La vicentina Sagam Anodizzazione incrementa la propria capacità e la propria qualità produttiva aggiornando il proprio impianto per l’elettrodeposizione dei metalli con i performanti e modulari raddrizzatori per galvanica realizzati e forniti da RCV.
Grazie a un processo elettrochimico che crea uno strato di ossido artificiale sulla lega metallica con classe 10, 15 oppure 20 micron è tra le lavorazioni a tutt’oggi più resistenti agli agenti atmosferici, al sole e alla salsedine.
Stiamo parlando dell’anodizzazione dell’alluminio, attività in cui Sagam Anodizzazione è specializzata da quasi mezzo secolo.
Era infatti il 1974 quando a Grumolo delle Abbadesse, in provincia di Vicenza, due giovani decidono di mettersi in gioco nel settore dell’artigianato, dando vita a un’attività che ancora oggi viene svolta dalla seconda generazione.
«Attività – precisa Manuel Candian, alla guida dell’azienda insieme alla sorella Erica – alla quale nel 1988 si è affiancata anche la parte di verniciatura dell’alluminio, con la nascita della consociata Sagam Verniciatura.»
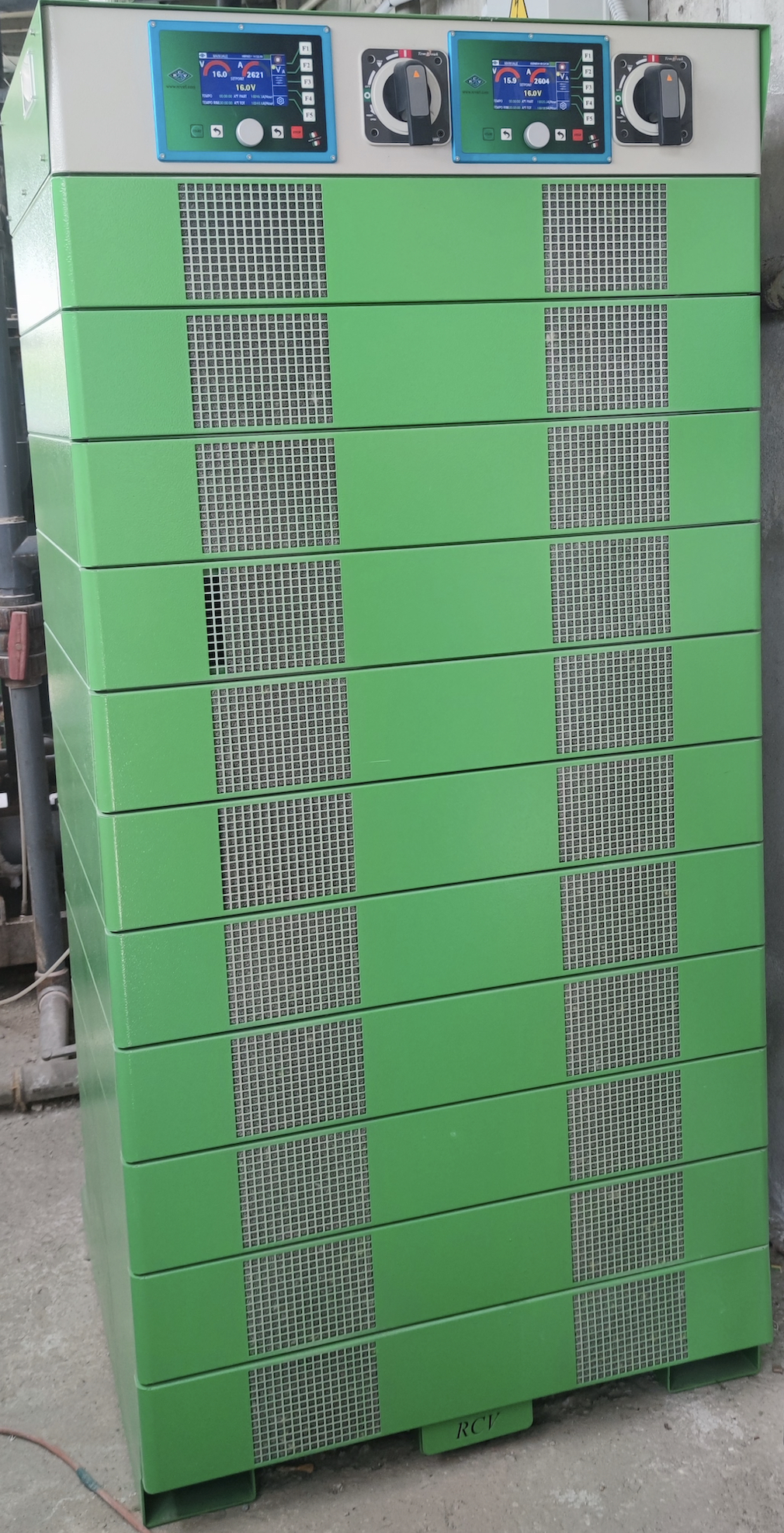
Le due aziende sono così in grado di offrire un servizio completo, nonché proporsi quale punto di riferimento territoriale per piccole e medie imprese che da tempo collaborano e si intrecciano per soddisfare le richieste del mercato.
«Un portfolio clienti – precisa Candian – comprendente, fra gli altri, fonderie, svariati magazzini di alluminio, importanti operatori del settore dei serramenti e dell’edilizia in genere, alcuni dei quali aventi sede anche oltre confine. Clienti per i quali processiamo profili industriali di tutti i tipi, piuttosto che profili per la realizzazione di serramenti, di facciate continue, oltre a barre, tubolari, griglie e lamiere, e manufatti in genere.»
Clienti che dallo scorso dicembre possono beneficiare delle prestazioni offerte dal performante impianto per l’elettrodeposizione dei metalli dove sono operativi i due nuovi raddrizzatori switching per galvanica serie R.S.D.T. realizzati e forniti da RCV.
Il valore aggiunto della modularità
Le motivazioni per cui Sagam Anodizzazione ha deciso di optare per questo nuovo investimento sono molteplici, ed è proprio Candian a spiegarle.
«Prima di tutto si è trattato di un aggiornamento tecnologico, visti anche gli oltre vent’anni di onorato servizio del precedente impianto, peraltro sempre realizzato e fornito da RCV. Ma a convincerci sono stati alcuni interessanti aspetti della nuova serie di raddrizzatori. Per esempio, la loro modularità e quindi la possibilità, in caso di malfunzionamento, di poter escludere il modulo critico e poter continuare, seppur con minore potenza, la produzione. L’impianto tradizionale richiedeva invece non solo l’intervento tecnico ma, in caso di guasto non riparabile in loco, il trasferimento per la riparazione con tutte le immaginabili conseguenze dal punto di vista del fermo produzione.»
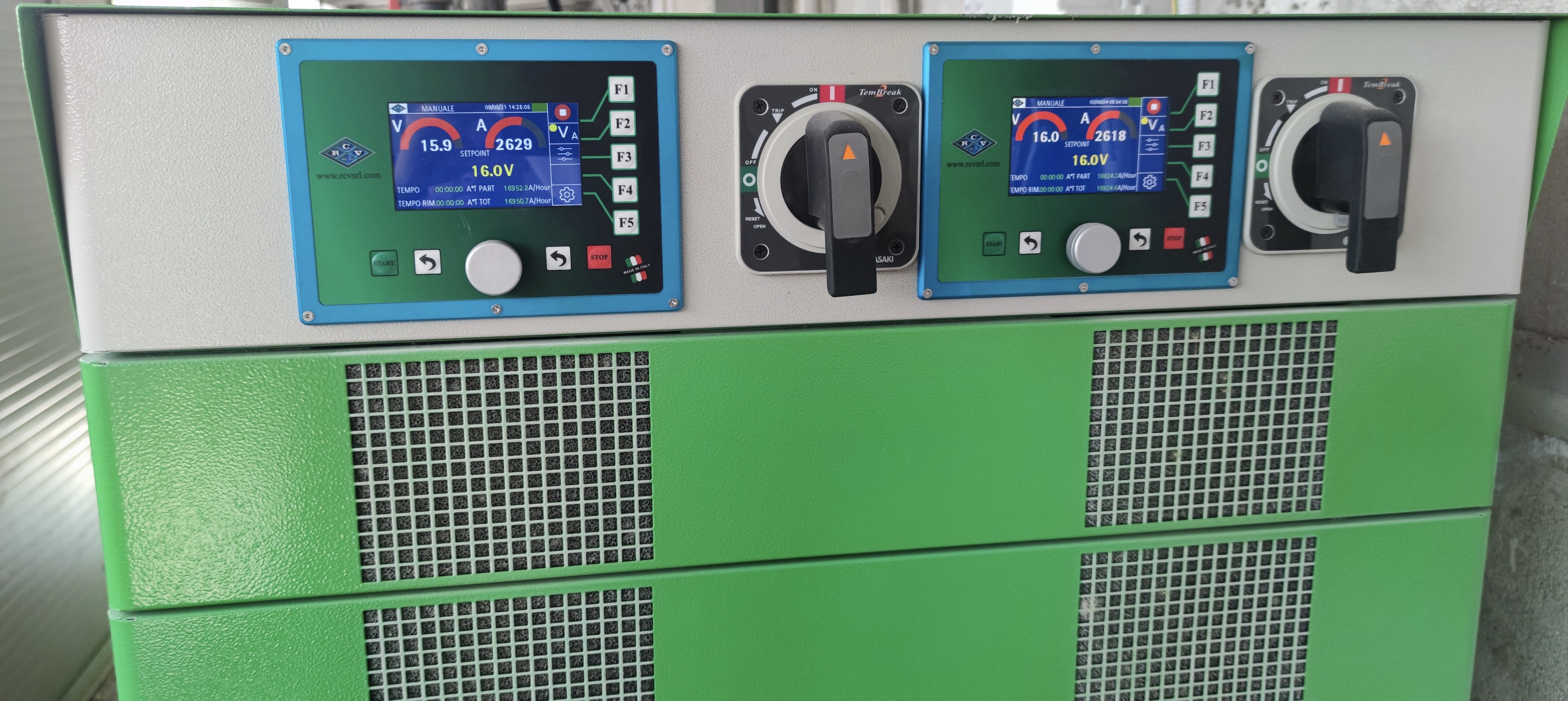
Il nuovo impianto, le cui vasche possono ospitare prodotti fino a 7,5 m di lunghezza e alte fino a 1,40 m, sfrutta il potenziale produttivo di due serie di raddrizzatori switching R.S.D.T. da 20 moduli ciascuno, per un totale di corrente di 20.000 A/20 V.
La modularità consente di annullare totalmente il fermo della produzione causato da eventuali anomalie.
In caso di guasto di un modulo, infatti, questo sarebbe automaticamente escluso mentre tutti gli altri compenserebbero la potenza mancante, permettendo così all’impianto di continuare a lavorare mentre si provvede alla riparazione.
Semplici da sostituire, senza dunque dover necessariamente attendere un tecnico RCV, i raddrizzatori R.S.D.T. sono anche auto-configuranti.
Ciò significa che qualora si fosse in possesso di raddrizzatori di varie potenze (tensioni diverse), acquistando un solo modulo di scorta si risolve il problema di tutta la linea galvanica garantendo la continuità della produzione.
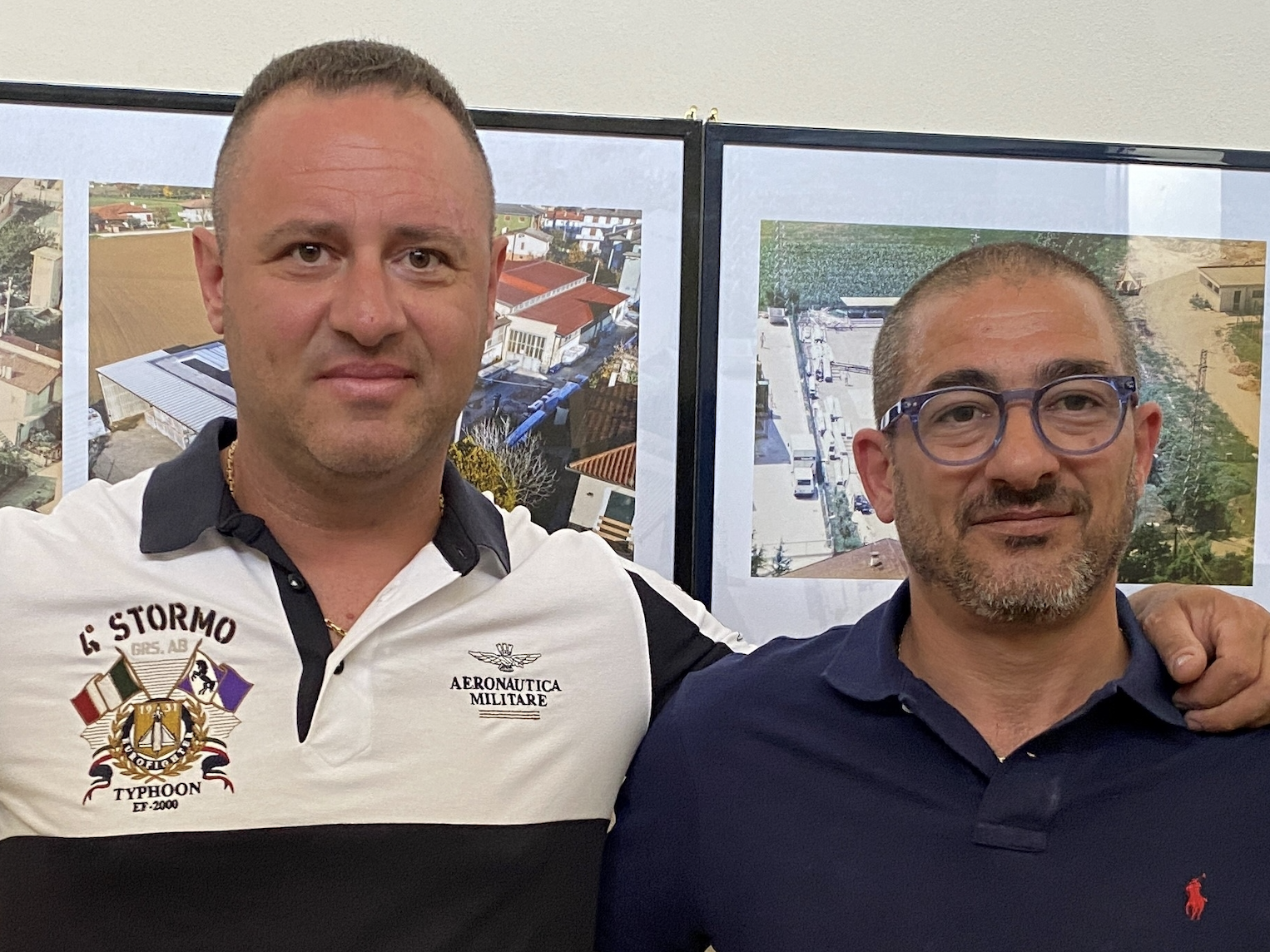
Configurazione peraltro scelta dalla stessa Sagam Anodizzazione.
Maggiore produttività, minori consumi
«Dopo quasi un anno – continua Candian – si è rivelato molto interessante anche l’aspetto legato ai consumi. La nuova tecnologia, rispetto al precedente impianto, ha permesso un risparmio medio di energia elettrica di circa il 20%. Ma c’è di più, in quanto non si tratta solo di maggiore efficienza, ma anche di maggiori prestazioni. Lo strato d’ossido di alluminio risulta infatti come spessore dal 5 al 10% in più a parità di tempo. In altre parole, si ha una maggiore produzione con minori consumi energetici.»
Un ulteriore beneficio che i nuovi raddrizzatori serie R.S.D.T. di RCV hanno portato in Sagam Anodizzazione riguarda anche il minore surriscaldamento del bagno anodico, aspetto questo che si traduce nella minore necessità d’uso del gruppo refrigerante.
«Maggiore efficienza, maggiori prestazioni e minori consumi – sintetizza Candian – ma anche la possibilità da parte nostra di poter accelerare la velocità di processo e dunque aumentare la produttività, ovvero produrre pari spessori in minor tempo, con dati verificabili in tempo reale.»
Da segnalare infatti che tutti i modelli della serie sono provvisti di ingresso Ethernet IP.
Questo permette non solo a RCV di intervenire con un’assistenza da remoto, ma consente all’utilizzatore di poter monitorare, controllare e comandare a distanza i raddrizzatori sfruttando in tempo reale molteplici funzionalità: invio di tutti i comandi (start/stop/tensione-corrente ecc.); riferimento richiesto di tensione/corrente da pannello operatore o PLC; stato del raddrizzatore; tensione e corrente erogata di ogni singolo modulo; dati di configurazione e di processo; comandi inviati da e verso PLC; dati rete elettrica di alimentazione; allarmi su pagina di registrazione Log.
Per ogni modulo che compone il raddrizzatore, grazie a una comoda interfaccia HMI di ultima generazione è possibile vedere sempre in tempo reale dati come, per esempio: la velocità del ventilatore di raffreddamento; le temperature IGBT di regolazione e dei diodi di potenza; la temperatura del filtro di livellamento di uscita; la temperatura barre di uscita (che permette di capire in anticipo un collegamento non corretto all’impianto galvanico); la temperatura della Cpu e quella dei radiatori di raffreddamento; il componente guasto (diodi-IGBT-Trasformatore-filtro AC ingresso di rete ecc.).
Il fattore competitività
«La decisione di innovarci e passare ai nuovi raddrizzatori R.S.D.T. – conclude Candian – non è stata in realtà all’inizio così facile da prendere. La nostra reticenza in questo cambiamento risiedeva nella consapevolezza di avere ancora a disposizione un impianto, sempre realizzato e fornito da RCV, sicuramente meno performante ma che per un ventennio ha svolto più che egregiamente tutte le sue funzioni. Da aggiungere che su impianti medio-grandi come il nostro, per l’ossidazione non vengono normalmente impiegati. O meglio, non si trovano raddrizzatori sul mercato come gli RCV, in quanto erroneamente ritenuti troppo delicati per l’applicazione, contrariamente a quanto avviene nei diffusissimi e normalissimi piccoli impianti. A distanza di quasi un anno non possiamo che essere più che soddisfatti del nuovo investimento, che ha dimostrato tutta la sua affidabilità, col quale oggi serviamo ancora meglio i nostri clienti, e grazie al quale siamo riusciti ad elevare ulteriormente la nostra competitività e la qualità delle superfici dell’alluminio per i componenti trattati».
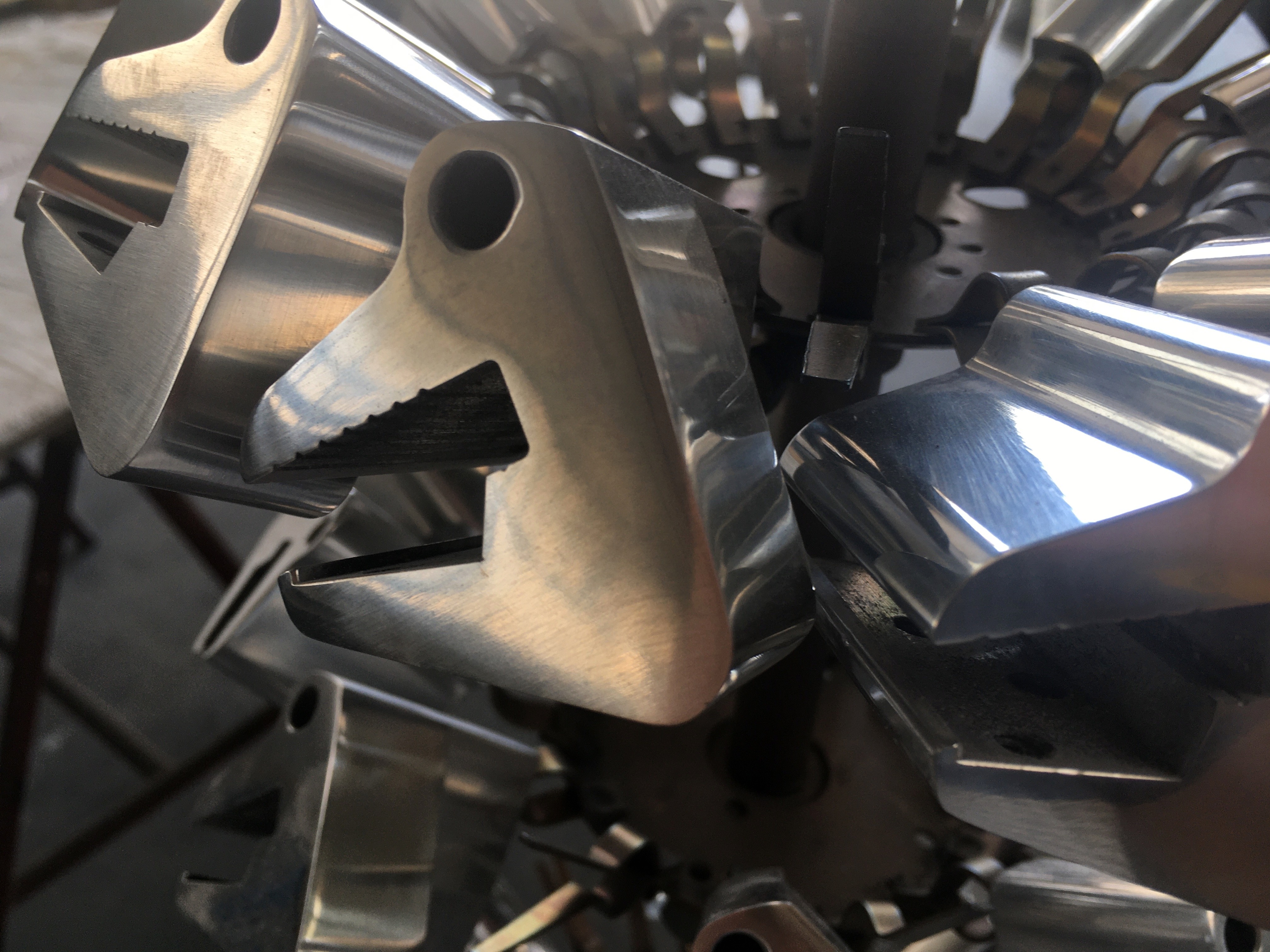
Trattati con cura e attenzione tipica del fare artigianale, ma con una gestione e un’impostazione industriale del processo, in grado di soddisfare le esigenze della piccola e della grande azienda.
Da segnalare, infine, che in ottica di miglioramento continuo, la stessa Sagam Anodizzazione ha recentemente installato un impianto fotovoltaico da 150 kW di potenza sulla copertura del proprio stabilimento.
Un importante e ulteriore investimento che assicura la fornitura di energia elettrica da fonti rinnovabili pari a circa la metà della quotidiana necessaria all’attività produttiva.
I colori dell’ossidazione anodica
L’argento, il bronzo e l’elettrocolore sono le colorazioni dove Sagam Anodizzazione si è nel tempo maggiormente specializzata.
L’anodizzazione argento, nota anche come “anodizzazione naturale”, è il trattamento più semplice, la base di ogni eventuale colorazione.
In questo caso non vengono impiegate colorazioni particolari ma semplicemente si determina la finitura dell’alluminio che può essere spazzolata, lucida o chimica.
Anche l’argento a poro aperto è una lavorazione dell’alluminio ancora molto richiesta, soprattutto per quei prodotti destinati alla verniciatura o al rivestimento plastico, dal momento che non prevede il fissaggio finale.
Quando si parla di bronzo e testa di moro il materiale, dopo la lavorazione base, viene trattato con bicarbonato, permanganato e acetato di cobalto che definiscono la colorazione richiesta, e consolidato con il trattamento finale di fissaggio.
L’elettrocolorazione (peraltro ancora molto richiesta nel territorio dove ha sede l’azienda) varia infine da una tonalità più chiara chiamata acciaio a una più scura definita semplicemente nero.
L’esperienza di chi, come Sagam Anodizzazione, lavora da anni in questo settore, si nota proprio in questo momento, quando le bagnate elettrolitiche sono date dalla pratica minuziosa e infine perfezionate.
I numeri di SAGAM
- 760.000 mq superficie anodizzata;
- 1.000 mq di superficie produttiva;
- 15 dipendenti;
- 1.800 ton alluminio anodizzato all’anno Sagam in cifre.
di Gianandrea Mazzola