Gli ingranaggi in plastica si stanno diffondendo notevolmente e la loro progettazione richiede una particolare attenzione
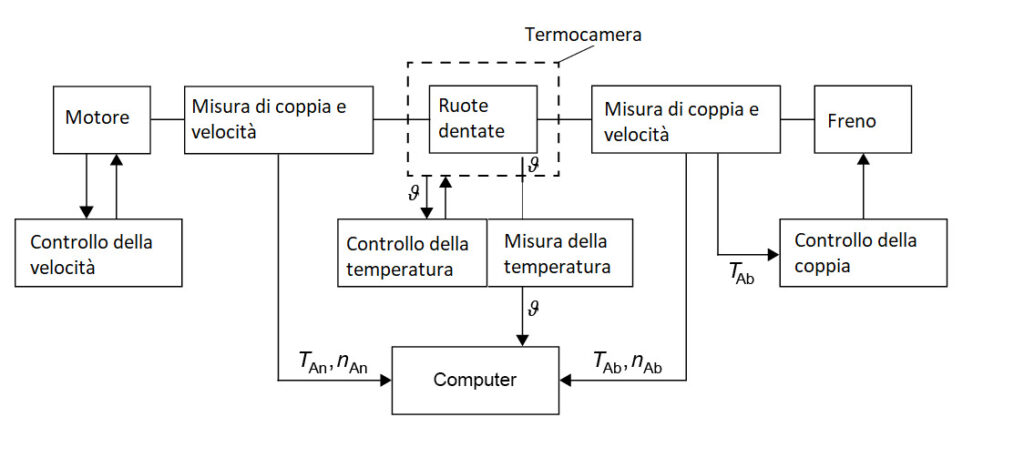
I progettisti di ingranaggi sono abituati alle regole dell’acciaio, sia per quanto riguarda la fabbricazione (taglio per asportazione di truciolo, spesso per generazione), sia per le caratteristiche meccaniche, che rimangono sostanzialmente invariate nel range di temperatura di funzionamento tipico degli ingranaggi in acciaio da cementazione o da bonifica.
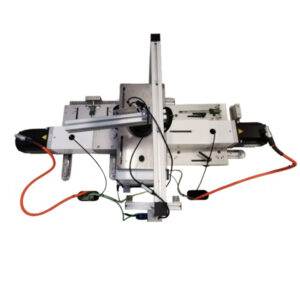
Invece, per quanto riguarda la plastica, la forma del dente e di tutto il corpo ruota è molto più libera, perché spesso si tratta di ingranaggi stampati, e i materiali sono tantissimi, per via delle combinazioni di matrici (POM, PA, PET, …), additivi (fibre di carbonio o vetro, lunghe o corte, in percentuali diverse) e lubrificanti (teflon, grafite…).
Inoltre, lo stesso materiale presenta caratteristiche meccaniche molto diverse in funzione della temperatura e del lubrificante.
Una corretta progettazione degli ingranaggi in plastica
Per una corretta progettazione o scelta delle ruote in plastica è quindi fondamentale la conoscenza perlomeno dei limiti di fatica a flessione del dente del materiale, in funzione della temperatura: proprio per questo motivo è stato realizzato dalla Longato Srl il banco prova descritto qui di seguito.
Il banco prova è del tipo “non mechanically closed loop”, come indicato nella VDI 2736 parte 4 (fig. 1).
La velocità e la coppia del motore e del freno sono controllati da un encoder e da un torsiometro (fig. 2). Gli ingranaggi sono collocati all’interno di una cella climatica per eseguire test a temperature differenti (fig. 3).
L’interasse di montaggio viene scelto in modo garantire il gioco in tutto il range di temperature, da quella di montaggio a quella di test. I diversi coefficienti di dilatazione termica dei vari materiali (ruote e cassa) richiedono infatti un’attenta analisi di questo aspetto, che viene preventivamente eseguita sul software KISSsoft.
La temperatura all’interno della cella climatica può essere gestita mantenendo costante la temperatura del fianco del dente o del piede del dente o dell’aria all’interno della cella stessa.
La cella climatica viene costantemente tenuta in controreazione attraverso un software di controllo che riceve ed elabora i segnali termici inviati sia dalla sonda PT100 che si trova al suo interno, sia dalla termocamera (fig. 4).
Il banco prova è in grado di eseguire test a secco, in bagno d’olio o con grasso.
Nel banco è stato implementato un sistema di arresto istantaneo della rotazione che interviene appena si verifica la rottura di un dente (figura in apertura: Sistema di arresto istantaneo della rotazione, in caso di rottura di un dente).
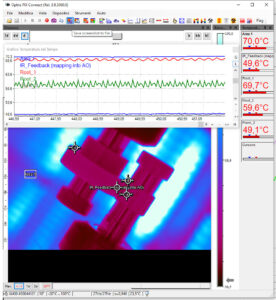
Le caratteristiche del banco prova sono le seguenti:
- Interasse: da 20 mm a 150 mm con risoluzione ± 0,01 mm
- Coppia: fino a 10 Nm con risoluzione ± 0,1 %
- Velocità: da 500 a 4000 rpm con risoluzione 20 bit/rev
- Temperatura: da -15 °C a + 150 °C con risoluzione termo camera. ± 0,037 °C.
Le condizioni di prova sono definite dai seguenti tre parametri:
- velocità dell’albero di ingresso [giri/min],
- temperatura del fianco del dente della ruota da testare [°C],
- momento torcente sull’ingranaggio condotto [Nm].
Prima del test, gli ingranaggi vengono messi in rotazione a velocità costante senza l’intervento del freno, fino al raggiungimento della temperatura richiesta, per favorire un riscaldamento graduale e uniforme.
Ovviamente, questa fase transitoria di riscaldamento verrà successivamente eliminata durante la post-elaborazione.
L’errore medio calcolato sulle misure effettuate è inferiore al 2%.
I punti medi di ogni prova su un grafico semilogaritmico mostrano una correlazione del 97% (grafici 1 e 2).
A parità di materiale si evidenzia che le due curve hanno pendenze diverse per temperature diverse.
Geometria delle ruote testate
Per derivare le caratteristiche del materiale dai risultati delle prove sperimentali è stato usato il modulo Plastic Manager del software KISSsoft (fig. 5), che segue le indicazioni della VDI 2736-4 e richiede la conoscenza della geometria delle ruote testate.
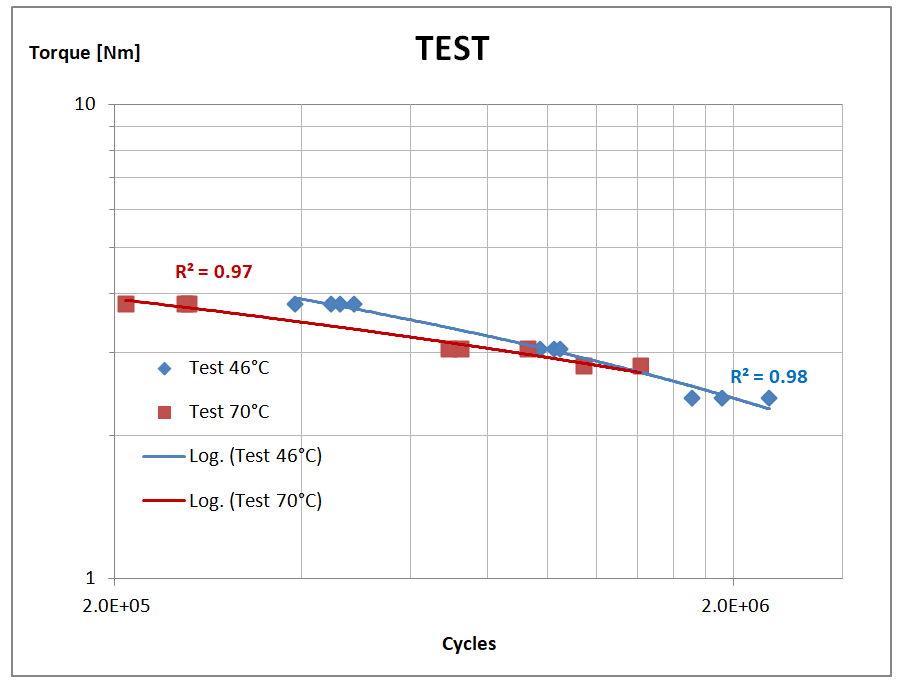
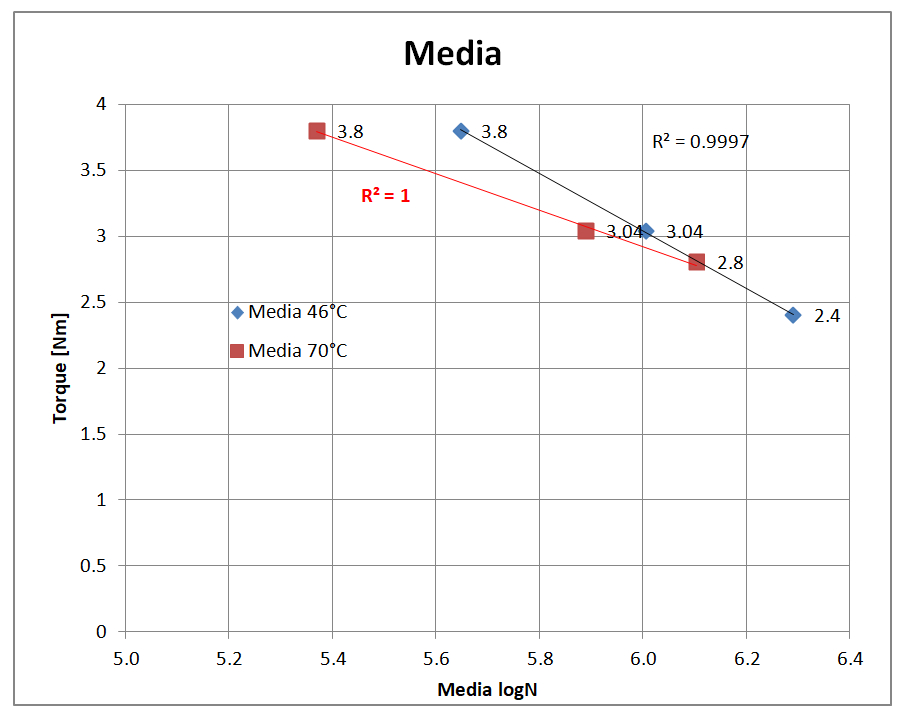
Nel caso in esame, non erano disponibili né i disegni di progetto né i modelli CAD degli ingranaggi. È stata quindi rilevata la geometria con uno scanner 2D e 3D.
Il confronto tra la geometria misurata (nuvola di punti) e la geometria generata da KISSsoft è mostrato nelle figure 6 e 7.
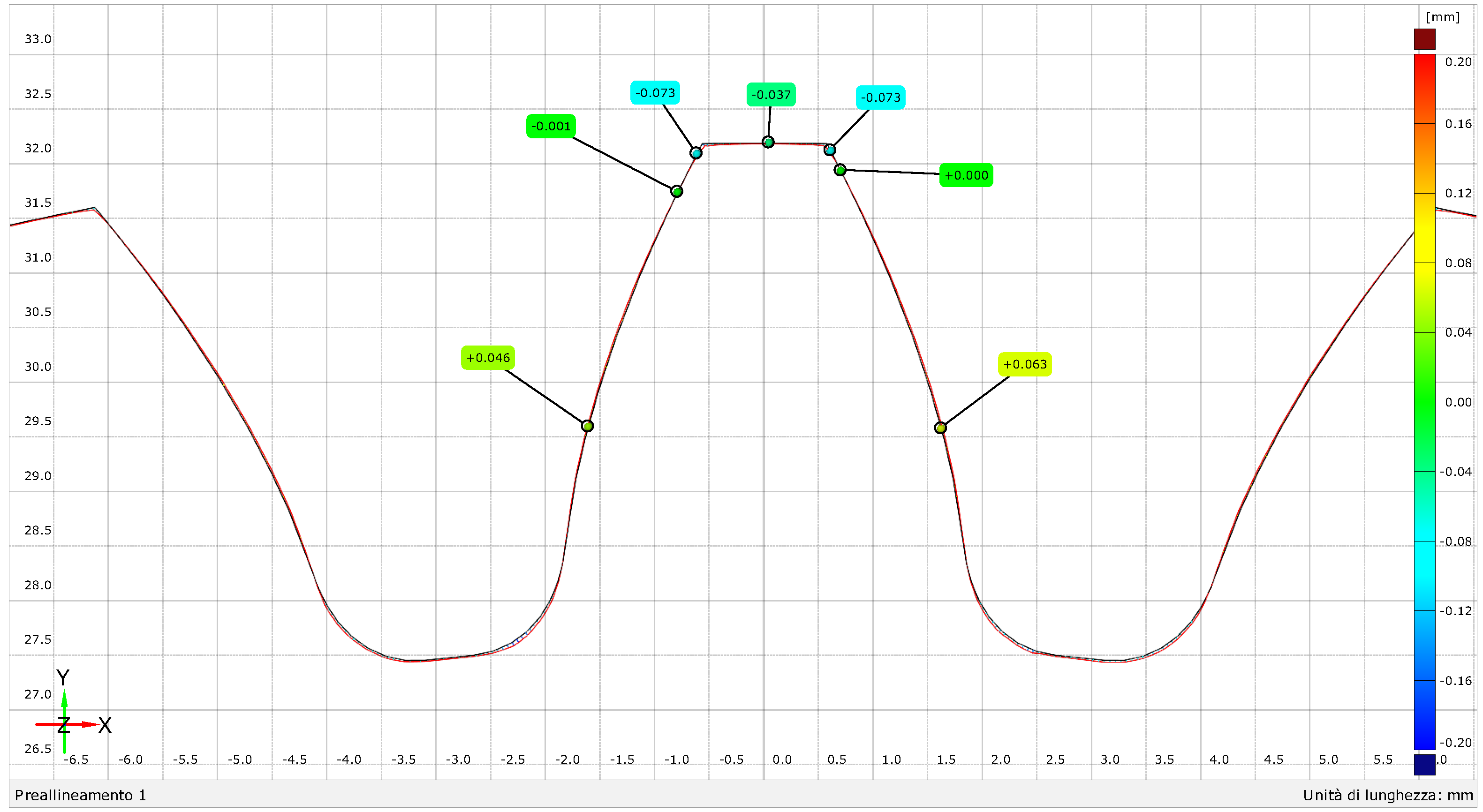
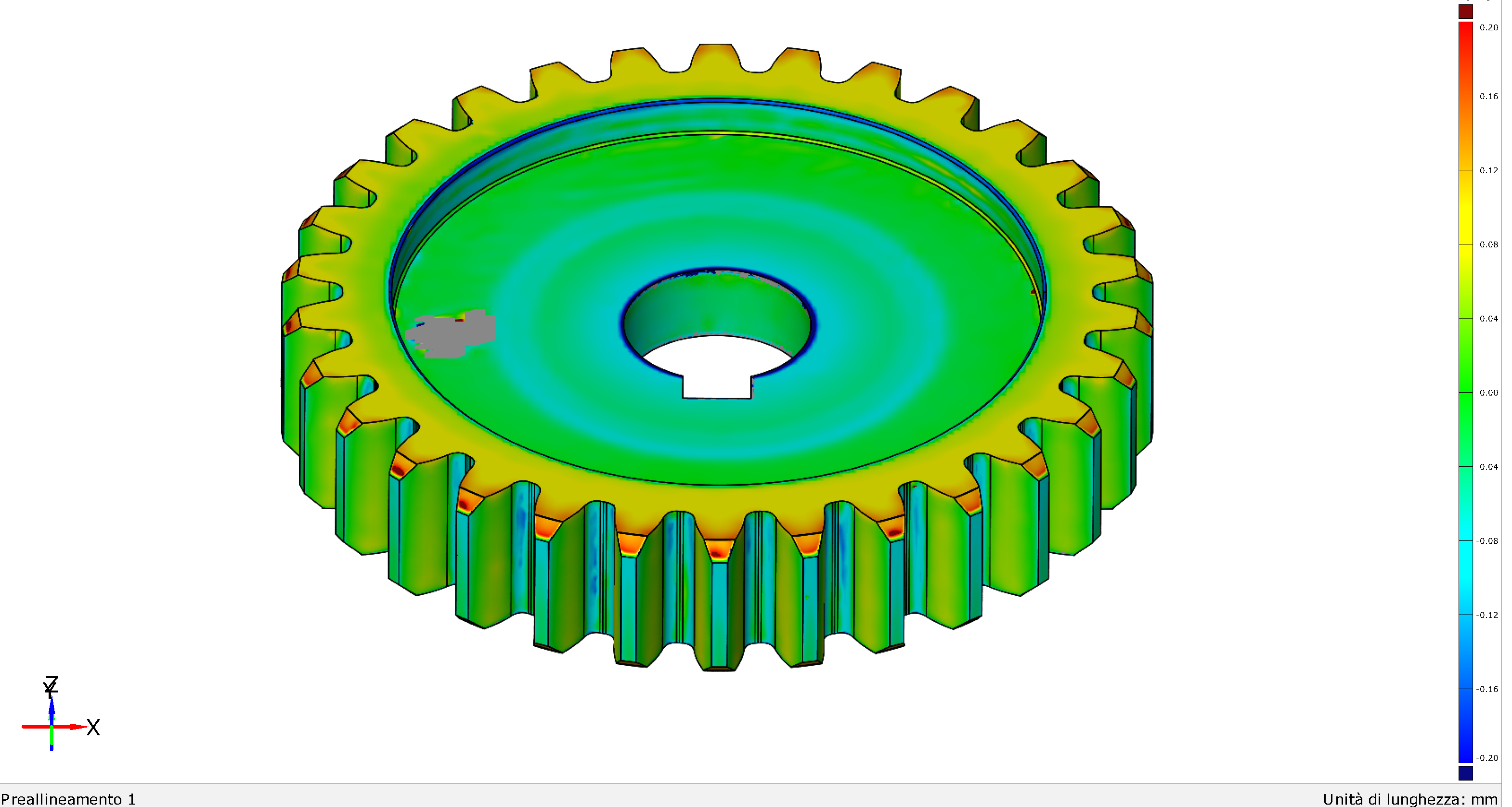
Uno speciale ringraziamento va a UNILAB Laboratori Industriali s.r.l. per il supporto prestato.