Le difficoltà di reperimento e la volatilità dei prezzi della materia prima si sono sommate alle stringenti esigenze dei committenti nel rendere sempre più strategiche le operazioni di controllo sugli stock in entrata ove il connubio fra esperienza e tecnologie innovative può fare la differenza.
In una fase storica in cui l’attenzione ai conti economici è necessariamente ai massimi, tanto presso i fornitori quanto presso i committenti, cinque aziende a vario titolo impegnate nella trasformazione dei metalli hanno spiegato a Lamiera in che modo riescano a garantirsi e lavorare materie prime di qualità e prive di difetti integrando strumenti innovativi con approcci empirici tradizionali.
Una risorsa in più dai controlli intermedi
Sede a Sovico in provincia di Monza e Brianza, Mobilferro è specializzata nella realizzazione di prodotti destinati a settori disparati che spaziano dal design e l’arredamento sino al medicale, l’elettronica e la meccanica. È di conseguenza ampia anche la scelta dei materiali e relative varietà utilizzati a seconda delle circostanze. Il ferro, specie nelle qualità DC01 e DD1; acciaio inox AISI 304, 316 e 430 e l’alluminio, in prevalenza come lega 5754. «Vengono adottati di volta in volta», ha detto a Lamiera il responsabile di direzione Maurizio Di Bernardo, «in base alle funzioni che i manufatti finiti dovranno poi assolvere. C’è attenzione all’estetica, certamente, ma questa deve sempre coniugarsi alle caratteristiche della durevolezza e della resistenza alle varie sollecitazioni».
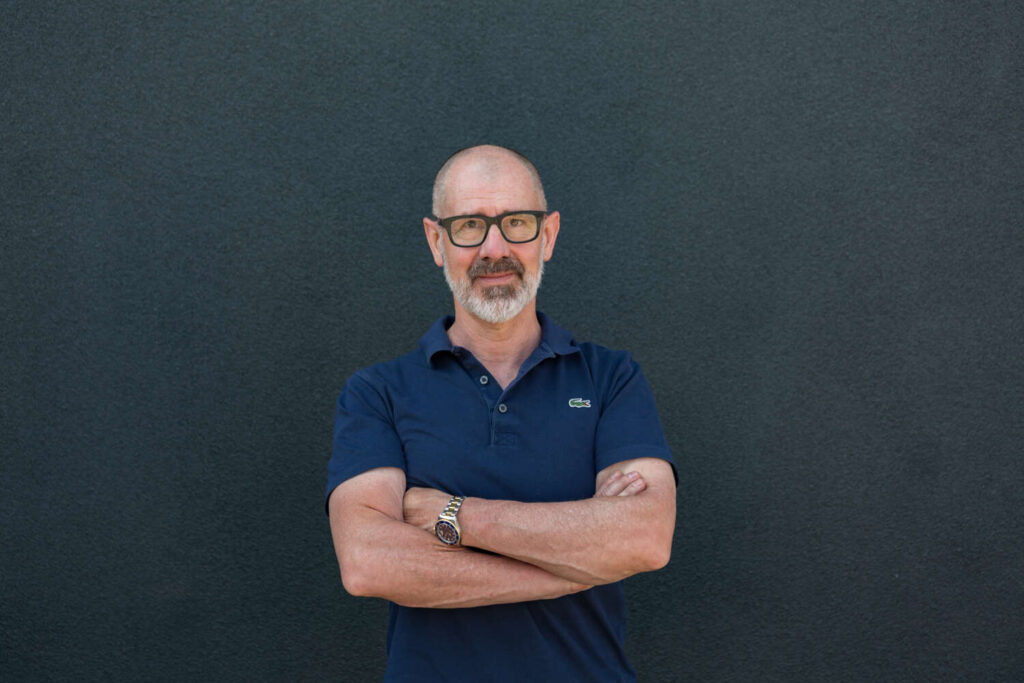
Per questo la loro selezione viene sovente svolta in collaborazione con i clienti e confrontandosi con loro su tutti gli aspetti «riguardanti la loro idoneità ai nostri processi e cicli di lavorazione» che includono «taglio laser, piegatura, assemblaggio ed eventuali operazioni di verniciatura e finitura». La qualità dei materiali è decisiva e per garantirla Mobilferro ha a disposizione una gamma di strumenti classici quali calibri, spessimetri, micrometri e misuratori di pH (pH-metri) integrati poi «con quelli presenti sulle attrezzature». L’obiettivo è quello di «poter effettuare ulteriori verifiche» e di conseguenza «godere di una maggiore mole di dati cui fare riferimento».
Soprattutto negli ultimi anni, però, l’approccio ai controlli è andato incontro a cambiamenti significativi. «Si conferiscono una crescente attenzione e importanza», ha proseguito Di Bernardo, «ai cosiddetti controlli intermedi eseguiti durante il ciclo produttivo, così da poter individuare quanto prima quei possibili difetti suscettibili di pregiudicare il livello qualitativo delle nostre produzioni. Ancora una volta, l’aspetto estetico non è per noi secondario ed è essenziale contare sul fattore umano, cioè sulla presenza di tecnici esperti in grado di valutare sia la bellezza sia le dimensioni di ogni pezzo».
Clienti e fornitori, sempre più coinvolti
Non solo il personale interno e i clienti, ma anche gli specialisti delle società fornitrici vengono sempre più spesso coinvolti nell’attività di Mobilferro, per ottenerne considerazioni dettagliate e precise, utili poi per supportare il cliente o sviluppare strategie, soluzioni, metodologie inedite. Col passare del tempo le esigenze della clientela si sono evolute facendosi più stringenti. «In primo piano c’è sia la qualità totale degli articoli realizzati», ha osservato l’intervistato, «sia la richiesta frequente di lotti sempre più piccoli dello stesso prodotto, con ripetibilità non costante nel tempo e termini di consegna rigorosi. Dobbiamo essere flessibili e pronti ad adattarci a necessità diverse».
Oltre a ciò, contrariamente a quanto accadeva in passato, i nostri interlocutori vogliono essere accompagnati via via lungo le varie fasi del ciclo di produzione in un’ottica di vera partnership. Questo impone la capacità «di dare indicazioni aggiuntive rispetto ai materiali utilizzati; offrire soluzioni per migliorie costruttive tali da incrementare le prestazioni dei manufatti o da ottimizzare i prezzi. Il servizio di sviluppo-prodotto deve saper assicurare al cliente l’opportunità di dialogare con un’unica interfaccia per arrivare a concepire e mettere in atto progetti in precedenza impensati. Analogamente, nel post-vendita siamo chiamati a reagire efficacemente e rapidamente agli inconvenienti e conservare una documentazione da richiamare, nel tempo, per ulteriori riflessioni».
Un aiuto dalle tecnologie
Fra shortage, rincari e volatilità – che costringono a tenere gli occhi spalancati sull’andamento delle quotazioni e a curare minuziosamente la gestione dei magazzini e dei fabbisogni – la qualità delle materie prime disponibili è a sua volta a rischio. Le fonti di approvvigionamento potrebbero cambiare e così pure la provenienza delle commodity; cresce il rischio che «i requisiti qualitativi possano esser disattesi rispetto alle richieste manifestate in sede di acquisto». La conseguenza è chiara: «I controlli in entrata, che seguono procedure ben definite dal sistema di gestione qualità», ha detto Di Bernardo, «debbono esser condotti dal personale ancora più attentamente, aumentando per esempio il numero di campionamenti, specie quando il materiale arriva da fornitori meno noti».
Le tecnologie 4.0 sono garanzia di valore aggiunto su più ambiti del processo produttivo e quindi anche sulla verifica dei materiali. Con i software gestionali dei quali Mobilferro è in possesso «è possibile tracciare più facilmente le movimentazioni e associare o integrare la documentazione utile a consolidare metodi di controllo magari già presenti» e già utilizzati, sì, ma con altre modalità.
«Il supporto», ha concluso Di Bernardo, «è significativo anche perché implica degli automatismi di grande aiuto per i nostri addetti per attività quali l’emissione automatica delle distinte base, il calcolo del fabbisogno e il suo collegamento ai documenti di supporto. Senza dimenticare il tracking dei controlli in relazione ai materiali utilizzati e il monitoraggio della supply chain, la registrazione dei dati supplementari: tutto è digitalizzato e per ciò stesso più immediato e puntuale».
Monitorare con gusto
La pistoiese Gi.Metal, che realizza articoli di vario genere per l’industria della ristorazione, è nota nel mondo per il suo posizionamento da primato in un comparto dalla elevatissima specializzazione: quello delle pale per pizzerie.
Per conseguenza, le materie prime che l’azienda utilizza devono sottostare e superare tanto i controlli di qualità quanto quelli di sicurezza e igiene per l’industria alimentare.
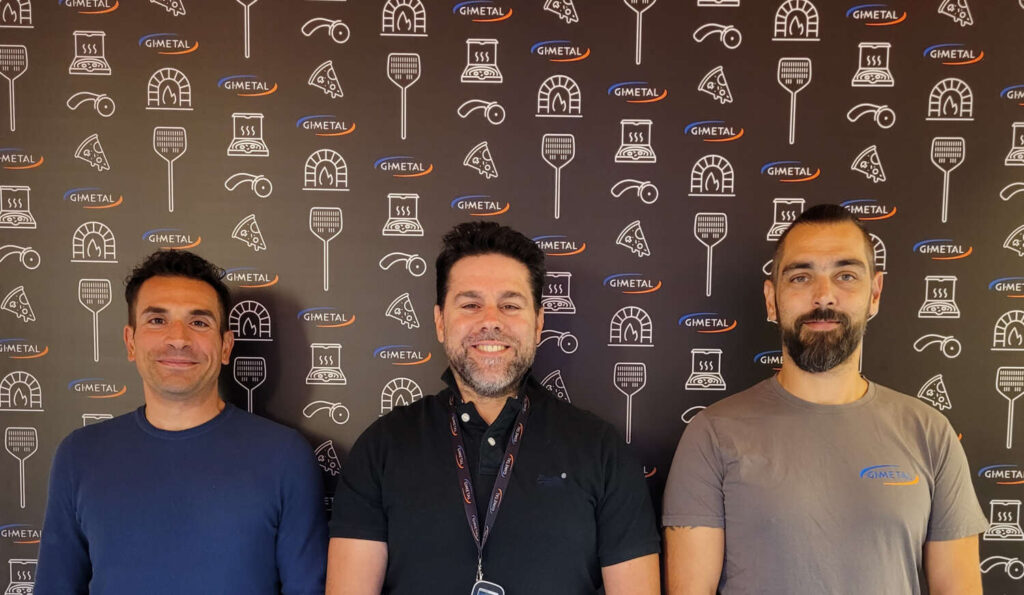
«Siamo soggetti», ha detto il responsabile di stabilimento Riccardo Barneschi «alla certificazione MOCA (Materiali a contatto con gli alimenti, ndr) e per questo i nostri prodotti e forniture sono regolarmente sottoposti a test presso laboratori esterni autorizzati e specializzati. È un vincolo importante e va a sommarsi alle certificazioni che, per evitare qualunque potenziale problematica, compiamo sulle colate e i manufatti finiti, lungo un ciclo operativo che già di per sé è lungo e articolato.
Lavoriamo alluminio e inox in lamiera, tondo, ovali, tubi ed estrusi e ci occupiamo di taglio laser su due e tre dimensioni e di stampaggio, oltre che di asportazione di truciolo e levigature superficiali. Il controllo preventivo degli spessori e finiture è fondamentale per portare alla luce rigature o difetti». Ai laboratori partner esterni sono quindi demandate le verifiche sul possibile rilascio di sostanze nocive, chiaramente molto critico per il settore che Gi.Metal presidia.
«Non possiamo permetterci errori», ha detto Barneschi, «né sui manufatti interamente lavorati, affilati e stampati o costampati in casa né sulle parti importate o sui manici acquistati in Cina e montati poi, qui, su lame e pale. Offriamo tre versioni diverse – per prezzo e caratteristiche, ma non per affidabilità – degli stessi prodotti: comuni a tutti sono proprio le rigorose procedure di controllo, specie sulle importazioni».
Organizzazione 4.0
Si ha così la certezza di arrivare al cliente con articoli dotati di tutte le caratteristiche preventivate e con tempi di consegna non superiori ai quattro giorni, salvi i casi di personalizzazioni significative.
Come altrove, anche in casa Gi.Metal la gestione degli stock è mutata in coincidenza con l’avvento della pandemia e allo scopo di limitare gli imprevisti: il volume delle scorte di materia prima è raddoppiato e anche in questo modo l’azienda è riuscita a conservare intatto il livello di qualità dei suoi pezzi e del suo servizio.
«Gli scarti in finitura o dovuti a inquinamento superficiale individuato dai test MOCA», ha ricordato Barneschi, «non sono mancati, perché si può dire che in alcuni periodi nei cubilotti finisse davvero un po’ di tutto».
Se altri sono stati però costretti a sospendere le attività a noi non è accaduto: certo è che negli ultimi anni è difficile fronteggiare l’aumento dei costi, che solo parzialmente possono essere riversati sui clienti.
Farli entrare in sofferenza vorrebbe dire soffrire a nostra volta e le criticità, per la ristorazione e la GDO che serviamo, sono già molte». Il prevalente ricorso al taglio laser fa sì che i controlli siano per la maggior parte statistici e di calibro; né il catalogo di Gi.Metal è tale da richiedere tolleranze micrometriche particolari, come accade invece in altri comparti del manifatturiero.
«Un’ispezione visiva attenta è spesso sufficiente», ha concluso Riccardo Barneschi, «e dal momento che le operazioni di montaggio e assemblaggio vengono eseguite internamente, i nodi vengono senz’altro tutti al pettine ben prima della vendita. Le stesse tecnologie 4.0 ci interessano più sotto l’aspetto organizzativo e la gestione dei movimenti di magazzino (monitorati in tempo reale), per avere risposte immediate sugli scarti e sulla qualità degli stock ma non sono utilizzate in sede di puro controllo».
Ma i problemi non finiscono
Taglio laser e pressopiegatura delle lamiere sono, corredate da una gamma di servizi di assistenza, le specialità della trevigiana Spadotto, sede a Motta di Livenza e 40 anni di esperienza alle spalle. «Come terzisti», ha esordito il titolare Flavio Mario Spadotto, «dobbiamo seguire le richieste del mercato anche in tema di controlli. Parte di essi è standardizzato grazie a scanner evoluti per la decodifica delle bindelle e soluzioni atte a tracciare e documentare le condizioni dei materiali: AISI, alluminio, altro ancora. Se però si deve analizzare la materia prima il controllo-qualità è in primo luogo visivo o supportato, per esempio, da durometri.
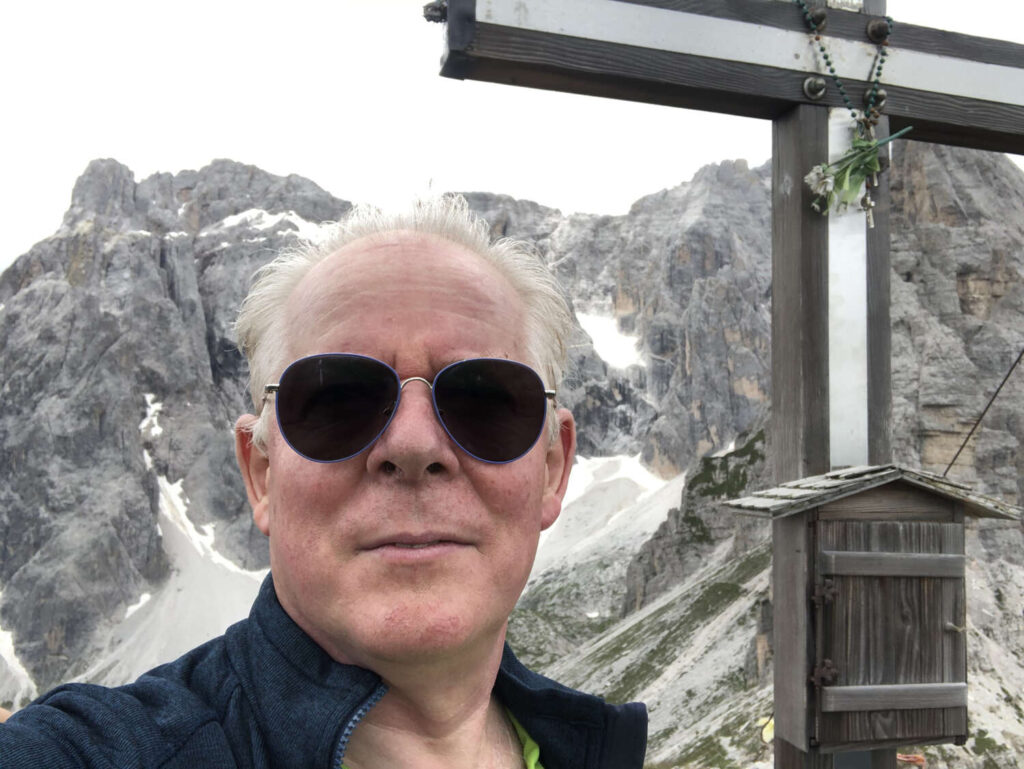
Quando un certo lotto non corrisponde a quel che è stato dichiarato nei documenti – e al momento del taglio, piega o filettatura i problemi emergono sempre – dimostrare le non-conformità resta comunque difficile se non impossibile. Nel servire alcuni clienti le carpenterie non hanno esigenze particolarmente stringenti ma quando si parla di componenti strutturali e non si può derogare da livelli qualitativi molto elevati, le verifiche dirette, sul campo, sono indispensabili.
E tutto si complica se ci si accorge che il materiale dà problemi in piega o lavorazione meccanica». Avere fornitori fidelizzati, certificati, qualificati e affidabili resta il modo più efficace di prevenire le problematiche; l’altro è l’esperienza che suggerisce quando fermarsi, dinanzi ai dubbi, per fare verifiche ulteriori; a maggior ragione qualora non si disponga di risorse tecnologiche dedicate.
I canali abituali e quelli alternativi
L’azienda ha preso in considerazione sia l’acquisto di strumentazioni portatili sia la creazione di un laboratorio di analisi interno: a oggi i progetti sono in stand-by, soppesati i costi e i benefici, ma tutt’altro che abbandonati.
«Per la gestione interna dei materiali», ha continuato Spadotto, «ci basiamo da una parte sulla documentazione dall’altra su processi che comunque sono a prova di certificazione e sul tracciamento degli ingressi e delle commesse tramite i gestionali di fabbrica». Dallo scorso febbraio, il conflitto russo-ucraino ha resa necessaria una diversificazione dei fornitori, con tutte le immaginabili complicazioni.
«Sin da subito», ha puntualizzato il titolare, «abbiamo capito cosa facesse davvero al caso nostro e cosa no. Pertanto, ai nuovi fornitori alternativi sono state date specifiche chiare e i flussi sono stati ottimizzati: fra l’avere un buon materiale lavorabile e le certezze che un’ispezione accurata può garantire, c’è parecchia differenza.
E per analizzare le materie prime il ricorso agli strumenti tradizionali – durometri, per esempio – può non bastare. Ideali sarebbero le tecnologie di vaporizzazione, i laser e la lettura dei procedimenti di fusione: sono tutti molto onerosi, però, tanto dal punto di vista economico quanto per la formazione del personale».
Dalla sua, tuttavia, l’azienda veneta ha un parco-clienti vasto dal quale non è mai provenuta alcuna contestazione nonostante le moli di lavoro e di materie prime da trattare, ognuna con le sue specificità e i conseguenti controlli ad hoc. Anche sotto questo aspetto, una relazione di fiducia con la supply chain è determinante, sebbene la si possa costruire solamente lungo il corso del tempo.
Verifiche fatte con lo stampo
Peroni Stampi è specializzata nella progettazione e costruzione di stampi e attrezzature di precisione per la deformazione a freddo della lamiera e ha il suo quartier generale in quel territorio bresciano – a Castegnato – che nelle attività della metallurgia può vantare una tradizione solida e duratura. In più, è legata a doppio filo all’industria automobilistica i cui player sono fra i più esigenti e attenti agli aspetti della qualità dei materiali oltre che del prodotto finito. «I committenti», hanno detto i titolari Mirko e Alessandro Peroni, «ci impongono con le loro richieste di perseguire la massima efficienza generale. Per migliorarla costantemente siamo fortemente focalizzati su quattro aspetti: qualità, puntualità, flessibilità e costi.
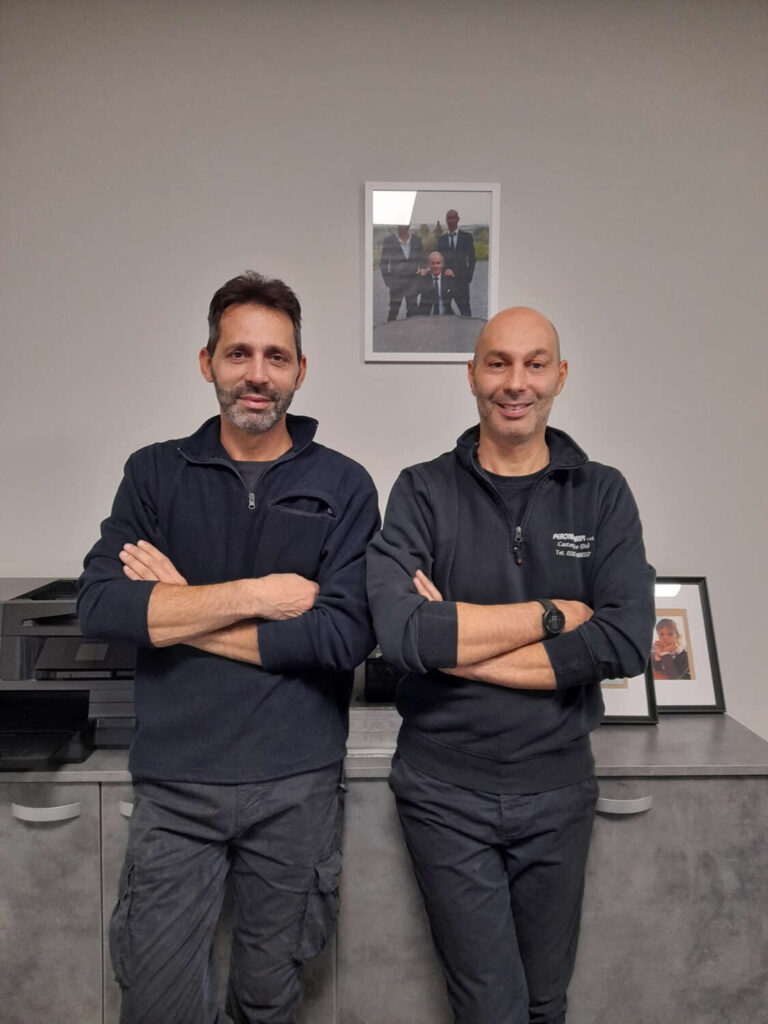
Data l’aggressività dei principali concorrenti di mercato, specie se esteri, questi quattro temi-chiave sono curati con attenzione crescente soprattutto negli ultimi anni e il controllo sui materiali in entrata è un elemento determinante per la nostra attività». Verifiche puntuali e meticolose sono effettuate su tutte le materie prime in uso presso Peroni, che nel reparto stampaggio predilige lamiere in varietà FE 360; 420 e 530 e in attrezzeria ricorre invece per lo più a «varie tipologie di acciaio da costruzione quali C45 e 1-2312 o acciaio da utensili come 1-2379; 1-2343; 1-2842».
Per quanto ogni fornitura sia sempre certificata – con analisi chimica, colata e dimensionale – e provenga da canali di comprovata affidabilità, al ricevimento merci si provvede a ulteriori verifiche: dimensionali, per mezzo di calibri; di quantità tramite pesatura; di qualità (visive) e della durezza mediante durometri. Il traguardo è l’eccellenza del servizio offerto. «Non si può dire che i controlli si siano intensificati a causa delle turbolenze che hanno interessato le materie prime», hanno considerato Mirko e Alessandro Peroni, «che, al contrario, impattano negativamente la marginalità aziendale e la puntualità delle consegne.
Per quanto invece il loro apporto in sede di verifica dei materiali non sia preponderante, gli strumenti di Industria 4.0, fra macchine e soluzioni, sono fondamentali per cogliere il traguardo dell’incremento dell’efficienza».
Dalle norme alla pratica quotidiana
Il production manager della veronese Manni Sipre, Luca Faccioli ha ricordato come nel campo dei controlli qualità la norma di riferimento sia la ISO 9001 che rappresenta una linea guida per le aziende nel redigere procedure a supporto dell’attività. La società del gruppo Manni ha però deciso di andare ben oltre, implementando «una base di controlli addizionali oltre a quelli richiesti dalle normative tecniche di prodotto e interessano una molteplicità di parti e aspetti.
Sono eseguiti già in magazzino prima e dopo il processo produttivo», ha detto Faccioli, «sulla scorta dei parametri normativi. Le procedure prevedono controlli visivi e strumentali come previsto dalle norme di riferimento. I difetti di laminazione o di tipo meccanico visibili sono ispezionati attraverso strumenti dedicati con personale di comprovata esperienza. Per quanto attiene alle dimensioni, fondamentali e sempre verificate, l’intenzione è implementare in futuro tecnologie ispettive laser per le lamiere, in base alle classi di acquisto e le relative tolleranze e sempre in linea con le norme tecniche di prodotto».
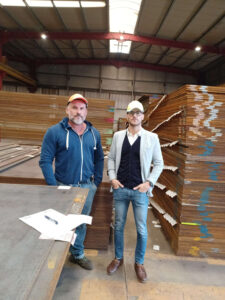
L’azienda, specializzata nella produzione di elementi strutturali in acciaio, analizza poi le varie caratteristiche dei prodotti anche attraverso strumenti analogici (calibri, spessimetri, stecche o altro) essendo questo il metodo più rapido secondo le tolleranze previste dalla norma, anche senza usare strumentazioni digitali. A loro volta tali strumenti sono validati con campioni certificati e custoditi dalle figure responsabili. Anche il peso del materiale è analizzato in occasione del ricevimento-merce; mentre sui carroponti sono stati integrati dinamometri automatizzati per le analisi degli stock in entrata e uscita.
Tutto questo è parte delle consuetudini di Manni: l’esplosione dei costi della materia prima e le carenze non hanno fatto che intensificarlo, causa anche la maggiore attenzione della clientela finale e le sue più frequenti richieste di modifica e personalizzazione dei manufatti. «Nell’industria meccanica per esempio», ha spiegato Faccioli, «accanto alle prove non distruttive (VT, MT e UT) sono oggi più richiesti i test di laboratorio (analisi chimica, prove meccaniche, durezze e resilienza). Il passaggio delle informazioni all’interno della filiera è più stringente poiché più sentito è il tema della sicurezza.
Sono in più di una occasione necessarie lavorazioni aggiuntive in funzione dei possibili limiti di una fornitura; o controlli non distruttivi e di laboratorio, che magari esternalizziamo, anche su materiali già esaminati dalle acciaierie fornitrici».
L’internazionalizzazione ha contribuito a elevare la soglia di attenzione per stoppare sul nascere le eventuali, onerose contestazioni. E oltre che sulle tecnologie, con la prospettiva di installare nuovi rilevatori da agganciare ai carroponti per monitorare i materiali in ingresso, uno sforzo ingente è destinato alla formazione degli addetti, «perché un buon controllo a monte evita problemi a valle».
Allo stesso tempo, si lavora per digitalizzare completamente, in senso 4.0, i processi e flussi di produzione, insieme allo scambio di informazioni e certificazioni fra gli ERP interni e in futuro anche dei fornitori.
Roberto Carminati