Non è un paradosso: grazie a questa nuova tecnologia è possibile realizzare oggetti in lamiera robusti e leggerissimi
La formatura della lamiera ha sempre richiesto tecniche imponenti da molti punti di vista: pressioni elevatissime, stampi complessi, macchinari pesanti e di dimensioni ciclopiche. Tutti questi fattori comportano costi elevati sia dal punto di vista degli impianti che della produzione. Complessità e requisiti tecnologici emergono in maniera ancora più rilevante nel caso delle tecniche più evolute, come la deformazione superplastica ad alta temperatura, oppure l’idroformatura. Non a caso, questi processi sono usati soprattutto in campo automobilistico ed aeronautico. Da alcuni anni un nuovo processo si è aggiunto al panorama della deformazione plastica dei metalli. Si tratta della FIDU, dal tedesco Frei Innen Druck Umformung ovvero deformazione libera tramite pressione interna. Si tratta di un procedimento che rende possibile la trasformazione della lamiera da lamina bidimensionale a prodotto tridimensionale. Come l’idroformatura, anche la FIDU sfrutta una pressione interna per “gonfiare” la lamiera, in modo simile a quanto fa un mastro vetraio con la massa fusa. Le analogie tra i due processi però si fermano qui: mentre l’idroformatura necessita di altissime pressioni e stampi complessi, per la FIDU sono sufficienti pressioni di pochi bar, ovvero 2-3 ordini di grandezza inferiori. Inoltre, grazie allo studio di spessori e sagome delle lamiere tagliate, durante il gonfiaggio il prodotto si deforma e va ad assumere la forma desiderata senza bisogno di stampi.
Principali vantaggi
Il principale vantaggio di questa tecnologia è che la produzione è molto veloce e facile. Si inizia ricavando due o più elementi piatti tagliati a laser, che poi vengono saldati lungo i bordi o in altri punti predefiniti. Anche la saldatura è effettuata al laser per garantire precisione e uniformità nella giuntura. La lamiera utilizzata è principalmente alluminio, acciaio, o acciaio inossidabile con spessori che vanno da 0,5 e 2 mm. Le lamiere possono anche essere di spessori diversi, per ottenere forme asimmetriche o dare maggiore rigidità e resistenza a determinate parti del prodotto.
Tramite una valvola viene insufflata aria compressa o altro gas, con una pressione compresa tra 50 kPa (0,5 bar) e 5 MPa (50 bar). Il valore dipende dal materiale, dallo spessore, e dalla geometria del pezzo da realizzare. Grazie a valori così bassi, la sagomatura può essere realizzata persino con una semplice pompa da bicicletta o un comune compressore da officina. A differenza dei metodi tradizionali di formatura, la FIDU non richiede stampi o matrici per sagomare il pezzo, e quindi può essere fatta direttamente in cantiere, in ufficio, o addirittura in casa.
Invece dell’aria è anche possibile usare acqua o emulsioni di acqua e olio, che permettono di controllare maggiormente la deformazione essendo fluidi incomprimibili. Tuttavia, rimuovere il liquido dalla cavità interna può essere complesso. Si possono sfruttare anche dei reagenti chimici che, a seguito di un’attivazione esterna, sviluppano dei gas che vanno a gonfiare il pezzo. Ne è un esempio Hot Pin, un appendiabiti da parete. Inizialmente si presenta come un disco piatto di lamiera, ma dopo un passaggio in forno a 200 °C “lievita” e si trasforma in un piccolo cuscino tondeggiante, già predisposto per il fissaggio.
Sperimentazione continua
Lo studio Zieta Prozessdesign sta sperimentando anche l’uso di sostanze schiumogene che poi solidificano contribuendo a migliorare la rigidità e la resistenza agli urti.
Se la parte produttiva è tutto sommato semplice e tradizionale, lo stesso non può dirsi della progettazione. Arrivare alla sagoma corretta dei pezzi tagliati richiede un attento studio, che tenga conto del comportamento della lamiera, delle saldature e della geometria. Tutti questi fattori si sommano e si influenzano in maniera non lineare durante il gonfiaggio.
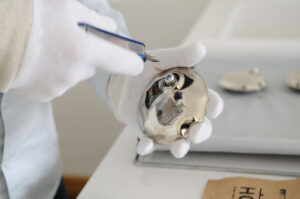
Lo studio richiesto è comunque un piccolo prezzo da pagare considerando gli ottimi risultati ottenuti. Ad esempio lo sgabello Plopp, vincitore di molti premi di design, pesa pochi kg ma è in grado di reggere un peso superiore a 2 tonnellate. Per aumentare la rigidità del pezzo è possibile inserire all’interno degli elementi di vincolo e di collegamento come cavi, piastre, e barre di rinforzo. Questi elementi possono anche essere previsti per “guidare” la deformazione durante il gonfiaggio. Un’altra applicazione è quella di realizzare facilmente serbatoi e cisterne di grandi dimensioni, con già all’interno delle paratie antioscillazione per ridurre il fenomeno dello “sloshing”.
Non solo applicazioni domestiche
La formatura FIDU può essere applicata anche a componenti di medie e grandi dimensioni per architettura e ingegneria. Lo studio Zieta ha studiato un nuovo modello di pala eolica leggera, economica, e completamente riciclabile. Secondo l’ing. Dohmen, le pale di una turbina di piccola potenza sono comunemente realizzate in fibra di vetro o di carbonio. Ogni pala, lunga circa 2 metri, costa circa 600 €. Il prezzo dello stesso elemento realizzato con tecnologia FIDU costa solamente 25 € e ha una durata maggiore: potrebbe quindi contribuire ad aumentare la diffusione e la competitività delle energie rinnovabili.
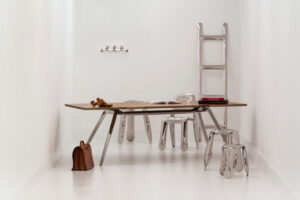
Le caratteristiche di leggerezza, espandibilità, basso costo e leggerezza rendono il metodo FIDU un potenziale candidato anche per la realizzazione di strutture orbitali o per la costruzione di moduli abitativi lunari o su altri pianeti. Per vedere queste applicazioni, tuttavia, dovremmo attendere ancora qualche decennio.
Un altro vantaggio economico ed ecologico della deformazione per pressione interna è il volume ridottissimo degli elementi prima del gonfiaggio. I pezzi sono sostanzialmente bidimensionali: possono essere trasportati facilmente riducendo i costi di spedizione e l’impatto ambientale. Questo aspetto è particolarmente utile anche nel caso di installazione di oggetti di grandi dimensioni all’interno di strutture esistenti. È molto più facile far entrare un elemento piatto e flessibile all’interno dell’edificio e poi espanderlo in opera, piuttosto che dover creare aperture ad hoc o assemblare componenti separati. Inoltre il gonfiaggio è un’operazione facile e pulita, che non richiede manodopera specializzata, saldature, o finiture. Non produce sporcizia né fumi, non inquina, non fa rumore e non richiede di attendere tempi tecnici per la solidificazione o l’incollaggio.
Come tutte le tecnologie, anche la FIDU non è una panacea o una bacchetta magica in grado di risolvere tutti i problemi della deformazione della lamiera. La formatura per pressione interna ha come principale svantaggio una bassa precisione e ripetibilità: le caratteristiche intrinseche della lamiera e le variabili introdotte dal taglio e dalla saldatura non permettono di prevedere o controllare in maniera assoluta la forma e le dimensioni finali. Nel caso di oggetti artistici o decorativi questo fattore di imprevedibilità può essere comunque considerato un aspetto positivo, che rende ogni prodotto un pezzo unico e irripetibile.
Marco Basso