I vantaggi della tolleranza zero sono molteplici: dalla flessibilità produttiva per la scelta della tolleranza da utilizzare per dimensione e posizione, alla riduzione dei costi di produzione attraverso la diminuzione degli scarti
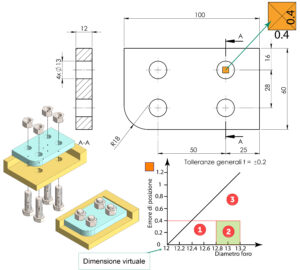
Molti progettisti sarebbero perplessi davanti a un’indicazione di una tolleranza zero nel disegno del componente di figura 1; in realtà, con questa prescrizione, si può ottenere il massimo vantaggio dall’interrelazione dimensione-posizione di un elemento, ottenendo il miglior bilanciamento tra le esigenze progettuali e produttive. Per questo motivo, l’indicazione di tolleranza zero deve essere sempre seguita dal simbolo di massimo o minimo materiale. Si consideri l’assieme mostrato in figura 2 in cui una piastra con 4 fori viene assemblata con 4 bulloni (vite + dado). Nella stessa figura viene mostrata la quotatura tradizionale della piastra, senza tolleranze geometriche: la zona di tolleranza dei fori ha forma prismatica, con una sezione quadrata di lato 0.4 mm (equivalente alla tolleranza generale). Si osservi a questo proposito il diagramma di analisi delle tolleranze, in cui sulla scala delle ordinate troviamo i valori della tolleranza di localizzazione e su quella delle ascisse le dimensioni consentite dei fori (la dimensione minima corrisponde alla dimensione virtuale VC).
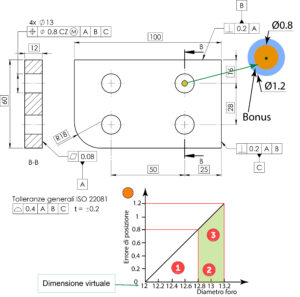
L’area tratteggiata di colore verde rappresenta la zona dei pezzi accettabili al controllo, per cui i pezzi, i cui fori siano stati misurati e contrassegnati con i numeri 1 e 3, vengono scartati.
Il componente disegnato con la quotatura a coordinate è difficilmente verificabile dal punto di vista metrologico, soprattutto per la mancata indicazione di riferimenti ed errori di forma e posizione. Pertanto, nel caso della figura 3, la piastra viene quotata con i necessari requisiti dimensionali e geometrici, calcolando la tolleranza di posizione con la formula:
Toll. = FMMC – V = 12.8 – 12 = 0.8 mm
dove FMMC è la dimensione del foro al massimo materiale e V la dimensione della vite. Si noti che la dimensione virtuale del foro è: VC = 12.8 – 0.8 = 12 mm.
I fori vengono localizzati con una tolleranza di posizione 0.8 col modificatore del massimo materiale, ottenendo un bonus di 0.4 mm. La zona di tolleranza è cilindrica e l’area tratteggiata del diagramma diventa più estesa: si evita quindi di scartare il componente 3 i cui fori rientrano nella zona verde.
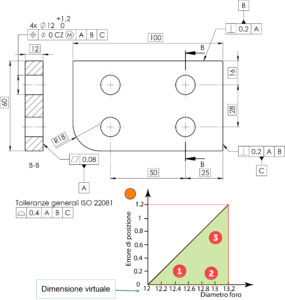
Nella figura 4 la tolleranza di posizione dei fori viene ridotta da 0.8 mm a un errore “zero” col modificatore di massimo materiale, aumentando però della stessa quantità la tolleranza dimensionale. In pratica il diametro limite minimo del foro (12) viene ottenuto sottraendo la tolleranza di posizione 0.8 dalla dimensione al massimo materiale (12,8), mentre il diametro limite massimo resta invariato (13.2). In questo caso si evita di scartare tutti i componenti i cui fori sono contrassegnati col numero 1, sicuramente accettabili dal punto di vista funzionale.
I vantaggi della tolleranza zero
Da un punto di vista pratico, i vantaggi della tolleranza zero sono molteplici, tra i quali: a) aumento della tolleranza dimensionale b) flessibilità produttiva per la scelta della tolleranza da utilizzare per la dimensione e per la posizione; c) riduzione dei costi di produzione attraverso la riduzione degli scarti.
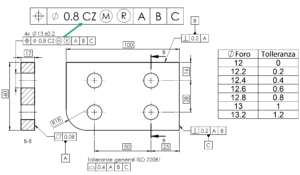
Figura 5 – In alternativa all’indicazione di tolleranza zero, è possibile utilizzare il requisito di reciprocità (RPR) che deve essere indicato insieme al requisito di massimo o minimo materiale, inserendo nel riquadro delle tolleranze il simbolo Ⓡ. Il requisito RPR consente di aumentare la tolleranza dimensionale quando la deviazione geometrica sul pezzo reale non viene sfruttata al massimo valore, secondo i valori della tabella
Come evitare la tolleranza zero?
Esiste un modo per evitare la tolleranza zero (non molto simpatica agli ingegneri di produzione)? È possibile utilizzare il requisito di reciprocità (RPR) che deve essere indicato insieme al requisito di massimo o minimo materiale, inserendo nel riquadro delle tolleranze il simbolo Ⓡ come in figura 5. Il requisito RPR consente di aumentare la tolleranza dimensionale quando la deviazione geometrica sul pezzo reale non viene sfruttata al massimo valore, consentendo una scelta flessibile della distribuzione dell’errore consentito tra tolleranze dimensionali e geometriche in base alle capacità di produzione. Da sottolineare che il simbolo di reciprocità sia un simbolo delle norme ISO, quindi non disponibile nello standard ASME.
(di Stefano Tornincasa, Politecnico di Torino)