In generale la lavorazione delle superfici piane non presenta grosse difficoltà, ma i problemi crescono in maniera esponenziale mano a mano che sono richieste maggiori qualità.
Esistono molte parti meccaniche che hanno due facce parallele e non poche di esse devono rispondere a stringenti requisiti di qualità, in particolare con strette tolleranze di planarità, parallelismo e spessore e con rugosità superficiale estremamente ridotta, per esempio con Ra < 0,1 µm. Le difficoltà aumentano se si devono eseguire pezzi con spessore molto piccolo, come per esempio meno di 1 mm. Se si devono produrre piccole e medie serie sarebbe comunque necessaria una macchina speciale dedicata che non potrebbe essere saturata e quindi non ammortizzabile in breve tempo. La soluzione a questi problemi è quella di avvalersi di strutture adeguatamente attrezzate che offrano un servizio per conto terzi.
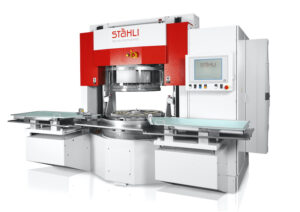
Il connubbio Stähli-FGS
La casa svizzera Stähli, che costruisce macchine specializzate per la superfinitura e la lappatura di superfici piane, offre già da tempo un servizio per conto terzi con centri nei pressi di Stoccarda, Detroit e Shanghai, con complessive 40 macchine dedicate. Ispirandosi a queste iniziative è nata l’italiana FGS (Fine Grinding Service) con sede a Bologna. Questa nuova realtà si è dotata di una macchina Stähli DLM710 dedicata alla rettifica fine (o microrettifica) e altre due lappatrici che operano in supporto all’unità.
La FGS propone un servizio ad aziende che richiedono pezzi di estrema precisione. La scelta va dalla pura lavorazione conto terzi alla definizione dei processi per i clienti che hanno già macchine simili e/o al supporto ai clienti che sono in attesa di ricevere una nuova macchina e devono comunque iniziare a produrre. I campi di applicazione sono i più vari e vanno dalle più banali rondelle per il common rail agli anelli dei cuscinetti e ai corpi e le lame per le pompe a palette, dagli inserti in metallo duro alle tenute in ceramica o in grafite, fino agli ingranaggi di precisione.
La DLM710 lavora con la tecnologia a doppio piatto, tecnica che è stata usata finora solo da importanti aziende con produzioni di grandi serie. FGS vuole rendere questa tecnologia fruibile ad un considerevole numero di imprese che non possono giustificare l’investimento e la gestione di macchine nate per l’alta produttività.
Il “fine grinding” è un’operazione di alta precisione, nota anche come micro rettifica, tramite la quale si ottengono particolari con planarità e parallelismo dell’ordine di grandezza del micron o di decimali del micron. Al tempo stesso le finiture ottenibili sono quelle tipiche della lappatura.
I moderni processi di asportazione con tale tecnica utilizzano macchine evolute a piatto singolo o a doppio piatto rivestiti da pellet o segmenti in super abrasivi, cioè diamante o CBN. Questi vengono incollati su dischi in ghisa o alluminio secondo schemi che generano un riempimento della corona utile in una percentuale che garantisca una copertura sufficiente al sostentamento dei pezzi senza impuntamenti, e ad assicurare la massima taglienza possibile. I leganti utilizzati sono del tipo vetrificati o resinoidi, raramente metallici. L’asportazione del sovrametallo è controllata dalla pressione esercitata dal piatto superiore: un fattore importante da tenere in considerazione per la verifica preliminare di quanti pezzi per carica possano essere “rettificati” è il massimo carico per cm2 ammissibile dalla struttura della macchina in uso.
Per quanto riguarda la forma dei segmenti si può dire che quella trapezoidale garantisce il massimo grado di ricoprimento, utile per pezzi molto piccoli. La forma quadrata è la più
economica, mentre i tasselli esagonali sono i più diffusi ed efficienti. I segmenti tondi permettono l’uso di sezioni diverse. Oltre alle forme semplici sono possibili, ove conveniente, anche combinazioni delle stesse. Ad esempio, nei casi in cui sia necessario rinforzare il bordo esterno di un piatto, si ricorre a speciali segmenti rettangolari o a pellet a doppio esagono dalla caratteristica forma a otto.
La disposizione dei pellet su ciascun disco avviene secondo schemi che vengono definiti in
matematica come tassellazione o pavimentazione. Quindi non solo forma e dimensioni di ciascun tassello sono importanti, ma anche la loro distribuzione nella corona utile.
Un elemento che ha una funzionalità fondamentale è la distanza tra i pellet, chiamata in gergo “gap”. La sua funzione è quella di realizzare un canale di drenaggio del fluido lubrorefrigerante (sempre che non sia invece necessario stuccare tutte le fessure), ma svolge anche la funzione di fare in modo che i bordi del tassello agiscano come taglienti essi stessi. Il gap in sostanza condiziona la superficie reale di abrasivo, e questo influisce anche sulla azione tagliente della mola. Variando il gap si può rendere la mola più dura o più tenera lasciando invariati tutti gli altri parametri.
Sebbene l’asportazione sia relativamente lenta (comunque proporzionata alla finitura superficiale ed alla precisione geometrica richiesta), il processo è estremamente efficiente: infatti ogni carica consiste di numerosi particolari inseriti in appositi dischi satelliti dentati che vengono posti simultaneamente in rotazione dall’ingranamento con un anello interno. Essi vengono fatti rotolare su una corona esterna fissa che deve poter scorrere verso il basso per consentire il carico scarico. Le mole sono poste simultaneamente in rotazione da motori separati ed indipendenti. Le velocità ed il senso di rotazione relativo può essere regolato singolarmente ed in maniera autonoma. Assieme alla pressione esercitata, la velocità di rotazione relativa dei piatti e dei satelliti influenza le caratteristiche del ciclo e quindi i risultati ottenuti. Nel moto combinato i pezzi descrivono quindi traiettorie epicicloidali o ipocicloidali per cui la velocità di ciascun pezzo, nel moto roto-traslatorio, cambia continuamente in direzione ed intensità.
Talvolta si sottovalutano aspetti che sembrano secondari ma che, se opportunamente controllati, sono determinanti per il successo di una operazione. Nel fine grinding si utilizza olio intero (oppure acqua deionizzata per la ceramica), la cui adduzione avviene tramite una serie di fori passanti ricavati attraverso il piatto superiore – sia nel disco di supporto che nella corona di abrasivo. Il compito svolto dal fluido è quello di garantire la rimozione del calore che si sviluppa nell’area di taglio e contemporaneamente quella di mantenere pulita l’area di lavoro. Per assolvere ad entrambe queste funzioni il circuito idraulico deve avere una portata sufficiente ed il lubrorefrigerante una temperatura controllata. Il primo aspetto ha due conseguenze: la prima è che un eccesso di olio potrebbe produrre l’effetto “acquaplaning” e la seconda, nel caso contrario, cioè una scarsa quantità, potrebbe causare un consumo quantomeno prematuro dei piatti.
Il drenaggio avviene per forza centrifuga e la successiva filtrazione deve essere adeguatamente accurata affinché le impurità non diventino agenti inquinanti impropri tali da compromettere la rugosità superficiale.
Anche la ravvivatura dei piatti riveste una importanza cruciale nella resa degli utensili e nella performance del ciclo. Essa condiziona il rendimento delle mole perchè permette una pulizia ottimale della superficie abrasiva e quindi di esporre nuovi taglienti acuminati quando necessario.
Infine un cenno alla preparazione dei pezzi, che devono essere preliminarmente selezionati entro gamme comparabili in maniera stretta, cioè comprese in un range di dimensioni limitato. Questo restringe il sovrametallo a quello effettivamente da asportare e riduce i tempi di lavorazione. Nell’economia del processo incidono i tempi improduttivi della ravvivatura e, se la perdita di geometria nasce da una gestione poco accurata dei pezzi, i costi aumentano anche per il conseguente spreco di abrasivo prezioso.
I dischi satelliti (Figura 4) hanno lo scopo di posizionare correttamente i pezzi sul piatto inferiore e di trascinarli in rotazione. Hanno quindi degli alloggiamenti in cui possono essere collocati i pezzi.
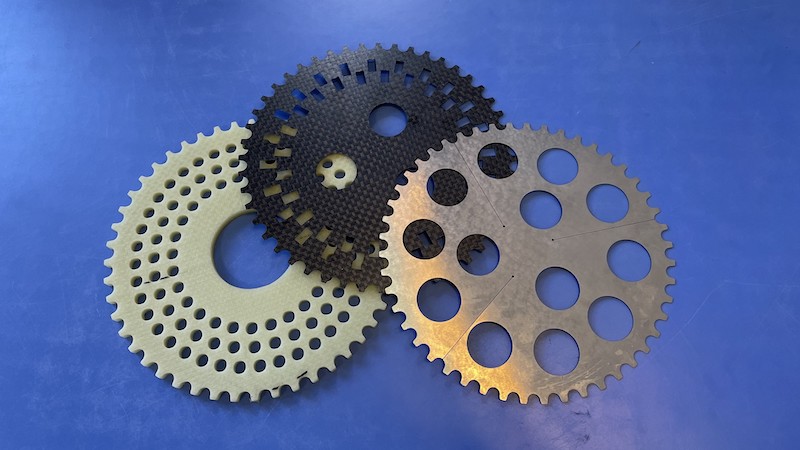
Naturalmente devono avere uno spessore inferiore a quello dei pezzi da lavorare e, poichè molte volte devono essere rettificati pezzi molto sottili, i dischi non devono deformarsi sotto sforzo o per effetto del calore sviluppato durante la lavorazione.
Il materiale usato per la loro costruzione può essere Vetronite, bachelite, CFK o titanio.
Sono stati realizzati dischi satelliti con spessore 0,3 mm in CFK per lavorare pezzi di spessore 0,4 – 0,5 mm.
La rugosità superficiale dipende naturalmente sia dalla granulometria dell’abrasivo che dalle condizioni di lavoro, ma per componenti di orologi Rolex si sono ottenute rugosità di appena Ra = 0,07 µm.
I super abrasivi come il diamante e il CBN (nitruro cubico di boro) sono i materiali ideali per questa specifica applicazione. Le loro caratteristiche li rendono congeniali grazie alle ridotte forze di taglio che sviluppano, alla conseguente elevata capacità di asportazione, al contestuale ridotto tasso di usura. In termini di tecnologia applicata, le loro affinità con questo particolare processo generano un’assoluta affidabilità e ripetibilità, un’accuratezza e precisione dimensionale costante e una drastica riduzione dei tempi passivi.
Nella Tabella 1 sono riportate le granulometrie relative a CBN e diamante adatte alle specifiche operazioni.
Nella Figura 5 si riporta il diagramma che mette in relazione la rugosità Ra con la granulometria dei super abrasivi CBN e diamante.
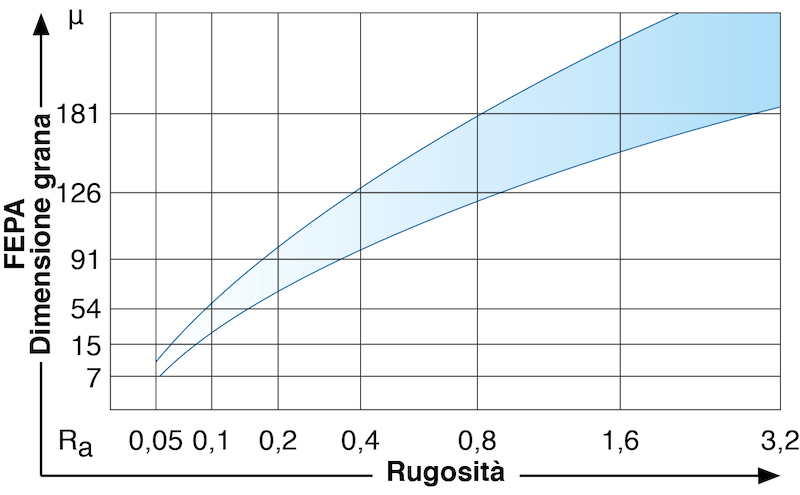
Come si può notare per ogni dimensione del grano viene indicata una Ra entro un certo range e questo perché la rugosità oltre che dipendere dalla granulometria è fortemente influenzata dal materiale lavorato, dalle condizioni di lavoro, dal lubrorefrigerante utilizzato, dallo stato di usura della mola e altro.
di Gianfranco Bianco