La Zanelli progetta e realizza miscelatori/turbodispersori, mescolatori/dispersori, impastatrici orizzontali ed estrusori. Macchine e impianti apprezzati e riconosciuti in Italia e nel mondo per le loro prestazioni, la qualità di processo e l’affidabilità. I telai, le carterature e svariati componenti vengono oggi lavorati con una nuova pressa piegatrice Ermaksan, fornita e installata da Co.Ma.F.
Automotive, edilizia, tessile, aerospaziale, cosmetica, elettronica, chimica, materie plastiche, grassi industriali. Sono questi solo alcuni dei principali settori dove trovano applicazione le macchine e gli impianti progettati e realizzati dalla Zanelli di Collecchio (PR), tecnologie in grado di processare tutto ciò che sia miscelabile: dai liquidi ai mix di liquidi e polveri, dalle paste ai sigillanti, caratterizzati soprattutto da gradi di viscosità medio-alte.
Parliamo di turbodispersori, di mescolatori/dispersori, a cui si aggiungono anche impastatrici orizzontali ed estrusori, apprezzati in tutto il mondo per le loro elevate prestazioni, la qualità di processo e la grande affidabilità nel tempo che sono in grado di assicurare. «Macchine – spiega l’ing. Alberto Zanelli, direttore tecnico-operativo, nonché seconda generazione alla guida dell’azienda, insieme al fratello Alessandro direttore commerciale e alla sorella Simona, direttore amministrativo – con potenze fino a 250 kW su singolo albero, con capacità vasca che possono raggiungere i 15.000 litri, e che nell’ultimo triennio sono state oggetto di un ancora più accurato focus per quanto concerne la loro ingegnerizzazione e la loro personalizzazione, al fine di elevarle verso un’eccellenza ancora più marcata e differenziante».
Un nuovo e sfidante obiettivo che ha richiesto, proprio per garantire livelli di qualità ancora più stringenti, nuovi investimenti necessari per rinnovare il parco macchine, sia nel reparto di asportazione truciolo, sia nel reparto di carpenteria. Ed è proprio nel reparto di carpenteria che è stata fornita e installata nella primavera dello scorso anno da Co.Ma.F. di Sovico (MB) una nuova pressa piegatrice Ermaksan serie Power-Bend Falcon.
Processi sempre più 4.0
«Sin dall’inizio dell’attività – afferma l’ing. Zanelli – la scelta dell’azienda è stata quella di produrre tutto al nostro interno, in Italia, per avere un controllo totale della filiera: partendo dal foglio di lamiera, arrivando fino alla parte software d’uso della macchina. Una gestione resasi necessaria non solo per la specialità che caratterizza le nostre tecnologie, ma anche perché abbiamo sempre voluto mantenerci detentori del know-how e del processo, per poter dettare al meglio i tempi operativi in base alle esigenze del mercato. Una vision che ha permesso nel tempo di minimizzare il time-to-market e di migliorare in modo significativo tutte le attività di service e di manutenzione correlate, rendendo agevole qualunque tipo d’intervento».
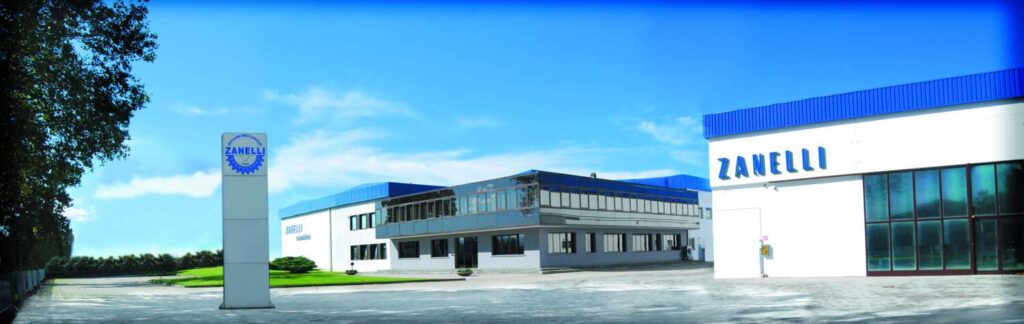
In quest’ottica, l’integrazione della nuova pressa piegatrice si inserisce in una gestione fortemente evoluta del ciclo di sviluppo di prodotto. Tant’è che risale ormai all’inizio degli anni 90 l’introduzione del primo software gestionale in Zanelli, con tracciabilità totale delle varie fasi di produzione.
«In assenza di una produzione seriale di alti volumi – rileva l’ing. Zanelli – sapere instante per istante lo stato d’avanzamento di ogni commessa, è stato per noi un elemento determinante per poter garantire al tempo stesso la massima qualità e la massima competitività. In sintesi, la nostra scelta è stata quella di puntare più sull’ottimizzazione di processo e delle varie lavorazioni, che sulla produttività intesa in senso stretto. L’avvento di Industria 4.0, della possibilità di raccolta dai vari macchinari nei reparti dei più svariati big data, grazie alla business intelligence, ha permesso e permette costantemente di individuare rapidamente criticità di flusso, e di adottare i necessari correttivi. Raccolta dati che oggi coinvolge anche la nuova presso piegatrice Ermaksan, appositamente richiesta completa di data logger, proprio per poter essere anch’essa oggetto di analisi. Un monitoraggio preciso, tracciabile, per rendere pro-attiva anche la fase di piegatura dei manufatti, e cercare di migliorare con un’impronta più manageriale e industriale i tempi di fermo, i tempi di attrezzaggio, i reali tempi di piega, in base alla priorità delle commesse».
L’acquisto della nuova Ermaksan è servito dunque per introdurre in Zanelli un nuovo modo di gestire questa fase di lavorazione, prima gestita interamente in manuale, mentre oggi con approccio sempre più orientato ai canoni di Industria 4.0.
«Oggi – conferma l’ing. Zanelli – partiamo da un modello solido in 3D, per poi sviluppare la lamiera grazie al simulatore software di cui ci siamo dotati, per poi inviare il tutto a bordo macchina, con le sequenze di piega per l’operatore, con assoluta garanzia della ripetibilità».
Prestazioni e precisione di piega, dalla singola semplice alle multiple complicate
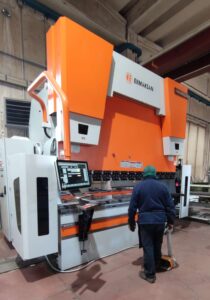
Come già sottolineato, la nuova macchina fornita e installata da Co.Ma.F. è una pressa piegatrice idraulica sincronizzata Ermaksan Power-Bend Falcon a 4 assi da 400 ton, per 3.100 mm di massima lunghezza di piega. Riprogettata dal costruttore turco sulla base delle preferenze e dei feedback raccolti dai propri clienti per caratteristiche elettroniche e meccaniche, partendo dal modello base Power-Bend, questa nuova serie riesce perfettamente a soddisfare esigenze di processo per la singola e accurata piega piuttosto che pieghe multiple complicate. Con distanza tra i montanti che raggiunge i 2.550 mm, il modello di pressa scelta da Zanelli si distingue per la corsa del registro pesante asse X e asse R, rispettivamente di 1.000 mm e 500 mm, entrambi motorizzati come standard con movimenti precisi grazie alla presenza di servomotori. La profondità incavo è invece di 510 mm, la velocità di avvicinamento pari a 110 mm/s, quella di lavoro di 8,4 mm/s e quella di ritorno di 130 mm/s.