Gli autori di questa ricerca mostrano nuove soluzioni per la lavorazione di materiali ibridi. A livello industriale gestire compositi di lamiera metallica e termoplastici a fibra lunga (“LFT”) può essere una sfida complessa. Tuttavia, utilizzando le giuste tecnologie e i processi adeguati queste difficoltà possono essere facilmente superate.
Le esigenze del mercato sono profondamente mutate negli ultimi anni. I clienti sono sempre più pretenziosi poiché necessitano prodotti dalle performance superiori, con qualità elevata e a costi sostenibili. Inoltre, le richieste variano con una notevole rapidità obbligando i produttori a modificare frequentemente i componenti offerti e i cicli di lavorazione.
Avere lotti produttivi di grandi dimensioni è ormai un lontano ricordo, costringendo così ad adeguarsi a ordini in continua evoluzione. Queste ambiziose richieste rispecchiano le esigenze del mercato finale in cui i prodotti devono essere offerti a costi concorrenziali, pur garantendo il soddisfacimento delle numerose certificazioni, ad esempio, a livello di sicurezza e di emissioni.
In questo difficile contesto, essere in grado di rispondere alle richieste non diventa solo un fiore all’occhiello, ma una necessità per sostenere la competitività futura. Offrire ai propri clienti processi all’avanguardia e in continua evoluzione con lo stato dell’arte industriale è fondamentale.
Materiali ibridi
I settori a elevato valore aggiunto come, ad esempio, l’aerospazio e l’automotive, stanno spingendo verso un incremento di utilizzo dei materiali compositi. Le loro proprietà permettono infatti di risparmiare peso e aumentare l’integrazione funzionale del componente. Nei materiali compositi fibre di vetro e di carbonio sono utilizzate per rinforzare le matrici polimeriche e permettono l’utilizzo di plastiche anche per componenti strutturali.
I materiali termoplastici rinforzati con fibre lunghe (in inglese “long fibre-reinforced termoplastics” o “LFTs”) offrono la possibilità di essere prodotti in tempi rapidi oltre ad avere un costo della materia prima accettabile. La combinazione di materiali termoplastici rinforzati con lamiere metalliche crea i cosiddetti materiali ibridi. Unendo i due materiali è possibile ottenere un comportamento affidabile: la duttilità del metallo contrasta le rotture fragili dei compositi.
La grande opportunità offerta da questo tipo di materiale è quella di ridurre il peso dei componenti. Ciò risulta di notevole interesse nel campo dei trasporti poiché la riduzione di ogni grammo di peso comporta una riduzione dei consumi durante tutta la vita del prodotto. Ad oggi la principale barriera nell’adozione di questi materiali sono i costi produttivi. Solitamente la parte plastica e quella metallica vengono ottenute da due processi produttivi differenti, richiedendo notevoli costi e tempi. Gli autori dello studio sottolineano l’importanza dell’utilizzo dei corretti processi.
Viene infatti mostrato come sia possibile ottenere componenti in semplici fasi produttive sfruttando tecniche produttive idonee a questi materiali ibridi. Con i giusti processi è possibile abbattere sia i tempi che i costi produttivi, così da poter offrire componenti dalle elevate performance a prezzi concorrenziali.
Formatura ibrida
Per la produzione di componenti ibridi metallo-LFT è stato proposto un innovativo processo, efficiente sia per tempistiche che per costi. Questo processo (rappresentato in Figura 1) è la combinazione di una imbutitura per la lamiera e di uno stampaggio a compressione per il materiale termoplastico.
In questo processo il materiale termoplastico fuso viene utilizzato come mezzo per formare la lamiera, analogamente a quanto avviene nelle tecniche di idroformatura. In seguito alla formatura della lamiera, grazie al materiale termoplastico fuso e allo stampo rigido, anche il materiale LFT si solidifica.
Il risultato è un componente in cui una struttura di rinforzi coadiuva la lamiera a creare un componente ibrido.
Il principale vantaggio di questa tecnica è quello di permettere, in un’unica fase, la creazione di un componente. In questo modo i tempi sono notevolmente ridotti e solamente uno stampo è necessario per trasformare entrambi i materiali interessati.
Taglio waterjet
La tecnologia di taglio ad acqua (o waterjet) utilizza un getto d’acqua ad altissima pressione (fino a 7000 bar) per lavorare diversi materiali (rappresentato in Figura 2). Questa tecnologia è caratterizzata dalla versatilità, dai costi contenuti e dall’elevata qualità. Solitamente, le lavorazioni waterjet possono essere divise in due categorie in base alla composizione del getto: esso può essere con o senza abrasivo. Per tagliare materiali ad alta resistenza (ad esempio plastica rinforzata con fibre o metalli) è necessario utilizzare materiali abrasivi insieme al getto d’acqua.
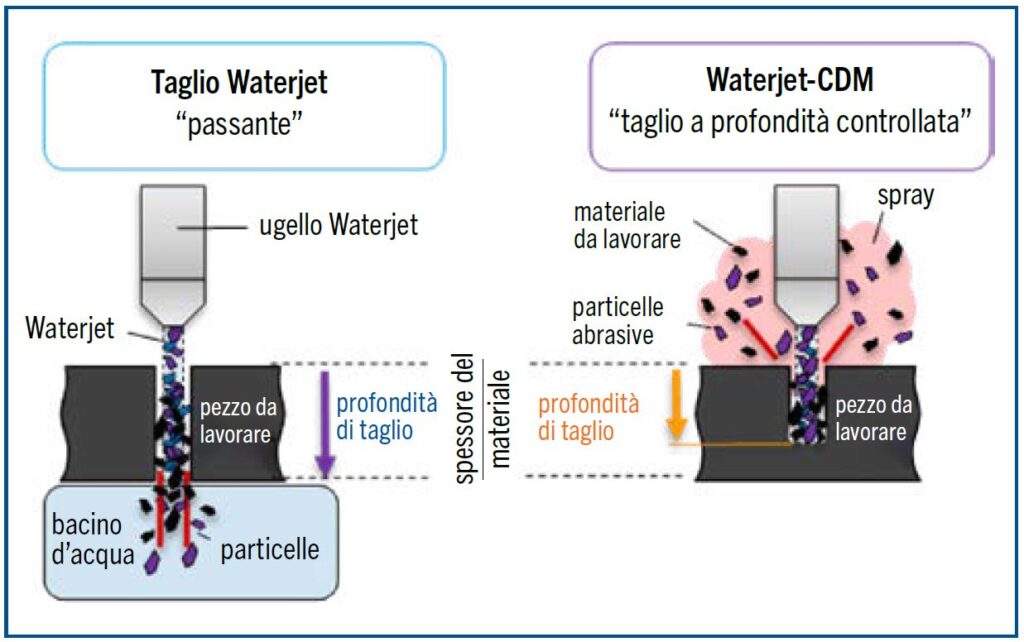
L’abrasivo viene accelerato dal flusso di acqua ad alta pressione e, quando il getto colpisce la superficie, la forza erosiva rimuove il materiale creando uno stretto solco che può attraversare il componente da lavorare creando un taglio.
I ricercatori tedeschi per la sperimentazione hanno sfruttato un macchinario waterjet H.G. Ridder a 5 assi dotato di una pompa in grado di arrivare fino a 6000 bar di pressione. Il risultato è stato successivamente analizzato tramite un microscopio digitale Keyence VHX-500 e tramite un sistema ottico di misura coordinate Alicona Infinite Focus G5. L’obiettivo è quello di analizzare il risultato di taglio per ottimizzarne la qualità. La sperimentazione mostra come, aumentando la velocità di taglio, migliori la qualità superficiale di un materiale, ma peggiori sull’altro.
Importante è anche la scelta della direzione di taglio (Figura 3). Generalmente un taglio inverso (partendo dal materiale polimerico a fibra) presenta una miglior qualità superficiale e geometrica. I risultati sottolineano l’importanza di trovare un giusto compromesso tra i parametri per ottenere un prodotto dalle caratteristiche bilanciate.
Lavorazione a profondità controllata
Un’interessante applicazione alternativa della tecnologia waterjet è quella di sfruttare il taglio a profondità controllata (Figura 2 a destra). Il risultato è analogo a quanto ottenuto tramite fresatura tradizionale.
Queste lavorazioni possono essere utilizzate per diversi scopi come, ad esempio, la rimozione del materiale nell’area superficiale per effettuare giunzioni o la lavorazione di superfici metalliche destinate a lavorare meccanicamente a contatto. Per questi studi sono state sfruttate diverse soluzioni di abrasivi e parametri di lavorazione. Gli abrasivi tradizionali possono infatti contaminare l’area lavorata. Per risolvere questi problemi potrebbe essere interessante approfondire l’utilizzo di abrasivi solubili (e.g. Sodio), così da produrre una superficie pulita a seguito della lavorazione.
Gli autori della ricerca mostrano nuove soluzioni per la lavorazione di materiali ibridi. A livello industriale gestire compositi di lamiera metallica e termoplastici a fibra lunga (“LFT”) può essere una sfida complessa. Tuttavia, utilizzando le giuste tecnologie e i processi adeguati queste difficoltà possono essere facilmente superate. Inoltre, i vantaggi di questa soluzione sono importanti poiché è possibile creare componenti più leggeri del 20%, incrementando le performance meccaniche e riducendo i costi.
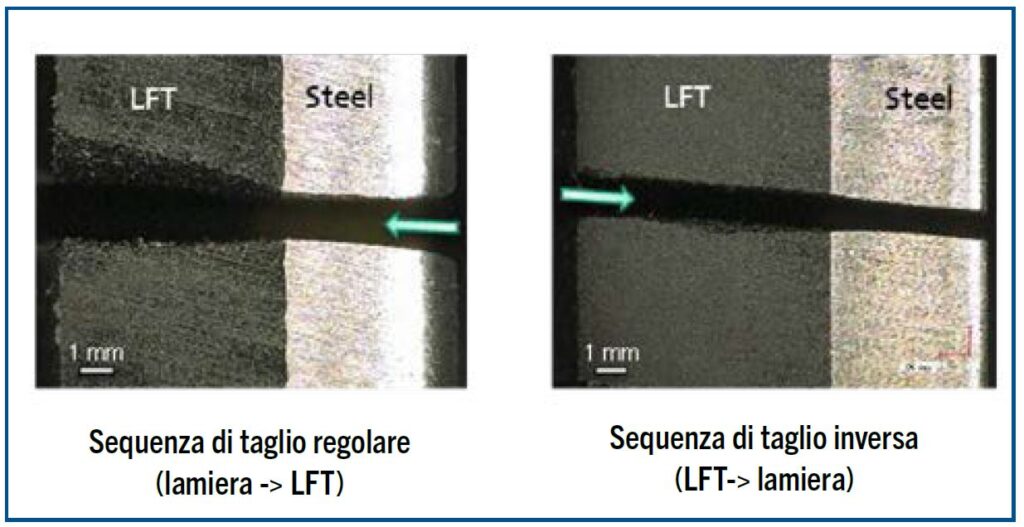
Fondamentale per i produttori che desiderano restare al passo con i tempi è l’adeguamento delle tecnologie proposte ai clienti. I processi convenzionali possono presentare dei limiti quando si tratta di lavorare nuovi materiali o di introdurre nuove applicazioni. Proprio per questo è importante essere pronti a offrire la giusta soluzione per distinguersi dalla concorrenza e soddisfare le nuove richieste dei clienti.
A cura di Stefano Grulli
Fonte: Schüler, M., Heidrich, D., Herrig, T., Fang, X. F., & Bergs, T. (2021). Automotive hybrid design production and effective end machining by novel abrasive waterjet technique. Procedia CIRP, 101, 374–377. https://doi.org/10.1016/j.procir.2021.02.039