Le produzioni nel settore farmaceutico richiedono competenze interdisciplinari con un alto livello di automazione. Un problema importante è costituito dal trasferimento di materiali sfusi, tipicamente polveri o elementi solidi. L’uso di sistemi di trasporto pneumatico offre buone soluzioni, anche in funzione dell’estrema pulizia richiesta. Diverse tipologie di trasportatori ad aria possono soddisfare esigenze differenti.
L’industria farmaceutica è un settore molto importante nell’economia italiana.
Il settore riunisce tutte le attività relative alla ricerca, allo sviluppo, alla produzione, alla commercializzazione dei farmaci per la medicina umana e veterinaria, nonché di altri prodotti, quali i cosmetici e gli integratori alimentari.
Pertanto, si tratta di un comparto strategico piuttosto esteso e articolato. La sua importanza può essere sottolineata facendo riferimento a dati resi disponibili dalle aziende che sviluppano e producono farmaci, soprattutto per conto delle grandi multinazionali.
Questo gruppo di aziende è individuato con l’acronimo CDMO (Contract Development and Manufacturing Organization).
Secondo un’indagine presentata nel 2021, i bilanci delle aziende CDMO italiane hanno raggiunto nel 2019 un fatturato di circa 2,3 miliardi di euro, pari al 23,3% dell’intero fatturato europeo e si sono collocati al primo posto, davanti alla Germania (2,1 miliardi di euro) e alla Francia (1,9 miliardi di euro).
Negli anni della pandemia il settore ha registrato una ulteriore crescita. In particolare, nel 2020 l’aumento delle produzioni iniettabili è aumentato del 34% rispetto al 2019, mentre la crescita nel 2021 è stata del 4% rispetto al 2020.
Notevole è anche la variazione delle produzioni ad elevata tecnologia e delle biotecnologie, salite dell’11% tra il 2020 e il 2019 e del 13% tra il 2021 e il 2020.
Nel complesso il settore è caratterizzato da una grande vivacità, con una forte propensione all’esportazione, soprattutto verso paesi a elevato sviluppo: quasi il 70% è esportato verso gli Stati Uniti, l’Unione Europea e il Giappone.
La produzione dell’industria farmaceutica coinvolge numerose discipline, a partire dalla chimica, alle biotecnologie, alla medicina, con una forte presenza della meccanica, della robotica e dell’automazione in generale.
Quest’ultima è assolutamente indispensabile per una industria dove i livelli di produzione sono elevati e i cicli di produzione sono molto spesso piuttosto complessi e possono svolgersi sia con linee di tipo continuo, sia con lavorazioni con lotti di prodotto.
Una esigenza tipica è quella di trasferire tra differenti stazioni di lavorazione o di accumulo prodotti sfusi, che possono essere polveri, granuli, pastiglie, compresse o altro.
Se associamo questa necessità all’importanza dell’estrema pulizia, che sempre si associa alle produzioni farmaceutiche, risulta prioritario un trasferimento in ambiente chiuso e protetto.
Una buona soluzione è offerta dai sistemi di trasporto ad aria nei quali il materiale viene spostato dall’aria all’interno di un tubo, con modalità diverse secondo il processo, ma sempre in maniera da preservare l’integrità di quanto trasferito.
Nell’articolo verranno indicate alcune tipologie di sistemi di trasporto pneumatico, nei quali si utilizza aria compressa per spingere o si produce vuoto per aspirare quanto è necessario, e si indicheranno le condizioni di uso.
Saranno anche presentati esempi di applicazioni industriali in campo farmaceutico.
Il trasporto pneumatico per la movimentazione di prodotti sfusi
Il trasporto pneumatico è utilizzato in moltissimi settori per la movimentazione di prodotti sfusi, che vengono spostati facendoli scorrere in modo semplice in un tubo invece che mediante la manipolazione di contenitori, con soluzioni più complesse.
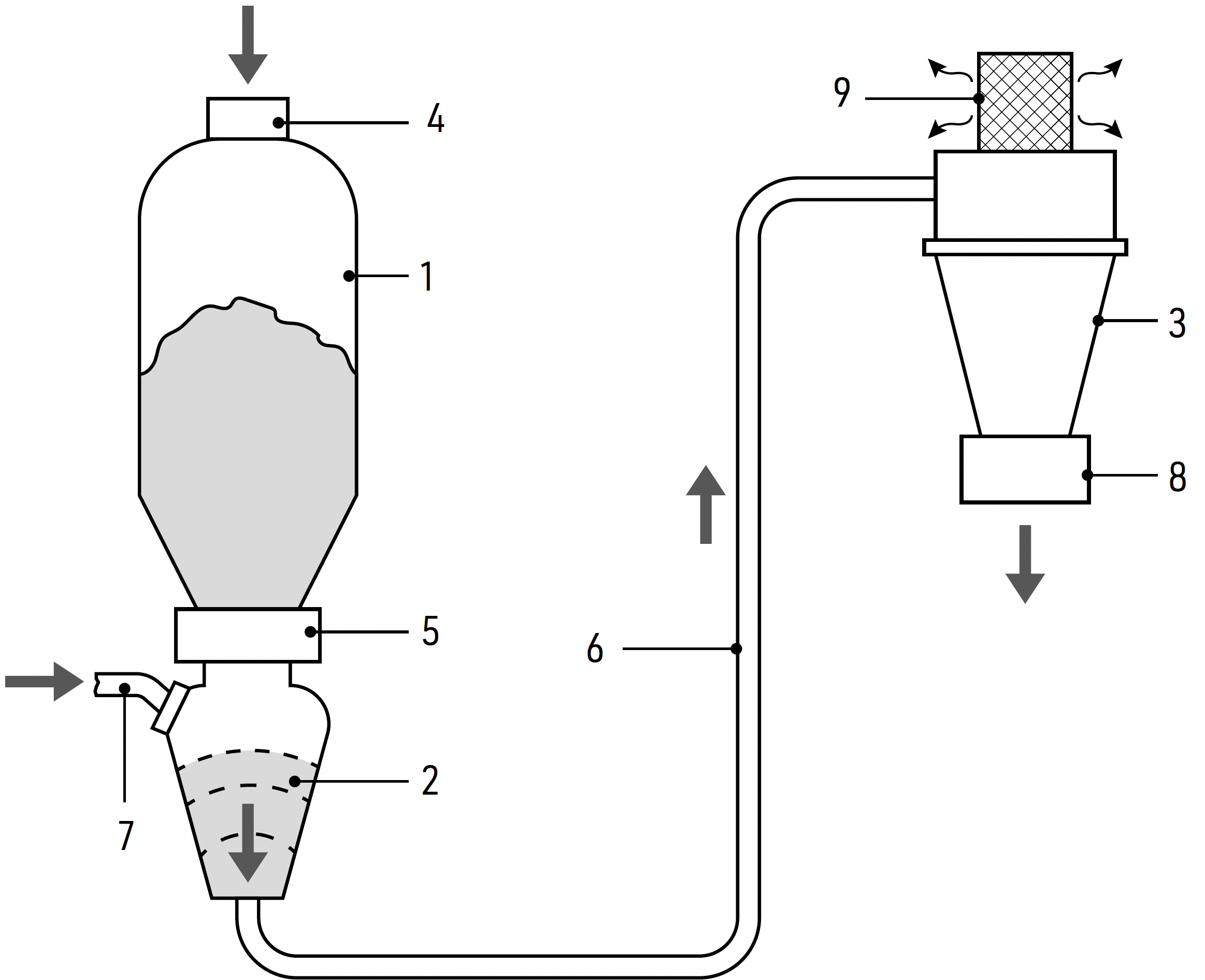
Il trasferimento avviene grazie all’interazione tra il materiale che deve essere mosso e un gas che si sposta con una determinata velocità, spinto da una differenza di pressione.
Normalmente, il gas utilizzato è aria, disponibile ovunque e mossa da compressori o pompe da vuoto.
In alcuni casi particolari, come capita nel trasporto di materiali potenzialmente esplosivi o per prodotti facilmente ossidabili, può essere utilizzato un gas diverso, in particolare l’azoto, che è inerte e non reagisce con il materiale con cui entra in contatto.
Nella figura 1 è mostrato a titolo indicativo il principio di funzionamento di un trasportatore pneumatico a spinta di aria compressa.
Lo spostamento del materiale avviene tra un serbatoio di accumulo 1 e un serbatoio di raccolta finale 3. Per la spinta viene usato un dispositivo propulsore 2 collegato al serbatoio di accumulo da una valvola 5. Con 6 è indicato il tubo di collegamento tra il propulsore e il serbatoio finale. All’inizio il serbatoio 1 viene riempito tramite la bocca di alimentazione superiore 4. Aprendo la valvola 5 il materiale scende in basso e riempie il propulsore. Una volta riempito, si alimenta aria compressa tramite il tubo 7 e l’aria spinge il materiale nel tubo 6. A questo punto il trasferimento avviene con modalità che possono differire da caso a caso, come sarà mostrato più oltre. Alla fine del trasferimento tutto il materiale contenuto nel propulsore raggiunge il serbatoio 3, da cui può essere scaricato aprendo una valvola 8. Con 9 si indica un filtro che consente l’espulsione all’ambiente dell’aria in eccesso durante il trasferimento del materiale e trattiene all’interno del sistema il materiale stesso.
Lo spostamento può avvenire in modi diversi, secondo le esigenze, con un flusso intermittente o con un flusso continuo.
Il sistema nel suo insieme è semplice, di facile applicazione ed è facilmente inseribile nei processi produttivi.
Per questi motivi il trasporto con l’ausilio dell’aria è un sistema molto utilizzato in ambito industriale per trasferire materiali in diversi punti di uno stabilimento e tra diverse stazioni di lavorazione attraverso condutture chiuse.
Le applicazioni coinvolgono i settori più diversi.
Si può pensare, per fare solo qualche esempio, all’edilizia (spostamento del cemento in polvere), alle fonderie (spostamento della sabbia per gli stampi), all’industria tessile (spostamento di fibre), all’agricoltura (movimento di grano, granaglie, semi e vari altri prodotti), all’industria alimentare (farine, polveri da impasto, …), all’industria farmaceutica.
In questo ultimo caso si possono trovare vari processi di miscelazione, trasformazione, granulazione, concentrazione e confezionamento, che interessano sia preparati in polvere, sia capsule, pastiglie e altri prodotti finiti.
Differenti tipi di trasporto pneumatico
Nelle applicazioni industriali la necessità di trasportare materiali granulari o in polvere può essere risolta con trasportatori pneumatici che muovono queste sostanze dentro tubazioni, generalmente circolari, in sospensione fluida mediante una corrente d’aria di adeguata velocità.
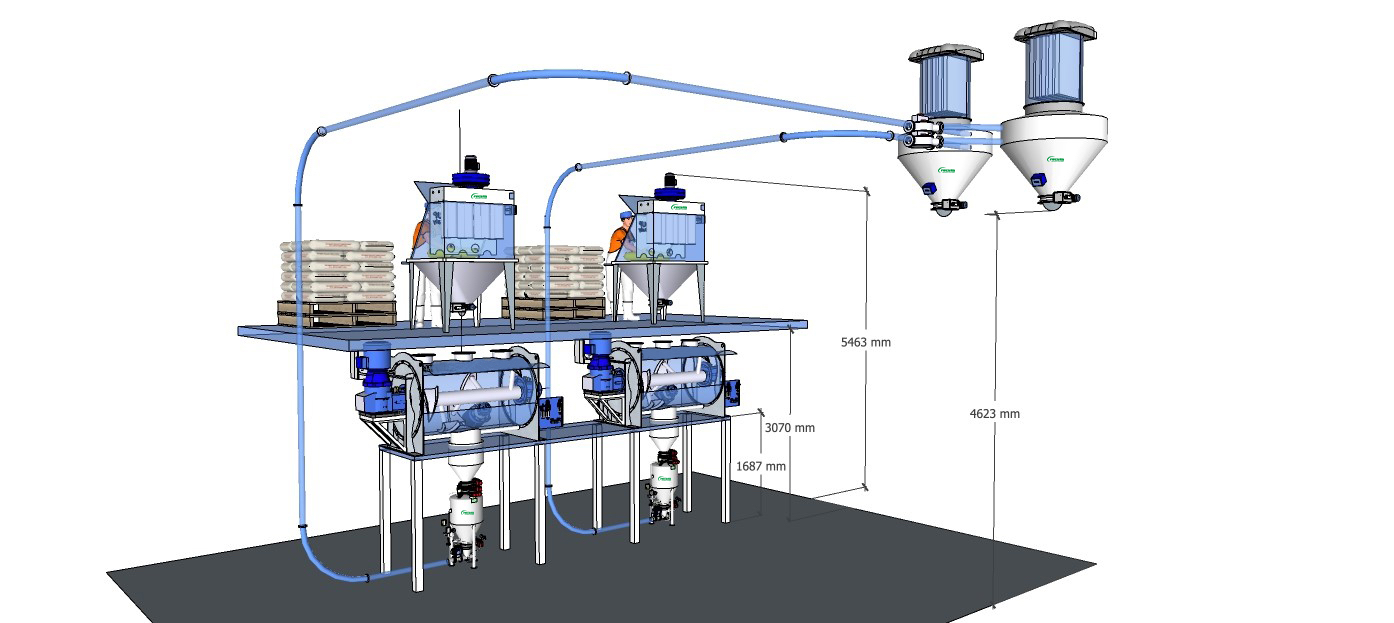
I vari tipi di trasporto pneumatico si differenziano per il modo in cui è realizzato il movimento del materiale: mediante una corrente d’aria in depressione (in aspirazione) oppure con gas in pressione (in spinta).
Una seconda differenza è rappresentata dal tipo di spostamento del materiale: intermittente o continuo.
Vengono quindi prese in considerazione le principali tipologie di trasporto pneumatico che possono essere utilizzate, in particolare nel settore farmaceutico.
Esse sono:
- a) Trasporto pneumatico in pressione, in fase densa;
- b) Trasporto pneumatico in pressione, in fase diluita;
- c) Trasporto pneumatico in vuoto, in fase densa;
- d) Trasporto pneumatico in vuoto, in fase diluita.
I differenti sistemi di movimentazione hanno prestazioni diverse e vengono quindi usati in funzione delle specifiche esigenze di ogni applicazione.
a) Trasporto pneumatico in pressione, in fase densa
Il trasporto pneumatico in pressione utilizza l’aria compressa come mezzo propulsore per spingere il materiale da trasferire, come è mostrato in figura 1.
In generale, consente di percorrere distanze più lunghe rispetto ai sistemi in aspirazione Nel sistema in pressione in fase densa si opera con una velocità di trasporto piuttosto bassa compresa tra 2 e 10 m/s.
Tale velocità, più ridotta rispetto al trasporto in fase diluita, consente di preservare l’integrità del prodotto limitando al minimo i cambiamenti di densità apparente e di granulometria.
L’utilizzo di aria compressa secca e a bassa temperatura conserva le caratteristiche del prodotto trasportato.
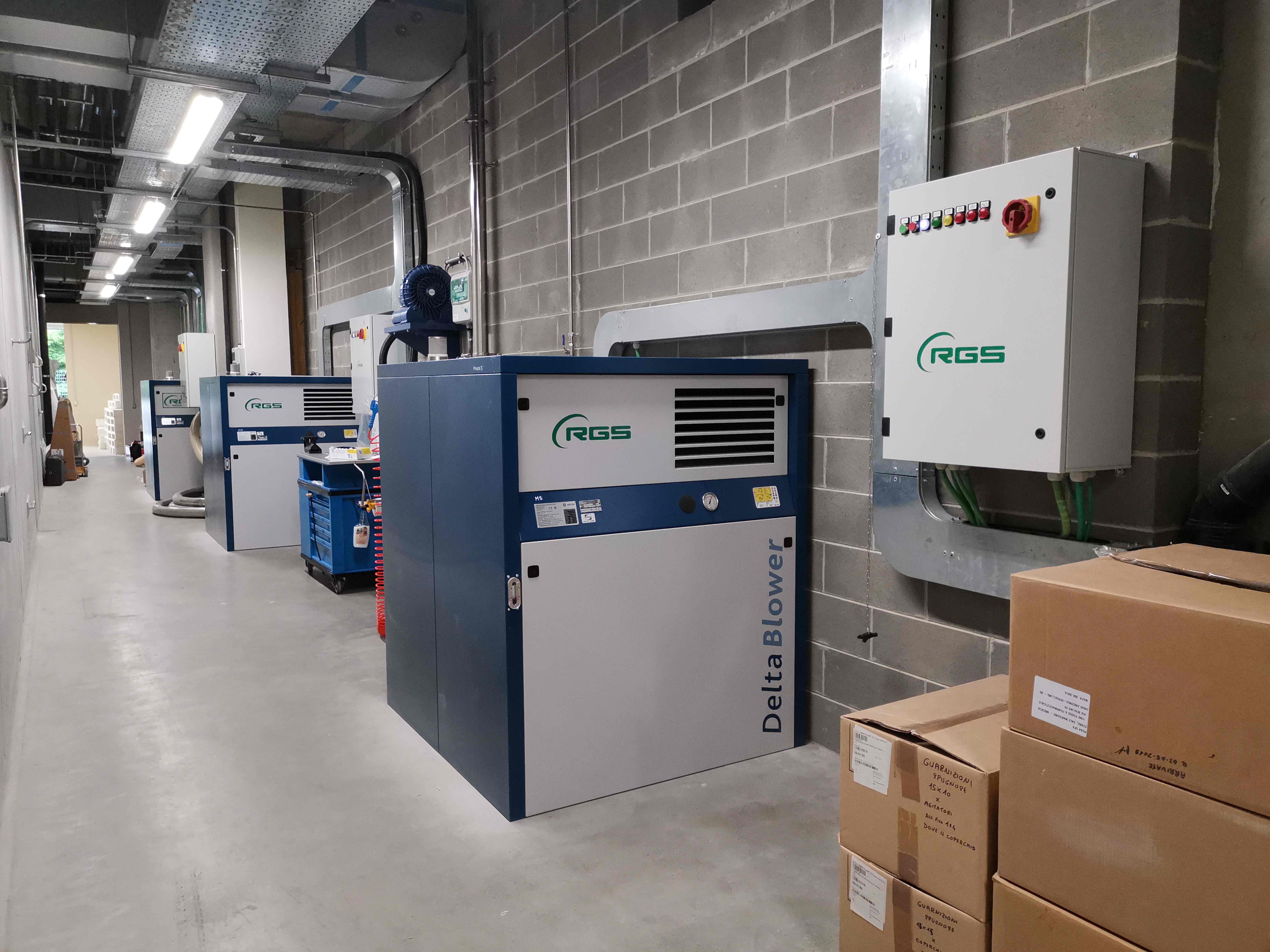
Il rapporto tra il prodotto trasportato e l’aria utilizzata è molto elevato.
Il sistema opera con un basso consumo di aria e nessun motore elettrico sempre acceso: si ottiene quindi un ridotto consumo di energia.
L’utilizzo di poca aria consente di limitare l’ossidazione e la bassa velocità garantisce una usura delle tubazioni ridotta.
Per un buon comportamento contro l’usura e la conservazione del materiale mosso i propulsori possono essere realizzati in ferro verniciato, acciaio inox AISI 304 o AISI 316.
Vantaggio di questo tipo di trasportatore è l’assenza di problemi in caso di interruzione dell’energia elettrica.
Al contrario di quanto capita in impianti più tradizionali, nei quali un’interruzione forzata del trasporto provoca il disarmo della linea che deve essere svuotata per farla ripartire, il trasportatore in fase densa può fermarsi e ripartire in qualsiasi momento senza nessuna necessità di intervento straordinario.
Per quanto riguarda le modalità di gestione vi sono tipologie diverse, con flussi discontinui o con flussi continui, adatte a differenti situazioni.
I flussi discontinui si realizzano quando vi sono fasi in cui vengono trasferiti lotti di materiale, seguite da fasi di interruzione del trasporto.
Lo spostamento con lotti indicato come trasporto con tubo vuoto (o trasporto “batch”) prevede un funzionamento discontinuo secondo il quale tutto il materiale, caricato nel propulsore, viene spinto lungo la tubazione sino alla destinazione tramite aria compressa.
Al termine di questa fase il propulsore e la tubazione restano completamente vuoti e tutto il materiale caricato nel propulsore è stato trasferito alla destinazione. Questo tipo di trasporto è indicato per distanze medio/corte, fino a circa 50-60 metri.
Il trasporto con tubo pieno prevede dei cicli di funzionamento secondo i quali il propulsore viene alternativamente riempito e svuotato, spostando il materiale contenuto nel tratto iniziale del tubo. In questo modo il materiale viene spostato a poco a poco lungo la tubazione.
Dopo aver riempito la linea, il materiale inizia ad essere scaricato nella destinazione con bassissime velocità. Questo tipo di trasporto è indicato per distanze molto lunghe (oltre 100 metri) e /o per trasportare materiali molto fragili o molto abrasivi.
I flussi continui si realizzano quando vi è un’unica fase in cui il materiale viene trasferito senza interruzione del trasporto.
In questo caso si parla di trasporto a tubo pieno in continuo e si prevede l’utilizzo di due propulsori che funzionano alternativamente in parallelo, spingendo il materiale nella stessa tubazione.
Nella figura 2 è mostrato il rendering di un impianto di trasferimento pneumatico in fase densa “Ready Mix” realizzato dalla società RGS Vacuum Systems, società leader nel settore del trasporto pneumatico.
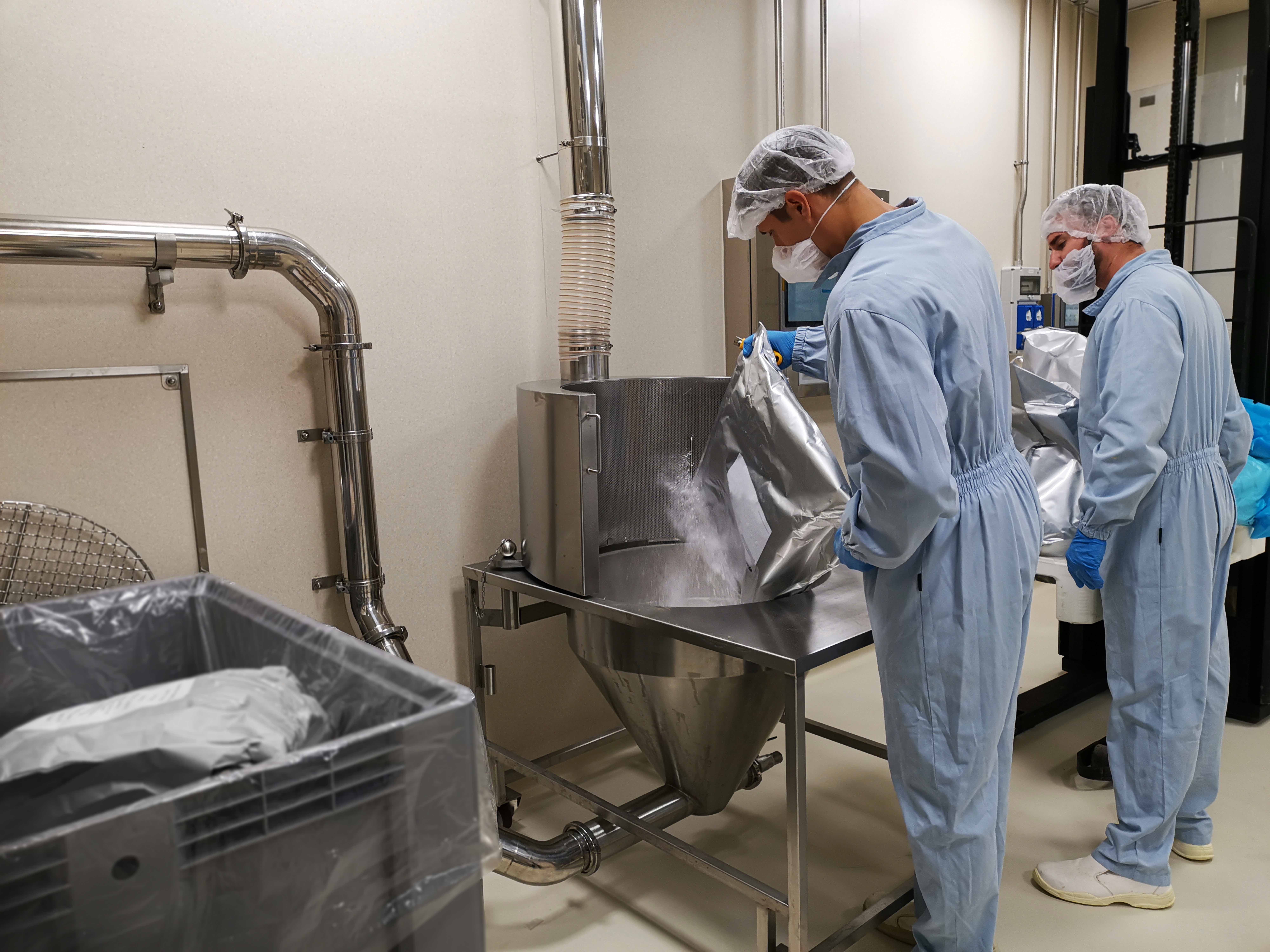
In questo sistema il prodotto arriva in lotti di sacchi e viene immesso per gravità dagli svuota sacchi in un miscelatore rotante.
Nella figura sono visibili due stazioni di carico con pallet e sacchi nella parte alta dell’impianto e due miscelatori al disotto.
In basso si trova il propulsore che viene alimentato dal miscelatore. Mediante travaso con un tubo di trasporto in fase densa il prodotto raggiunge infine le tramogge di ricezione, poste in alto a destra, e alimenta le macchine riempitrici.
Il sistema è destinato alla lavorazione per pesticidi ecologici, a base di funghi e maltodestrine.
Gli impianti di trasporto pneumatico RGS Vacuum Systems vengono personalizzati secondo le esigenze dei clienti e sono disponibili con certificazione PED, ASME e con componentistica ATEX.
In definitiva, i sistemi di trasporto pneumatico in pressione in fase densa possono essere usati vantaggiosamente quando si devono trasportare grandi quantità di polveri o granuli, materiali fragili, materiali molto abrasivi, miscele di prodotto che devono restare omogenee, da pochi metri sino a grandi distanze (superiori a 100 m).
I flussi possono arrivare anche a decine di ton/h. In molti casi il sistema risulta essere la migliore tecnologia di trasporto, in quanto le basse velocità consentono di preservarne l’integrità del prodotto e di evitare l’usura degli impianti. Importante è anche la facilità della pulizia.
b) Trasportatori pneumatici in pressione in fase diluita
La caratteristica propria degli impianti di trasporto pneumatico in pressione in fase diluita è quella di avere un generatore di pressione (rappresentato spesso da un adeguato ventilatore) posizionato a monte del sistema.
Pertanto, tutti i tubi ed i diversi componenti sono in sovrappressione rispetto all’atmosfera. Il materiale viene immesso nel tubo, che ne consente il trasporto fino alla destinazione finale, tramite un sistema di iniezione forzata, che si innesta sulla tubazione stessa.
A seconda delle necessità l’inserimento del prodotto può avvenire con un alimentatore rotativo a tenuta oppure con un iniettore ad aria compressa.
Nei punti di arrivo il prodotto è separato dall’aria di trasporto tramite filtri. Il trasporto pneumatico in pressione in fase diluita opera fluidizzando il materiale, ossia disperdendolo nell’aria di trasporto.
I vari elementi o granuli trasportati tendono così ad essere separati tra loro e ne risulta un insieme a bassa densità.
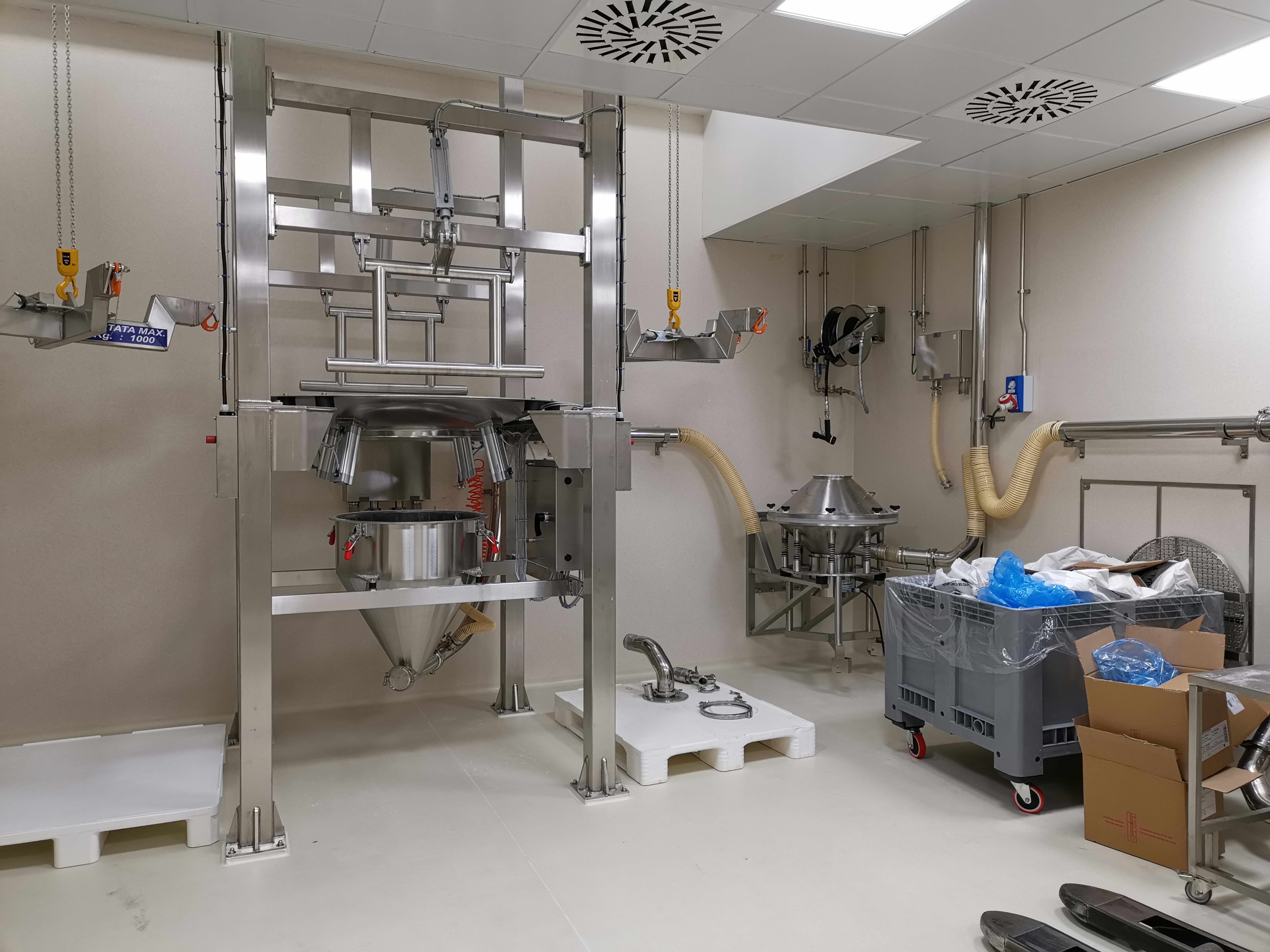
Questo trasporto è indicato per prodotti poco abrasivi, non friabili e dal peso specifico basso e non è assolutamente indicato per il trasporto di prodotti miscelati.
Materiali tipici che vengono trasportati sono: bicarbonato di sodio, ossido di zinco, farine, zuccheri, granuli di plastica, pasticche, ecc.
c) Trasporto pneumatico in vuoto, in fase densa
Nel trasporto pneumatico in vuoto la differenza di pressione necessaria a produrre un flusso di gas è ottenuta realizzando una depressione a valle del tubo di trasporto, invece di spingere con gas in pressione a monte.
In questo tipo di trasportatore si genera, quindi, una depressione all’interno della tubazione e il prodotto viene aspirato dal punto di prelievo al punto di scarico attraverso il tubo di trasporto.
Il materiale aspirato viene inviato mediante un tubo all’interno di un contenitore, dove avviene la separazione tra il prodotto e l’aria.
L’aria aspirata durante il trasporto viene depurata da un filtro ed espulsa dalla sorgente di vuoto.
Tutto il processo è gestito da un’unità di controllo.
Con questo tipo di trasporto la velocità dell’aria è ulteriormente ridotta rispetto ai trasportatori in pressione, fino a valori inferiori a 10 m/s e il vuoto arriva a oltre gli 800 mbar.
La velocità dell’aria non è sufficiente a mantenere in volo le particelle all’interno del tubo.
Pertanto, il materiale tende a rimanere compatto e viene trasportato a blocchi, intervallati da spazi vuoti.
La bassa velocità consente un trattamento delicato dei materiali ed è indicata per prodotti viscosi, abrasivi, miscele, prodotti molto fragili (riso, fibra di vetro, atomizzati ceramici, altro), liquidi.
Tra i vantaggi si possono annoverare la bassa frantumazione dei prodotti, le ridotte dimensioni delle tramogge e dei vari apparati come tubi e pompe da vuoto, modeste superfici filtranti, la buona pulizia interna.
Per la generazione del vuoto si usano unità con canali laterali o a lobi con portate da 2000 a 3000 m3/h con cabina acustica e dotati di filtro di aspirazione e gruppo di ventilazione opzionale.
Tutte le unità sono inoltre dotate di indicatori di pressione analogici o digitali per un facile controllo.
Nella figura 3 è visibile un vano tecnico in cui sono installati aspiratori a lobi con quadri di comando posti a parete.
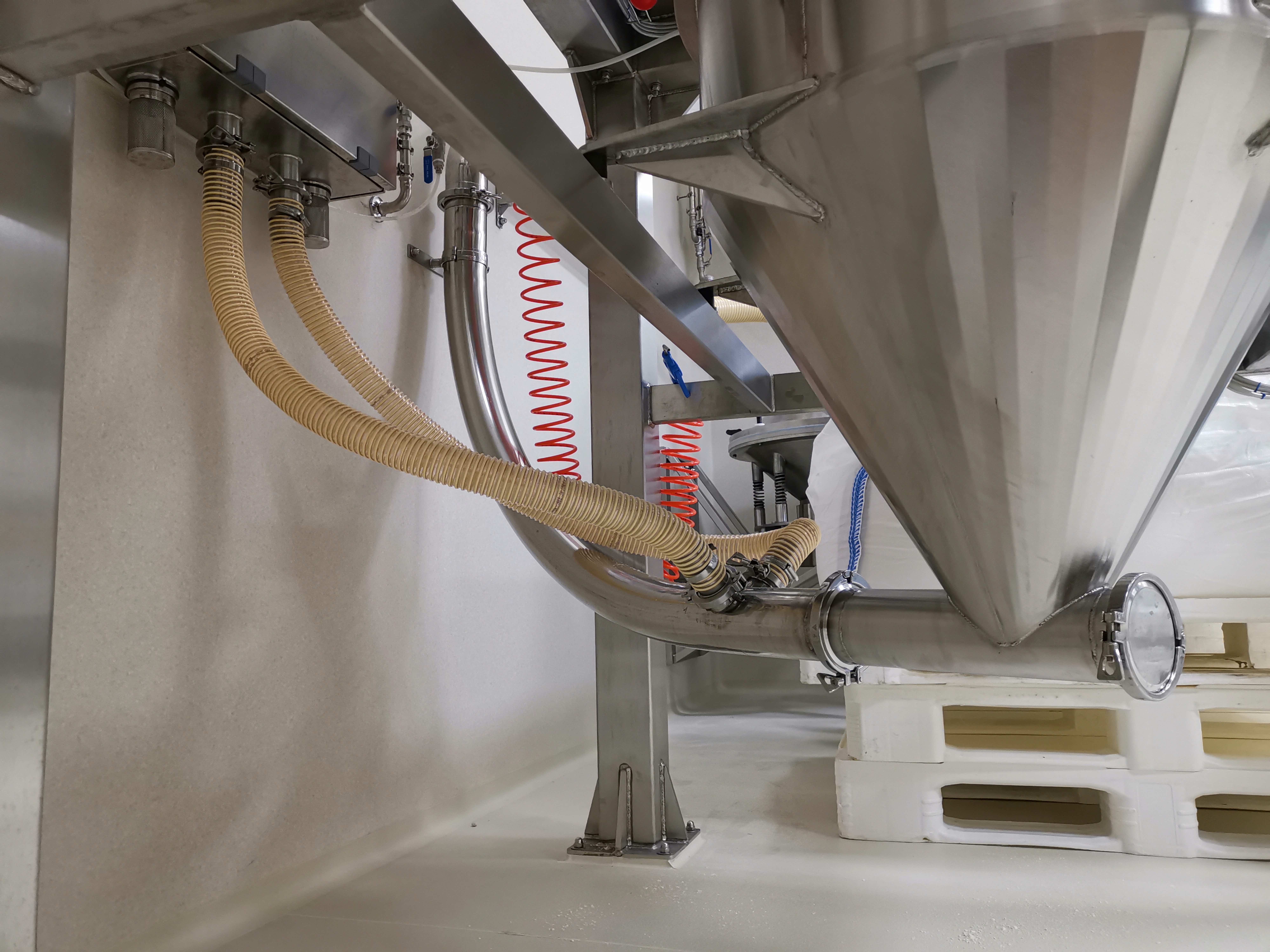
Nella figura 4 è mostrata una stazione manuale di svuotamento di sacchi con sistema di depolverazione.
Il prodotto che deve essere movimentato viene aspirato direttamente dalla base della tramoggia.
La figura 5 mostra una stazione svuota sacconi, indicata anche come stazione big-bag.
Tale stazione è una delle possibili stazioni di carico per un prodotto da movimentare con un trasporto pneumatico.
In generale, il materiale può essere prelevato sia da una stazione svuota sacconi big-bag che da una stazione svuota sacchi, come visto in figura 4.
In entrambi i casi, comunque, il materiale prelevato attraversa un vibrovaglio dove grumi o eventuali corpi estranei vengono bloccati e scartati.
Nella figura 6 si vede il dettaglio del fondo della stazione svuota big-bag. Il prodotto viene aspirato e miscelato con l’aria, modulandone l’apporto con l’utilizzo di due valvole di regolazione differenti.
d) Trasportatori pneumatici in vuoto, in fase diluita
Il trasportatore opera con vuoto e genera una depressione all’interno della tubazione di trasporto, per cui il prodotto viene aspirato dal punto di prelievo verso il trasportatore stesso.
Il materiale prelevato viene inviato, mediante una tubazione, all’interno di un contenitore, dove avviene la separazione tra il prodotto e l’aria.
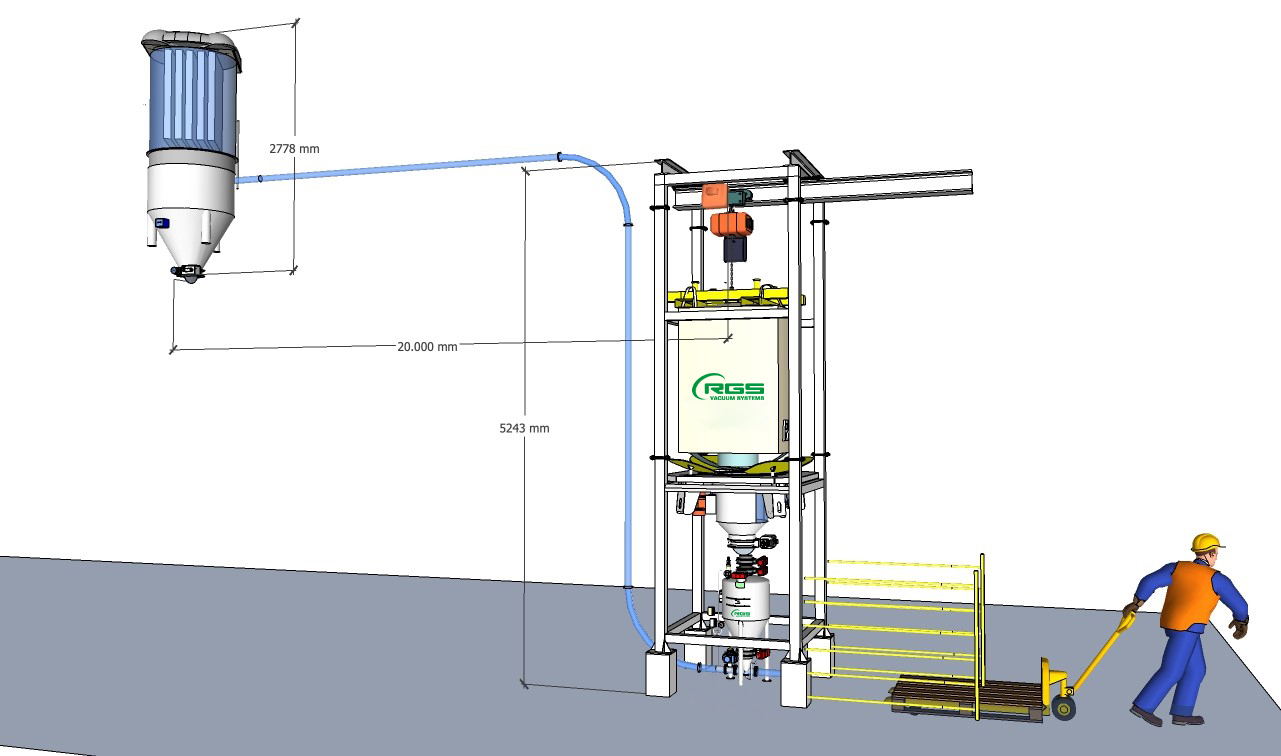
L’aria aspirata viene, infine, depurata con un filtro ed espulsa all’esterno dalla pompa del vuoto.
Il trasporto pneumatico in fase diluita, o a bassa pressione, si caratterizza per il valore ridotto del rapporto di concentrazione di massa del prodotto per m3 di aria.
La velocità dell’aria all’interno delle tubazioni è generalmente compresa tra 20 e 40 m/s con una depressione massima di 400/500 mbar.
La velocità delle particelle di prodotto è sensibilmente più bassa, ma tale da non permettere il deposito del materiale all’interno della linea di trasporto.
Tra i vantaggi possono essere ricordati: la possibilità di funzionamento in continuo del sistema di trasporto; la facilità di gestione e di manutenzione degli impianti, l’operare con costi contenuti, la possibilità di raggiungere distanze elevate.
Il trasporto pneumatico in vuoto in fase diluita è particolarmente indicato nell’industria farmaceutica, cosmetica, chimica, alimentare e dolciaria.
È consigliato per la movimentazione di polveri e granuli, materiali non abrasivi e materiali poco fragili.
La differente configurazione tra impianti di trasferimento pneumatico in pressione e impianti di trasferimento con vuoto è chiarita dalla figura 7.
In figura 7a è mostrato un esempio in cui il materiale viene caricato con una stazione svuota sacconi big-bag e trasferito a una tramoggia ricevente visibile in alto a sinistra. Sulla tramoggia è presente un grosso filtro di scarico dell’aria.
Nella figura 7b il materiale è mosso da un trasportatore a vuoto che ha inizio con una stazione di carico big-bag. Sulla tramoggia ricevente, sempre in alto a sinistra, vi è un filtro collegato a una pompa da vuoto.
Esigenze specifiche e applicazioni nel settore farmaceutico
La preparazione e il confezionamento dei prodotti farmaceutici richiedono di soddisfare alcune importanti condizioni collegate con la specificità dell’applicazione.
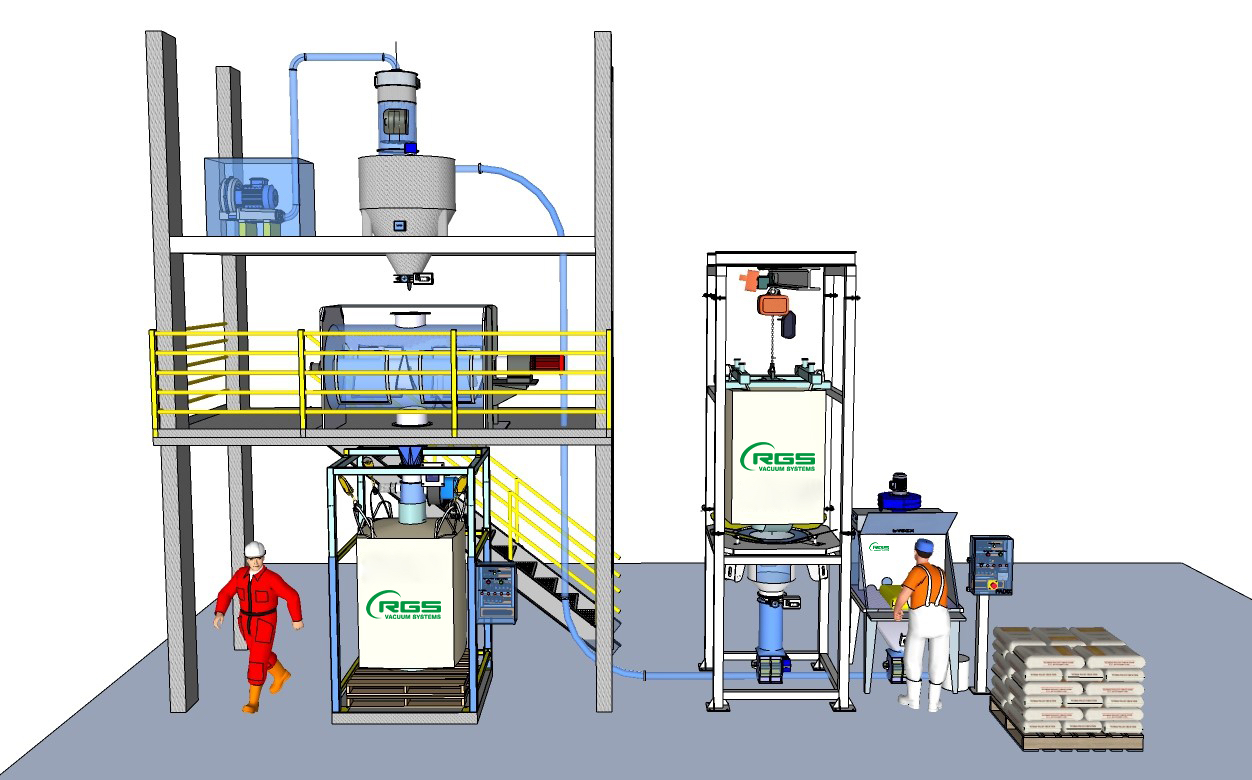
Tra queste è opportuno ricordare che viene movimentato un materiale destinato a interazioni dirette con l’uomo. Pertanto, occorre garantire non solo condizioni di pulizia, ma spesso anche la necessità di evitare qualsiasi contaminazione.
Tutto questo ha riflessi nella scelta dei materiali, nella definizione dei sistemi di filtrazione, nella necessità di isolare quanto viene trattato dall’esterno.
Un trasporto pneumatico, in cui tutto viene mosso all’interno di tubi chiusi, con presenza di filtri e protezioni viene incontro all’esigenza.
Altra condizione è quella di non danneggiare i materiali, soprattutto quando si parla di prodotti finiti (capsule, pastiglie ecc.).
Da questo punto di vista un trasporto con aria, applicato con le dovute condizioni operative, appare molto adatto.
L’aria infatti può agire come mezzo per sostenere e isolare gli elementi da muovere, evitando strisciamenti significativi, urti e relative abrasioni e rotture.
Il trasporto pneumatico è largamente usato nell’industria farmaceutica, con applicazioni di vario tipo, come indicano le fotografie riportate.
Nella figura 8 è mostrato la configurazione di uno stabilimento per la produzione di integratori alimentari (proteine del siero di latte/collagene/aminoacidi/maltodestrine/vitamine).
Il sistema comprende un impianto di miscelazione e riempimento da big-bag e sacchi con alimentazione pneumatica. Tutte le parti in contatto con il prodotto sono realizzate in acciaio AISI 304.
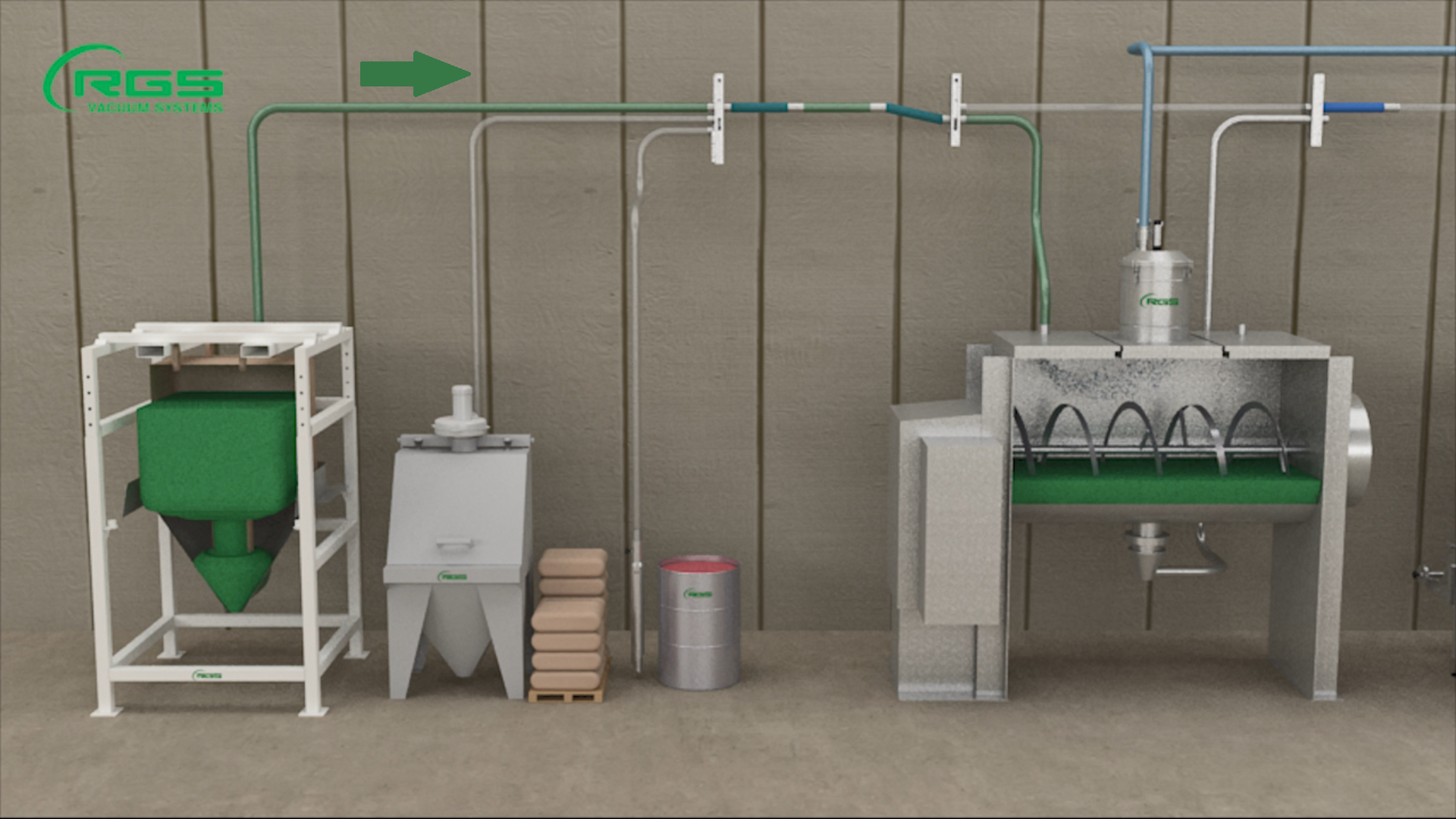
La materia prima arriva in sacchi e sacconi, viene alimentata al piano terra tramite lo svuota big-bag e lo svuota sacchi.
Il trasferimento pneumatico avviene in depressione, la miscela viene alimentata alla torre di miscelazione e viene lavorata con il conseguente riempimento del big-bag successivo. Vengono riempiti vasi da 1800 g e buste da 500 g e 1000 g.
In figura 9 è mostrato il rendering di una stazione di lavoro in cui due diversi prodotti vengono mescolati da un miscelatore a spirale.
Il trasferimento dalla stazione di carico dei prodotti al miscelatore avviene con trasporto pneumatico.
In figura 9a viene alimentato il primo prodotto (indicato in colore verde) e nella figura 9b viene trasferito il secondo prodotto (indicato con colore giallo).
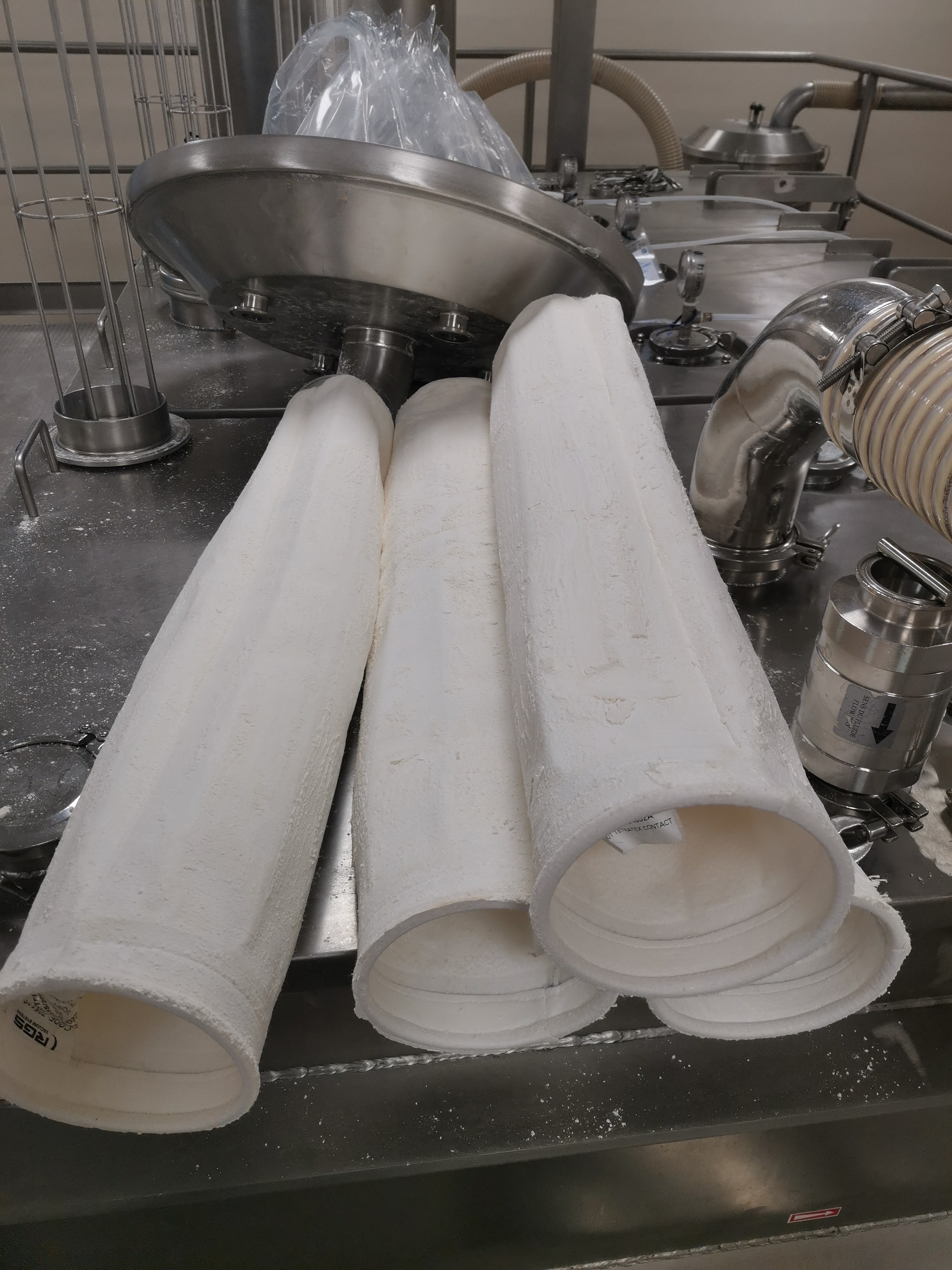
In tutte le applicazioni si fa largo uso di filtri per la separazione dell’aria dai prodotti movimentati; il problema è particolarmente importante nel caso di prodotti polverosi.
Nella figura 10 è mostrato lo smontaggio di uno di questi filtri (filtro a maniche).
In conclusione
Il settore farmaceutico è piuttosto complesso, con una varietà di attività che vanno dalla preparazione di sostanze, al processo di fabbricazione di prodotti, al loro confezionamento.
In varie fasi del processo è necessario movimentare materiale sfuso, dalle polveri ai prodotti granulari (semilavorati o prodotti finiti).
L’uso di sistemi di trasporto pneumatico facilita la movimentazione di prodotti sfusi e facilita il processo produttivo. Le diverse esigenze possono trovare una risposta adeguata in soluzioni di trasporto ad aria differenti.
La pneumatica si conferma, ancora una volta, una tecnologia multiforme, che si affianca alle altre per risolvere nel modo migliore i più svariati problemi.
Si ringrazia la società RGS Vacuum Systems per la collaborazione e per la fornitura di materiale fotografico.
Riferimenti:
- https://rgsvacuumsystems.com
- G. Belforte, “Manuale di pneumatica – terza edizione”, Tecniche Nuove, 2019.
di Guido Belforte