La trasformazione digitale di SKF inizia dall’Italia. Lo stabilimento di Cassino (FR) è un punto di riferimento per la digitalizzazione di SKF. Un sito produttivo a elevata innovazione, dove è al lavoro il primo algoritmo proprietario di machine learning e un’infrastruttura avanzata di monitoraggio.
La strada di SKF verso l’Industry 4.0 passa da Cassino. Lo stabilimento laziale svolge oggi un ruolo guida in ottica di digitalizzazione. I progetti sviluppati qui vengono spesso utilizzati per tracciare le linee guida da adottare successivamente a livello globale.
Il percorso della trasformazione dello stabilimento di Cassino ha avuto inizio nel 2018 con il progetto pilota Digital 2Win, con il quale sono state poste le basi per il completamento della digitalizzazione dell’intera officina definendo gli standard da esportare negli altri stabilimenti del Gruppo.
Il progetto si è posto l’obiettivo di accrescere competitività e redditività attraverso la gestione del processo produttivo in remoto, l’Industrial Internet of Things, l’integrazione delle interfacce-operatore con i sistemi di pianificazione e tracciabilità e l’autonomia nel setup di linee integrate. Un’iniziativa ambiziosa, che ha richiesto un enorme patrimonio di competenze digitali e un radicale cambio di mentalità dell’intero stabilimento.
Spazio agli algoritmi di machine learning
L’integrazione del machine learning all’interno dello stabilimento di Cassino ha avuto inizio a settembre 2020 con la raccolta di numerosi parametri operativi di produzione, qualità, condition monitoring, manutenzione, tracciabilità qualitativa e quantitativa dei componenti.
Il team dedicato ha individuato, tra i 200 parametri monitorati 24 ore al giorno per 7 giorni, i 30 a maggiore impatto sul livello di silenziosità del cuscinetto con l’obiettivo di raggiungere gli standard più elevati di silenziosità per cuscinetti radiali rigidi a sfere.
Oggi i nuovi algoritmi SKF permettono di svolgere in modo automatizzato l’analisi di milioni di dati raccolti ogni giorno.
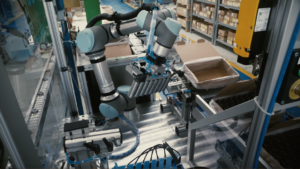
Gli algoritmi sono stati implementati a Cassino perché il machine learning può essere adottato dove i dati sono già gestiti in modo digitale: “Il machine learning ci dirà come raggiungere nel modo più efficiente il miglior standard di silenziosità del cuscinetto – evidenzia Roberto Napione, Knowledge Area Manager Manufacturing – e se è possibile andare oltre quella soglia. Capire qual è il limite più basso di rumorosità raggiungibile sui cuscinetti radiali rigidi a sfere è fondamentale per la competitività di SKF nel mercato dei motori elettrici, dove la silenziosità contribuisce ad accrescere il valore percepito dai clienti.”
Dopo la fase di analisi, gli algoritmi SKF sintetizzano i dati su un cockpit che ne mostra l’andamento storico, riuscendo in questo modo a stimare con una altissima accuratezza la qualità della produzione nei successivi 40 minuti. Come per le previsioni meteo, all’aumentare della finestra temporale di predizione decresce l’accuratezza dell’algoritmo. È questa una funzionalità innovativa che mette in condizione l’operatore di intervenire per tempo, correggendo eventuali deviazioni. All’interno di linee di alta produzione, 40 minuti di anticipo sugli eventi risultano rilevanti sul modo di lavorare e sui risultati ottenibili.
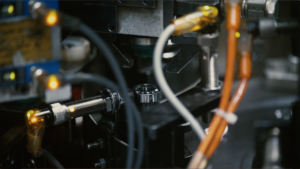
In questa prospettiva, l’algoritmo semplifica ma non sostituisce l’attività umana.
“Le decisioni saranno sempre prese dalle persone – aggiunge Napione – ma sulla base di indicazioni fornite da un sistema che esamina milioni di dati: un supporto decisivo, nell’ottica del miglioramento continuo.”
Oltre all’affidabilità delle indicazioni fornite, il secondo grande vantaggio del machine learning è la possibilità di cercare correlazioni tra i dati stessi, dalle quali è possibile ottenere nuova conoscenza. Confrontando milioni di dati, per esempio, è possibile individuare quali parametri strutturali portano alla minore performance di un turno di lavoro.
Il progetto è stato realizzato in collaborazione con Alten, gruppo francese specializzato nelle tecnologie avanzate, ed è stato finanziato con i fondi del CIM 4.0. “Il progetto Beat 4.0 messo a punto da SKF e Alten è stato giudicato vincente dal Competence Industry Manufacturing 4.0 – spiega Renato D’Uva, Head of Industrial Service Product Line – sia per l’elevato tasso di innovazione, sia per il ritorno economico sul processo produttivo.”
La sinergia tra SKF e Alten ha giocato un ruolo fondamentale: “In un progetto di ricerca come questo il risultato non è mai scontato – sottolinea Gianluca Montrucchio, Analytics, Big Data and Machine Learning Solution Manager Alten – la flessibilità si è rivelata l’arma vincente della nostra collaborazione, unita alla convinzione che tramite un approccio innovativo si potesse ottenere valore dai dati, come in effetti è successo.”
Un sistema modulare
L’approccio SKF alla fabbrica digitale è basato su moduli, che permettono di integrare le funzionalità dei sistemi in base alle specifiche esigenze. Alla base di ogni progetto di digitalizzazione c’è un’infrastruttura formata da una rete di fabbrica, un server centrale e chilometri di cavi, armadi di rete, firewall, switches. L’infrastruttura è il “sistema nervoso” che coordina i diversi moduli della fabbrica digitale SKF: Digital 2Win (D2W), Digital Factory Value Chain (D-FVC), Digital Cockpit, Condition Monitoring (CoMo), Big Data, Facilities Monitoring.
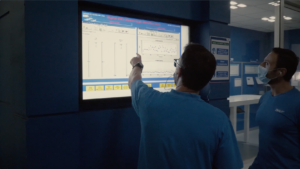
Il modulo D-FVC è pienamente integrato nello stabilimento di Cassino e verrà presto implementato anche all’interno del sito produttivo di Massa. Permette di monitorare i flussi di produzione, dall’ingresso della materia prima all’uscita del prodotto finito, integrandosi con il sistema di ERP XA degli stabilimenti SKF.
“Definita l’infrastruttura con il supporto costante dell’Information Technology SKF – dichiara Sara Del Greco, Project Manager Digital Factory Value Chain – la D-FVC esegue il monitoraggio qualitativo e quantitativo di tutta la catena del valore, garantendo la tracciabilità di materiali e prodotti.”
Il Digital 2Win presiede alla connettività delle macchine impiegate in produzione e qualità. Ne permette il controllo remoto, ne acquisisce i dati e permette di ottimizzare i cambi di produzione. Il condition monitoring è invece fondamentale per controllare le condizioni di esercizio delle macchine e garantirne la disponibilità. “Il cuore dell’Industry 4.0, tuttavia, è la gestione dei big data – dichiara Marian Banda, Project Manager Digitalization Cluster dei cuscinetti radiali rigidi a sfere – ogni giorno lo stabilimento di Cassino acquisisce in tempo reale 200 parametri diversi relativi a magazzino, impianti, macchine di produzione e di qualità. Sulla base storica dei big data possono essere elaborate sia analisi statistiche puntuali sia analisi più evolute attraverso il machine learning disponibile in ambiente cloud. La digitalizzazione semplifica i flussi, corregge le deviazioni e ottimizza i processi perché dove puoi misurare, puoi migliorare”.
Lo sforzo per fare evolvere il manufacturing SKF ha richiesto un enorme patrimonio di competenza digitale, ma la chiave di volta è stata la motivazione di tutto lo stabilimento. “L’aspetto più importante della digitalizzazione – spiega Antonio Molle, Global Operations and Lean Production Champion dei cuscinetti radiali rigidi a sfere – è stata l’attività di change management svolta insieme alle maestranze, alle quali abbiamo chiesto di imparare in breve tempo un nuovo modo di lavorare. La risposta è stata entusiasmante”.
Lo stabilimento SKF di Massa si sviluppa su una superficie coperta di 7.160 metri quadri ed è specializzato nella produzione di cuscinetti e supporti per applicazioni industriali. Certificazioni: ISO 9001:2015, ISO 14001:2015, ISO 50001:2018, ISO 45001:2018.