Industria 4.0 e IIoT costituiscono le basi per una completa digitalizzazione dei processi di produzione e manutenzione. In questo contesto, il ruolo dei cuscinetti sta subendo una profonda trasformazione.
Oggi l’Industria 4.0 e l’Industrial Internet of Things (IIoT) stanno ponendo le basi per una completa digitalizzazione dei processi di produzione e manutenzione nell’ottica di quella che sarà la fabbrica intelligente del futuro.
La crescente interconnessione, la necessità di elaborare grandi moli di dati e processi decisionali decentralizzati stanno cambiando il modo di concepire, progettare, fabbricare e manutenere i prodotti.
Sarà sempre più richiesto uno scambio continuo di informazioni in tempo reale tra produttori, costruttori di macchine, operatori e team di manutenzione. Cambiamenti significativi si stanno già verificando nei modelli di business e nei reparti di progettazione.
Temi come il consumo energetico, macchine modulari, facilità di manutenzione e ridondanza, stanno iniziando ad assumere un nuovo significato.
Cruciale sarà la pianificazione a supporto della produzione automatizzata dove i tempi di inattività ed eventuali componenti difettosi saranno ridotti al minimo.
Un ulteriore contributo nella trasformazione delle organizzazioni è legato poi allo sviluppo dell’intelligenza artificiale (AI) e delle tecnologie cognitive, nonché la loro integrazione con i processi produttivi per favorire l’eccellenza operativa.
In generale, il processo di produzione 4.0 dovrebbe essere in grado di auto-organizzarsi, i prodotti dovrebbero sapere in qualsiasi momento a che punto si trovano all’interno del ciclo di produzione e le macchine dovrebbero essere dotate di meccanismi di controllo indipendenti. Il focus è sui dati a supporto di processi produttivi automatizzati.
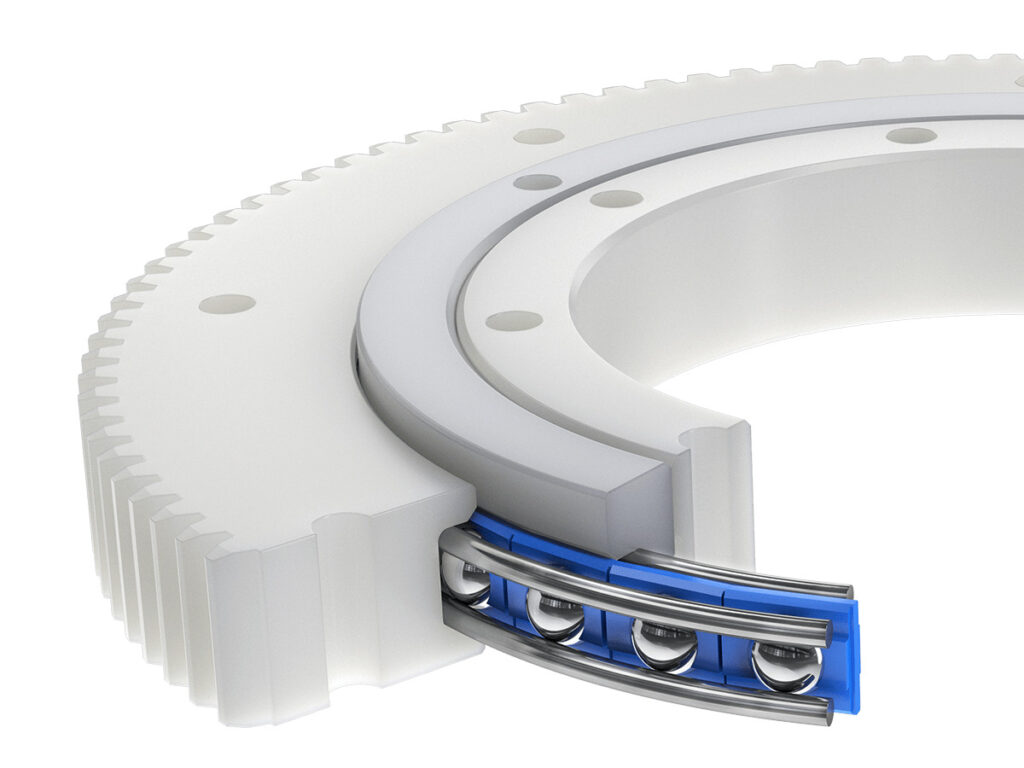
In questo contesto, il ruolo dei cuscinetti sta subendo una profonda trasformazione. I cuscinetti sono componenti chiave in qualsiasi macchinario o apparecchiatura industriale. Tutti gli elementi rotanti e oscillanti richiedono cuscinetti a supporto delle loro funzioni, garantendo funzionalità e precisione della macchina stessa.
Essi trovano impiego in migliaia di applicazioni: industriali, automobilistiche, marine, aerospaziali, etc. Nelle applicazioni industriali di fascia alta, come treni ad alta velocità, aerei, generatori di turbine eoliche, etc., le condizioni di salute dei cuscinetti determinano la sicurezza e l’affidabilità dell’intero sistema.
Basti pensare che, come suggerisce la letteratura, i cuscinetti sono responsabili di circa il 45-55% dei guasti a macchinari e apparecchiature. Rilevare e misurare le variabili relative alle condizioni di un cuscinetto rappresenta quindi oggi un passo fondamentale.
Il condition monitoring dei cuscinetti del futuro
Per decenni il design dei cuscinetti ha seguito criteri consolidati. Le novità hanno riguardato principalmente l’impiego nuovi materiali (come i ceramici, i polimeri e soluzioni ibride) e nuove opzioni in termini di lubrificazione.
In figura 1, ad esempio, si riporta un cuscinetto assemblato in polimero con elementi di scorrimento e rotolamento in acciaio inox. Tipicamente, i materiali costitutivi di un cuscinetto servono a migliorarne il funzionamento.
Altri elementi di progettazione cruciali per i cuscinetti del futuro sono sintetizzati in figura 2. Un aspetto fondamentale in fase di progettazione riguarda soluzioni per il miglioramento dell’affidabilità del cuscinetto, misurata valutandone prestazioni e durata di vita.
Migliorare l’affidabilità dei cuscinetti significa aumentare il tempo medio che intercorre tra un guasto e il successivo.
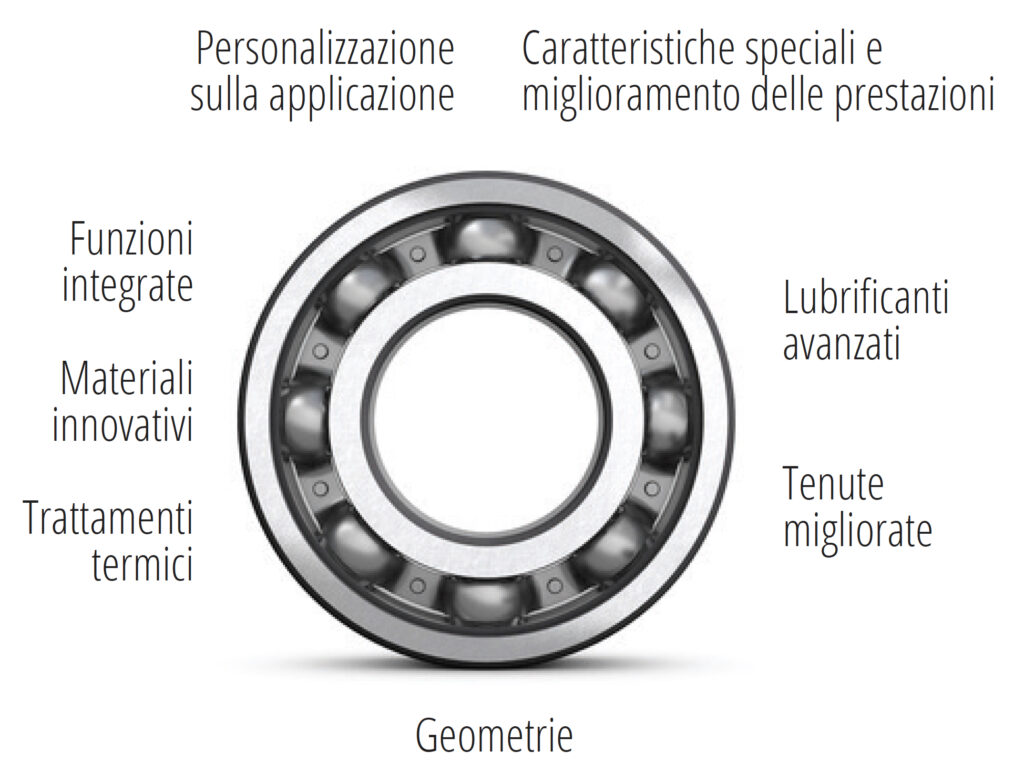
In condizioni operative severe, l’affidabilità del cuscinetto può essere migliorata attraverso speciali trattamenti termici, l’impiego di materiali avanzati, la scelta di corretti interventi di movimentazione, manutenzione e montaggio, tolleranze di produzione più rigide, l’aumento della resistenza all’usura, l’implementazione di migliori lubrificanti, la prevenzione della corrosione, la riduzione dell’attrito e delle particelle da esso derivanti, dell’erosione galvanica, e del surriscaldamento.
Talvolta i cuscinetti subiscono un danneggiamento inaspettato in sede progettuale.
Oggi, grazie alla digitalizzazione, cuscinetti intelligenti sono in grado di autodiagnosticare guasti e rotture imminenti.
Sensori integrati direttamente nel componente consentono di rilevare una serie di parametri, successivamente trasmessi a un sistema di controllo, dove tecnici specializzati potranno accedere alle informazioni in tempo reale sulle condizioni e lo stato di salute dei cuscinetti e di altri componenti.
In questo modo è possibile mettere a punto un sistema di diagnostica avanzata, con avvisi tempestivi in caso di deterioramento delle condizioni dei cuscinetti.
Si parla quindi di un approccio proattivo alla manutenzione che, anziché limitarsi a gestire i segnali di un errore in corso, è in grado di intervenire e risolvere le cause alla radice del problema, con tutti i vantaggi correlati alla sicurezza e al prolungamento della vita utile del componente o della macchina.
In condizioni operative, per massimizzare la durata e determinare i periodi di sostituzione dei cuscinetti nonché gli intervalli di reintegro del lubrificante, indicatori chiave di prestazione, misurabili mediante appositi strumenti e sensori, sono la rumorosità, le vibrazioni, la temperatura e lo stato del lubrificante stesso.
Essi permettono, analizzandone le caratteristiche, di rilevare e distinguere possibili guasti imminenti. Ad esempio, è possibile distinguere un danno ai corpi volventi grazie al rumore prodotto e anche risalire alle possibili cause favorendo l’adozione di contromisure preventive.
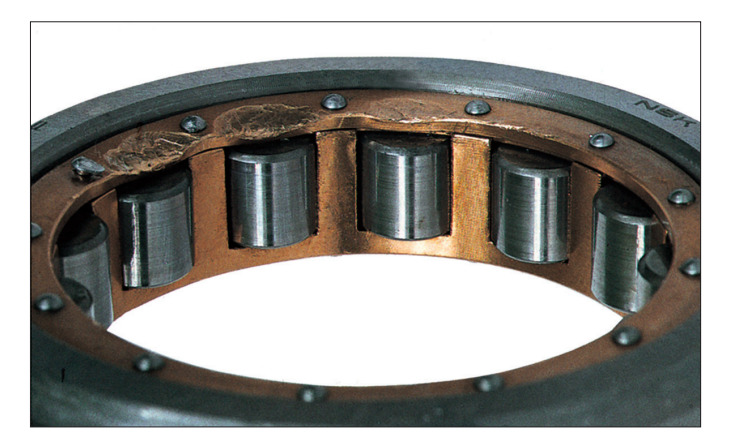
Inoltre, durante le ispezioni periodiche della macchina e le sostituzioni dei componenti, il cuscinetto dovrebbe essere ispezionato a fondo, per valutare le sue reali condizioni e decidere se sia possibile continuare ad utilizzarlo o meno.
Ad esempio, le tracce sui corpi volventi forniscono una serie di preziose informazioni, consentendo di capire se si siano verificati carichi imprevisti o errori di montaggio.
Sistemi avanzati di diagnostica permettono poi di individuare la natura del guasto e le possibili cause al fine di adottare appropriate misure correttive e preventive.
Misure efficaci ridurranno l’insorgere di guasti simili o li impediranno. In figura 3, la gabbia in ottone di un cuscinetto a rulli cilindrici presenta una deformazione della faccia laterale a causa di un forte urto durante il montaggio.
Importanza della fase di montaggio
Come già evidenziato, il montaggio di un cuscinetto è uno degli aspetti più impattanti sulle sue prestazioni e sulla sua durata.
Secondo alcune stime, un caso su sei cedimenti prematuri dei cuscinetti è imputabile a errori di montaggio o movimentazione.
Anche per i cuscinetti del futuro, la fase di montaggio richiederà esperienza, precisione, cura e pulizia oltre a metodi e strumenti adeguati.
Selezionato il metodo di montaggio più idoneo, seguono una serie di attività preparatorie con lo scopo di identificare il tipo, le dimensioni e la variante del cuscinetto più adeguata per l’applicazione.
È importante, durante le varie fasi, preservare le condizioni di stoccaggio del cuscinetto, che, idealmente, dovrebbe essere conservato in un locale asciutto, su scaffali non soggetti a vibrazioni, nella sua confezione originale chiusa e integra, per evitare l’esposizione ad agenti contaminanti e corrosione.
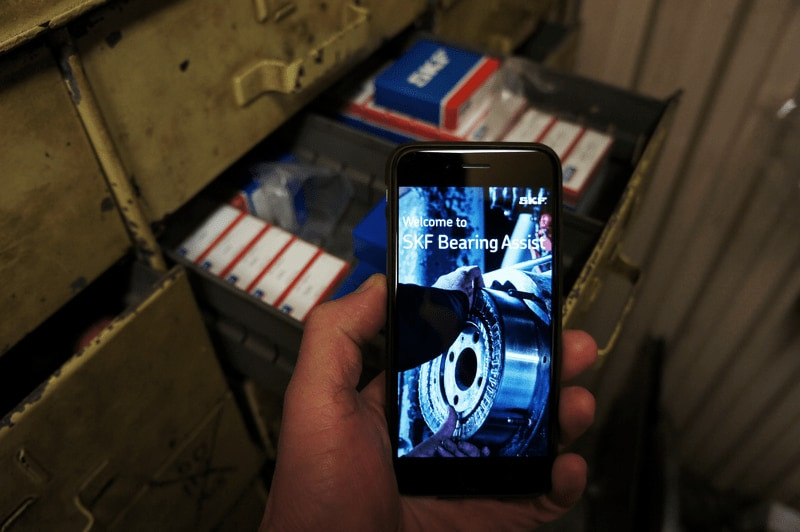
Stesso discorso vale per l’ambiente di montaggio del cuscinetto, che deve essere adeguatamente protetto da umidità, polvere, trucioli ed altri sottoprodotti dei processi di lavorazione.
In sintesi, è consigliabile che un processo di montaggio includa le seguenti fasi:
- Pulizia del cuscinetto e delle aree circostanti;
- Controllo delle dimensioni e delle condizioni di finitura dei componenti;
- Rispetto della procedura di montaggio;
- Corretto utilizzo del lubrificante.
Inoltre, dopo il montaggio, è sempre importante effettuare un test di funzionamento per confermare che il cuscinetto sia stato montato correttamente.
Nel contesto di fabbrica intelligente, è chiaro quanto, nella fase di montaggio giochi un ruolo chiave la condivisione delle informazioni.
Oggi le aziende sono continuamente alla ricerca di nuovi strumenti e soluzioni che, grazie alle tecnologie informatiche, possano agevolare attività e processi mediante lo scambio di informazioni.
In figura 4, a titolo di esempio, si mostra “Bearing Assist”, un’ applicazione sviluppata da SKF e implementata per la mappatura dei problemi di montaggio dei cuscinetti.
“Gemelli digitali” a supporto dei cuscinetti del futuro
I moderni processi produttivi e macchine sempre più sofisticate rendono i potenziali guasti o fermi impianto economicamente gravosi.
A supporto del problema, gli approcci più recenti contemplano la creazione e implementazione di “gemelli digitali”, o “digital twins”, nella progettazione, produzione e gestione del ciclo di vita dei cuscinetti volventi (Klebanov et al.).
Un “gemello digitale” non è altro che un modello virtuale altamente dettagliato del suo corrispettivo fisico, che ne rappresenta una replica fedele.
Modelli matematici avanzati possono simulare il movimento e l’interazione degli elementi interni del cuscinetto, la dinamica del lubrificante negli interstizi, la deformazione meccanica, la rigidezza, la resistenza delle parti, le prestazioni delle guarnizioni, e infine il cuscinetto nel suo insieme.
Tra i benefici dell’applicazione di gemelli digitali, oltre a un incremento di affidabilità e durata, si osserva una significativa riduzione di tempi e costi di progettazione e produzione.
Essi consentono di individuare design ottimali, un controllo sulla qualità e una valutazione delle effettive prestazioni del componente e delle specifiche per la sua produzione, compresi i relativi costi e le variabili che incidono sulla realizzazione dell’idea progettuale.
Il gemello digitale è una fonte preziosissima di informazioni. Esso viene relazionato al componente fisico mediante una serie di sensori posti su aree importanti per la funzionalità del componente stesso, che consentono di analizzare numerosi parametri prestazionali: temperatura, vibrazioni, energia dissipata, etc.
L’analisi dei dati, combinata con altre informazioni, consente di capire il comportamento istantaneo del cuscinetto e di prevederne quello futuro.
Il flusso continuo di informazioni permette, altresì, al gemello digitale di eseguire simulazioni, rilevare e analizzare eventuali problematiche di prestazione e studiare possibili migliorie.
Materiali e tecnologie di produzione innovative
L’impiego di materiali innovativi nella costruzione dei cuscinetti, unitamente a tecnologie di produzione all’avanguardia come la manifattura additiva, consente di adattare in modo ottimale i cuscinetti all’applicazione specifica.
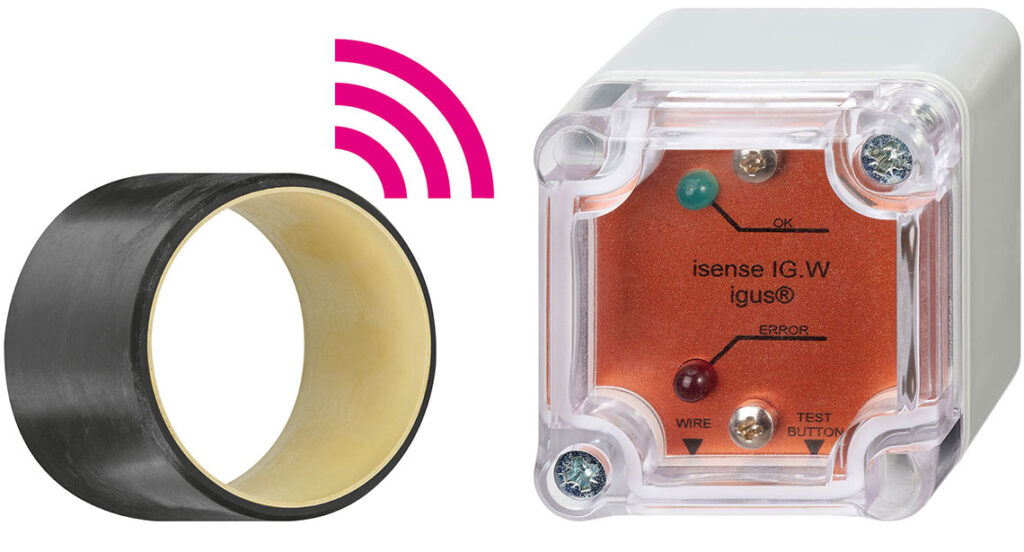
Il materiale utilizzato influenza proprietà come:
- peso;
- capacità di carico;
- idoneità a determinate condizioni ambientali (contaminazione, umidità, contatto con alimenti).
Un ulteriore vantaggio è poi rappresentato dall’impiego di soluzioni a minore impatto ambientale.
Ne sono l’esempio i cuscinetti in polimero, per l’80% più leggeri dell’acciaio, silenziosi, resistenti all’usura, alla fatica, alla corrosione e alle sostanze chimiche e praticamente esenti da manutenzione.
Tecnologie additive applicate ai cuscinetti
Una delle tecnologie più promettenti nel campo della costruzione leggera è la manifattura additiva, famiglia di processi che apre possibilità completamente nuove nel design dei cuscinetti, offrendo soluzioni alleggerite e compatte, elevata capacità di carico, affidabilità, buona durata ed elevata personalizzazione.
Sono documentate soluzioni con notevoli riduzioni in peso, pari al 90% circa rispetto ad analoghe varianti tradizionali in acciaio ed al 60% rispetto varianti in alluminio.
Cuscinetti alleggeriti mediante manifattura additiva sono impiegati nell’industria meccanica, aerospaziale, nella bioingegneria, nell’automotive e nella robotica (fig. 5).
Cuscinetti resistenti all’usura da stampa 3D
Le tecnologie di produzione additiva rendono possibile la produzione di componenti intelligenti, a costi competitivi e in tempi brevi.
La tecnologia “3D isense” di igus, utilizzata per la realizzazione di cuscinetti, si avvale di sensori incorporati all’interno del componente realizzato in tecnopolimero che, grazie alla stampa multimateriale, misurano la durata d’esercizio e avvisano circa la necessità di sostituzione prima che si verifichi un guasto.
Tra i principali benefici, il sistema permette di rilevare eventuali sovraccarichi e arrestare immediatamente l’applicazione per impedire ulteriori danni sia ai cuscinetti che all’intero impianto.
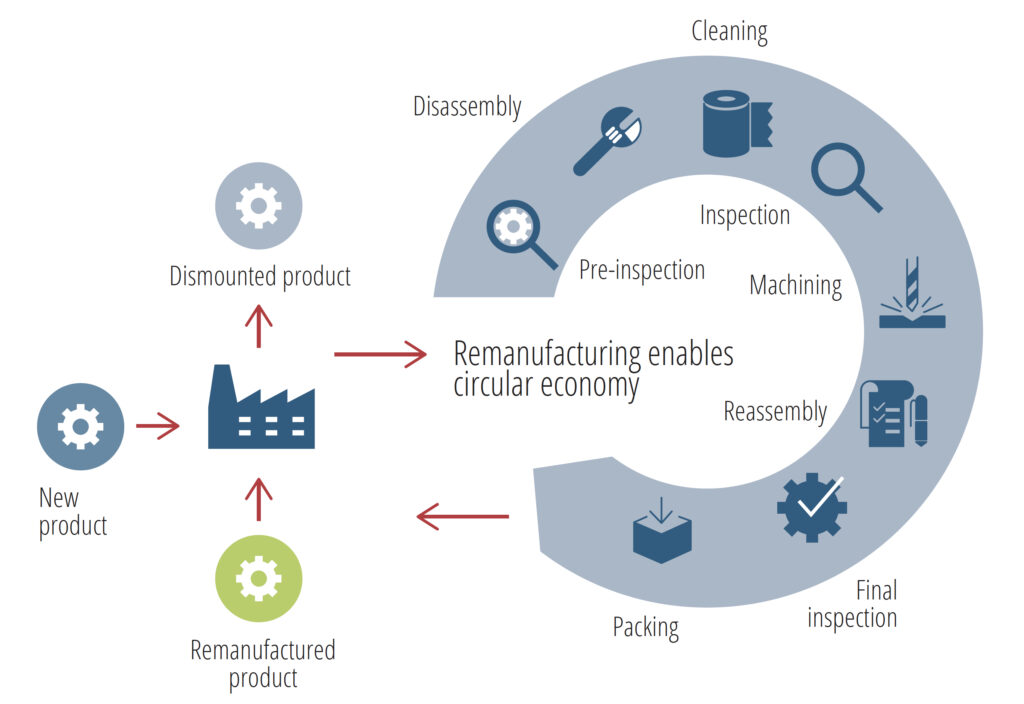
È inoltre possibile integrare componenti speciali nel processo di manutenzione preventiva, riducendo fermi macchina e interventi di manutenzione.
Il cuscinetto a strisciamento “isense”, in figura 6, segnala il proprio stato di usura prima che la macchina possa subire danni o guasti.
Disponibile in cinque materiali, può essere impiegato in numerosi settori industriali e in altrettante applicazioni.
Ulteriori vantaggi della tecnologia riguardano infine:
- operatività in assenza di lubrificazione;
- minori sprechi e scarti di materiale grazie alle tecnologie di manifattura additiva;
- tecnologia a supporto dell’economia circolare della plastica e degli investimenti in riciclo chimico.
Più sostenibilità con i cuscinetti ricondizionati
Usura, corrosione, intagli, microcricche, condizioni particolari di funzionamento come la contaminazione o contatti anomali nella zona di rotolamento, e altri fattori possono provocare danni ai cuscinetti.
Di conseguenza, la durata di esercizio di un cuscinetto è spesso inferiore alla vita stimata. Quando un cuscinetto sta per rompersi, il primo pensiero è quello di sostituirlo con uno nuovo.
Un’analisi approfondita seguita da opportune fasi di rigenerazione può tuttavia riportare i cuscinetti alle loro prestazioni originali.
L’economia lineare prevede l’impiego di nuove risorse, la creazione nuovi prodotti che, tuttavia, al termine della loro vita non vengono in alcun modo recuperati.
Il processo di rigenerazione dei cuscinetti, come ad esempio quello sviluppato da SKF, supera tali modalità operative, prevedendo la completa rigenerazione del componente.
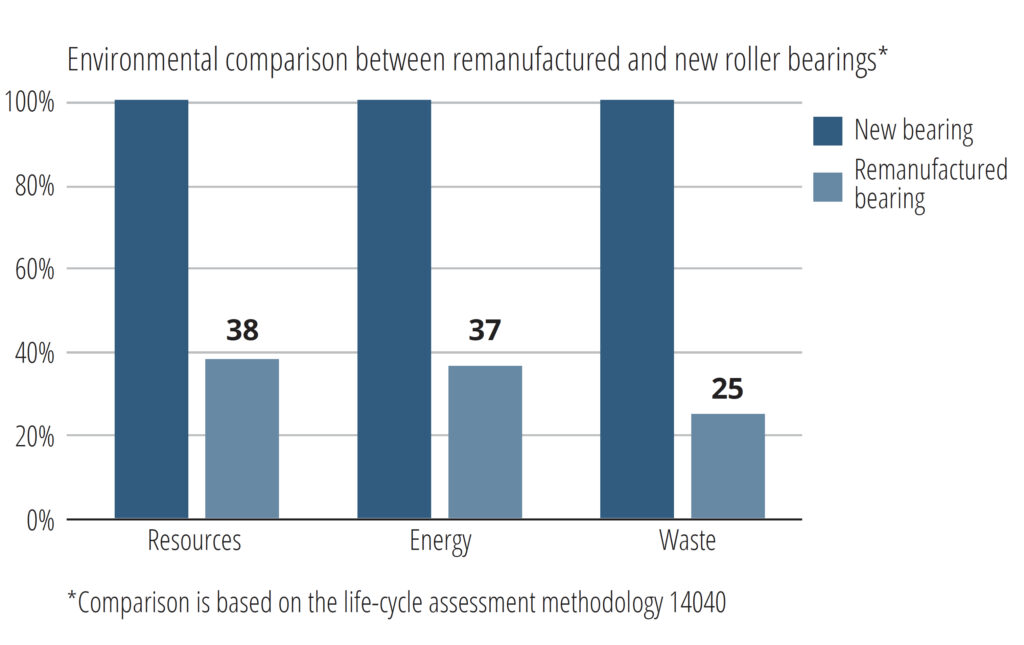
Riutilizzando vecchie parti e riciclando il materiale di scarto, si riduce la quantità di nuovo materiale.
Il processo fa parte di quella che è definita nuova economia circolare (fig. 7).
La rigenerazione ha un impatto più che positivo sull’ambiente (fig. 8).
A seconda dell’entità del ricondizionamento, un cuscinetto rigenerato può ridurre le emissioni di carbonio sino al 90% rispetto alla produzione di un cuscinetto nuovo e anche in termini di consumo energetico si ha un risparmio sino al 90%.
I servizi di ricondizionamento SKF comprendono attività di pulizia dei cuscinetti e di gestione dei rifiuti rispettose dell’ambiente.
Grazie al prolungamento della durata di esercizio, il ricondizionamento evita la rottamazione dei componenti e lo spreco di risorse naturali.
Anche i tempi di consegna di un cuscinetto ricondizionato saranno ridotti.
A titolo esemplificativo, si consideri una grande azienda in cui durante la manutenzione vengano sostituiti 2000 cuscinetti all’anno. Poiché la metà delle sostituzioni può essere effettuata con cuscinetti rigenerati, quello stabilimento evita l’emissione di circa 30 tonnellate di CO2 l’anno, contribuendo agli obiettivi di riduzione delle emissioni di CO2 previsti a livello globale.
Il ricondizionamento spesso rappresenta l’alternativa più rapida per la sostituzione di un cuscinetto guasto, soprattutto in caso di scarsa disponibilità di componenti a magazzino.
In questo modo i tempi di consegna si fanno più rapidi, garantendo qualità elevata anche in caso di un’ampia rigenerazione.
Utilizzando cuscinetti rigenerati, è inoltre possibile ottenere un notevole risparmio sui costi di gestione e manutenzione, spesso molto elevati.
Le attività di ricondizionamento vengono realizzate, in base a specifiche rigorose, da una rete globale di specialisti che operano presso centri di assistenza dedicati.
Le procedure iniziali riguardano pulizia, sgrassaggio e smontaggio dei cuscinetti. Tutti i componenti vengono quindi ispezionati.
Esperti analisti di cuscinetti valutano il cuscinetto e stabiliscono quale sia il processo di rigenerazione più efficace per ripristinarlo, compatibilmente con i requisiti dell’applicazione.
In base ai risultati, viene preparato un report dettagliato di analisi.
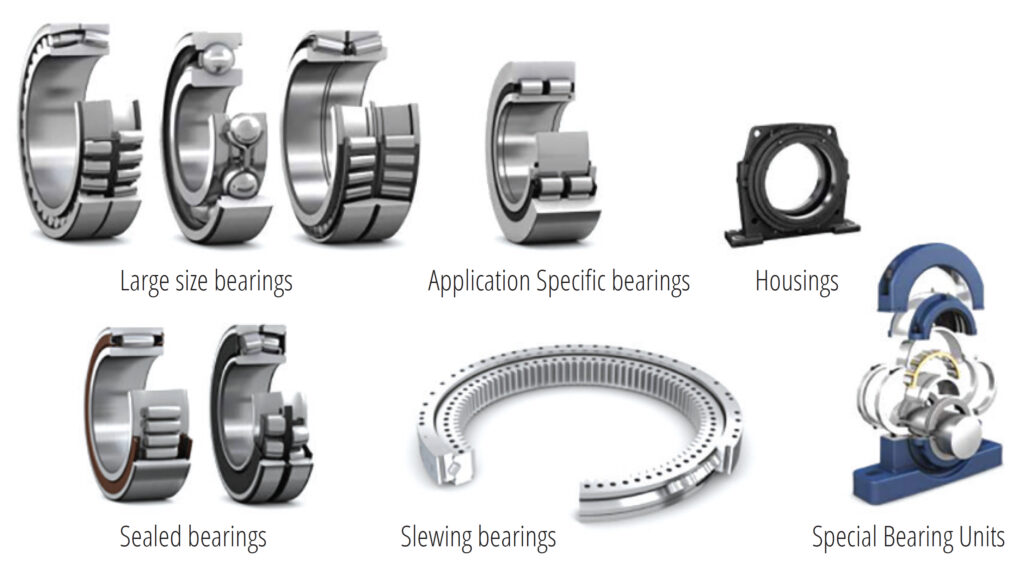
I cuscinetti che non presentano danni irreparabili vengono quindi riportati in condizioni di efficienza attraverso procedure adeguate, tra cui lucidatura, rettifica e sostituzione dei componenti.
Qualsiasi cuscinetto con oltre il 30% di vita residua stimata può rivelarsi un perfetto candidato per il ricondizionamento.
Come base per la rigenerazione dei cuscinetti, vengono utilizzati gli stessi standard, processi dedicati, attrezzature speciali, controllo qualità, conoscenze e competenze impiegate per la produzione di nuovi cuscinetti, inclusi criteri di accettazione che garantiscono risultati di alta qualità, anche in caso di rigenerazione estesa.
Inoltre, per garantire la tracciabilità del singolo cuscinetto, possono essere utilizzati sistemi di marcatura durante il processo di rigenerazione, per rintracciare il cuscinetto anche nel suo futuro ciclo di vita.
Oltre al metodo standard, sono poi disponibili anche ulteriori procedure di ricondizionamento in base a specifiche nuove o superiori, incluso il montaggio di sensori, l’aggiunta di lubrificazione integrata, rivestimenti speciali, soluzioni di tenuta o la rilavorazione in base a specifiche diverse.
I candidati tipici per la rigenerazione di cuscinetti industriali sono:
• cuscinetti di grandi dimensioni;
• cuscinetti a rulli sferici utilizzati nelle linee di rulliere continue;
• cuscinetti assiali di supporto.
Nel caso di SKF, viene eseguita la rigenerazione di cuscinetti industriali di tutte le principali marche e impiegati in diversi settori industriali quali, ad esempio, l’industria dei metalli, miniere, lavorazione dei minerali e del cemento, energie rinnovabili e tradizionali, cellulosa e carta, industria marina, ferroviaria e alimentare.
Attraverso questi processi di rigenerazione, le superfici funzionali rilevanti vengono rigenerate, compresa, se necessario, la sostituzione dei componenti del cuscinetto. Di conseguenza, la vita utile potenziale del cuscinetto può essere prolungata (fig. 10).
La corretta tempistica per la rimozione dei cuscinetti e la loro rigenerazione è essenziale per un equilibrio ottimale tra lunga vita operativa e bassi costi di esercizio.
I vantaggi dell’adozione di un programma di rigenerazione possono poi essere sfruttati appieno in associazione alla manutenzione predittiva.
Analizzando in profondità le cause dei guasti è possibile ottenere un insieme cause-effetti, oltre a un piano completo di azioni correttive per evitare il ripetersi dei danni.
Conclusioni e scenari futuri
Gli obiettivi dell’industria 4.0 mirano ad aumentare l’autonomia delle macchine utensili, la loro capacità di auto-regolazione, di correzione degli errori e gestione delle incertezze legate all’impiego di materiali innovativi, alla complessità dei processi o condizioni operative particolarmente esigenti.
L’estensione di tali tecnologie al segmento dei cuscinetti favorisce l’efficienza operativa grazie alla fusione di tecniche produttive e operative con il progresso digitale e la disponibilità di componenti intelligenti fornendo come risultato quella che sarà la fabbrica interconnessa del futuro.
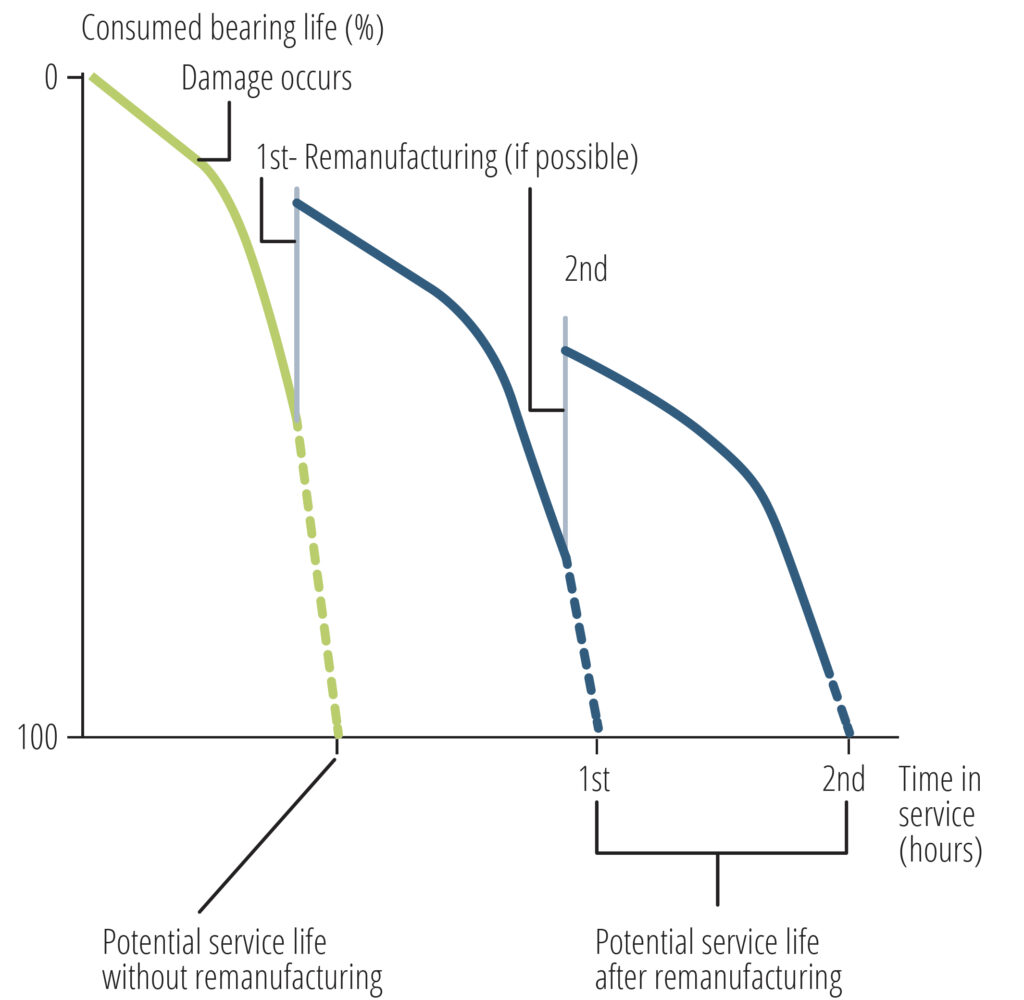
Come noto, i cuscinetti rappresentano un componente critico in ambito industriale. Oltre alle funzioni primarie, i cuscinetti hanno un ruolo chiave anche nel monitoraggio generale della salute di un macchinario e dell’intero sistema industriale.
L’evoluzione futura dei cuscinetti coinvolgerà aspetti come la riduzione del rumore, delle vibrazioni, il miglioramento dell’affidabilità, maggiore sostenibilità ambientale, funzionamento in assenza manutenzione ed elevata personalizzazione, oltre allo sviluppo di funzioni integrate, sensorizzazione, soluzioni compatte e ad alta densità di potenza.
Le future tecnologie si concentreranno sempre più sul “cuscinetto come servizio” piuttosto che sul “cuscinetto come prodotto”.
Secondo questa accezione, il cuscinetto raccoglie, elabora e trasferisce i dati per una migliore comprensione del comportamento della macchina utensile o dell’apparecchiatura industriale nonché del sistema nel suo complesso.
Occorrerà saper gestire enormi quantità di dati e implementare algoritmi di intelligenza artificiale per poterli interpretare e utilizzare con finalità migliorative di prodotto, di performance e di processo.
Riferimenti bibliografici
- https://www.industr.com/en/industrial-bearings-in-the-time-of-industry-where-is-it-heading-2637058
- https://www.ien.eu/article/industrie-40-intelligent-rolling-bearing-solutions/
- https://www.engineerlive.com/content/what-smart-bearing
- https://www.nsk.com/common/data/ctrgPdf/bearings/e7005c.pdf
- https://evolution.skf.com/the-future-of-bearing-mounting/
- https://www.skf.com/it/support/engineering-tools/bearing-assist
- https://www.innovationpost.it/tecnologie/digital-twin-che-cose-come-funziona-e-quali-sono-i-vantaggi-del-gemello-digitale/
- https://www.franke-gmbh.it/cuscinetti-su-filo/settori-di-innovazione/materiali-alternativi/
- https://www.htcfranke.it/news-29-Leggerezza-in-3D
- https://www.igus.it/info/3d-printing-embedded-sensors
- https://www.skf.com/it/industries/wind-energy/operation-and-maintenance/bearing-remanufacturing-services
- https://www.skf.com/it/services/reconditioning-and-customization
- Klebanov, Y.M., Murashkin, V.V., Polyakov, K.A. et al. Dynamic Loading in High-Speed Ball Bearings. Russ. Engin. Res. 38, 65–71 (2018). https://doi.org/10.3103/S1068798X18020107
- Murashkin, V.V., Klebanov, Y.M., Danilchenko, A.I. et al. Loads and Stress-Strain State of Gas Turbine Engine Bearing Cages. Russ. Aeronaut. 60, 658–661 (2017). https://doi.org/10.3103/S106879981704026.
di Giorgio De Pasquale, Dipartimento di Ingegneria Meccanica e Aerospaziale, Politecnico di Torino, Smart Structures and Systems Lab,
Elena Perotti, Senior data analyst