Dalla sua invenzione nel 1960, il laser non ha mai smesso di sorprenderci. In questo articolo parliamo di come usarlo per la pulitura tramite ablazione.
Prima di qualsiasi lavorazione, e spesso anche dopo, la maggior parte dei pezzi deve essere pulita. Saldatura, verniciatura, incollaggio: tutti questi processi richiedono una superficie di metallo intatta. Sarebbe bello prendere due lamiere dal piazzale e saldarle così come sono; purtroppo, quasi sempre la zona di saldatura andrà molata o spazzolata per rimuovere calamina o ruggine: un lavoro lento, rumoroso e inefficiente.
In molti casi anche dopo la saldatura i pezzi vanno ripassati per togliere scorie e ossidi che possono causare corrosione. Nel caso dell’acciaio inossidabile, la zona termicamente alterata e le caratteristiche zone colorate sono anche un difetto estetico da eliminare. Per ripristinare il film di passivazione servono sostanze chimiche pericolose e una mano esperta.
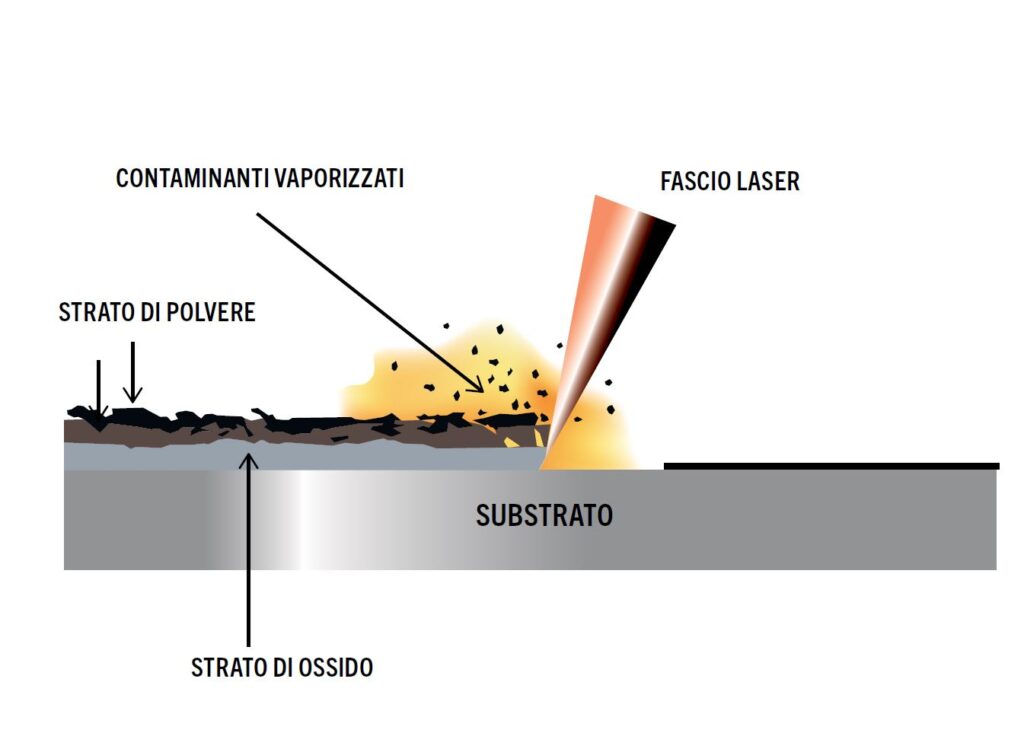
Lo stesso accade quando bisogna rimuovere altre sostanze come olio, polvere, grasso, vernice, e altre impurità per ripristinare la corretta funzionalità. In determinati settori come quello alimentare o navale, le incrostazioni di microorganismi, batteri e alghe producono il cosiddetto biofilm o biofouling, e devono essere periodicamente rimossi.
Nella maggior parte dei casi bisogna dotarsi di attrezzi specifici oppure solventi chimici aggressivi, che devono essere maneggiati con cautela e smaltiti correttamente.
Fortunatamente, da alcuni anni sono apparsi sul mercato dei dispositivi laser in grado di rimuovere facilmente e velocemente sporco e altri contaminanti. Si tratta della pulitura laser o laser cleaning: un processo che, tramite un raggio laser, fa sublimare lo strato superficiale senza danneggiare il metallo sottostante. Si tratta di un procedimento per certi versi analogo all’usare il taglio laser a bassa potenza per tagliare la pellicola protettiva delle lamiere di acciaio inox, senza però intaccare la lamiera stessa. Ma qual è il principio fisico alla base della pulitura laser?
Una questione di fisica
Il concetto fondamentale da tenere a mente è la cosiddetta soglia di ablazione (Ablation Threshold). È una caratteristica peculiare di ogni materiale, e definisce in sostanza il livello di energia e di lunghezza d’onda sotto la quale non avviene la sublimazione. Per nostra fortuna, la soglia di ablazione degli ossidi, delle vernici, e delle altre sostanze contaminanti è inferiore a quella del metallo sottostante. Regolando opportunamente i parametri di processo è quindi possibile pulire lamiere, attrezzi, e altri oggetti metallici.
Quali tipologie di laser, potenze, e lunghezze d’onda vengono usate? Lo abbiamo chiesto a Guillaume Jobin, Specialista di Applicazione alla Laserax, una ditta canadese specializzata in sistemi di pulitura laser. «Le potenze sono comprese tra i 10 W e i 3 kW a seconda dell’applicazione e dei tempi ciclo richiesti. A maggiore potenza corrisponde una lavorazione più veloce», ci spiega. «Inoltre, alcuni contaminanti come la scaglia di laminazione, richiedono energie più alte per essere rimossi, e quindi più potenza».
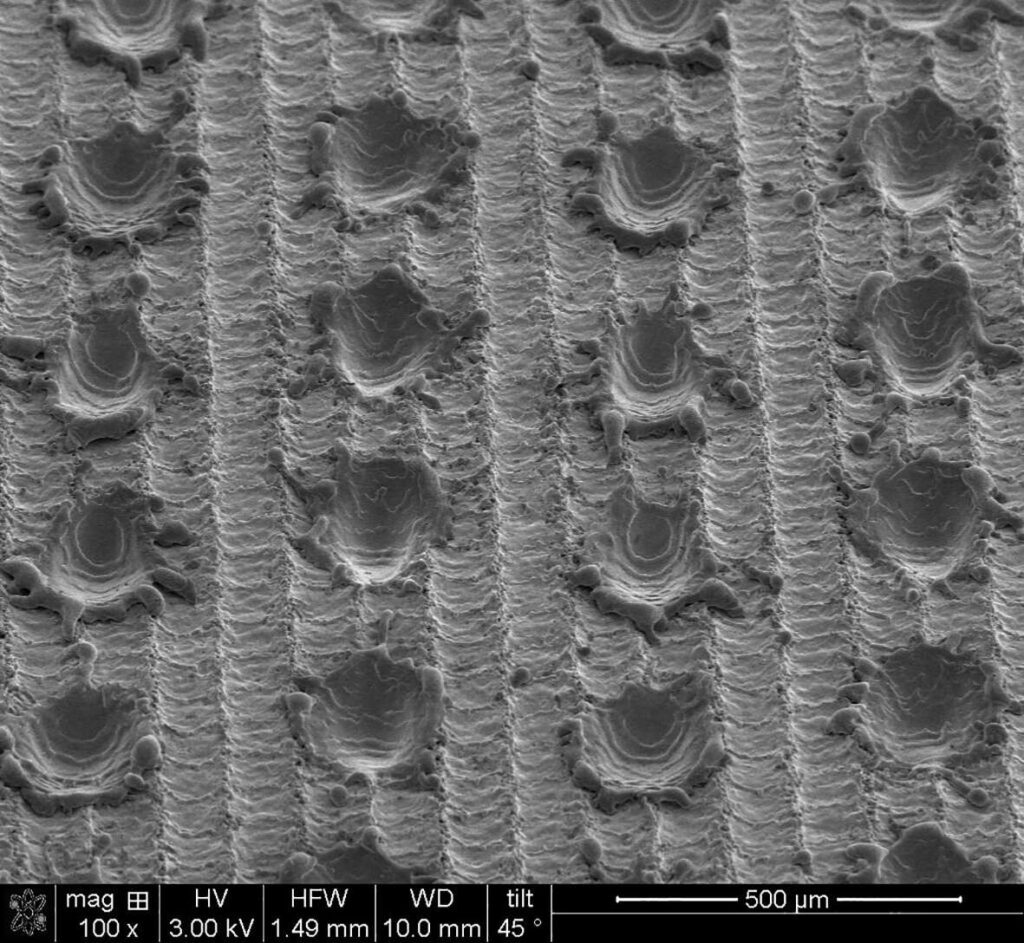
Per avere un’idea dei parametri in gioco, in tabella ritroviamo le velocità e le potenze specificate da Laserax per la pulizia da ruggine, vernice, e altri contaminanti. Per quanto riguarda la tipologia di laser e la lunghezza d’onda, solitamente si usano sorgenti fibra a 1064 nm: a questo valore corrisponde un buon assorbimento da parte di acciaio, alluminio, magnesio e zinco. Ma non tutti i materiali possono essere puliti con l’ablazione laser.
«La soglia di ablazione del substrato deve essere più alta di quella dei contaminanti, altrimenti andremmo a danneggiare il materiale base. Per questo motivo la pulitura laser non si può usare per la plastica, ma può essere invece usata per le superfici ceramiche», continua Guillaume Jobin. Oltre alla soglia di ablazione entrano in gioco anche altri fattori.
Ad esempio, la conducibilità termica: ruggine e polvere conducono meno il calore, e quindi evaporano prima. La parte di calore che viene trasferita al metallo base non ha energia sufficiente ad intaccarlo. Inoltre, i contaminanti sono spesso materiali opachi, e quindi assorbono maggiormente l’energia.
Parliamo di laser
Sebbene sia teoricamente possibile utilizzare un fascio laser continuo, nella quasi totalità delle applicazioni la sorgente lavora in modalità pulsata, in quanto si possono raggiungere gli elevati picchi di energia necessari per l’ablazione. Il raggio è quindi sotto forma di impulsi ad alta potenza ma breve durata, dell’ordine dei nanosecondi.
In questo modo facciamo evaporare istantaneamente il materiale indesiderato. Così evitiamo il surriscaldamento del substrato, che non sarebbe sublimato (a causa della più alta soglia di ablazione), ma potrebbe subire comunque effetti termici localizzati.
«La pulitura laser può rimuovere contemporaneamente sia l’ossido che la sporcizia di vario tipo» spiega l’ing. Jobin, «eliminando la necessità di usare prodotti chimici o processi differenti, e riducendo inoltre il tempo richiesto dalle attività di preparazione prima della saldatura». Come si vede dalle immagini, trattare la zona da saldare prima della saldatura diminuisce i difetti nel cordone causati dall’inclusione di impurità e bolle di gas.
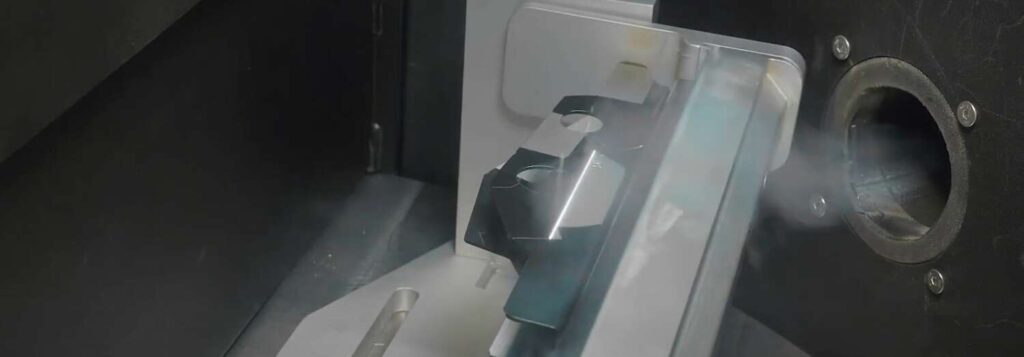
Un altro importante vantaggio di questo processo è che non diffonde sostanze chimiche nel substrato. Inoltre, non avendo parti a contatto con il pezzo, può essere usato anche tra materiali differenti. Possiamo quindi pulire acciaio comune e poi acciaio inox senza problemi, al contrario degli utensili tradizionali. Come sa bene chi lavora l’inossidabile, bisogna evitare assolutamente di usare la stessa spazzola o mola abrasiva prima su ferro comune e poi su inox, per evitare la corrosione dovuta alla contaminazione da carbonio.
In commercio esistono sia laser a fibra monomodali che multimodali: quali sono le differenze? «Il vantaggio dei laser monomodali è la possibilità di imprimere una trama superficiale, che migliora la successiva adesione di vernici o adesivi», continua l’ing. Jobin. «I laser multimodali non possono raggiungere la stessa densità di energia focalizzata dei laser monomodali, ma possono raggiungere una potenza media più elevata e hanno un fascio più ampio, che consente di pulire superfici più ampie e più rapidamente».
Un’altra importante applicazione dell’ablazione laser è la rimozione selettiva della vernice. In questo modo si può ridurre di molto la necessità della mascheratura, ovvero l’applicazione di nastri adesivi e altre pellicole o sostanze a protezione delle parti che non devono essere rivestite. Con il laser si può rimuovere la vernice nei punti desiderati con precisione, sia per processi successivi che per ragioni estetiche. Tutto il processo è controllato dal controller laser, una centralina che pilota tutti gli altri componenti della macchina, come la sorgente e gli specchi galvanometrici.
Gli utenti possono modificare i parametri nel software per ottenere risultati diversi, come la distanza tra le linee, la distanza degli impulsi, la frequenza degli impulsi, l’energia degli impulsi ecc. La casa madre preimposta tutti questi parametri per i suoi clienti prima della spedizione, in base alle loro esigenze. I parametri possono essere modificati in base alle necessità future, anche tramite strumenti di assistenza remota per aiutare gli utenti ad aggiornare i laser per nuove applicazioni o per risolvere eventuali problemi che possono verificarsi.
Ad esempio, variazioni di temperatura non pianificate sulla superficie del metallo o variazioni del livello di contaminanti, che a loro volta influenzano il modo in cui devono essere impostati i parametri di pulizia.
Entriamo in fabbrica
Le macchine per la pulitura laser sono tendenzialmente semplici da usare. Per padroneggiare le funzioni base della macchina serve una formazione di poche ore, che solitamente avviene presso la sede del cliente durante l’installazione. Possono essere necessari alcuni giorni di training approfondito se gli utenti vogliono imparare a controllare parametri laser più complessi e specifici.
Nella maggior parte dei casi, però, il laser è già operativo e non è quindi necessario alcun addestramento extra. Le macchine sono normalmente preconfigurate in fabbrica, ottimizzate per un’applicazione specifica (calamina, ossido, vernice ecc.) sulla base di quanto richiesto dal cliente. Preconfigurazioni aggiuntive possono essere caricate automaticamente per adattarsi a nuovi materiali e condizioni di lavoro. A livello di sicurezza, le precauzioni e protezioni richieste sono analoghe a quelle comunemente utilizzate per il taglio laser e per la saldatura.
La distinzione principale è tra sistemi manuali e impianti a cabina chiusa. Per i primi, i produttori raccomandano una protezione a doppia sicurezza, un interblocco a distanza, avvisi luminosi, occhiali di sicurezza per laser, un’area di lavoro isolata con segnali di avvertimento, e ovviamente un’adeguata formazione.
Per i secondi, i carter di protezione della macchina impediscono la fuoriuscita della radiazione laser, come nelle macchine da taglio. Entrambe le tipologie di macchina richiedono un efficace sistema di estrazione dei fumi e di filtraggio delle polveri. Ciò è particolarmente importante per le applicazioni di sverniciatura, che rilasciano pericolosi inquinanti nell’aria.
«La cattura dei fumi è più efficace quando la bocchetta di aspirazione è posizionata vicino alla fonte. Alcuni produttori eseguono la pulizia laser contemporaneamente alla saldatura e sfruttano un unico aspiratore di fumi di saldatura per entrambe le lavorazioni», conclude l’ing. Jobin. La torcia laser è infatti di piccole dimensioni, e per questo può essere installata accoppiata alla torcia di saldatura negli impianti robotizzati o automatizzati. Lo stesso robot può quindi eseguire la preparazione del pezzo, la saldatura, e la pulizia del cordone.
Marco Basso