Il recente incremento di richieste per la produzione dei dispositivi di supporto alle barelle per ambulanza ha spinto Stem Technology a ricercare soluzioni di saldatura efficienti e tempestive. La risposta è arrivata con la tecnologia Tawers di Panasonic, integrata da Roboteco-Italargon, che si è rivelata perfetta specie nella saldatura dei modelli in lega leggera prodotti dall’azienda.
Noi tutti abbiamo avuto modo in questi anni di toccare con mano gli effetti della pandemia sui nostri stili di vita ma soprattutto sulla nostra salute. L’intero sistema sanitario mondiale è stato messo sotto un’inimmaginabile pressione; in questo scenario, si è creata una catena di cure utili a garantire un tempestivo soccorso ai pazienti.
Il primo anello di questa catena è stato certamente il servizio di assistenza tramite ambulanze, utili per il trasporto degli assistiti in strutture ospedaliere con massima sicurezza e comfort. Tra le tante, un’azienda italiana – Stem Technology di Medesano (PR) – attiva da 35 anni e tutt’ora gestita dal suo fondatore, si è distinta sul mercato. Stem infatti, opera con successo nel settore dei dispositivi avanzati per il trasporto in ambulanza e idroambulanza.
Il prodotto di punta dell’azienda è ad oggi il supporto barella ammortizzato dotato di sospensione idropneumatica autoregolante in base al peso del paziente trasportato. Il telaio di sostegno di quest’ultimo è realizzato in tubolari in alluminio al silicio con spessore di 3,5mm, saldati tra loro e con piastre di rinforzo di spessore molto variabile, fino a 10mm.
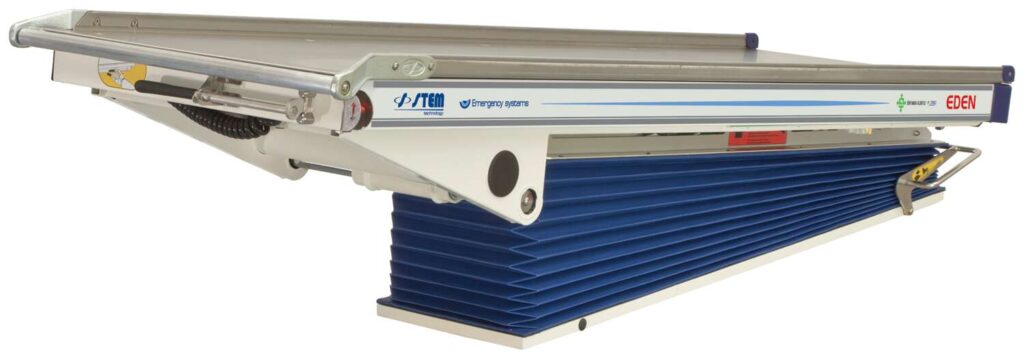
La partnership giusta per la massima efficienza dei processi produttivi
Stem ha da tempo scelto Roboteco-Italargon come partner tecnologico per il miglioramento continuo dei propri processi di saldatura robotizzata e, adesso che i volumi di produzione stanno avendo tassi di crescita a doppia cifra, l’esigenza principale dell’azienda è garantire la massima efficienza dei processi produttivi, sia in termini di affidabilità, tempo ciclo e “tasso di disponibilità” dei robot, oltre che ovviamente di incremento della qualità dei giunti saldati, tramite idonei sistemi integrati di controllo e tracciabilità dei dati.
La tecnologia Tawers di Panasonic si è rivelata la risposta migliore a tali esigenze, in particolare applicata alla saldatura dei vari modelli in lega leggera prodotti da Stem.
Tre sono le celle robotizzate attualmente in uso nello stabilimento di Medesano.
Due funzioni specifiche per una tecnologia di fusione unica nel suo genere
Tra le caratteristiche di base della tecnologia Tawers, ormai ben note nel mercato della saldatura robotizzata, risaltano due funzioni specifiche che si sono rivelate fondamentali per l’ottenimento degli obiettivi dell’azienda.
Entrambe le funzioni presuppongono l’utilizzo della speciale torcia SAWP (Super Active Welding Process) con il filo d’apporto che partecipa in modo “attivo” al bagno di fusione e sono rese possibili dall’architettura del controllo robot che “fonde” insieme sia il controllo di moto degli assi robot e dell’alimentatore filo con il controllo della dinamica d’arco del generatore di corrente. È questa ancora l’unicità della tecnologia di fusione Tawers.
Con la funzione detta SWLP (oscillazione a spirale con bassa pulsazione) il filo pendola su una sezione ellittica parallela all’avanzamento della saldatura (non più ortogonale come nei metodi tradizionali), garantendo così un ottimale rimescolamento del bagno di fusione con evidenti vantaggi in termini di estetica del cordone.
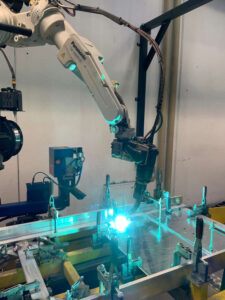
Questa funzione peraltro viene molto apprezzata anche in altri settori industriali come ad esempio il settore del motociclo. Nel caso dei telai Stem una gran parte dei giunti sono a spessori dissimili e la funzione SWLP viene in grande aiuto per regolare molto finemente e con estrema facilità di programmazione i parametri di saldatura durante il pendolamento a spirale.
Durante i 360° della rotazione ellittica si passa così dalle elevate potenze necessarie sullo spessore maggiore alle potenze più controllate sullo spessore minore in modo molto rapido e preciso, dosando al meglio l’apporto termico e di conseguenza la penetrazione al vertice, in assenza totale di spruzzi, porosità e soffiature.
La funzione ASP- Aluminium Stich Pulse – si indirizza invece alla saldatura dei piccoli e medi spessori. In questo caso la modalità filo attivo si alterna alla tradizionale modalità in arco pulsato.
La prima garantisce un innesco pronto e robusto, allontanando e avvicinando il filo dal bagno fuso con elevatissime frequenze, la seconda invece, subentra non appena l’arco si è stabilizzato e, tramite la funzione “stich pulse” gestisce il continuo spegnimento e accensione d’arco. Il materiale ha così tempo di raffreddarsi senza perdere la capacità di penetrazione dell’arco elettrico.
Il risultato è un’ulteriore riduzione dell’apporto termico con conseguente miglioramento delle tolleranze dimensionali del componente saldato, unito ad un eccellente aspetto estetico del cordone, assolutamente comparabile con un analogo giunto saldato in TIG.