La rettifica di ingranaggi interni ha sempre presentato dei limiti, perché richiede tempi lunghi e non consente di raggiungere precisioni elevate. Attualmente la situazione sta cambiando, grazie allo sviluppo di nuove tecnologie, che consentono interpolazioni a grande velocità tra i vari assi e permettono così nuovi metodi di rettifica.
Gianfranco Bianco
Il progressivo aumento della produzione di veicoli a trazione elettrica sta cambiando la struttura delle trasmissioni nel settore automotive.
Il cambio meccanico tradizionale non viene più montato su molti veicoli elettrici dove viene utilizzato prevalentemente un riduttore epicicloidale.
Questo tipo di riduttore è formato da una corona con dentatura interna su cui ingranano tre o quattro ingranaggi satelliti.
Sull’asse è montato un altro ingranaggio, detto solare, che ingrana con gli ingranaggi satelliti trasmettendo il moto al gruppo.
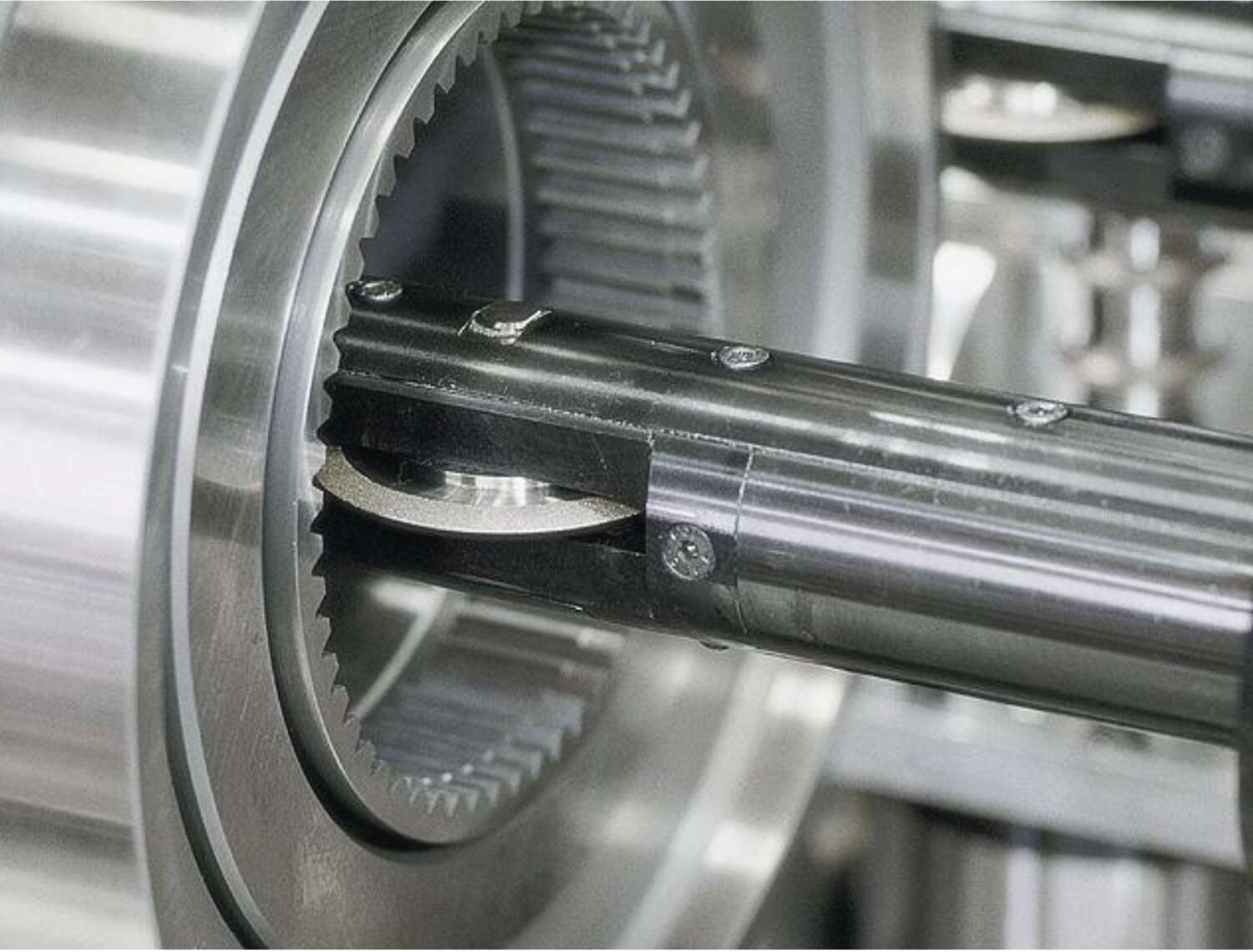
I vantaggi derivanti dall’utilizzo di un riduttore epicicloidale sono due: in primo luogo la possibilità di avere un rapporto di riduzione molto alto, secondariamente, di avere un ingombro ridotto con una riduzione del peso complessivo.
Questo ultimo aspetto è particolarmente apprezzato in quanto compensa, almeno in parte, il grande peso delle batterie.
Il maggiore rapporto di riduzione permette di avere in uscita una forte coppia che rende il veicolo più performante.
Poiché nei veicoli a trazione elettrica non c’è il mascheramento del rumore prodotto dal motore a combustione, tutti i rotismi devono essere il più possibile silenziosi.
È evidente quindi che le precisioni geometriche degli ingranaggi e le superfici attive della dentatura devono essere le migliori possibili, in genere di almeno una o due classi di precisione superiore agli ingranaggi utilizzati nei cambi tradizionali.
Il discorso interessa qui soprattutto la dentatura della corona del riduttore epicicloidale, che necessariamente deve essere rettificato.
Infatti, la sola brocciatura o la finitura con il coltello stozzatore o con il metodo Power Skiving non possono garantire gli standard di precisione richiesti.
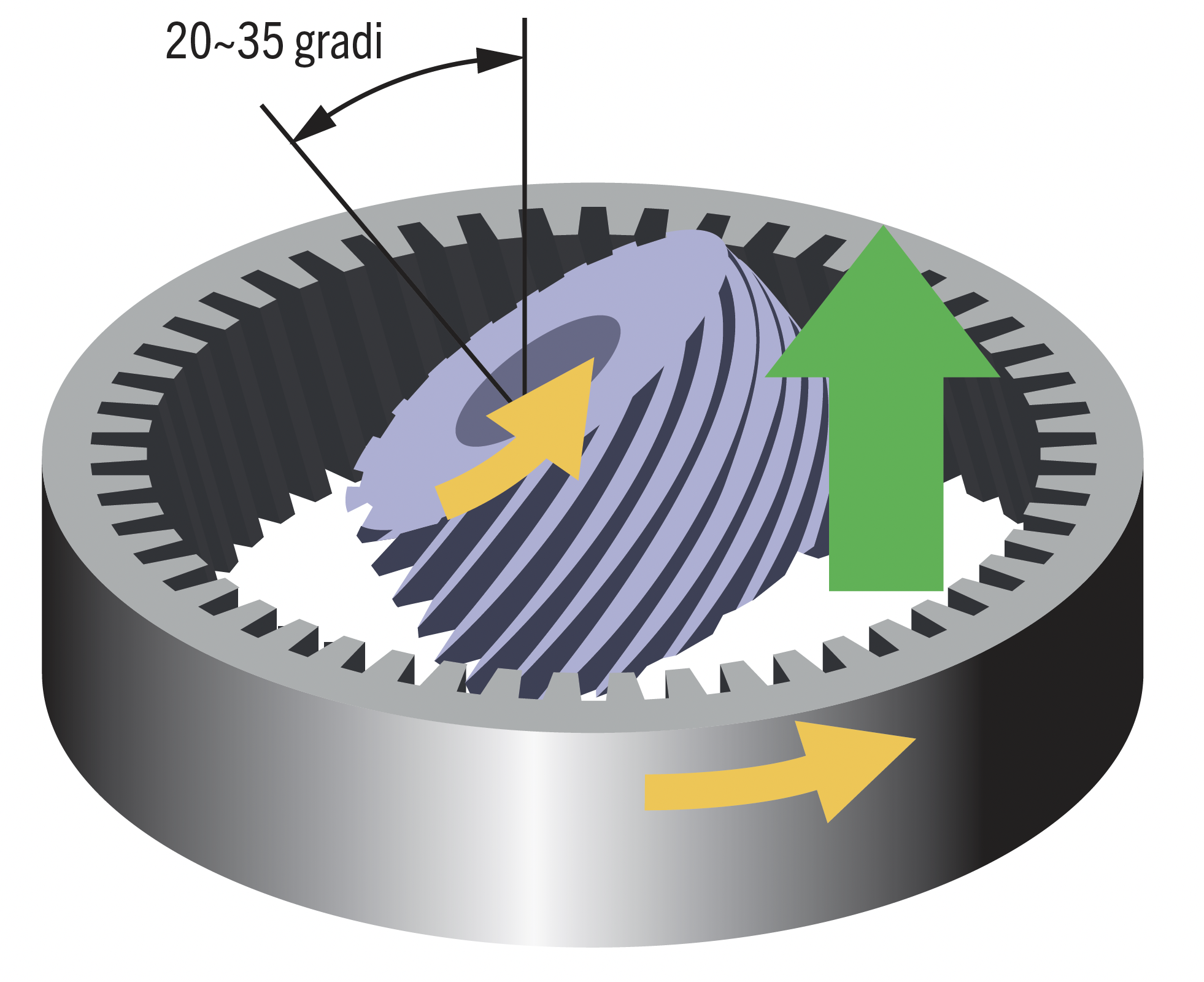
Con il metodo tradizionale di rettifica degli ingranaggi interni si usa una mola di forma di piccolo diametro che finisce un dente alla volta.
La mola può essere in corindone o in CBN.
Il tempo di rettifica è piuttosto lungo e i risultati, a volte, non sono ottimali a causa del piccolo diametro del mandrino e della sua lunghezza che permette flessioni più o meno forti, in relazione all’usura della mola.
I vantaggi della dentatura Super Power Skiving
Ora, grazie alla tecnica di dentatura Super Power Skiving, sviluppata e introdotta da Mitsubishi Heavy Industries Machine Tool Co. Ltd., è possibile ottenere precisioni elevate in tempi relativamente brevi.
Mitsubishi Heavy Industries Machine Tool Co. Ltd., che nell’agosto 2021- a seguito dell’acquisizione da parte di Nidec – ha cambiato il nome in Nidec Machine Tool Corporation produce e commercializza una rettificatrice per interni che lavora per generazione continua, utilizzando una mola a vite di piccolo diametro.
Si tratta di una particolare mola a vite, con un numero di principi molto alto che genera un grande angolo del filetto in modo da consentire un accoppiamento con l’ingranaggio da rettificare, con un angolo di incrocio di 20 – 35° (fig. 3).
L’angolo dell’elica del filetto della mola a vite, così come è inteso normalmente, ha quindi valori che variano da 70° a 55°.
Quindi in pratica si tratta di un ingranaggio elicoidale con un’elica pari all’angolo di incrocio.
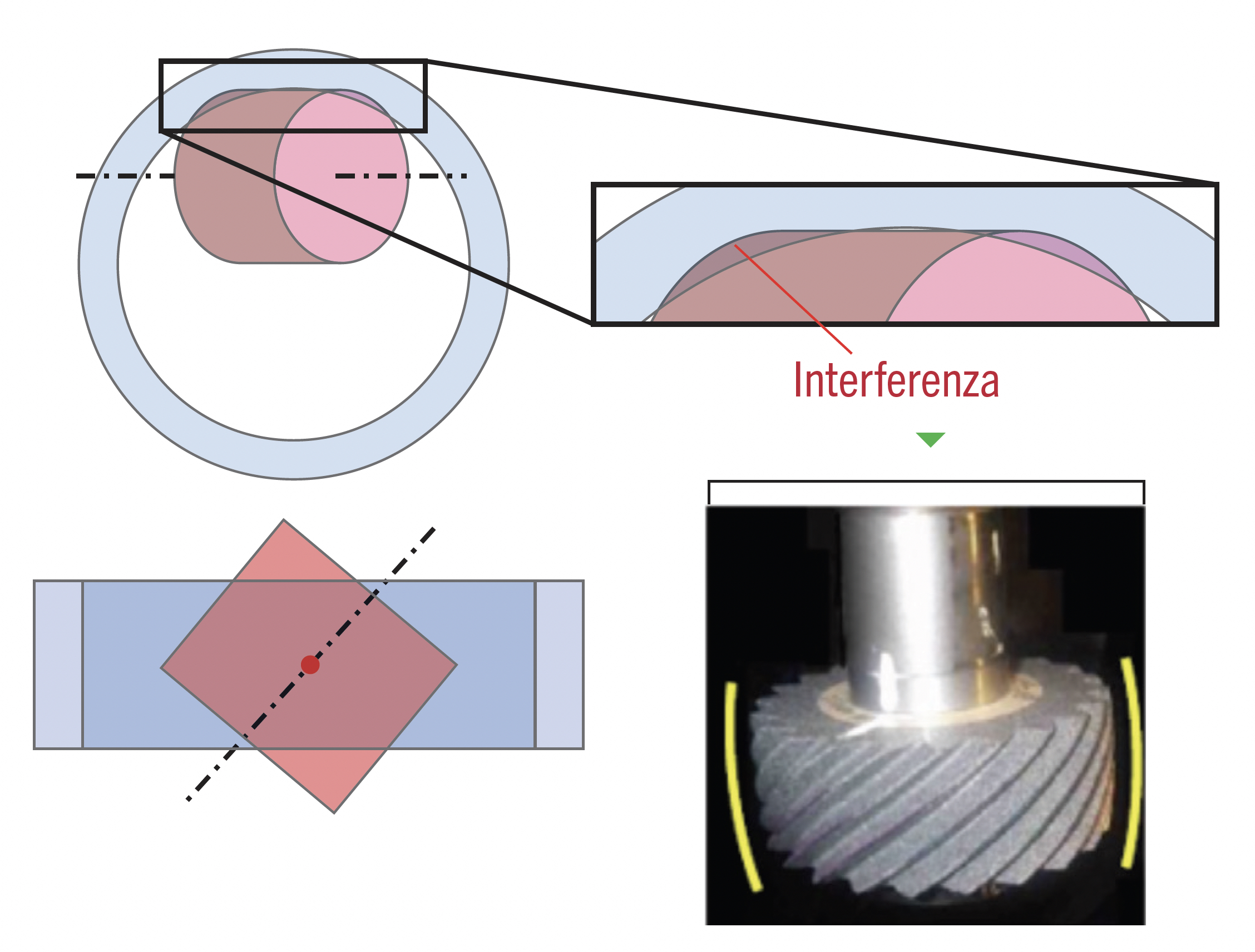
Questo se si tratta di una corona con denti dritti; se però la dentatura interna è elicoidale si può usare una mola che abbia un angolo della dentatura che si avvicina di più a quello di una vite.
L’angolo di incrocio di questa entità è necessario per avere una velocità di strisciamento adeguata per il buon funzionamento della mola, cioè circa 20 – 30 m/sec.
La mola inclinata dell’angolo di incrocio rispetto l’asse della corona interferisce, nelle due estremità, con la dentatura della corona.
Questa interferenza è tanto più marcata quanto minore è il diametro della corona e quanto più grande è l’angolo di incrocio.
Per questo motivo la mola deve avere una forma bombata, cioè la mola deve avere una sagoma tipo botte (fig. 4).
Diviene, perciò, assolutamente necessario montare la mola su un elettromandrino ad alta velocità che possa raggiungere almeno 15.000 giri/min (fig. 5).
Ovviamente, deve trattarsi di un mandrino di qualità, assolutamente privo di vibrazioni, del tipo direct-drive che consente una più veloce e precisa interpolazione con gli altri assi.
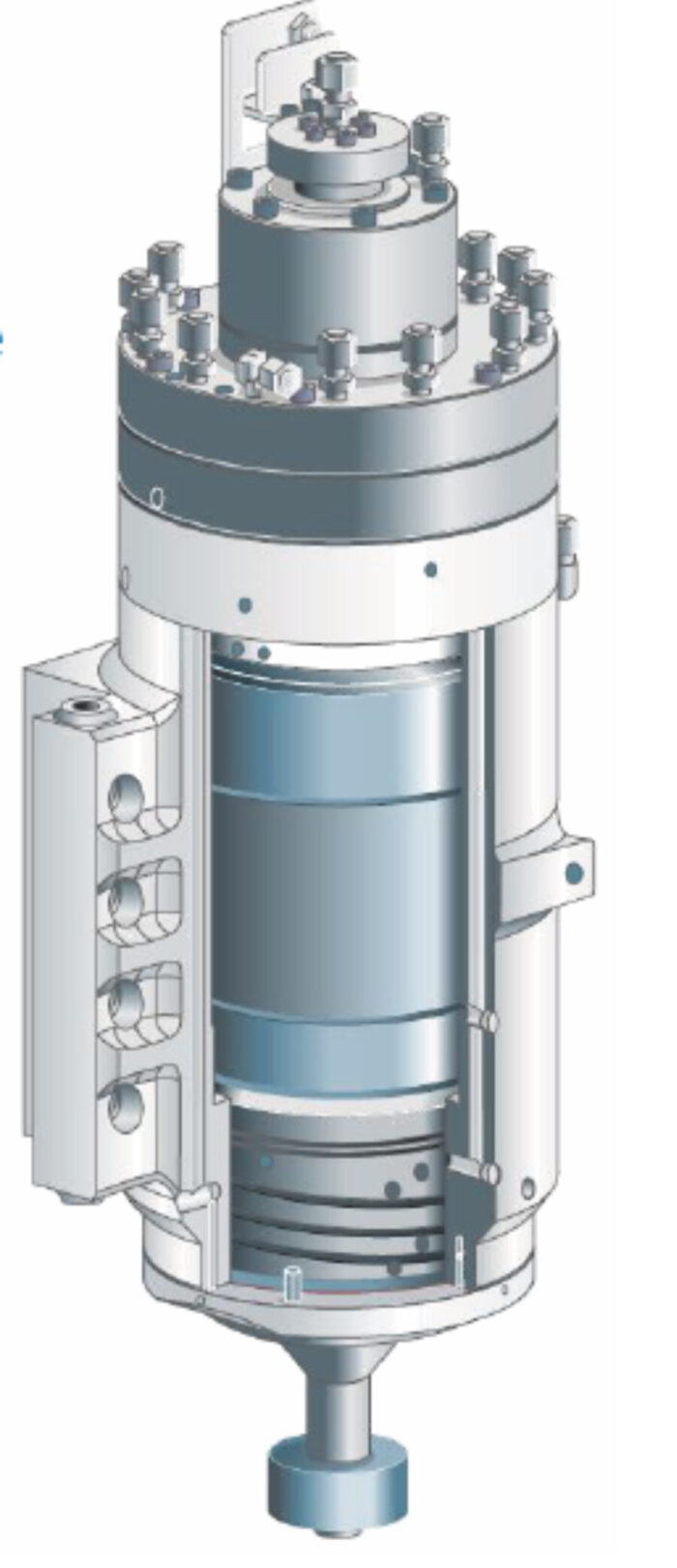
Una rettificatrice a otto assi per corone interne
Nidec presenta una rettificatrice di nuova concezione individuata dalla sigla Z120A.
Si tratta di una macchina a CNC a otto assi idonea alla rettifica di corone interne ma anche di ingranaggi esterni e, in particolare, grazie al piccolo diametro della mola, di ingranaggi vicini a spallamenti o ad altri ingranaggi.
Ciò è reso possibile utilizzando una mola di larghezza ridotta come indicato in figura 6.
Il potente CNC consente la sincronizzazione precisa tra mola e pezzo, anche ad alte velocità.
La macchina può essere automatizzata per produzioni di massa e quindi è dotata di un sensore (contactless) per la sincronizzazione tra le dentature della corona e della mola.
In genere si usano mole in corindone che in base al diametro e alle caratteristiche della dentatura, possono eseguire tra i 100 e 150 pezzi per ogni ravvivatura.
Il diametro della mola è in genere circa il 60 -70% del diametro del pezzo.
La ravvivatura delle mole può essere fatta con un master diamantato simile al pezzo in lavoro posizionato con gli stessi valori di set-up stabiliti nella operazione di rettifica.
Invece, per eseguire prototipi per la ravvivatura, si usa un disco diamantato avente il profilo uguale alla dentatura da eseguire.
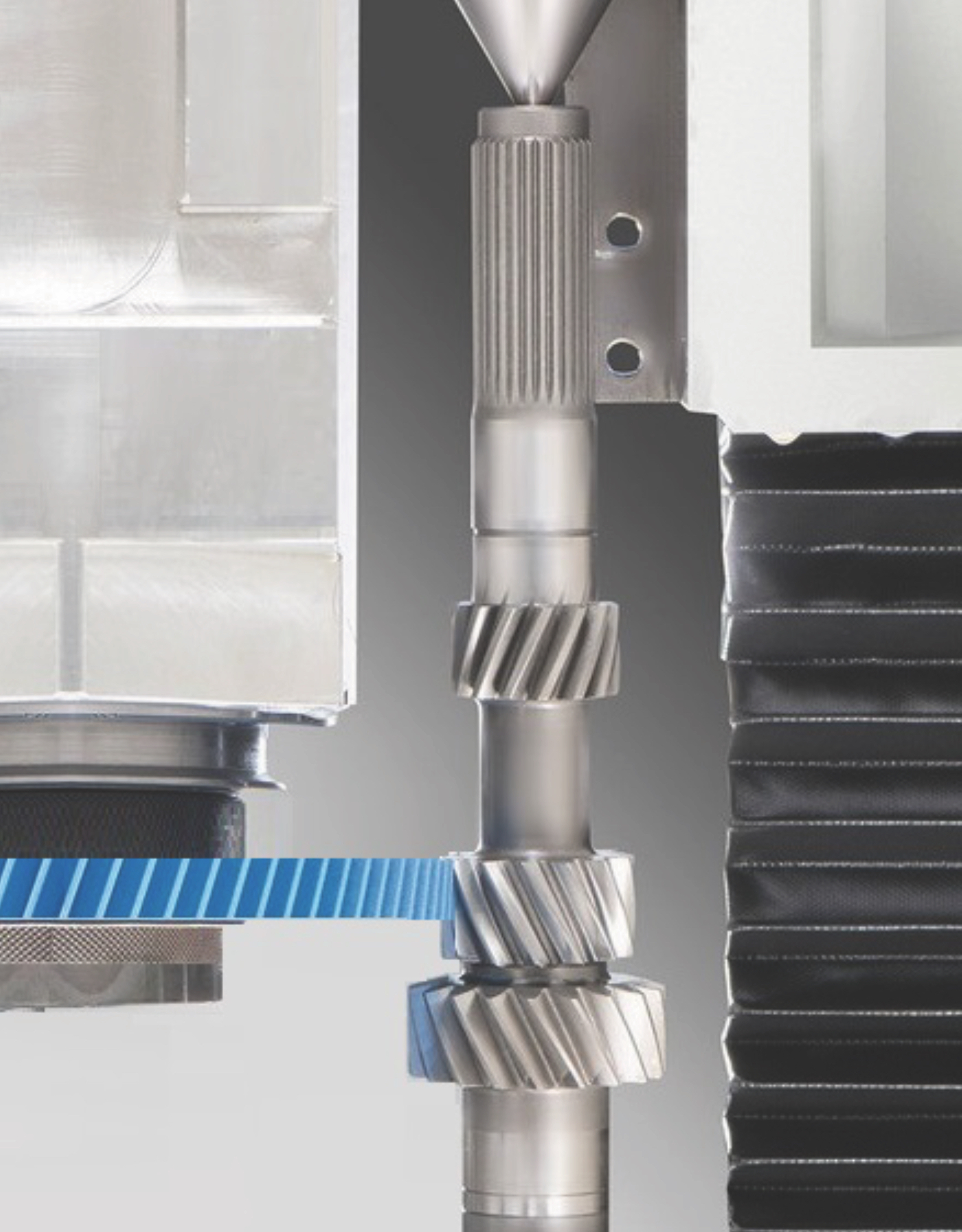
In tal modo si possono ed effettuare facilmente delle modifiche di set-up per l’ottenimento dei profili ottimali.
La macchina non solo esegue operazioni di rettifica, ma può effettuare anche finiture del tipo honing utilizzando in questo caso mole posizionate con angolo di incrocio minore (5-10°) e riducendo la velocità di taglio a circa 5 m/sec (fig. 7).
In collaborazione con il Laboratorio WZL dell’Università di Aachen, sono state eseguite delle prove, a dimostrazione dell’assoluta affidabilità e convenienza del processo. Si riportano qui di seguito i risultati di uno dei numerosi test eseguiti.
Caratteristiche del pezzo
- Modulo = 1,25 mm
- Numero di denti = 85
- Angolo di pressione = 20°
- Diametro primitivo = 106,25 mm
- Materiale 20 MnCr5 cementato e temprato
Caratteristiche della mola
- Materiale corindone
Condizioni di lavoro
- Velocità di taglio = 23,9 m/sec
- Avanzamento in sgrossatura = 0,035 mm/giro pezzo
- Avanzamento in finitura = 0,020 mm/giro pezzo
- Soprametallo per fianco = 0,05 mm
- Tempo ciclo = 125 secondi
Nella figura 8 sono rappresentati i diagrammi di profilo ed elica prima e dopo la rettifica.
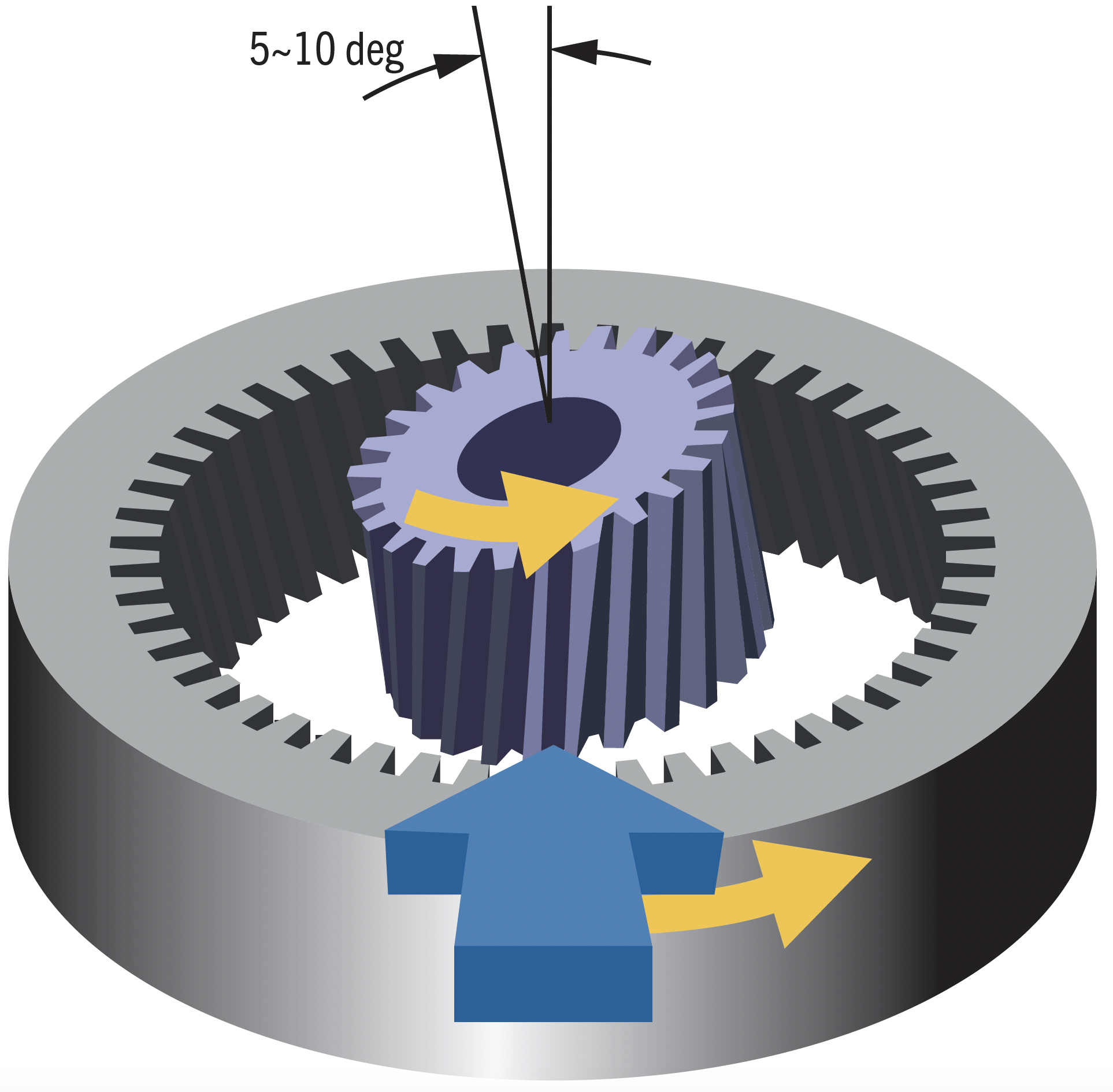
La rugosità superficiale è risultata di circa Ra = 0,2 μm.
L’analisi della superficie con attacco Nital non ha rilevato zone con bruciature rettificando con tempi ciclo accettabili in produzioni di massa.
La rettifica può essere eseguita anche con mole in CBN, ma accurate analisi eseguite dalla MHI hanno dimostrato che con questo tipo di mole non si ha sempre un significativo vantaggio economico, il che vuol dire che la scelta di usare il CBN deve essere ben ponderata.
L’Istituto di ingegneria FEV ha eseguito l’ottimizzazione microgeometrica del profilo dei denti per migliorare la simmetria di contatto tra i fianchi durante il rotolamento.
Queste microcorrezioni, come la bombatura sul fianco e la correzione dell’angolo dell’elica, possono essere ottenute programmando adeguatamente il processo durante la rettifica interna dell’ingranaggio.
Per avere un’idea della qualità ottenibile si riporta il diagramma di figura 9, in cui viene confrontata la deviazione nel rotolamento, espressa in mrad (millesimi di radiante) in tre diverse condizioni:
- senza operazioni di rettifica (zona di colore blu);
- con operazione di rettifica col metodo illustrato (zona di colore rosso);
- simulazione FEV con ingranaggio privo di errori (linea in nero).
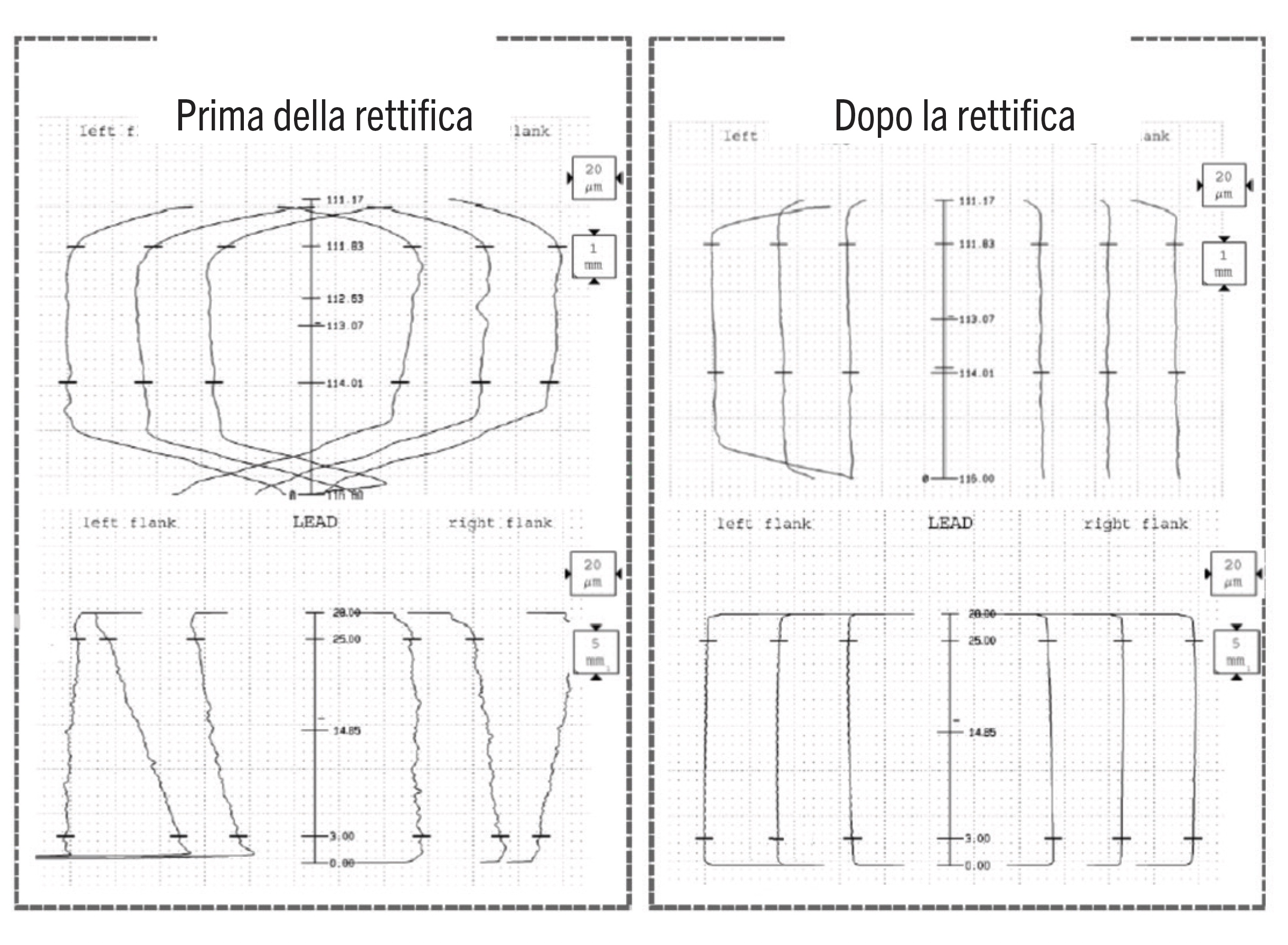
Bisogna considerare che a 1 milliradiante (mrad) corrisponde una deviazione di 0,1 mm su un diametro di 200 mm (raggio 100 mm).
Nella tabella 1 sono riportate le caratteristiche tecniche della rettificatrice Z120A.
In sintesi
• I riduttori epicicloidali sono i componenti più indicati per ottenere un elevato rapporto di riduzione ed un minor peso del gruppo.
• La richiesta di ridurre il livello della rumorosità delle trasmissioni diminuendo le vibrazioni è sempre maggiore. Il processo di produzione della corona con dentatura interna è fondamentale per raggiungere la qualità necessaria ad un costo ragionevole.
• Un ciclo di lavorazione che prevede la dentatura sul tenero e la successiva finitura dopo il trattamento termico è in grado di fornire la massima qualità a costi ragionevoli e permettere cicli compatibili con la produzione di massa automobilistica.
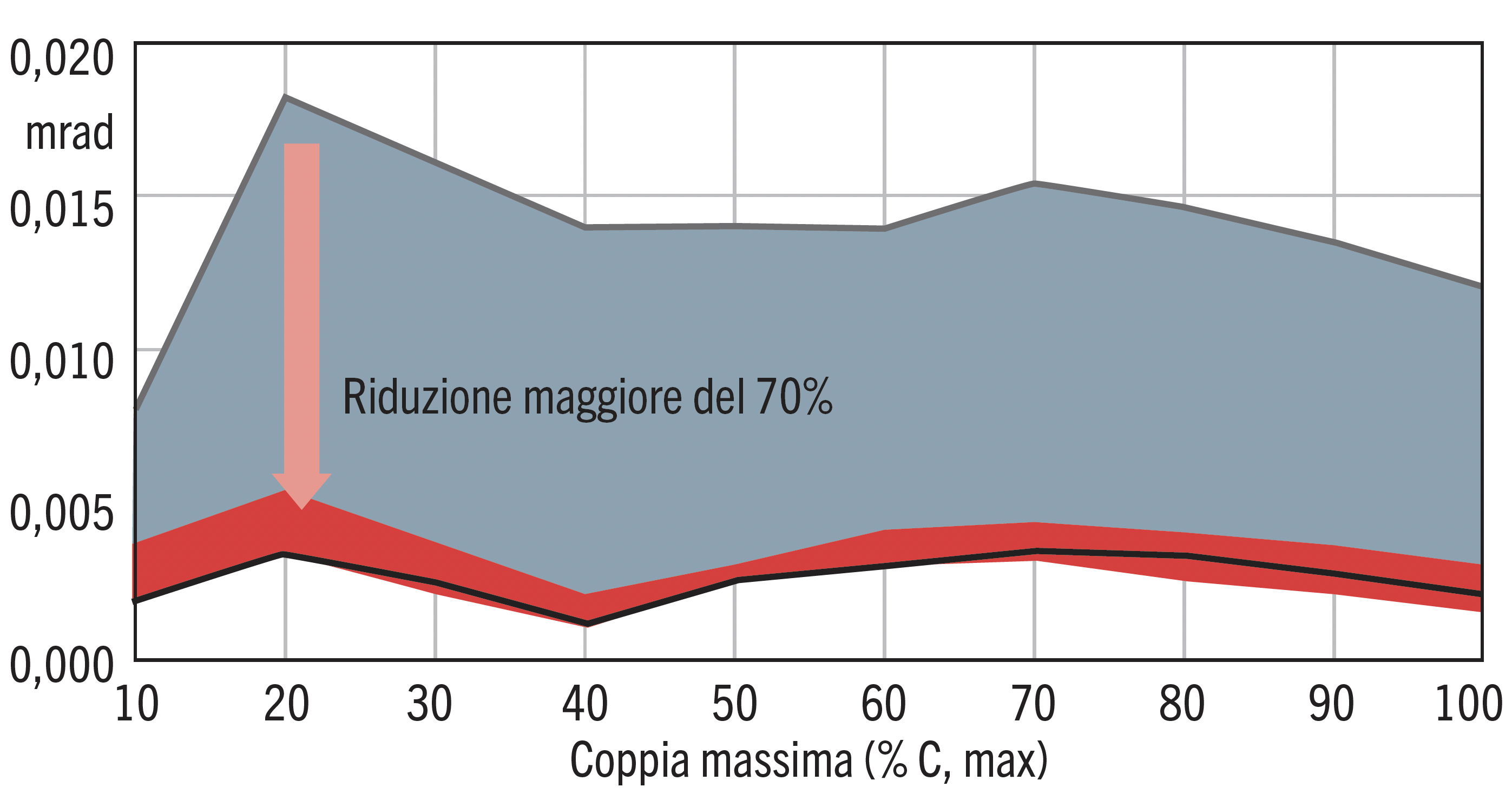
• Gli studi di processo hanno dimostrato che la rettifica per generazione interna è in grado di raggiungere una eccellente qualità complessiva, migliorando notevolmente gli errori di passo delle corone dentate.
• Attraverso la simulazione è anche possibile osservare che una riduzione degli errori del passo e di eccentricità possono limitare le risonanze meccaniche del sistema e ridurre in modo importante il rumore e le vibrazioni.
• La rettifica per generazione interna può migliorare la durata degli ingranaggi consentendo inoltre design più leggeri e compatti.
Ringraziamenti
Si ringrazia Roberto Bagni, Senior Sales Manager Machine Tool Division di Nidec per le informazioni tecniche e le immagini messe a disposizione.