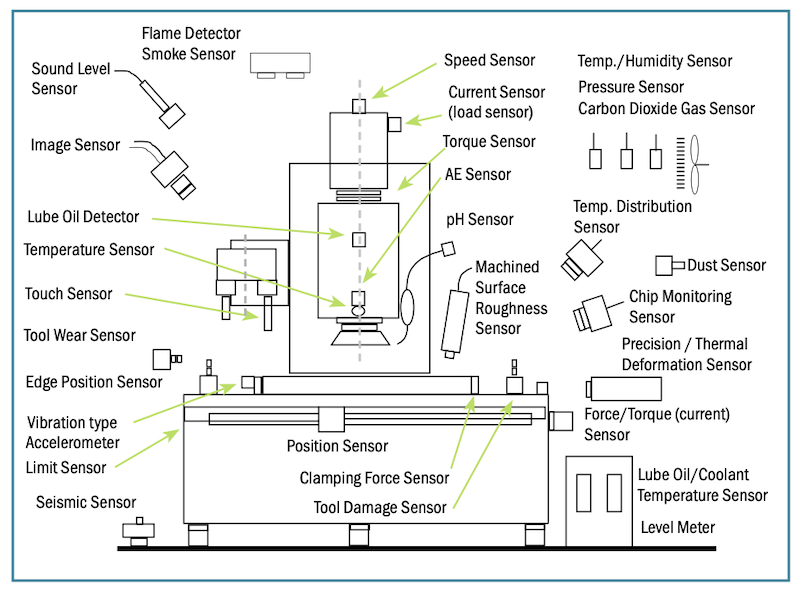
Monitoraggio e finalità
L’implementazione di sistemi di monitoraggio è un aspetto che riguarda sia il costruttore dell’impianto che l’utente finale, anche se con finalità diverse. Il costruttore ha una visione volta a proteggere la macchina da un uso improprio e da eventi inattesi, per migliorare il servizio post vendita. Questo ultimo aspetto è stato largamente promosso dalle recenti agevolazioni fiscali contenute nel Piano Nazionale Industria 4.0. L’utente finale ha invece la necessità di garantire continuità e qualità alla produzione e pertanto vuole sistemi affidabili, che identifichino prontamente e impediscano danneggiamenti alla macchina e al pezzo in situazioni critiche. Unitamente a questo, tali sistemi devono avere il minimo impatto possibile sull’operatività e sulla manutenzione. Gli studi compiuti negli anni ‘90 in merito ai sistemi di monitoraggio in uso nel settore automotive hanno messo in luce che l’affidabilità dei sistemi fino ad allora implementati a bordo delle macchine utensili era genericamente limitata e che molto era lasciato all’iniziativa dell’operatore. La limitata formazione degli operatori all’uso di tali sistemi – per lo più concepiti come prototipi da laboratorio che presentavano interfacce utente complesse – fu una delle principali cause di fallimento. In tempi recenti, però, grazie allo sviluppo di tecnologie elettroniche portatili, molti dispositivi informatici – una volta appannaggio di soli operatori esperti – sono divenuti oggetti di uso quotidiano semplici ed ergonomici, e quindi accessibili a tutti. L’enorme potenza di calcolo unita a un basso consumo energetico e alla connettività consentono funzioni complesse che conferiscono al sistema una propria “intelligenza”. Tale principio oggigiorno inizia a essere applicato anche ai sistemi di supervisione delle lavorazioni meccaniche.