L’articolo valuta la resistenza a erosione di un acciaio inox martensitico (AISI 410) indurito termicamente, mediante tempra e rinvenimento, con un rivestimento in carburo di tungsteno (86WC-10Co-4Cr). Il trattamento è stato ottenuto mediante deposizione termica a spruzzo di ossigeno ad alta velocità (HVOF). Il rivestimento riesce a raddoppiare la resistenza all’usura erosiva.
In diversi settori industriali si può essere in presenza di particelle solide trasportate da un fluido.
Questo avviene, ad esempio, negli impianti di estrazione di petrolio o gas dove sono utilizzate miscele multifase costituite da acqua, petrolio, sabbia e aria.
Queste particelle solide scorrono insieme al fluido trasportato e vanno a urtare i vari componenti di impianto provocando un’erosione superficiale conosciuta come usura erosiva o jet slurry erosion.
Questo lavoro analizza, in particolare, la perdita di volume di materiale sotto attacchi erosivi di un getto di liquido con particelle erodenti di allumina elettrofusa e angoli di incidenza di 30° e 90°.
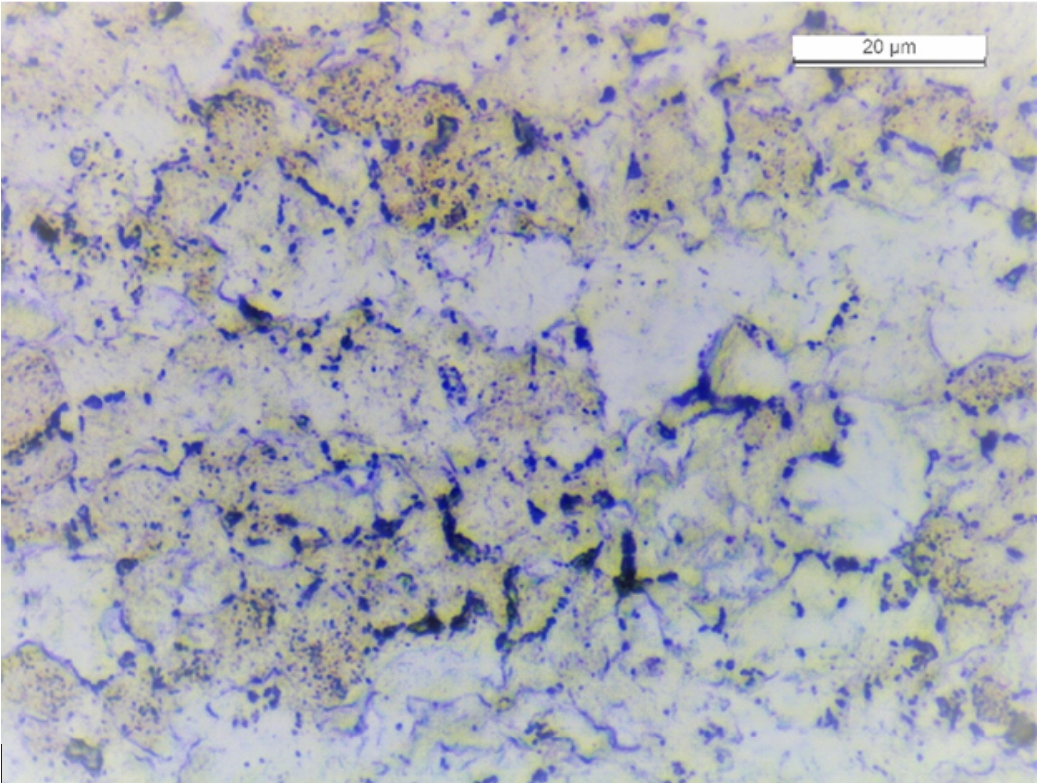
La condizione dei campioni è stata valutata in termini di microstruttura (SEM), spessore, rugosità, porosità, microdurezza, nonché della distribuzione granulometrica (LG) e morfologia delle particelle erodenti.
È emerso come un rivestimento HVOF (High Velocity Oxygen Fuel) in carburo di tungsteno (WC) riesca a raddoppiare la resistenza a usura.
Stato dell’arte
La jet slurry erosion, ossia l’erosione dei materiali (soprattutto metallici) dovuta alla presenza di particelle erosive in flussi liquidi, è un problema ricorrente e comune in varie applicazioni industriali quali turbine idrauliche per centrali idroelettriche, pompe di fango, lavorazione di minerali e tubazioni usati nell’industria petrolchimica.
L’effetto di queste particelle particolate nel liquido rappresenta un grave problema industriale, tale da influire sulla vita dei componenti, ridurre le loro prestazioni, richiedere un’intensa manutenzione preventiva e correttiva, aumentare i costi finanziari e ambientali nel loro complesso.
Pertanto, ogni qual volta si progettano parti che saranno soggette a questa forma di usura erosiva, la corretta scelta dei materiali da utilizzare gioca un ruolo chiave per combattere il fenomeno e assicurare un comportamento tribologico adeguato.
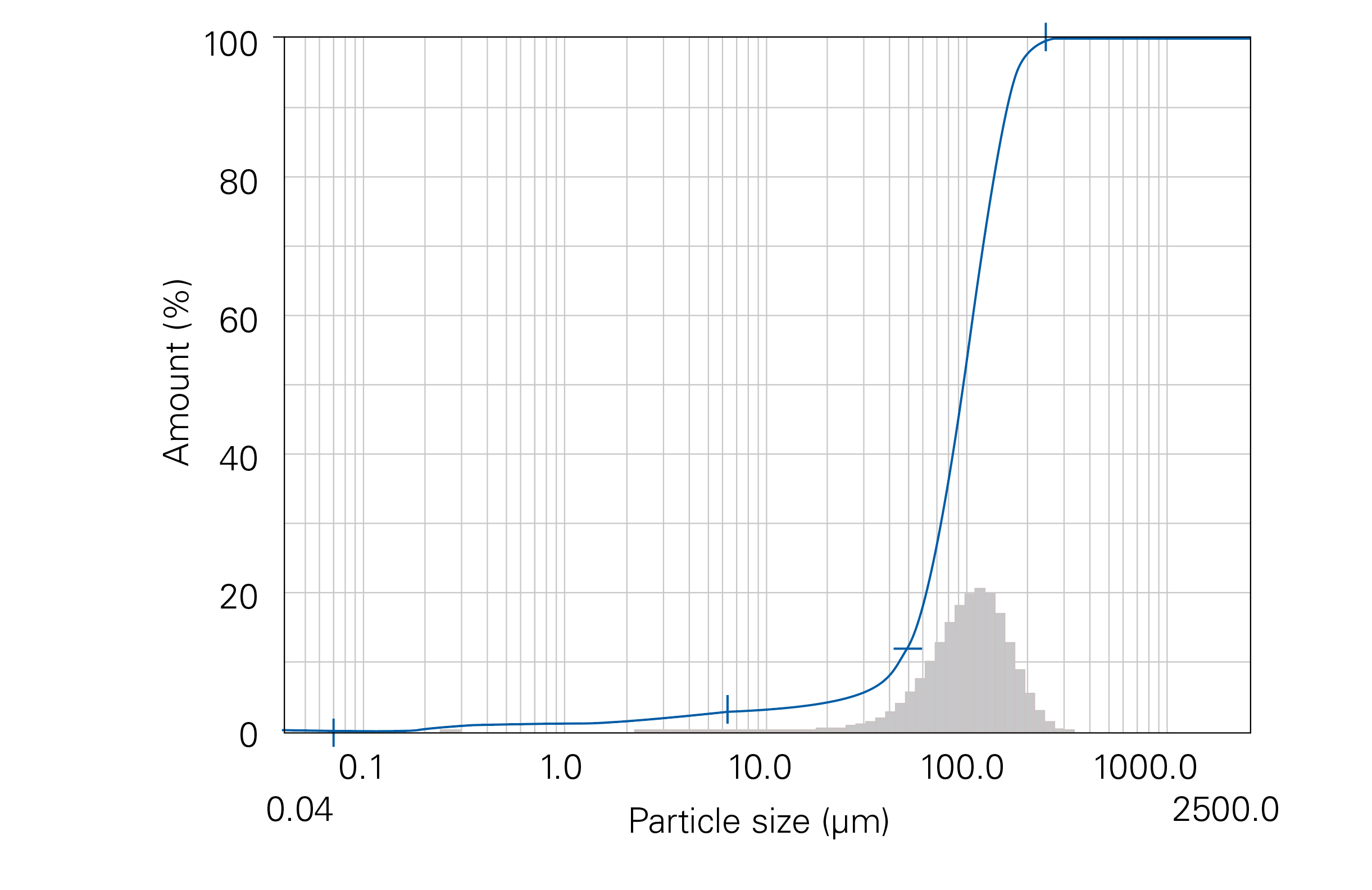
Supportata anche dai più recenti sviluppi, la tecnologia dei trattamenti superficiali e dei rivestimenti con film sottili si dimostra un metodo valido per rispondere in modo efficiente al problema.
Inoltre, lo studio dei meccanismi di usura superficiale resta un passaggio fondamentale per prevedere i guasti fornendo un adeguato supporto metodologico al dimensionamento delle parti.
A tale scopo si fa spesso affidamento alle proprietà dei rivestimenti, come ricavati da modelli ed esperimenti.
Tra i tanti materiali rivestiti, alcuni di quelli che possono risultare di maggiore interesse, data la loro ampia applicazione industriale, sono gli acciai inossidabili martensitici.
Comunemente adottati nell’industria automobilistica, sono anche sempre più utilizzati nella progettazione all’avanguardia di strutture complesse come nel caso di centrali elettriche e reattori nucleari.
Questi inox sono leghe ad alto contenuto di carbonio (0,1-1,2%) con cromo (12-18%) che conferiscono interessanti proprietà quali elevata resistenza, alta tenacità a bassa temperatura, buona resistenza alla corrosione e grande resistenza meccanica rispetto alle particelle erosive (rispetto all’acciaio austenitico).
D’altra parte, anche i materiali cermet hanno mostrato da sempre una eccellente resistenza all’usura erosiva, aumentando la resistenza, ad esempio, delle parti di idro-turbine.
Usati come rivestimenti, sono infatti in grado di migliorare in modo marcato la resistenza di particolari metallici rispetto all’erosione, alla corrosione oppure ad entrambe, specialmente in presenza di alte temperature.
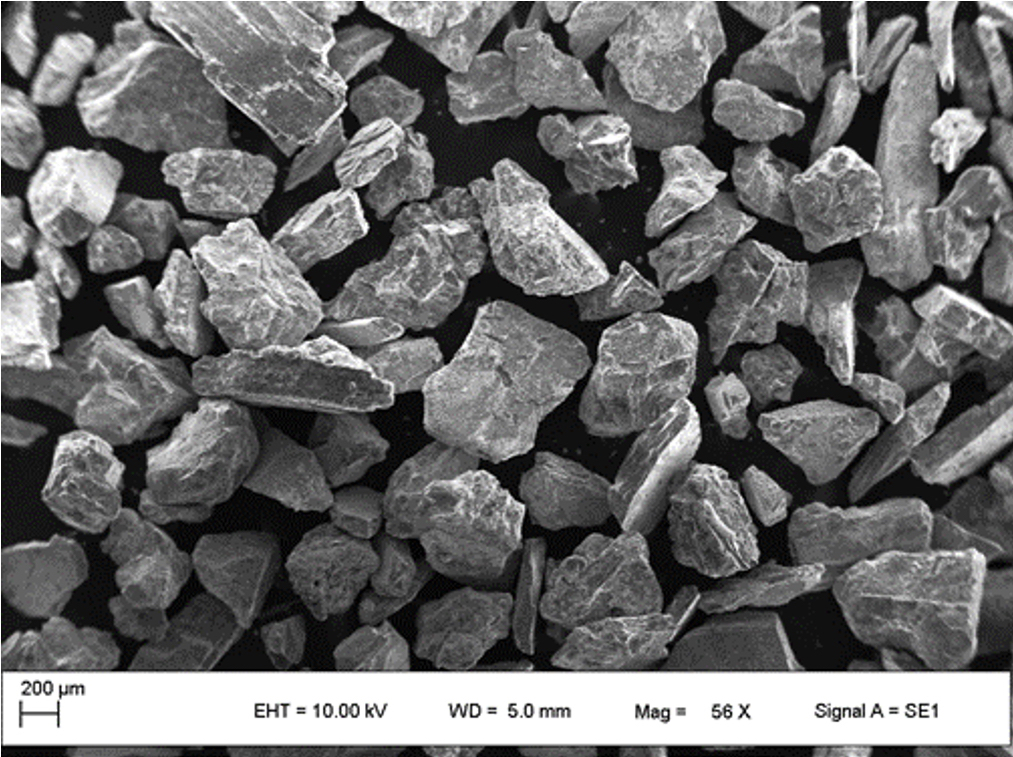
Nello specifico, sono state da tempo dimostrate le migliori proprietà di resistenza all’usura abrasiva offerte dal carburo di tungsteno (WC-Co), che va a coinvolgere anche la resistenza alla corrosione in presenza di piccole aggiunte di cromo (Cr).
La composizione di riferimento per questo WCCoCr è quella costituita da 86% di WC, 10% di Co e 4% di Cr, ampiamente utilizzata, per esempio, nei rivestimenti di elementi idrici per prolungarne la vita operativa.
Tali rivestimenti sono solitamente depositati con processo di verniciatura a spruzzo termico, comunemente conosciuto come HVOF (High Velocity Oxygen Fuel).
Lo stesso processo HVOF ha dimostrato di essere molto efficace per ottenere rivestimenti aderenti e a bassa porosità, mentre le proprietà meccaniche del materiale rivestito sono schermate da rivestimenti con elevate resistenze a compressione e trazione ed elevata durezza.
Tutto questo torna utile nel caso dell’erosione.
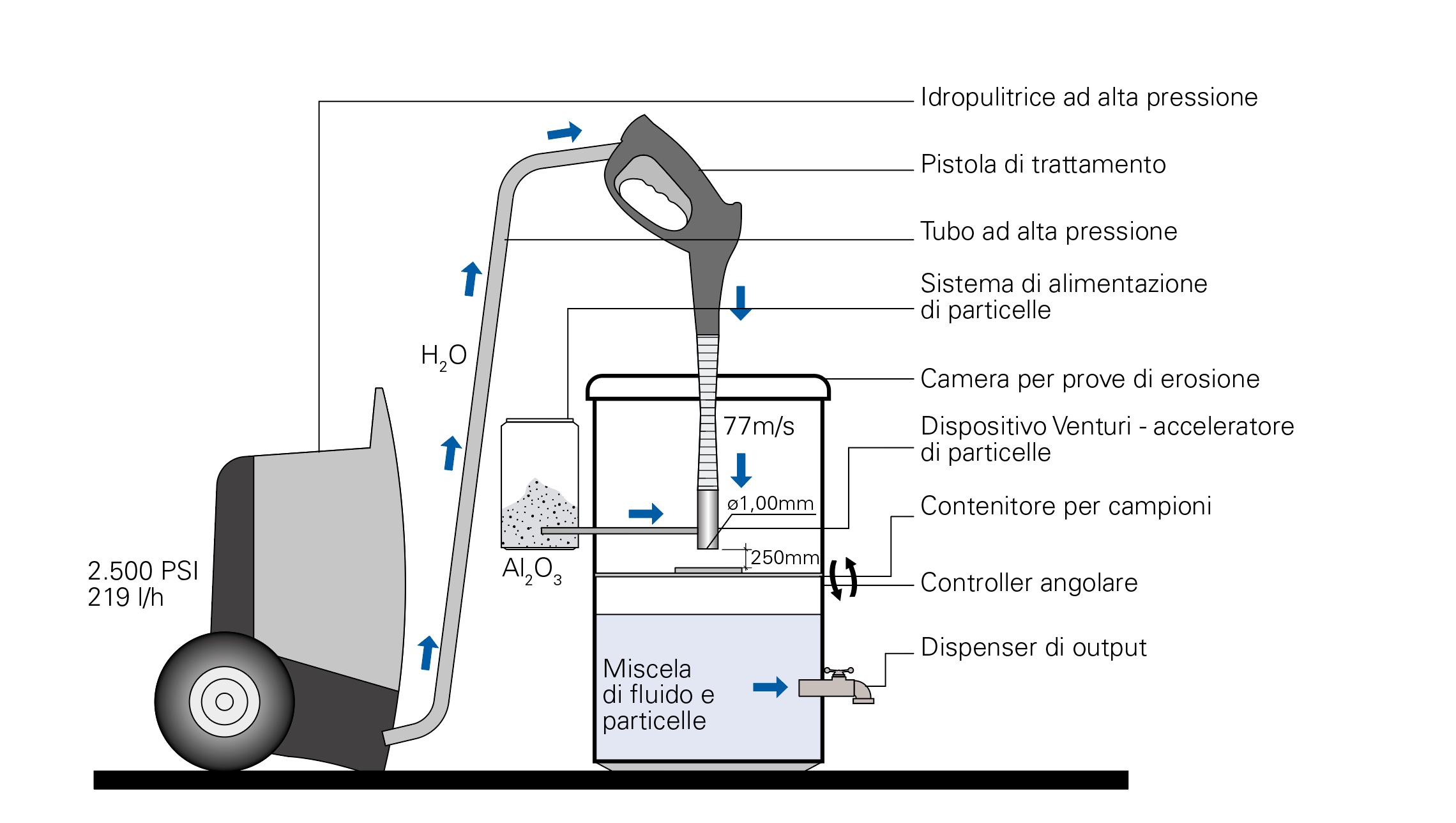
Inoltre, i rivestimenti HVOF possono aumentare la resistenza delle parti anche contro l’erosione da cavitazione-corrosione grazie a diverse sue caratteristiche tra cui l’utilizzo di un’alta velocità che porta a una bassa temperatura di fiamma.
Ciò consente, in pratica, di produrre rivestimenti densi con meno decarburazione e basso contenuto di ossidi.
Materiali e metodi
Materiali e rivestimenti
L’efficacia protettiva del rivestimento è stata valutata su un acciaio inossidabile martensitico bonificato (AISI 410) andando a misurare la perdita di volume in caso di jet slurry per diversi angoli di incidenza (30° e 90°) tra il flusso del fluido e la superficie dei campioni.
Nello specifico sono stati utilizzati cilindri AISI 410 di 30 mm di diametro e 10 mm di altezza. La composizione chimica dell’acciaio è presentata nella tabella 1.
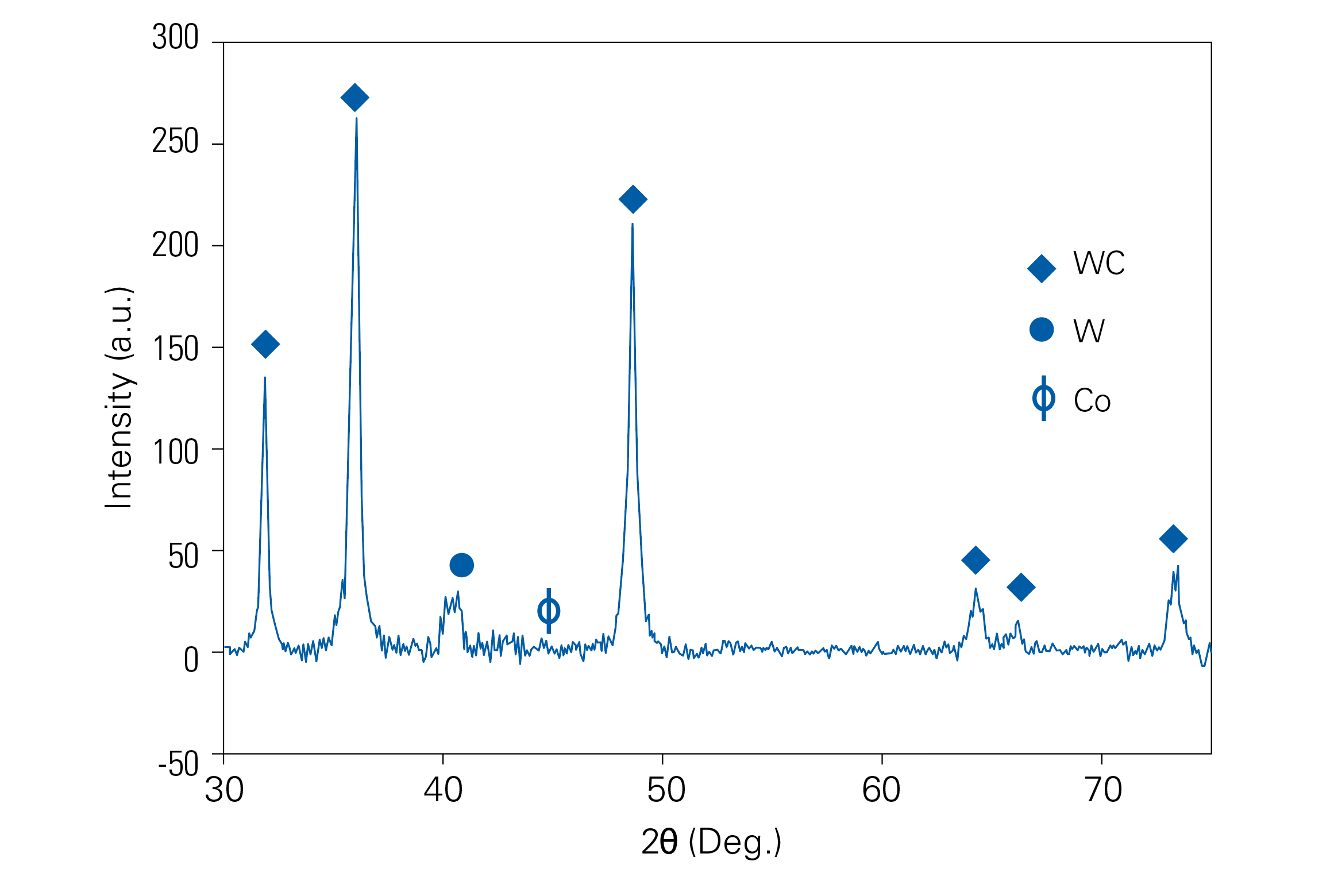
I campioni di acciaio sono stati temprati a 1263 K per 35 min e successivamente temprati in olio a 793 K per 35 min.
La microstruttura ottenuta dopo questa procedura evidenziava martensite con alcuni carburi precipitati sui contorni dei grani che rappresenta un esito tipico dei trattamenti termici di tempra e rinvenimento (fig. 1).
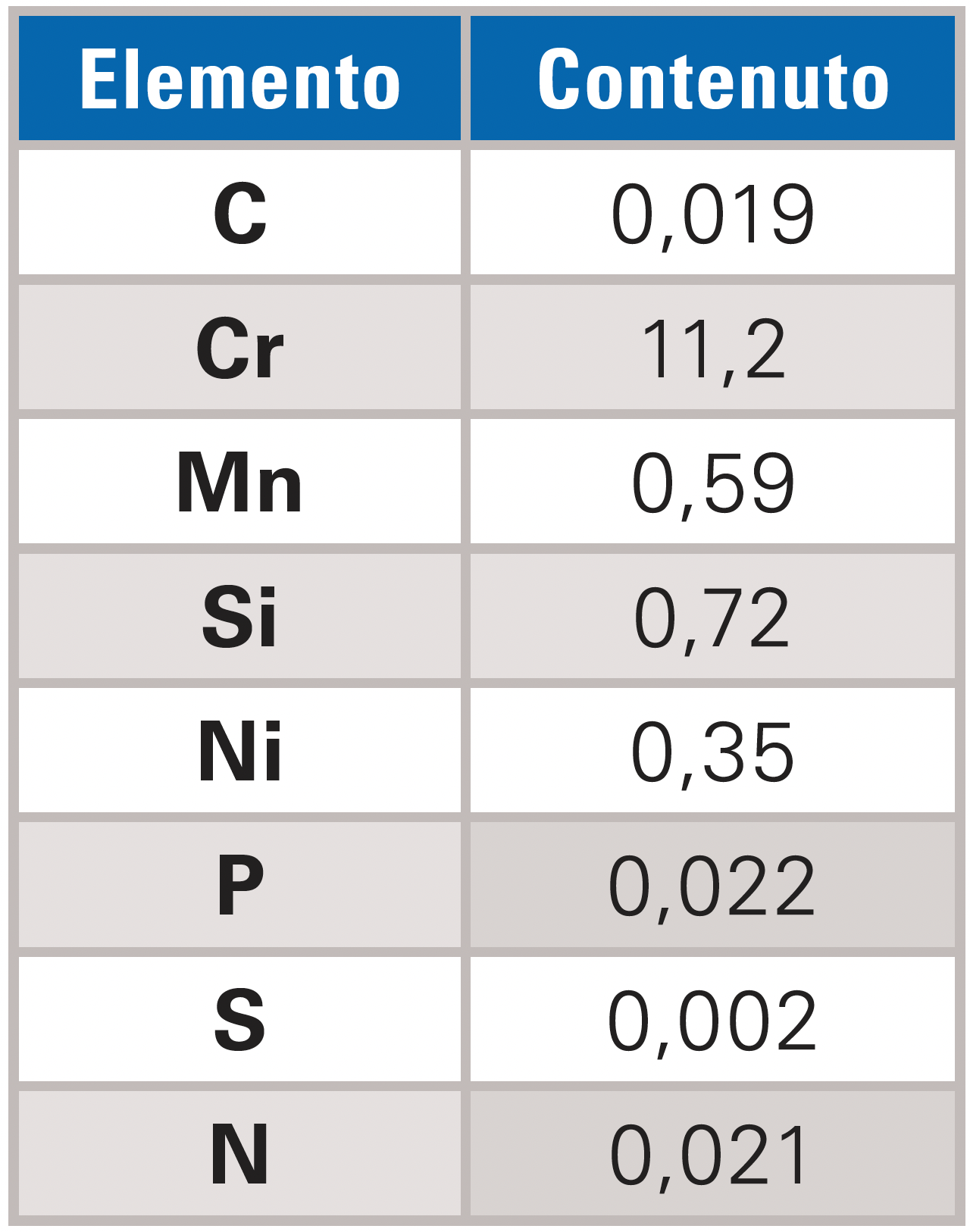
Per il rivestimento sono state utilizzate polveri sferiche WOKA-3653 (86WC-10Co-4Cr) di Oerlikon Metco. La composizione chimica approssimativa della polvere WOKA-3653 è riportata nella tabella 2.
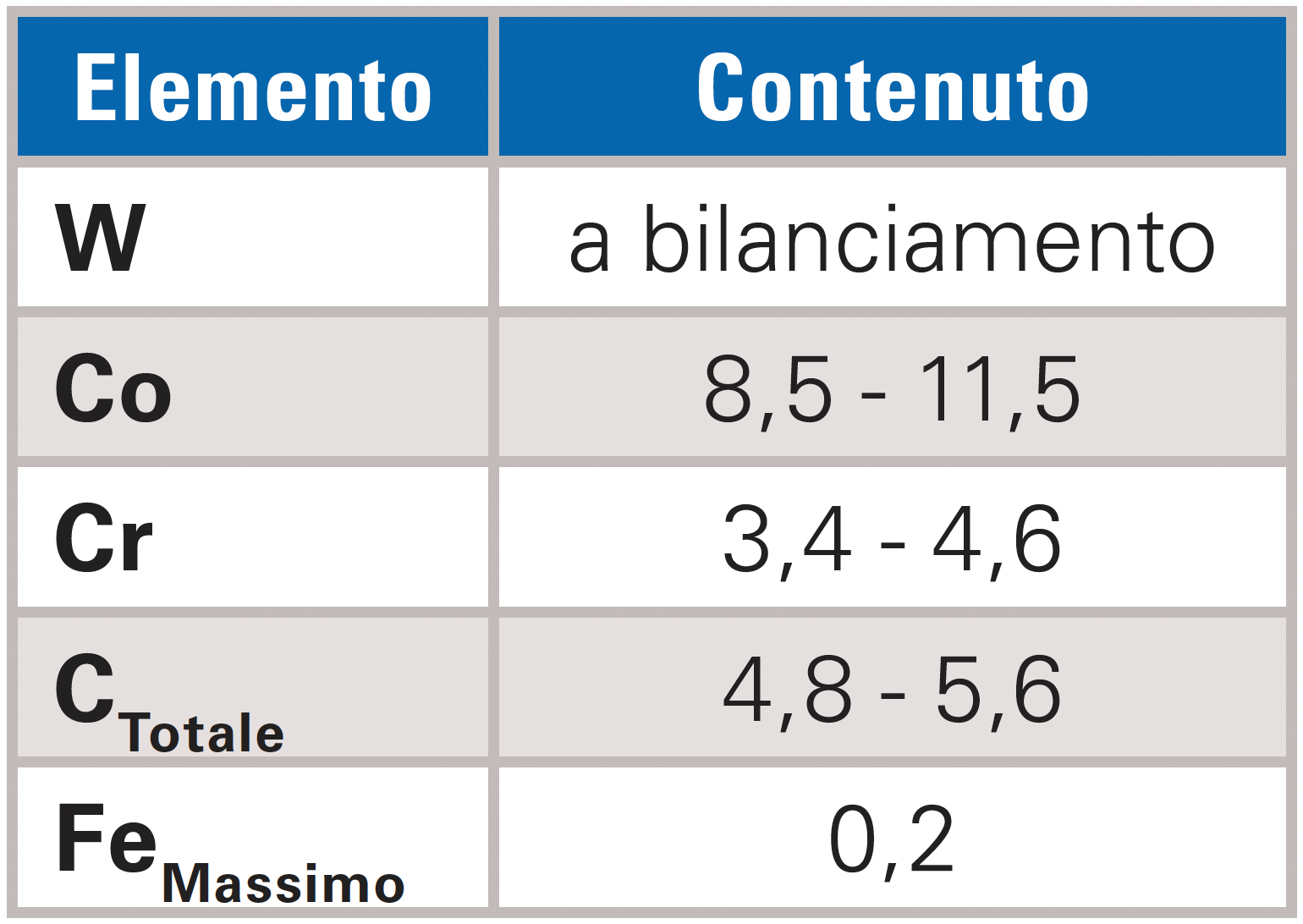
I principali parametri di trattamento HVOF sono riportati in tabella 3.
Processo di erosione
Quale materiale erodente sono state utilizzate particelle di allumina elettrofusa (Al203).
Distribuzione, dimensione e morfologia di queste particelle sono stata individuate mediante granulometria laser (LG).
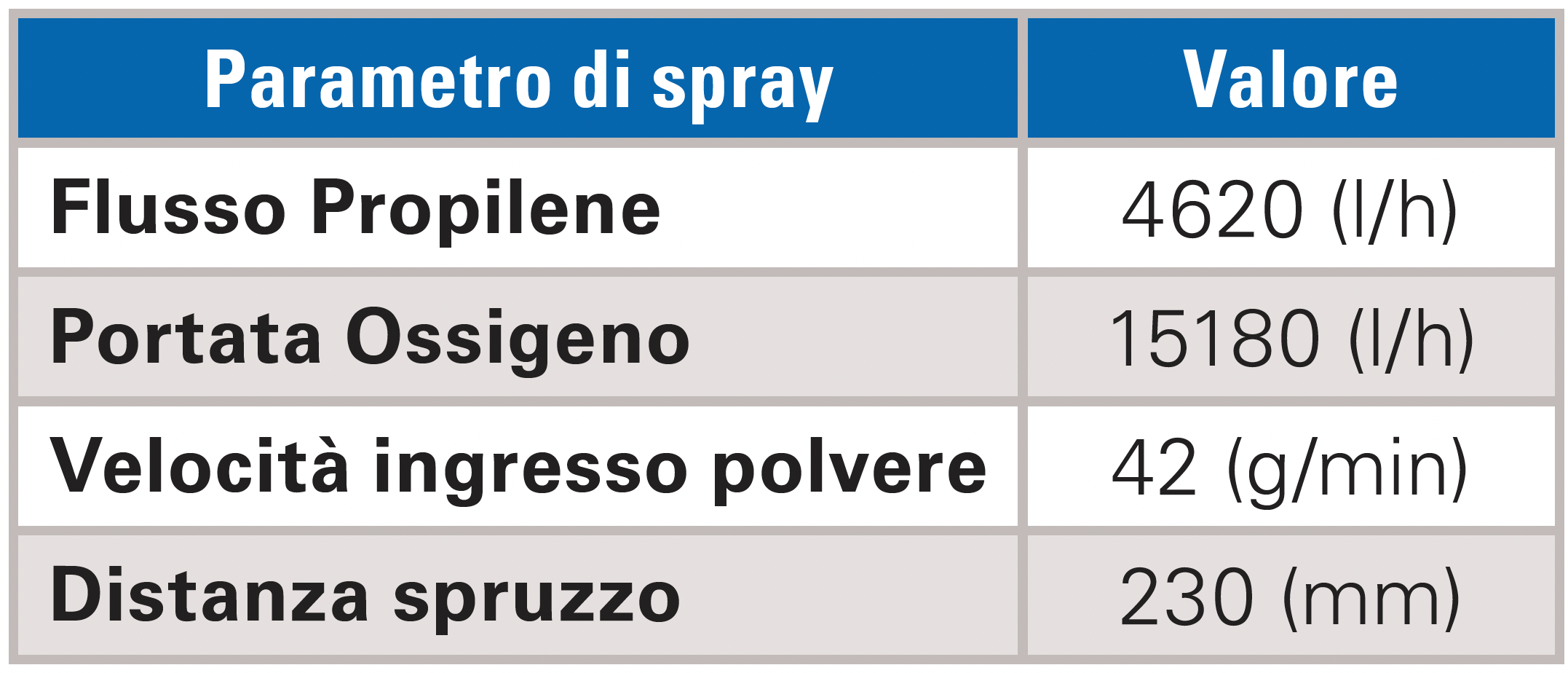
In particolare, è stato utilizzato un analizzatore laser Cilas 1180 che ha operato secondo lo standard ISO 13320:2009.
La distribuzione delle dimensioni delle particelle abrasive è rappresentata in figura 2 e mostra i risultati di una dimensione media delle particelle abrasive di circa 98,55 µm.
Inoltre, le particelle di forma angolare irregolare sono rappresentate dalla micrografia SEM di figura 3.
I test di erosione sono stati eseguiti in un’idropulitrice commerciale modificata basata sullo standard ASTM G-76.
Durante la prova sono stati mantenuti sotto accurato controllo tutti i parametri essenziali di processo.

Un sistema di alimentazione per le particelle erodenti è stato adattato nell’ugello della pistola utilizzando un acceleratore Venturi interno alla camera di prova.
Questa apparecchiatura ha permesso di controllare l’angolo di impatto, la velocità di impatto, la concentrazione di particelle erodenti nella sospensione e della temperatura di prova.
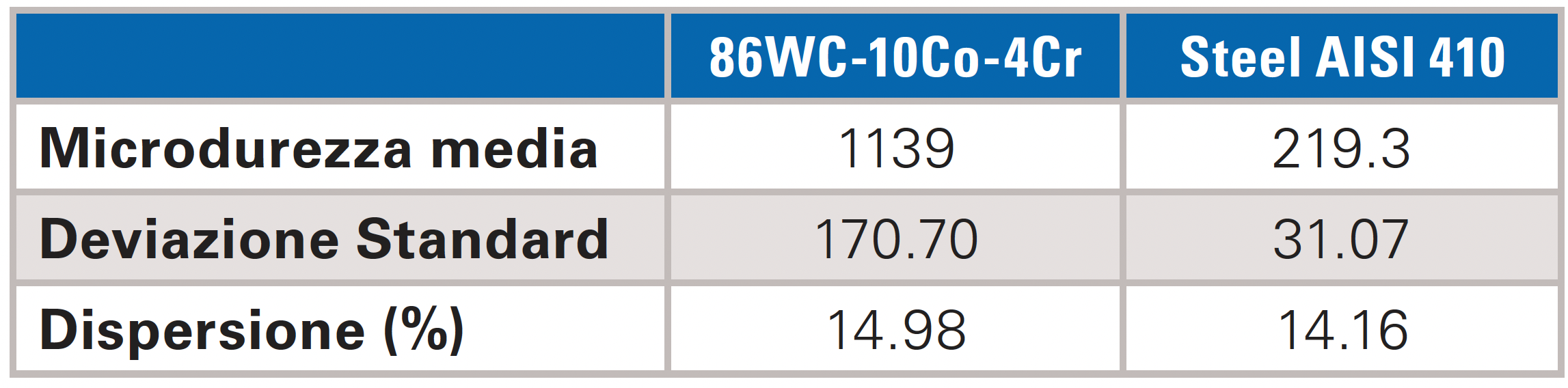
La figura 4 mostra la configurazione di test. Le prove sono state eseguite utilizzando acqua di temperatura compresa tra 25° C e 28° C con 960 g di erodente.
I campioni sono stati posti all’uscita dell’ugello per garantire una incidenza ottimale del fluido, ma anche una certa costanza nella velocità del getto, pari ad un valore medio di 77 m/s per il materiale erosivo in sospensione.
Questa velocità è stata calcolata utilizzando le misurazioni della portata, del tempo e dell’area dell’ugello dell’uscita del flusso. La concentrazione di particelle nella sospensione è stata mantenuta fissa al 7% in peso.
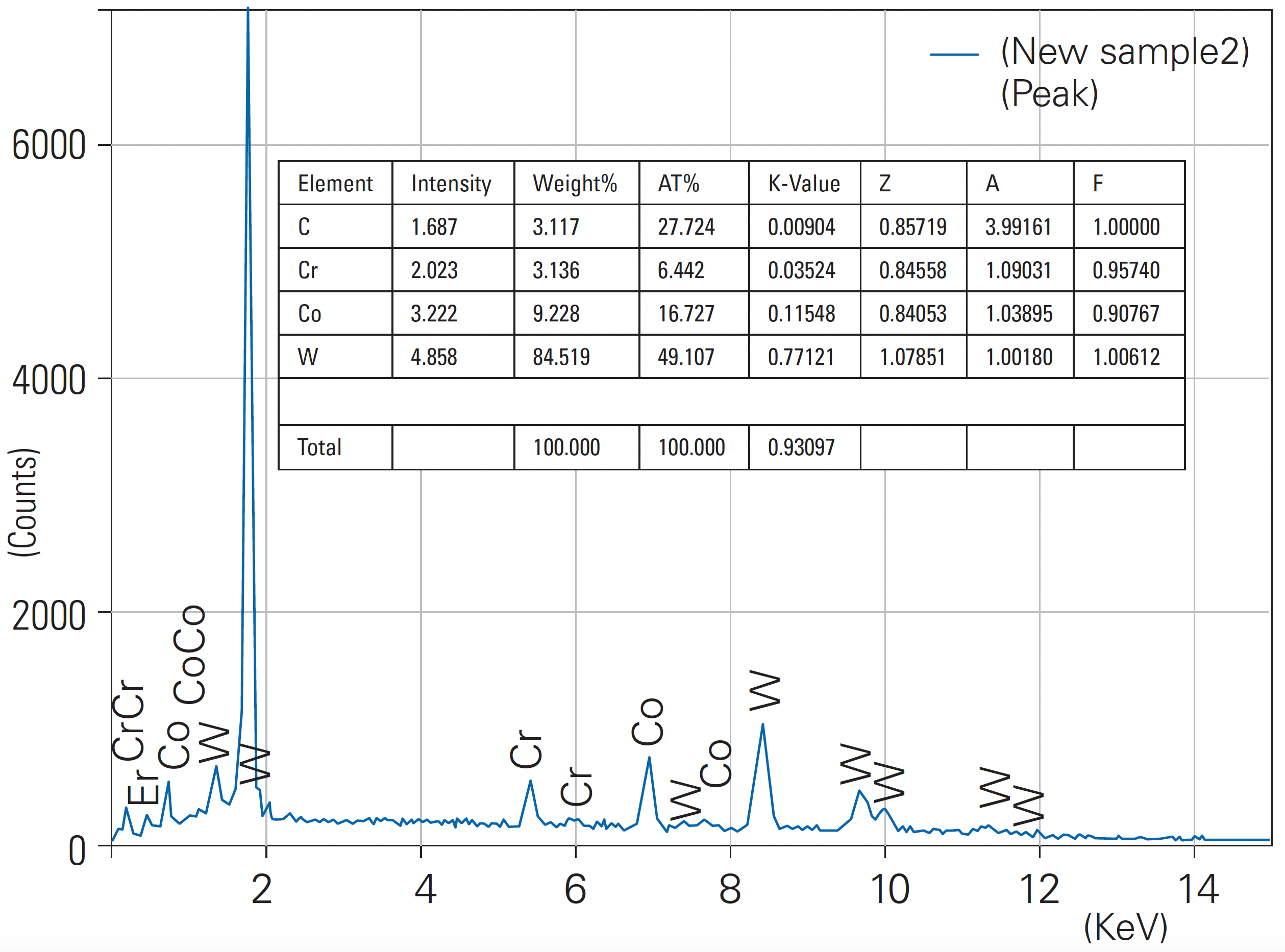
La resistenza all’erosione è stata determinata a partire dalla perdita di volume per unità di tempo, dalla differenza della perdita di massa, considerando la relazione della densità apparente dei materiali studiati (adottando il substrato come 7,73 g/cm3 e il rivestimento come 12,5 g/cm3).
Le perdite di massa sono state misurate ogni minuto utilizzando una scala con risoluzione di 0,01 mg.
La durata totale di ogni test è stata di 4 min. I campioni sono stati puliti in un bagno a ultrasuoni con acqua deionizzata, prima e dopo ogni prova; dopo l’operazione di pulizia, sono stati asciugati e pesati.
Caratterizzazione microstrutturale
L’erosione del materiale è stata valutata mediante misura di spessori, rugosità, porosità, microdurezza.
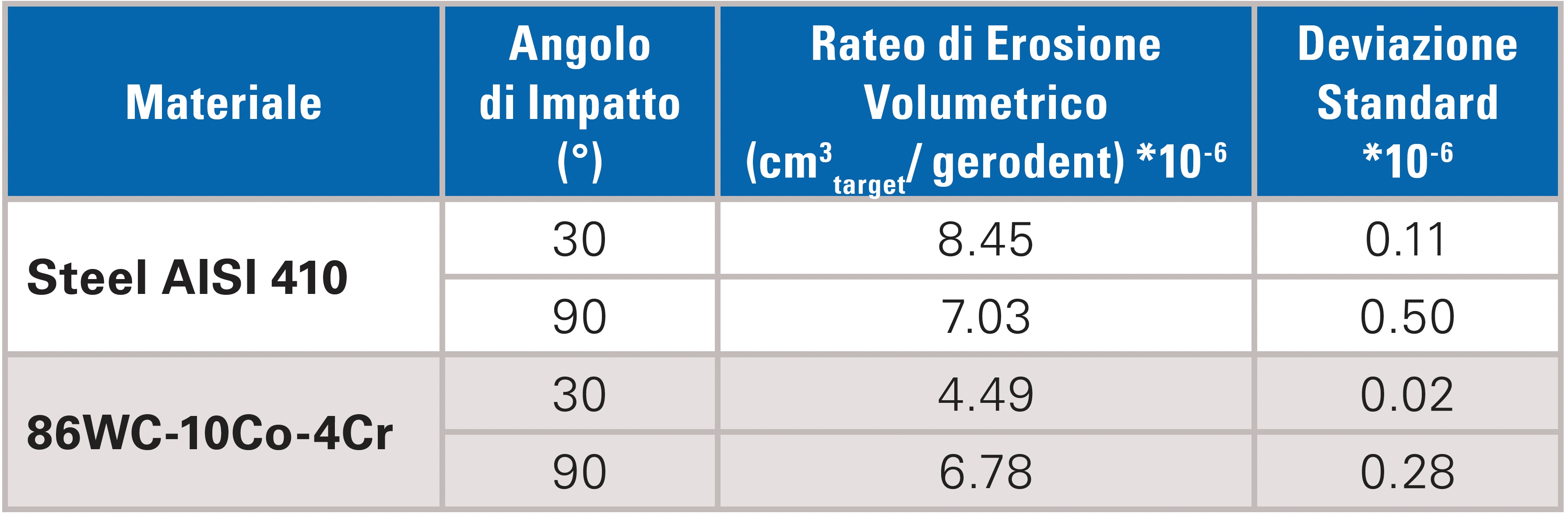
Sono state inoltre utilizzate la microscopia elettronica a scansione (SEM), la diffrazione di raggi X (XRD) e la spettroscopia di dispersione di energia (EDS).
In particolare, la caratterizzazione della microstruttura è stata eseguita utilizzando un SEM EVO MA10 e un microscopio ottico Leica DM2700 M.
La porosità totale dei rivestimenti è stata misurata mediante analisi di immagini digitali secondo lo standard ASTM E2109-01.
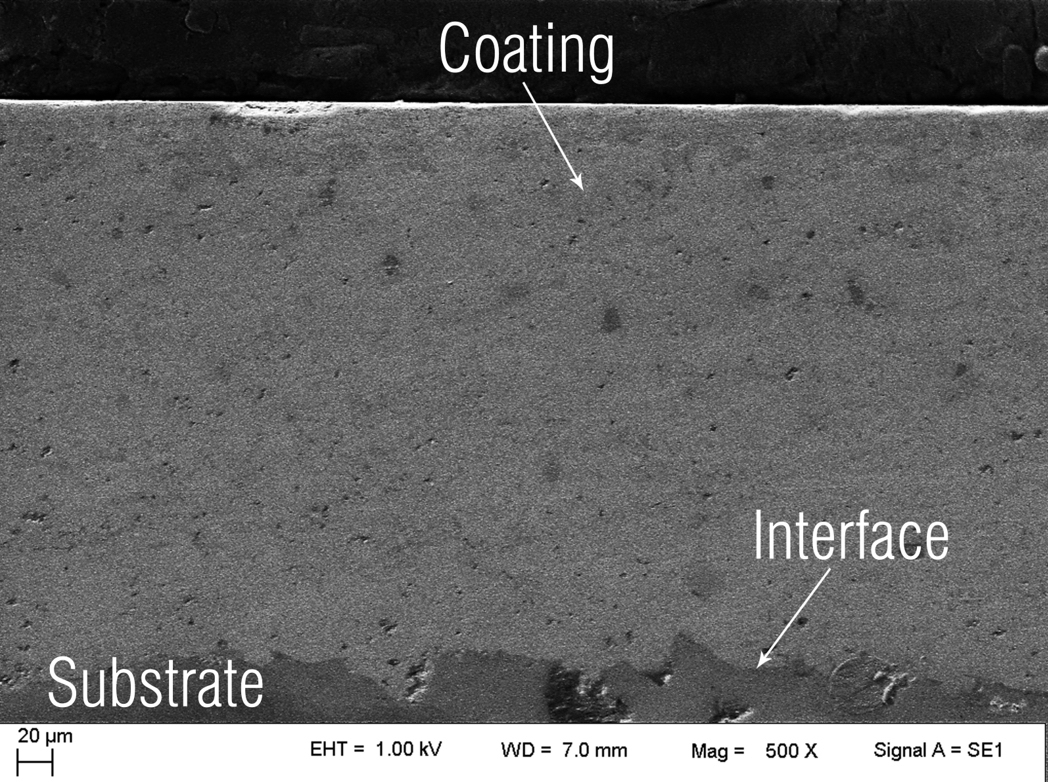
La rugosità superficiale dell’acciaio e dei campioni spruzzati è stata misurata prima e dopo il test utilizzando un Mitutoyo SJ-400.
Le misurazioni della microdurezza Vickers della sezione trasversale sono state eseguite utilizzando un tester di microdurezza Buehler Micromet 2001 (HV300 g, 30 s) secondo lo standard ASTM E-384-11.
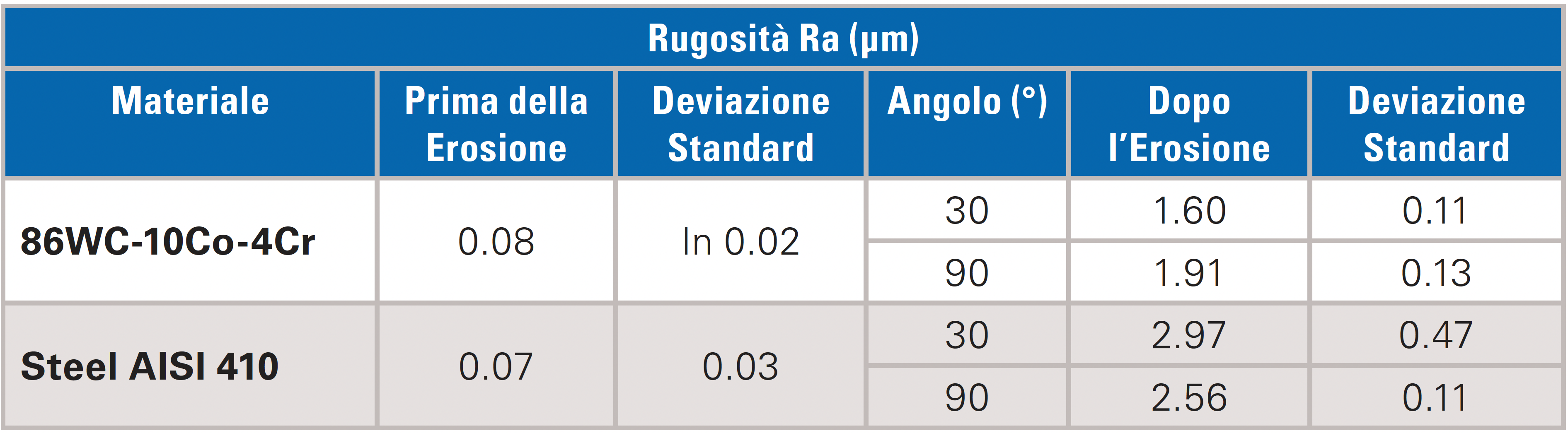
Per identificare le fasi nei rivestimenti e per comprendere la formazione di fase durante la formazione dei rivestimenti, l’analisi XRD della superficie dei campioni spruzzati è stata eseguita utilizzando il diffrattometro a raggi X Philips Xpert MDP con radiazione Cu-K.
Infine, analisi compositive localizzate dei campioni rivestiti sono state eseguite con uno spettrometro Shimadzu SSX-550 EDS accoppiato a EVO MA10 SEM.
Risultati e discussione
Analisi di diffrazione dei raggi X
La figura 5 mostra il pattern XRD del rivestimento 86WC-10Co-4Cr ottenuto da HVOF con la polvere WOKA-3653, dove le fasi WC, W e Co possono essere prontamente identificate.
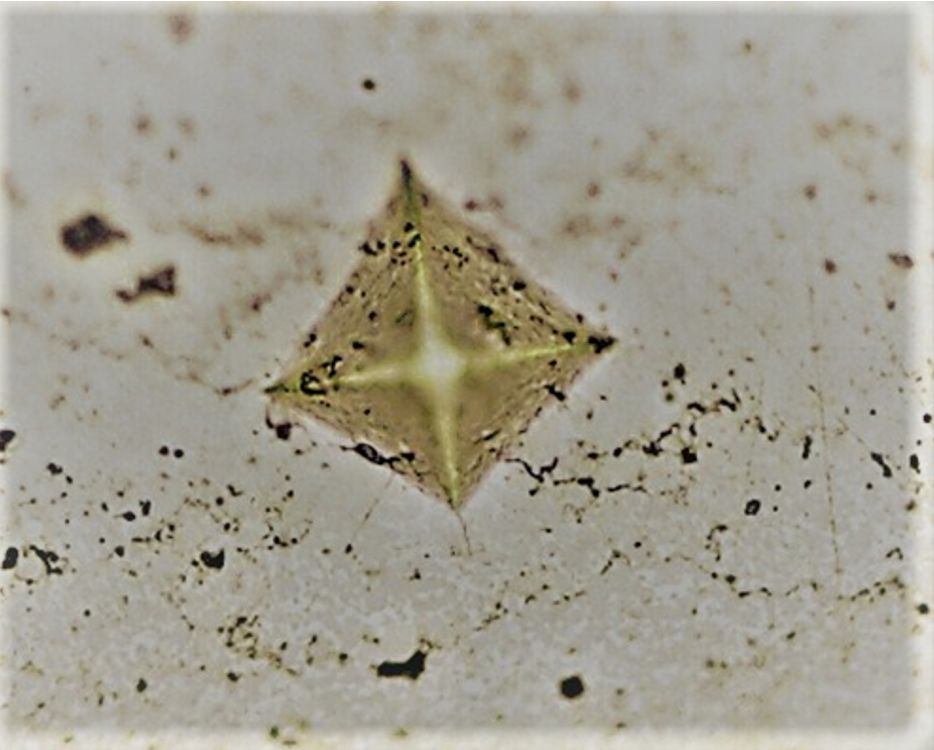
Il pattern XRD mostra che il WC è predominante nel diffrattogramma della polvere.
È inoltre possibile verificare la presenza di W e Co come fasi secondarie formate durante il processo di spruzzatura termica dalla decarburazione delle particelle di WC, riportate anche da altri ricercatori.
Rivestimento per analisi EDS
La figura 6 mostra la regione di microanalisi elementare della sezione trasversale del rivestimento utilizzando il sistema EDS, che evidenzia la presenza di W, Co, Cr e C nei campioni.
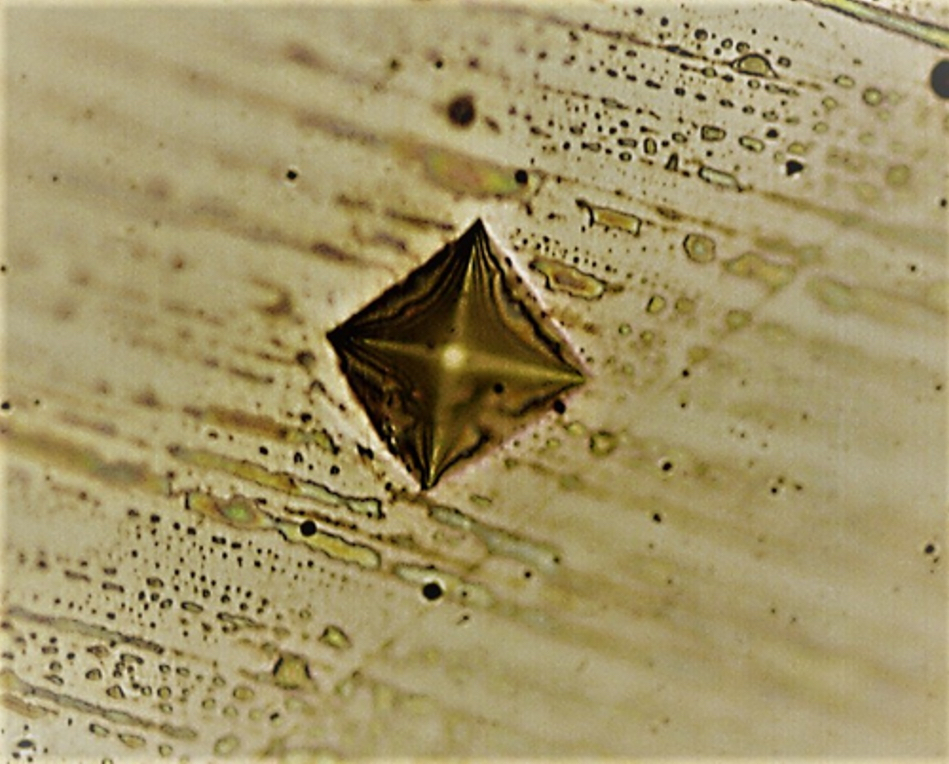
La figura 7 conferma la presenza di questi elementi in uno schema quantitativo che concorda con la figura 5, dimostrando una predominanza del tungsteno.
Risultati simili sono stati trovati considerando rivestimenti con la stessa composizione e tecnica di deposizione.
Proprietà meccaniche dei materiali
La figura 8 mostra la micrografia del rivestimento HVOF 86WC-10Co-4Cr. Presenta una bassa quantità di ossidi, forma continua e microstruttura omogenea, con bassa presenza di fessure e pori.
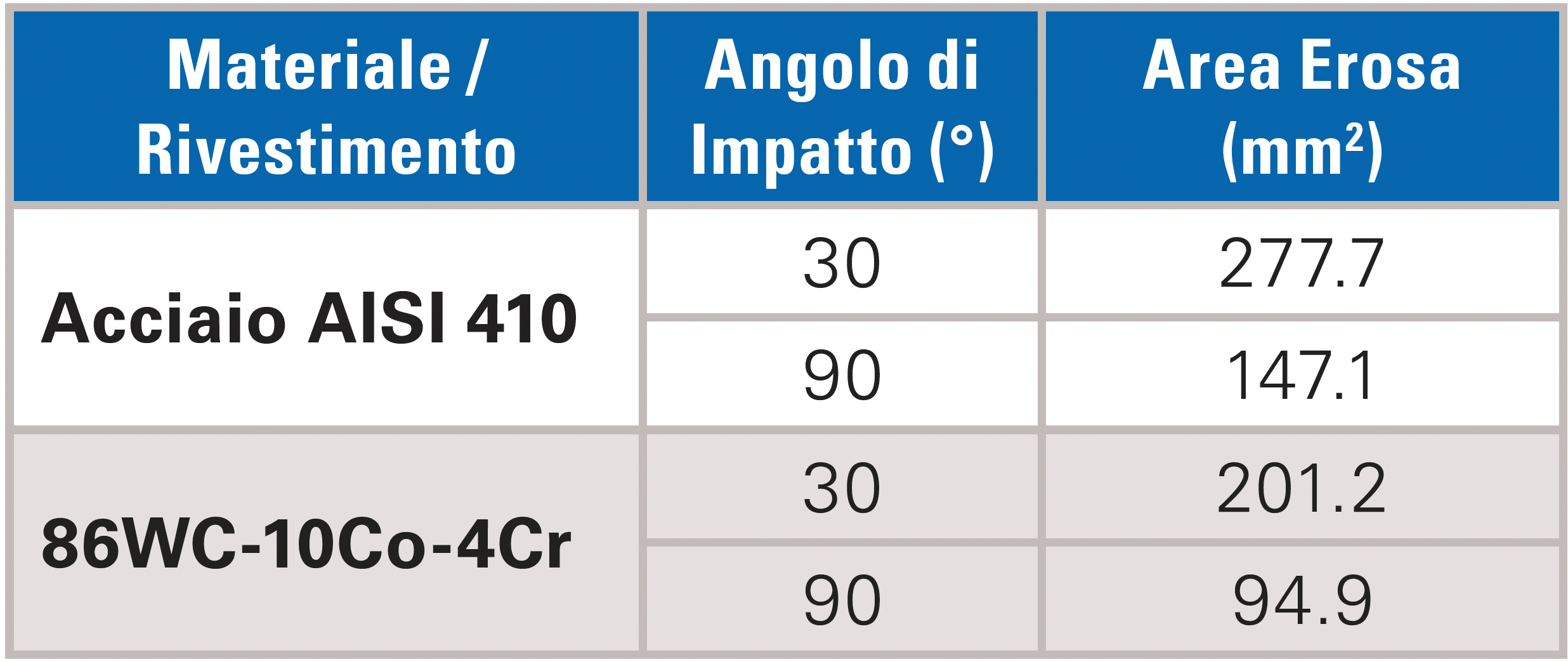
Non è possibile distinguere nessuna struttura lamellare. Ciò può essere spiegato dalla fusione delle particelle WC-Co-Cr, che induce una migliore distribuzione nel materiale di rivestimento.
Lo spessore medio del rivestimento HVOF 86WC-10Co-4Cr è stato calcolato utilizzando micrografie di sezioni trasversali elaborate nel software ImageJ e tra 100 e 200 misurazioni sono state eseguite su diversi campioni per ottenere una media aritmetica di circa 227 µm.
Tre analisi di tre campioni di rivestimento sono state misurate tramite analisi di immagine digitale secondo ASTM E2109-01, ottenendo una porosità media dello 0,7%, che è considerata accettabile entro i valori presentati in letteratura e secondo il criterio specificato dal produttore Oerlikon Metco di una porosità media inferiore all’1,0%.
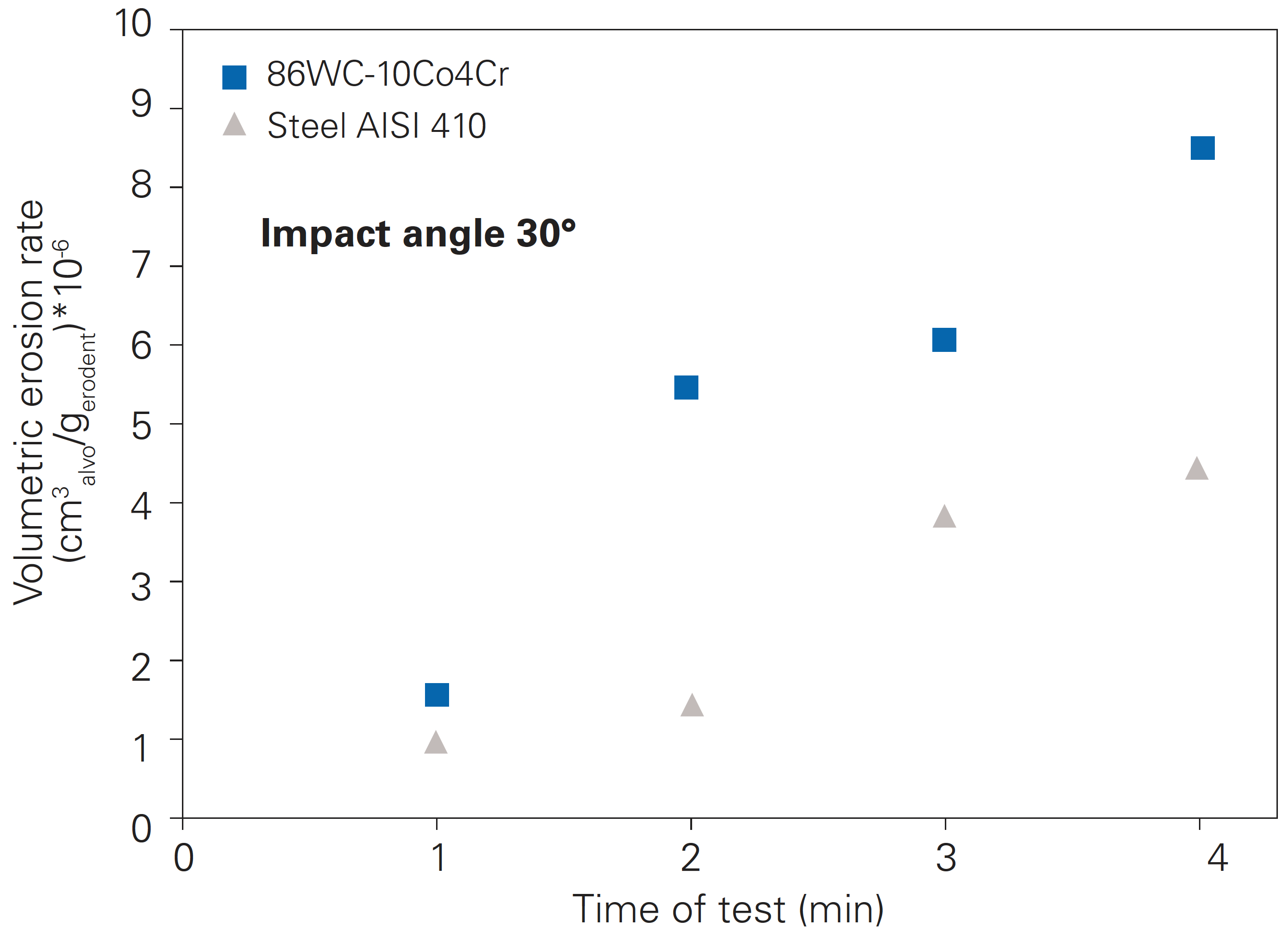
La microdurezza riflette la microstruttura e le proprietà fisiche e meccaniche sia del substrato che del rivestimento, che a loro volta dipendono dai materiali e dai processi impiegati nella loro fabbricazione.
La durezza è una proprietà che può essere considerata variabile in tutto il rivestimento in determinate zone, a causa di eventuali eterogeneità del materiale.
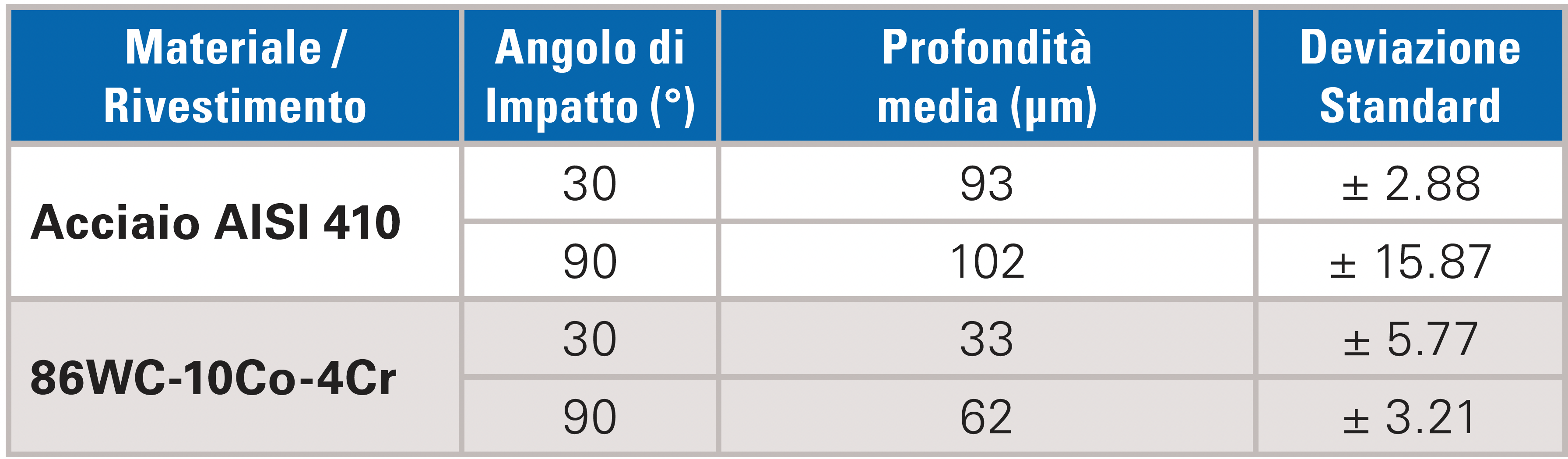
Per questo motivo, quando si misura questa proprietà, è necessario considerare la preparazione della superficie, la sezione analizzata, nonché il numero di rientranze eseguite.
Il valore di durezza del rivestimento è compatibile con la letteratura, in accordo con le specifiche del produttore della polvere di rivestimento (da 750 a 1450 HV0.3).
In base ai valori di microdurezza lungo la sezione trasversale del rivestimento a spruzzo, si sono avute variazioni dovute alla non uniformità delle fasi.
È stato dimostrato che è possibile osservare questo effetto lavorando con sottostrati (rivestimenti spruzzati), una volta che i valori di microdurezza possono variare poiché ogni punto di indentazione può essere posizionato in diverse microstrutture, in questo caso, carburi, ossidi, inclusioni e la matrice stessa.
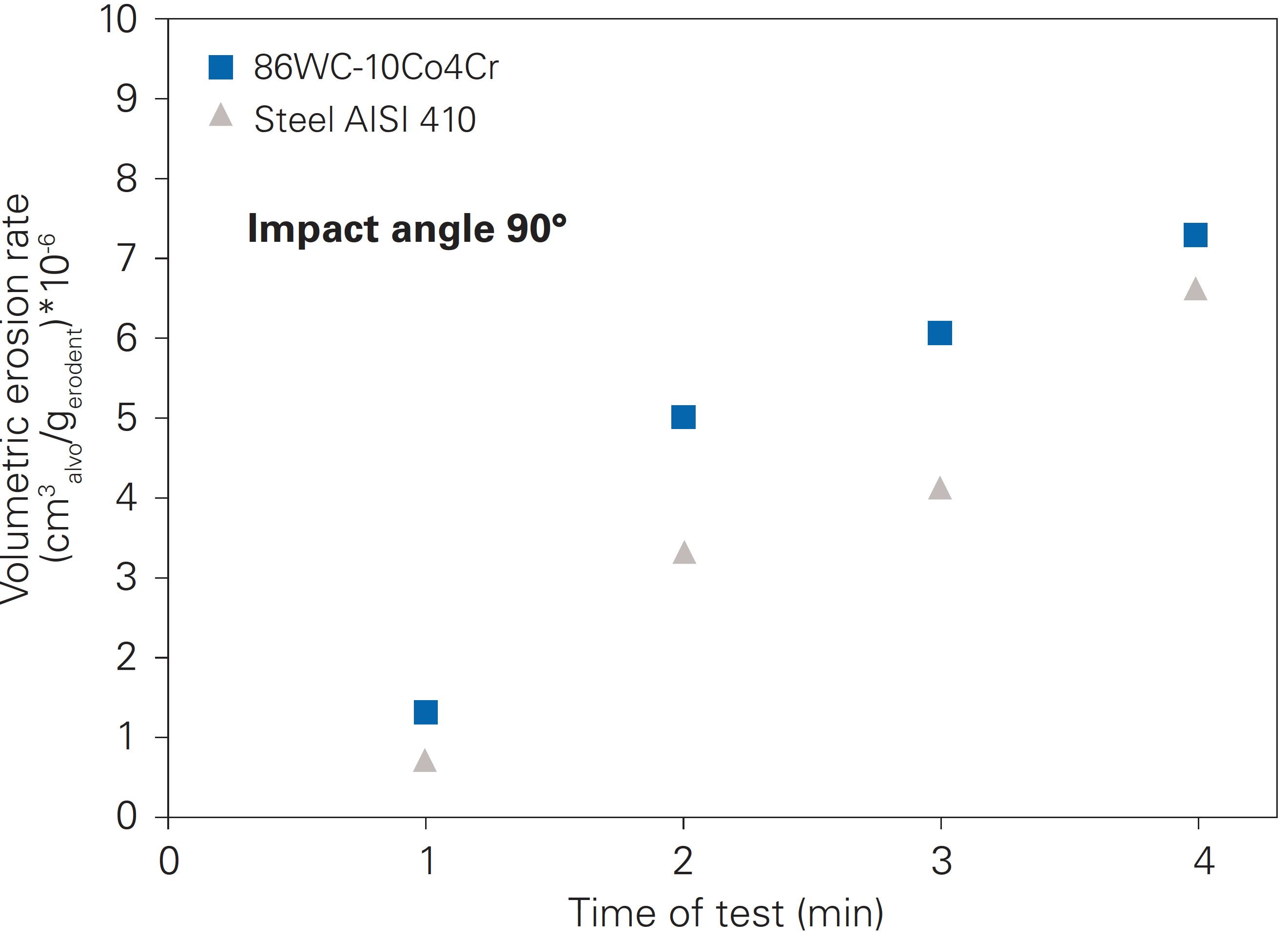
A questo proposito Trelleborg descrive i materiali a base di WC come compositi metallo-ceramica in cui i valori di microdurezza trovati sono associati a ciascun microcostituente.
A sua volta, la microstruttura dipende da fattori quali la composizione di ogni fase, la morfologia della polvere, la tecnica dello spray e la porosità.
La figura 9 mostra la rientranza eseguita sul rivestimento 86WC-10Co-4Cr, dove si osserva la presenza di piccoli grani e la forma dei quattro angoli della rientranza.
Questo punto aveva il valore più alto di microdurezza per il rivestimento (1448 HV0.3), essendo anche il più vicino alle specifiche del produttore.
Altri hanno ottenuto risultati simili di 1297 ± 45 HV0.3 e 1256 HV, rispettivamente, per i rivestimenti WC-CoCr spruzzati con HVOF.
Allo stesso modo, ad esempio, sono stati riportati valori di microdurezza di 1031 ± 99, 1180 ± 70, 1118 ± 131 e 1106 HV0.3 per rivestimenti spray simili applicati con la stessa tecnica.
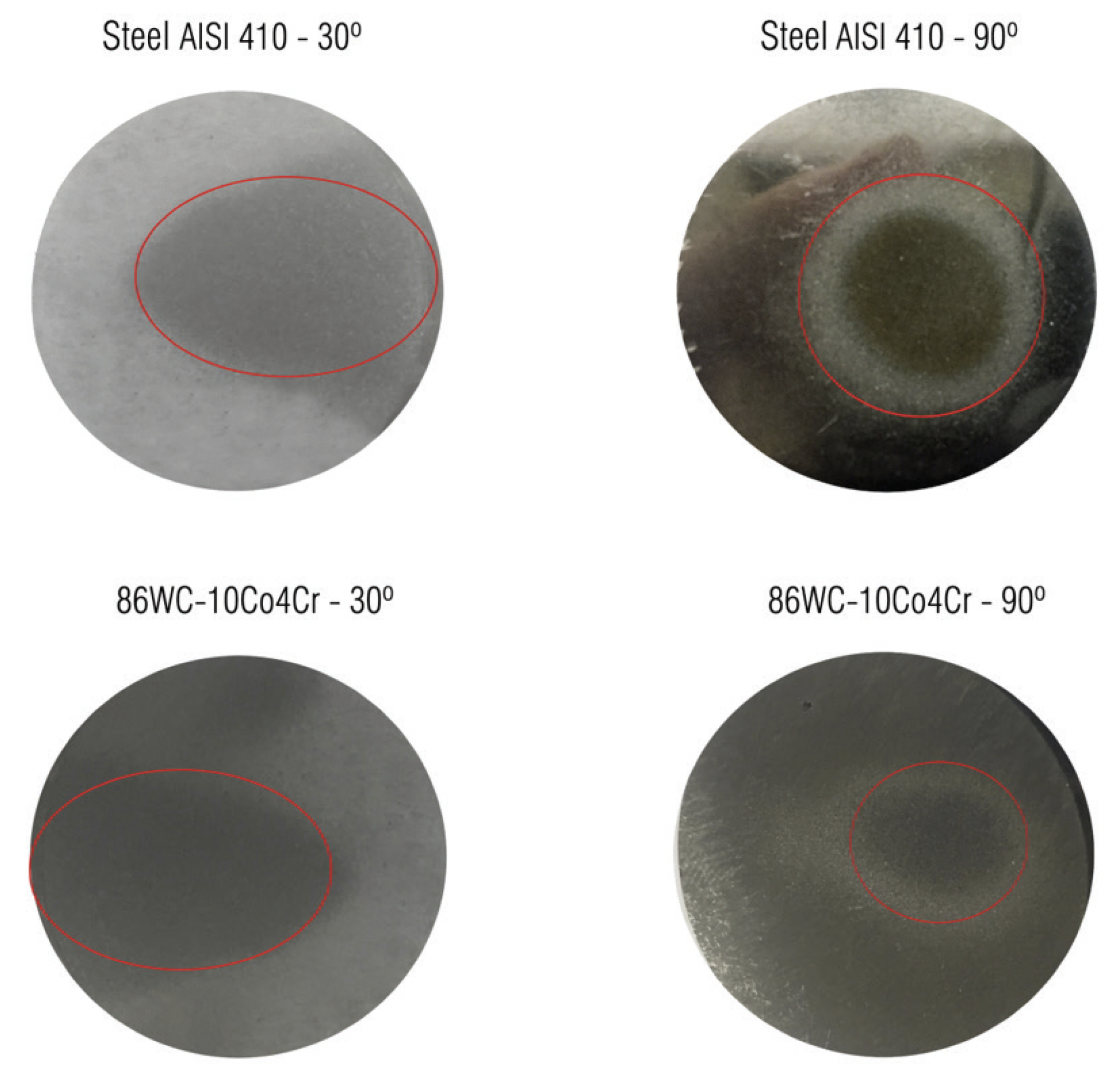
La figura 10 mostra la dentellatura eseguita sul substrato, corrispondente all’acciaio inossidabile martensitico trattato termicamente.
Il valore di microdurezza misurato è stato di 219 HV0.3, ancora una volta molto simile a quello riportato da altri di 199 HV0.3.
La tabella 5 mostra il tasso di erosione accumulato in massa di erodente in perdita di volume dei campioni testati, in funzione dell’angolo di impatto, in un tempo totale di 4 minuti, sia per il substrato che per il rivestimento.
Le figure 11 e 12 evidenziano come l’acciaio mostri un’usura erosiva molto più elevata a un angolo di impatto di 30° rispetto a 90°, dimostrando un comportamento duttile con un meccanismo di rimozione del materiale predominante, come riportato in letteratura.
Inoltre, molti autori confermano che i metalli presentano un tasso di erosione maggiore ad angoli inferiori.
La figura 12 mostra anche che, per l’angolo di impatto di 90°, il rivestimento in carburo di tungsteno presentava una velocità di erosione volumetrica accumulata leggermente inferiore a quella dell’acciaio inossidabile martensitico.
D’altra parte, confrontando le figure 11 e 12, si può vedere che il rivestimento presenta una maggiore usura erosiva ad un angolo di impatto di 90° rispetto a 30°, indicando un comportamento fragile di quel rivestimento.
Ciò è dovuto all’azione ripetuta delle particelle erosive perpendicolari impattate sulla superficie, producendo microfratture che contribuiscono all’usura del WC in metallo duro e determinando la sua eventuale rimozione, in accordo con i risultati riscontrati in altre indagini.
La figura 13 mostra in dettaglio le aree erose dei materiali sottoposti alla prova di jet slurry per gli angoli di impatto di 30° e 90°.
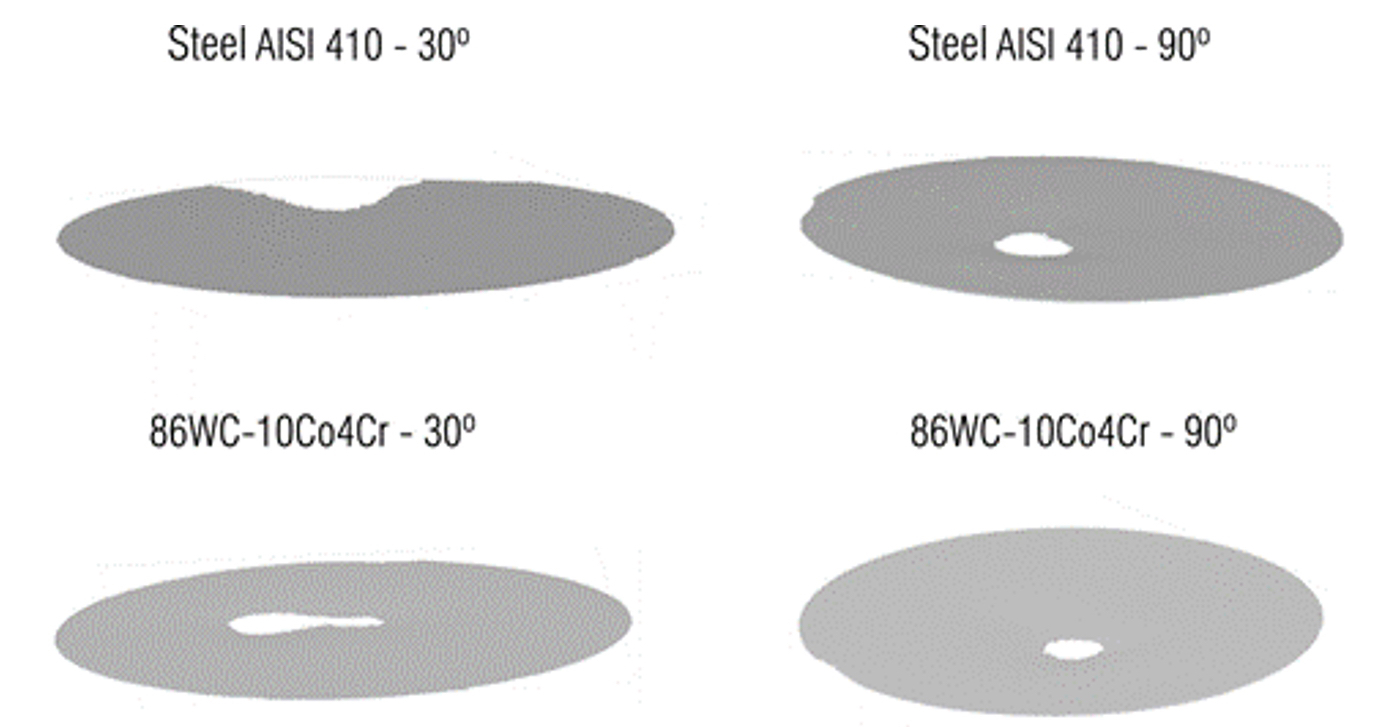
Si osserva che la regione erosa dei pezzi (evidenziata in rosso) per l’angolo di 30° ha forma allungata e maggiore area erosa.
L’erosione dei provini testati a 90° è più localizzata, ha un’area minore e una profondità maggiore.
Si può osservare la formazione dell’anello concentrico, noto anche come “erosione ad alone”, che è una caratteristica meccanica del danno dovuto allo sviluppo di crateri che appaiono come macro fosse sulla superficie per questo angolo.
La rugosità di queste regioni erose è mostrata nella tabella 6.
La tabella 7 mostra le aree erose in funzione dell’angolo di impatto.
Si osserva che l’area è maggiore per l’angolo di impatto di 30°. Rispetto al substrato, il rivestimento presentava aree erose più piccole per i due angoli di impatto studiati.
La figura 14 mostra la scansione tridimensionale dei campioni, con la quale è stato possibile stimare la profondità media di erosione della tabella 8.
Come previsto, dato che i test a 90° hanno portato ad aree usurate più localizzate, la loro profondità è superiore a campioni testati a 30°.
È stato infine condotto uno studio di erosione in tubi di acciaio, variando sia l’angolo di impatto che la velocità, ottenendo aree di erosione significativamente più profonde per 90° rispetto a 30°, a sostegno dei risultati qui trovati.
Allo stesso modo, è stata studiata la resistenza dell’acciaio inox AISI 420 sottoposto a prove di erosione particellare utilizzando due differenti abrasivi agli angoli di incidenza di 30°, 45°, 60° e 90°.
I loro risultati hanno anche dimostrato che i campioni valutati a 90° presentavano un profilo di profondità maggiore rispetto a quelli di 30° testati indipendentemente dall’abrasivo adottato.
Conclusioni
Questa indagine ha studiato l’effetto di erosione che particelle di allumina disciolte in liquido hanno sul rivestimento in carburo di tungsteno (86WC-10Co-4Cr) di un acciaio inossidabile martensitico (AISI 410) arrivando alle seguenti conclusioni:
• È stata sviluppata un’apparecchiatura sperimentale di simulazione del fenomeno conosciuto come jet slurry erosion, che ha permesso un controllo accurato dei parametri di prova come angolo di impatto, velocità di impatto, concentrazione di particelle erosive nella sospensione e temperatura di prova. Queste variabili sono tutte significative nella determinazione delle proprietà meccaniche e del comportamento dei materiali quando sottoposti alle condizioni proposte da questa indagine.
• Il rivestimento in carburo di tungsteno ha offerto una maggiore resistenza all’erosione rispetto all’acciaio inossidabile martensitico, probabilmente per merito della bassa porosità, della durezza delle particelle WC e delle migliori proprietà della matrice del materiale legante CoCr. Pertanto, l’applicazione di tale rivestimento può essere considerata vantaggiosa per incrementare la resistenza strutturale del substrato in applicazioni in cui l’acciaio è soggetta a condizioni erosive simili.
• L’elevata concentrazione di WC-Co nella miscela di rivestimento favorisce una maggiore connettività nella fase dura, portando a una maggiore resistenza meccanica e di resistenza all’erosione.
• L’acciaio inossidabile martensitico ha presentato un tasso più elevato di erosione volumetrica accumulata nell’angolo di impatto di 30° che denota un comportamento duttile. D’altra parte, la velocità di erosione volumetrica accumulata per il rivestimento in carburo di tungsteno era maggiore all’angolo di impatto di 90°, indicando un meccanismo di rottura prevalentemente fragile.
• Per l’angolo di impatto di 30°, il rivestimento in carburo di tungsteno ha presentato un tasso di erosione volumetrica cumulativa di circa il 50% inferiore rispetto all’acciaio inossidabile martensitico.
Ringraziamenti
Un ringraziamento speciale per i colleghi Cristiano Fragassa e Felipe Vannucchi De Camargo per il supporto fornito nella realizzazione della presente pubblicazione.
di Galileo Santacruz, Antonio Takimi, Carlos Pérez Bergmann