La realizzazione di ingranaggi per la mobilità elettrica impone ai costruttori di macchine nuove sfide che riguardano la qualità estrema e il minimo rumore.
I motori elettrici si trovano in tantissimi settori e, con l’elettrificazione spinta e programmatica a cui la UE e il mondo stanno andando incontro, essi acquisteranno sempre più diffusione e importanza. Gli azionamenti dei motori elettrici sono costituti da una serie di ingranaggi la cui progettazione e costruzione è davvero complessa perché le variabili a cui tali ingranaggi sottostanno sono moltissime: l’alto numero di giri, l’inversione della direzione del carico, gli alti rapporti di contatto, l’aumento del rischio di sfregamento, una possibile deformazione degli alloggiamenti e non da ultimo il rumore che deve essere il più basso possibile ora che manca il motore a combustione interna a coprirlo.
L’importanza del giusto strumento di calcolo
Concentrandosi sulla geometria degli ingranaggi, in fase di progettazione è possibile rispondere in maniera customizzata alle richieste e alle sfide a cui sono sottoposti gli ingranaggi. Nel suo evento “e-Drive days”, Gleason Corporation ha presentato le possibilità di progettazione offerte dal software KISSsoft (di Kisssoft AG, acquisita da Gleason nel 2017) per poter progettare con elevata precisione gli ingranaggi per gli azionamenti dei motori elettrici. KISSsoft è un pacchetto software completo per la progettazione, l’analisi e l’ottimizzazione degli ingranaggi, degli alberi e dei cuscinetti, così come dei riduttori e delle trasmissioni complete.
Come afferma Brian Stringer, Manager KISSsoft Sales & Application Gleason Corporation, KISSsoft rappresenta il che progettista di ingranaggi per azionamenti un vero e proprio strumento per risparmiare tempo perché con esso è possibile realizzare l’intero processo di progettazione, analisi e ottimizzazione sia dal punto di vista della macrogeometria sia della microgeometria degli ingranaggi, considerando gli effetti dell’albero e dei cuscinetti. I calcoli del software si basano su standard internazionali e nazionali; il che significa che è uno strumento analitico che risolve molto rapidamente anche i calcoli più complessi, che permette l’ottimizzazione delle geometrie, delle resistenze, delle efficienze e della rumorosità. «In passato, molte volte è successo che i progettisti abbiano ideato un fantastico progetto in termini di ingranaggi, ottimizzando la macro e la micro geometria e poi, quando hanno fornito questo progetto alla produzione, sia stato impossibile riprodurlo; quindi, se riusciamo a considerare la fase di produzione mentre progettiamo il set di ingranaggi, dovremmo snellire l’intero processo, risparmiando tempo e denaro» afferma Stringer.
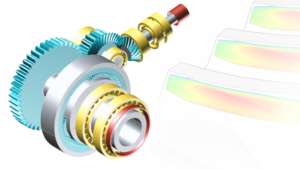
Dove viene usato il software KISSsoft? Il software KISSsoft può essere utilizzato ovunque vi siano motori elettrici, quindi nell’industria automobilistica e dei riduttori industriali, nelle applicazioni eoliche, aerospaziali e marine. A volte lo si usa solo per l’analisi dei cuscinetti a rulli ed esso dispone anche di funzioni per l’analisi degli ingranaggi in plastica e a passo fine. «Si tratta di un software di calcolo che consente un’ampia gamma di utilizzi in tutte le fasi, dall’ideazione alla produzione. Quindi non solo permette di progettare in anticipo, ma anche di ottimizzare e di fare analisi con possibili altre configurazioni ai fini di verificare la fattibilità; per fare analisi previsionali, valutare eventuali danni o guasti». Nel software KISSsoft confluisce, infine, tutta l’esperienza di primordine di Gleason nella progettazione e produzione di ingranaggi, portando costantemente dei miglioramenti e arrivando davvero a poter offrire ai clienti uno strumento di calcolo superiore.
Ingranaggi per la mobilità elettrica: qualità estrema nelle lavorazioni
La mobilità elettrica si sta affermando con forza e arriverà sul mercato più velocemente di quanto non si pensasse pochi anni fa: è questo il pensiero di Gottfried Klein, Director Product Management Hard Finishing Solution, Gleason Corporation. Con la mobilità elettrica si introducono nuovi concetti di mobilità anche dal punto di vista del motore e degli ingranaggi.
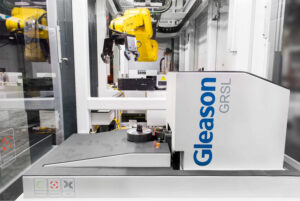
Tali nuovi concetti si trovano già anche nelle soluzioni di trasmissione ibride, tecnologie ponte verso i veicoli completamente elettrici, che siano veicoli elettrici a batteria o a celle a combustibile. La loro caratteristica è che hanno meno ingranaggi rispetto ai motori tradizionali. Di per sé gli ingranaggi non sono molto diversi nelle forme e geometrie ma con la mobilità ibrida o elettrica ad essi vengono richieste caratteristiche e requisiti diversi, soprattutto per quanto riguarda il rumore, la durezza, le vibrazioni. La produzione deve essere adattata a questi nuovi requisiti. Tutto questo crea nuove sfide anche per i processi di produzione. Tra i processi tipici della finitura degli ingranaggi per la trazione elettrica vi sono la dentatura, la smussatura, il Power Skiving, l’honing degli ingranaggi e la rettifica con mola filettata, comprese le tecnologie per creare gli utensili appropriati. Fondamentale nel passaggio produttivo è sempre il controllo della qualità.
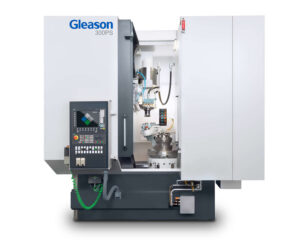
In origine solo il 5% circa dei pezzi prodotti veniva ispezionato e la maggior parte dei componenti, una volta prodotta, andava direttamente alla linea di assemblaggio, senza essere ispezionata. Per essere sicuri che anch’essi rispettino i requisiti di qualità richiesti, si usavano procedimenti statistici. Oggi, però, i requisiti richiesti agli ingranaggi diventano più severi e quindi anche i controlli di qualità devono esserlo. La statistica non basta più e quel 5% ispezionato deve tendere idealmente a 100. Impossibile? Non per Gleason che ha messo a punto un nuovo sistema (chiamato GRSL) che ha rivoluzionato il sistema di ispezione degli ingranaggi.
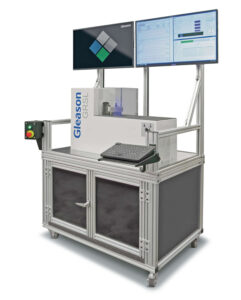
Con questo sistema, che incorpora un misto di tecnologie, tra cui l’utilizzo della scansione laser, è possibile realizzare una scansione e ispezionare gli ingranaggi alla stessa velocità con cui vengono prodotti. Si tratta dunque di un’ispezione ottica velocissima di tutte le caratteristiche standard come il profilo e il passo, che allo stesso tempo può anche misurare il DOP e lo spessore dei denti e fare valutazioni aggiuntive, come la valutazione dell’ondulazione, che è fondamentale quando si parla di rumorosità degli ingranaggi. Combinando questa unità con una macchina di finitura si ottiene una ispezione istantanea di tutti i pezzi prodotti.
Ma le sfide non finiscono qui. Per utilizzare al meglio la batteria si richiede agli ingranaggi il minor attrito possibile. Questo si raggiunge da una parte utilizzando degli oli a bassa viscosità e dall’altra assicurando un elevato livello di lavorazione della superficie degli ingranaggi. Gleason è in grado di offrire diverse soluzioni per operare in questa direzione e produrre ingranaggi che rispondano alle richieste attuali del mercato ovvero tramite smerigliatura e levigatura con tecnologie particolari.
• Il tool GAMA KTEPS che usa un rivoluzionario sistema di analisi per determinare la diagnosi del rumore. Analizza tutti i dati disponibili, dente per dente, ed è in grado di rappresentare i risultati di tale analisi su una interfaccia di facile uso. È, a detta dell’Azienda, uno degli strumenti più avanzati e precisi sul mercato ed è l’unico tool in grado di mostrare le conseguenze in termini di frequenze sonore delle deviazioni della superficie. Ha una elevata precisione;
• Il tool GAMA Advanced Waviness Analysis utilizza una singola traccia di dati per analizzare ciascun dente. Mostra i grafici delle armoniche e vi posiziona ciascun dente, indicando quali cadono fuori dia limiti di tolleranza. È un ottimo strumento per l’analisi “in linea” del 100% degli ingranaggi .
Gleason ha sviluppato una macchina testatrice universale – la 360T – per ingranaggi conici e cilindrici, veloce e flessibile. Il Tester Universale Gleason 360T è lo stato dell’arte dei tester di rotolamento comandati CNC che rende possibile il controllo di ogni tipo di ingranaggi. Il 360T aggiunge la capacità angolare e ospita una serie di innovazioni, risultando il solo tester del suo tipo che consente di testare coppie coniche spirali e ipoidi, coppie di ingranaggi cilindrici di ogni configurazione e angolo tra gli assi.