L’efficienza dei processi di stampaggio, piegatura, imbutitura e tranciatura delle lamiere e dei tubi può essere limitata da numerosi spiacevoli eventi. In parte, un miglior controllo sulla qualità dei materiali in ingresso al processo dei lubrificanti utilizzati può ridurre alcune fonti di inefficienza. Vedremo in questo articolo alcuni metodi specifici per una migliore caratterizzazione dei materiali in ingresso al processo.
Nei processi di deformazione e taglio della lamiera l’efficienza del processo, talvolta definita OEE con terminologia anglosassone (Overall Equipment Efficiency), può essere inferiore alle attese per numerosi motivi, sia organizzativi, sia tecnologici. Alcuni di questi vengono in fabbrica molto spesso attribuiti o direttamente collegati a un colpevole ben preciso: il materiale in ingresso. L’OEE può diminuire per vari motivi, ad esempio:
Perché si è costretti a fermare gli impianti per eseguire manutenzioni non programmate, dovute ad esempio a un’usura troppo rapida degli utensili. Se una matrice di tranciatura deve essere normalmente sostituita, ad esempio, ogni mezzo milione di colpi e invece un bel giorno ne esegue soltanto 100000 prima di non funzionare più bene, questo evento impone un fermo produzione imprevisto, oltre al costo vivo della sostituzione, riducendo la produttività.
Perché la messa in produzione di un nuovo lotto di materiale o di un nuovo stampo richiede tempi di cambio lotto superiori alle attese. Può capitare delle volte che alla ripresa delle operazioni, magari in corrispondenza con un cambio coil e un cambio turno serale, un processo che fino a prima della pausa andava benissimo cominci a generare difettosi.
Perché la messa in produzione di un nuovo prodotto richiede tempi di setup superiori alle attese. Quando si avvia in produzione un nuovo prodotto con un nuovo set stampi e un nuovo materiale è normale attendersi tempi lunghi prima che la produzione si assesti. Tuttavia, delle volte il processo si ostina a non andare in controllo per tempi troppo lunghi, inattesi.
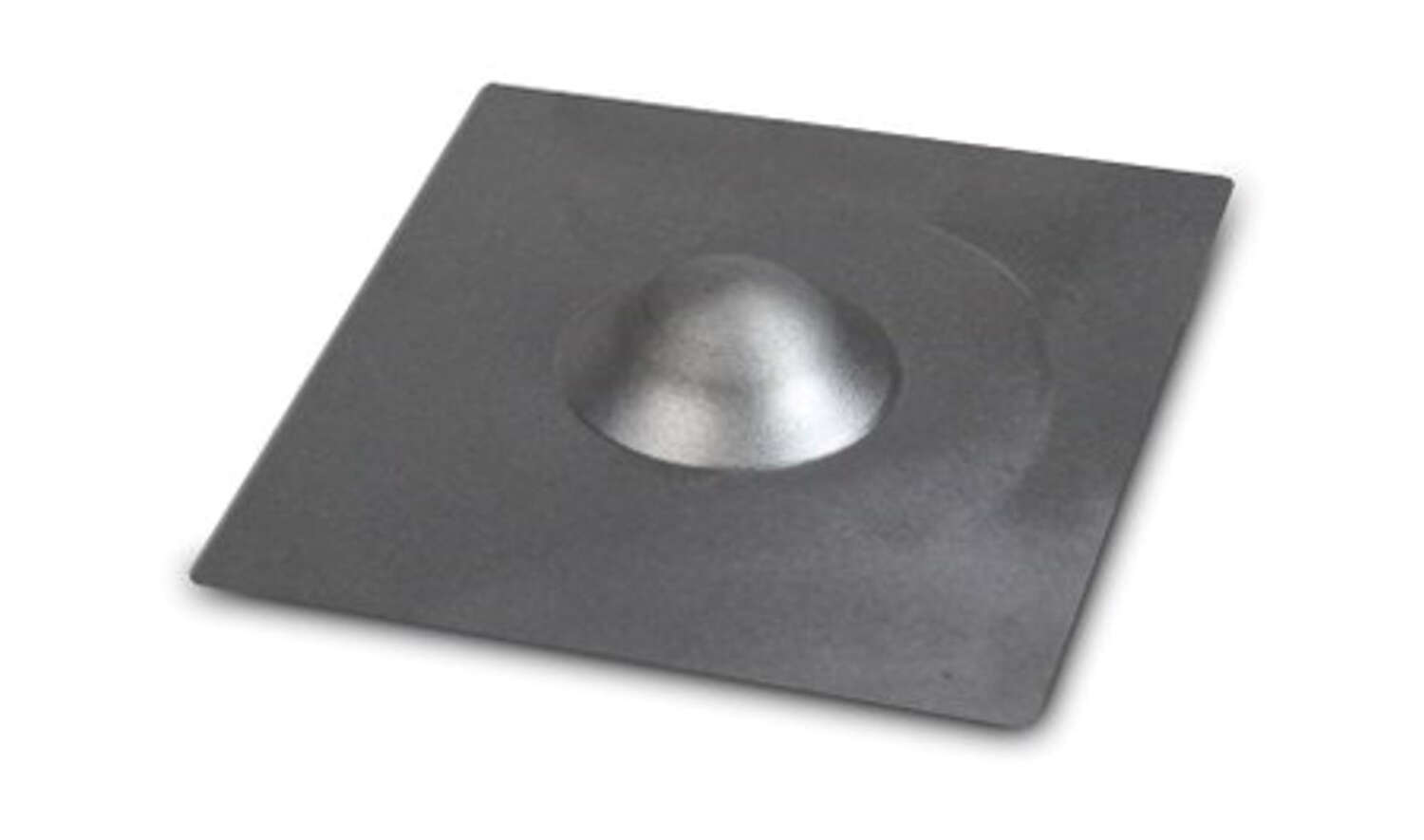
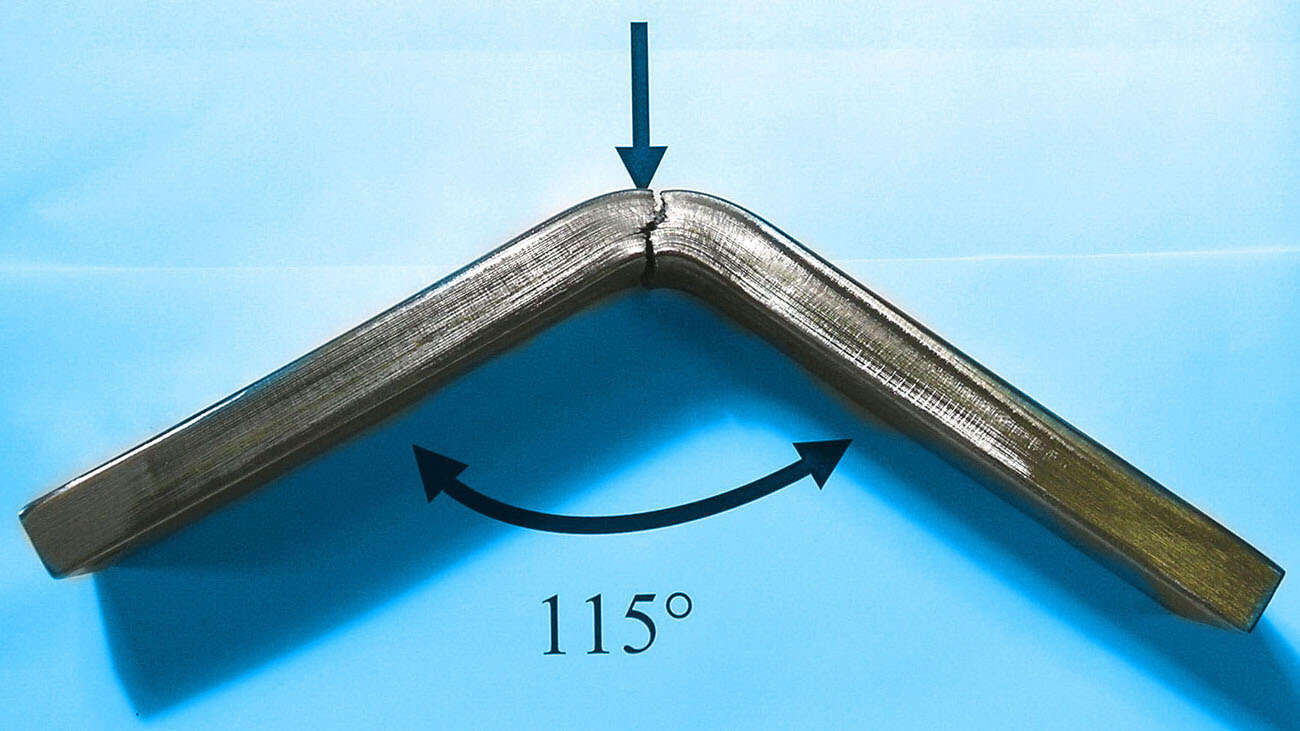
Perché si osserva un tasso di difettosità non previsto o troppo elevato, senza motivi evidenti. Le quote possono andare fuori tolleranza, il ritorno elastico può diventare troppo ampio o variabile, possono comparire dei difetti estetici o peggio delle grinze o delle fratture. In conseguenza di ciò occorre fermare il processo per capire cosa non stia funzionando, e delle volte tutto si aggiusta semplicemente rallentando il ritmo produttivo (ad esempio diminuendo il numero di colpi al minuto di una pressa).
Quando una di queste evenienze si verifica con troppa frequenza, di certo, una gran parte della responsabilità è dovuta a un processo che è stato spinto un po’ troppo al limite, che in altre parole è stato pianificato in maniera poco robusta. Cionondimeno un qualche rimedio va trovato ed è abbastanza tipico e comune del personale di reparto cercare di scaricare la responsabilità su un facile colpevole: ad esempio la qualità della lamiera in ingresso oppure la qualità del lubrificante.
Tuttavia, le cause di una mancata efficienza potrebbero facilmente trovarsi altrove: ad esempio in un’errata scelta dei parametri del processo, in un’imprecisa regolazione delle attrezzature, in derive termiche o meccaniche del processo o dei macchinari, ecc. Diventa dunque indispensabile separare le responsabilità, e accertare senza possibilità di errore se i materiali in ingresso non solo rispettino le specifiche contrattuali, ma abbiano delle caratteristiche di formabilità adatte al processo in oggetto. Sappiamo bene che i certificati che accompagnano i lotti di materiale acquistato possono essere datati o imprecisi.
La prima cosa da fare dunque è una rapida verifica delle caratteristiche più importanti, prima fra tutte la misurazione dello spessore. Se lo spessore è fuori dalle tolleranze previste, ovviamente il nastro va scartato, ma questa evenienza, occorre ammetterlo, è piuttosto rara.
Le prove meccaniche: parametri, vantaggi e svantaggi
Dunque per caratterizzare compiutamente la qualità della materia prima, acclarato che lo spessore è quasi sempre in tolleranza, occorre verificarne le caratteristiche meccaniche. La regina delle prove meccaniche è naturalmente la prova di trazione, in base alla quale vengono normalmente stilati tutti i certificati che accompagnano le lamiere e la quale tutte le acciaierie eseguono prima di fare uscire il prodotto di una colata. La prova di trazione è normalmente utilizzata per misurare e verificare i valori di modulo elastico E (GPa), di carico di rottura Rm (MPa), di carico di snervamento Rs (MPa), di allungamento percentuale a strizione A% oppure a frattura.
La prova di trazione può anche essere utilizzata, con le opportune modifiche e analisi, per calcolare tre importanti parametri di formabilità del materiale, tanto importanti quanto ignorati dalla maggioranza degli operatori: i parametri sono r, cioè il coefficiente di anisotropia normale, n, l’esponente di incrudimento, Dr, cioè il coefficiente di anisotropia planare.
Il coefficiente r (norma UNI 8341:1982) è un importante indice di formabilità, perché ci dice della maggiore o minore tendenza del materiale ad assottigliarsi. Valori di r maggiori di 1 sono da preferirsi, perché indicano una scarsa tendenza all’assottigliamento e dunque una buona formabilità.
Il coefficiente Dr (norma UNI 8341:1982) indica invece la tendenza della lamiera a comportarsi diversamente nelle varie dimensioni del piano, ad esempio a formare lobi oppure delle forme ovali in stampaggio quando invece ci si aspetta forme circolari. Valori di Dr vicino allo zero sono da preferirsi.
Infine, il coefficiente n (norma ISO 10275), facilmente calcolabile rielaborando i dati della prova di trazione, è un indicatore di formabilità, perché più esso è alto (ad esempio maggiore di 0,25) più forte è l’incrudimento del materiale durante lo stampaggio e più improbabile o ritardato sarà il fenomeno della strizione, cioè dell’assottigliamento localizzato.
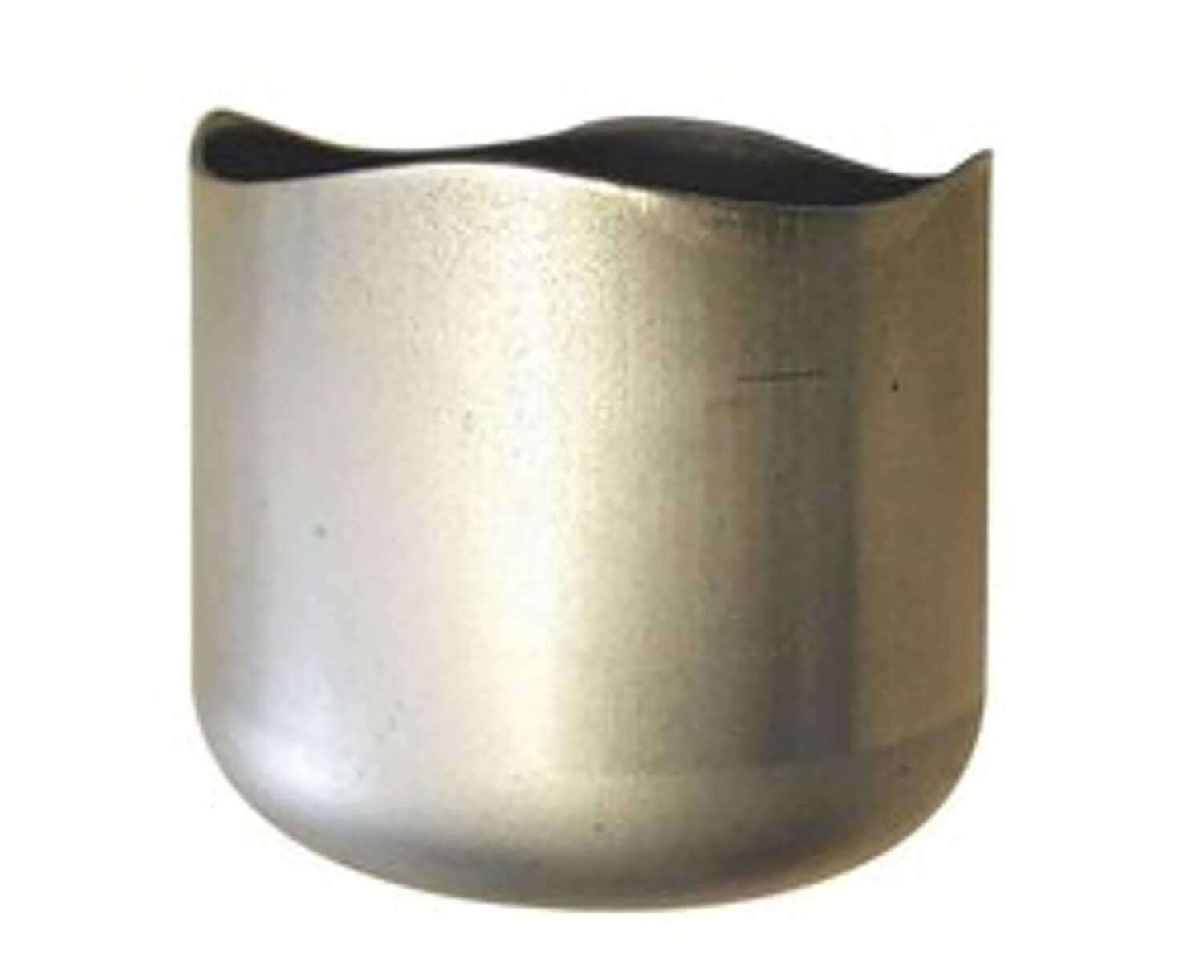
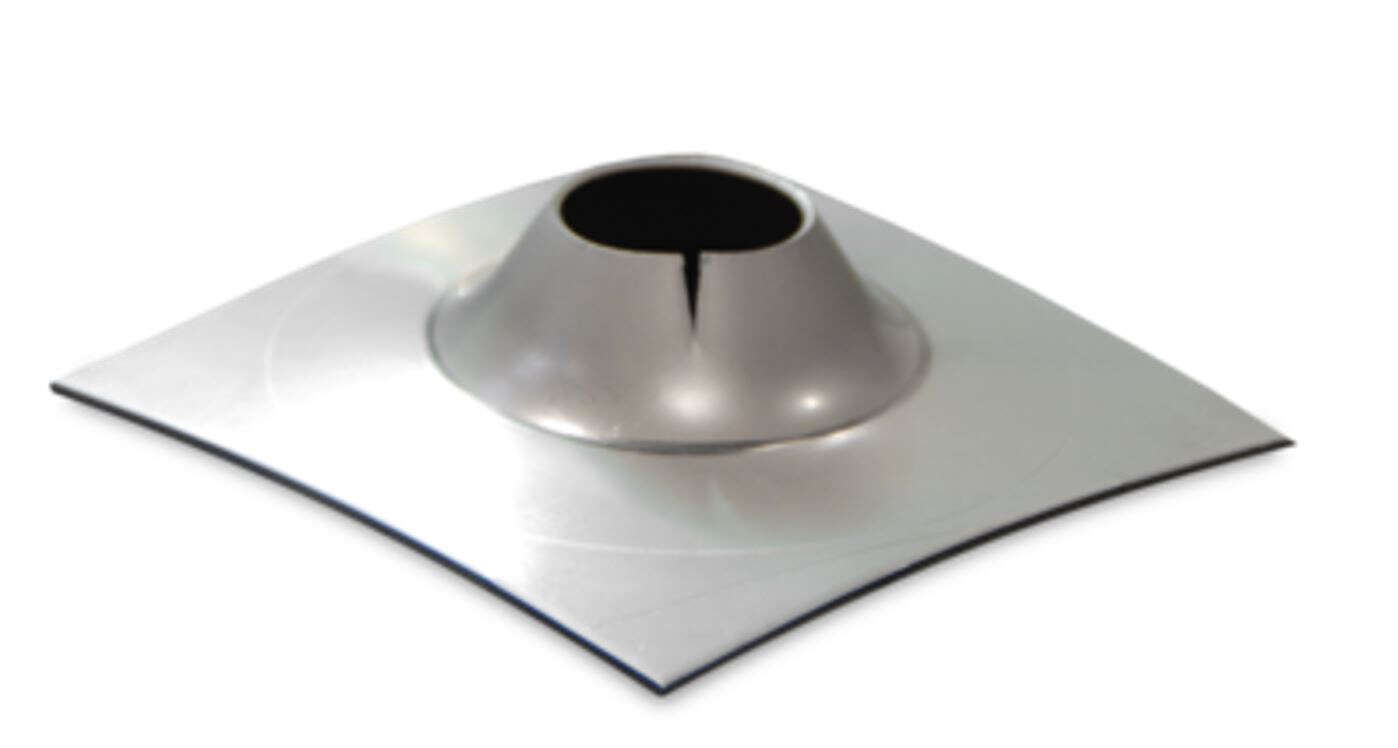
Tutti questi parametri finora elencati sono ricavabili dalla prova di trazione. Tuttavia, la prova di trazione ha dei limiti. Prima di tutto è una prova relativamente semplice, ma non semplicissima: richiede che un provino sia ritagliato dalla lamiera secondo la direzione di laminazione (ma anche secondo altre due direzioni ortogonali alla prima, se si vuole misurare l’anisotropia) in forma di “osso di cane”, richiede che i bordi siano tranciati con buona qualità, pena la prematura frattura dello stesso durante la prova, richiede che venga eseguita su una macchina di norma abbastanza costosa e richiede che venga eseguita da un operatore addetto ed esperto.
Insomma, non è certo una prova che si esegue “al volo”, sul campo. Una prova molto più semplice, veloce, e volendo anche trasferibile sul campo, è invece la prova di microdurezza; certo non facile da eseguire con accuratezza su provini molto sottili, ma rapida e semplice. La durezza è abbastanza ben correlata alla resistenza meccanica del materiale, cioè ai due parametri Rm ed Rs. Chiaramente la prova di durezza da sola non ci fornisce indicazioni sulla formabilità della lamiera, ma ci consente senza dubbio di classificarla in una categoria e di fare un rapido controllo di qualità in ingresso, qualora non si abbia il tempo di eseguire una prova di trazione completa.
Le prove simulative
Le prove meccaniche elencate al paragrafo precedente hanno il grande vantaggio di parlare un linguaggio universale, di essere universalmente accettate e standardizzate e di fornire informazioni neutrali sul materiale, indipendentemente cioè dalla sua applicazione effettiva. Le prove cosiddette simulative sono invece prove che non forniscono valori da intendere come proprietà meccaniche assolute dei materiali, ma sono comunque prove molto spesso normate e standardizzate. Di seguito riporto un breve elenco di quelle più utili e significative.
Prova di flessione a 3 punti (norme ISO 7438, ISO 5173): idonea a caratterizzare le lamiere di interesse di chi deve principalmente eseguire processi di piegatura e curvatura. Richiede una macchina di prova dinamometrica simile o uguale a quella usata per la prova di trazione, dunque soffre degli stessi svantaggi di praticità.
La prova fornisce utili indicazioni sulla curva carico-spostamento, che può essere trasformata in una curva carico-angolo di piega, con quale elaborazione matematica. Fornisce anche un modo per quantificare e quindi caratterizzare il ritorno elastico di una lamiera, informazione indispensabile per qualunque piegatore.
Prova di imbutitura (norma ISO 20482): come suggerisce il nome, adatta per chi esegue spesso operazioni di stampaggio e imbutitura, caratterizza bene la formabilità del materiale. Esistono dispositivi dedicati alle due varianti principali (Olsen o Erichsen), alcuni dei quali possono essere anche molto compatti e di semplice utilizzo, quindi possono essere usati più rapidamente di una prova di trazione. La prova di imbutitura dà una misura della formabilità delle lamiere molto semplice e diretta, cioè molto vicina alla formabilità reale che ci si può aspettare nel reale processo di deformazione plastica.
Test di earing (norma ISO 11531): ha lo scopo di caratterizzare l’anisotropia planare delle lamiere, dunque è il corrispondente simulativo della prova di trazione per il calcolo di Dr. È una prova – non molto diffusa, per la verità – che misura l’irregolarità, cioè la non circolarità, della circonferenza esterna della flangia di una lamiera che viene imbutita.
Test di espansione di un foro (norma ISO 16630): questa prova è soprattutto usata da chi deve lavorare con lamiere in acciai alto-resistenziali, cioè lamiere tendenzialmente fragili. Succede infatti spesso nella pratica di officina che si abbiano fratture non già nei punti in cui ci si aspetta la massima deformazione, ma piuttosto per via di cricche che partono dai bordi tranciati della lamiera. Per questo motivo, la prova prevede il movimento di un punzone che espande un foro circolare precedentemente tranciato su uno spezzone. Questa prova dunque misura la fragilità non già di tutta la lamiera ma in particolare del bordo tranciato, la cui qualità dipende, naturalmente, non soltanto dal materiale stesso ma dal modo con cui è stato tranciato, cioè dalla migliore o peggiore finitura superficiale del bordo.
Come usare i dati di qualità dei materiali
La prima, ovvia e pratica applicazione dei dati di caratterizzazione dei materiali è, in particolare, su quelli universali provenienti dalla prova di trazione, per stabilire degli accordi contrattuali, cioè per definire le tolleranze di accettazione del materiale. Tuttavia, capita abbastanza spesso che i dati materiale siano molto variabili, apparentemente troppo variabili e poi invece i processi di formatura corrispondenti risultino perfettamente in controllo.
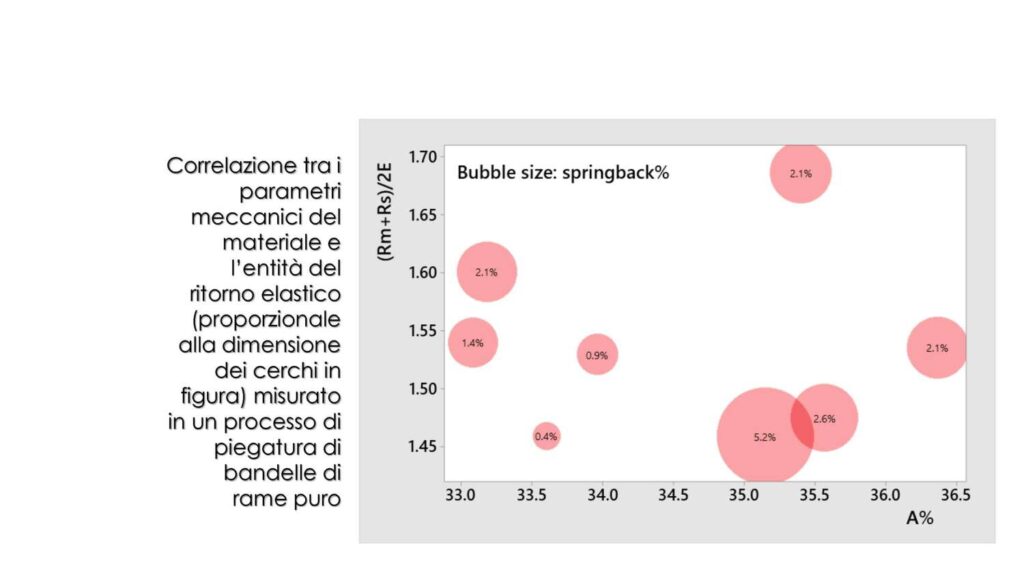
E viceversa, capita anche che da materiali apparentemente di ottima qualità siano eseguiti processi fuori controllo o comunque con elevato tasso di difettosità. È quindi estremamente importante stabilire, senza darle per scontate, se esistano correlazioni tra i parametri di qualità dei materiali e i parametri di qualità o di capability o di difettosità dei processi. Trovare queste correlazioni non è facile, ma ancora più difficile è escludere che esistano, queste correlazioni. Per questo le necessarie indagini andrebbero eseguito con metodo scientifico, e non a tentativi.
Verso la fabbrica digitale: incrociare i “big data”
Acquisire i dati dei materiali con ordine e digitalizzarli in un formato facilmente reperibile, associandoli cioè non solo al produttore, ma ovviamente anche al lotto, alla colata, alla data di esecuzione della prova ma poi anche alla data di messa in produzione del lotto stesso rappresenta un primo passo verso la costruzione di una gerarchia organizzata di dati informatici, i quali possono generare informazioni preziose per il futuro. La raccolta dei dati di qualità non deve essere solo completa e digitale. I dati di qualità dei materiali in ingresso devono essere archiviati in un “data lake”, cioè un supporto informatico che consenta l’accesso ad algoritmi di intelligenza artificiale.
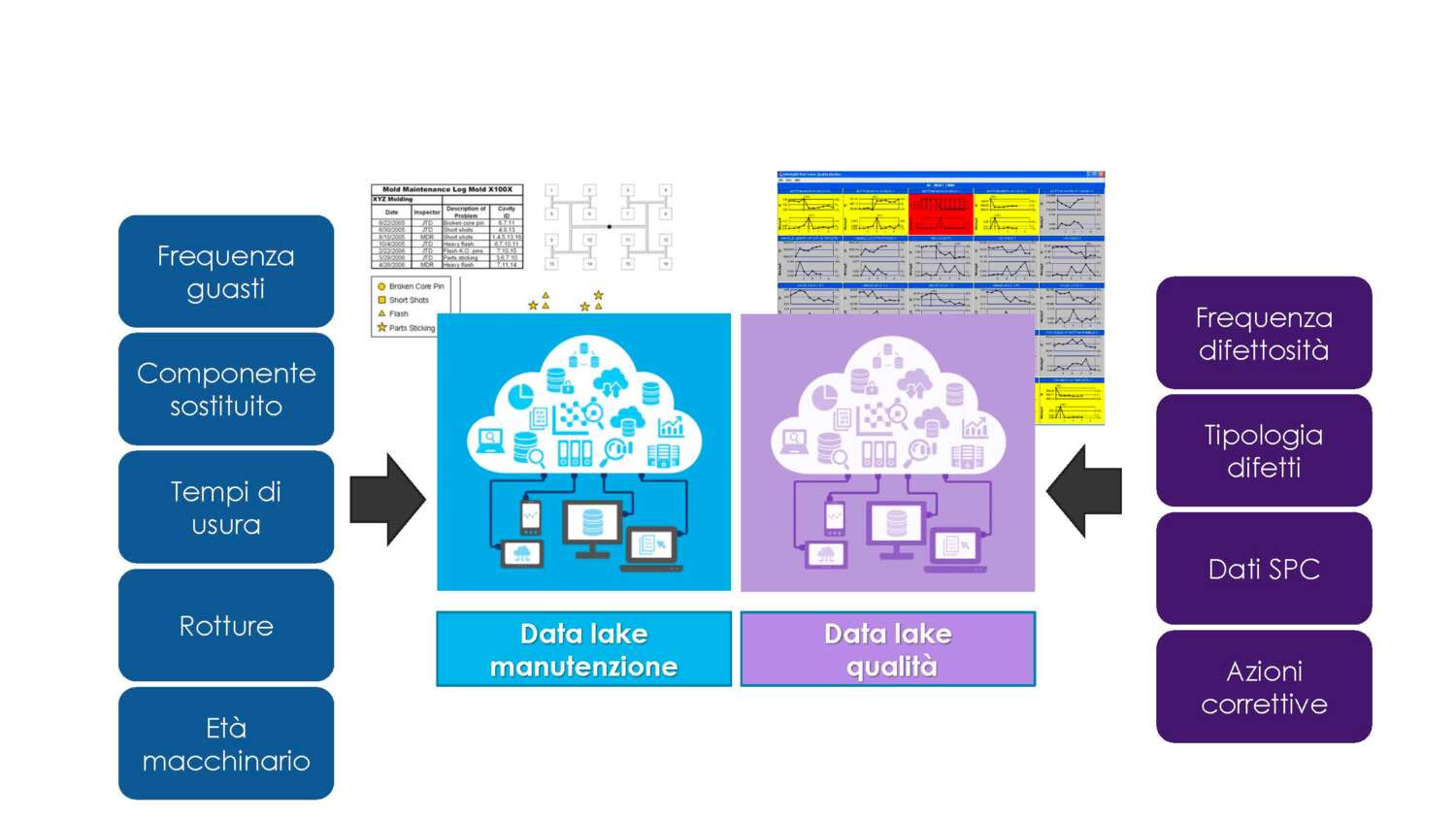

Il data lake dei dati materiale deve poi essere anche integrato e incrociato con altri 3 data lake, contenenti gli altri dati di produzione, molti dei quali già disponibili in azienda, cioè i dati di manutenzione di stampi e attrezzature, i dati di qualità dei prodotti stampati, i dati di processo.
I dati di manutenzione di stampi e attrezzature, cioè la frequenza di guasto o i tassi di usura, le statistiche sulle sostituzioni degli attrezzi usurati, le statistiche sugli eventi catastrofici (rotture degli utensili), le statistiche sulle età degli stampi e il numero di colpi eseguiti, ecc.
I dati di qualità dei prodotti stampati, cioè le statistiche di SPC (statistical process control), le statistiche sulle varie tipologie di difetti occorsi, la frequenza di difettosità o le percentuali di scarto, le eventuali azioni correttive intraprese sul processo, ecc.
I dati di processo, cioè i log delle macchine che eseguono i vari processi e, laddove possibile, i dati dei sensori presenti sulla macchina, eventualmente “zippati”, cioè compressi in modo da non saturare rapidamente le memorie informatiche.
Infine, tutti questi dati devono essere incrociabili, cioè devono contenere un’informazione sul momento di acquisizione (time stamp) del dato, e devono consentire di incrociare i dati. In altre parole, ad esempio un evento di manutenzione su uno stampo deve poter indicare con quale lotto di materiale in ingresso si è verificato, su quale prodotto, qual era la qualità del prodotto in quel momento, quali erano i dati di processo in quel momento.
Proprietà meccaniche principali delle lamiere | Unità di misura | |
E | Modulo elastico | GPa |
Rs | Carico di snervamento | MPa |
Rm | Carico di rottura | MPa |
A% | Allungamento % a strizione | – |
Dr | Coefficiente di anisotropia planare | – |
r | Coefficiente di anisotropia normale | – |
n | Esponente di incrudimento | |
Hv | Microdurezza Vickers | MPa |